数控机床多能量源的动态能耗建模与仿真方法
2017-12-25 来源: 重庆大学机械传动 南京理工大学机械工 作者:何彦 林申龙 王禹林 李育锋 王立祥
摘要:机床能量消耗过程的评估和分析是机床能效优化研究的基础。现有研究提出的机床能耗模型主要是静态能耗模型,少数对机床动态性能耗的研究又主要集中在机床运行状态的动态性的建模,缺乏对机床能量源特别是数控机床多能量源的动态性能耗的研究。针对数控机床能量源多、加工任务及加工参数动态变化等特点,提出了一种数控机床多能量源的动态能耗建模与仿真方法。对数控机床能耗过程的动态性进行分析;在此基础上,结合面向对象着色赋时Petri 网(Colored timedobject-oriented Petri netCTOPN)和虚拟部件方法建立数控机床多能量源动态能耗模型,其中CTOPN 模型用于描述数控机床能耗过程机床和多能量源运行状态的动态特性,虚拟部件方法用于描述数控机床多能量源受加工参数影响的动态特性;通过CTOPN 中“变迁”蕴含的信息来驱动虚拟部件模型实现对数控机床多能量源的动态能耗特性的建模。案例分析结果证明了该方法的可行性,上述模型可为数控机床动态能耗的预测、综合的能耗特性分析以及定量的能耗影响因素分析提供一种基础支持,具有较广阔的应用前景。
关键词:数控机床;多能量源;动态能耗;建模仿真
0 前言
近年来,随着制造业能耗和环境问题的日益严峻以及全球低碳化形势的发展,机床能量消耗问题的研究受到了欧美等发达国家地区政府的广泛关注。机床量大面广,能耗总量巨大,但机床有效能量利用率低[1]。因而研究机床的能量特性对机械制造行业的高效低碳运行具有重要意义。在美国、欧洲、日本等发达国家和地区,机械加工设备的能耗特性建模已受到广泛关注,特别是在欧洲,颁布的一系列能耗指令、标准[2-3]推动了大量的机床能耗建模技术研究。目前对机床的能耗特性建模的研究主要集中在基础性能耗、工艺性能耗、结构性能耗和动态性能耗建模等四个方面。
基础性能耗建模的研究主要采用热动力学方法研究机床加工过程的能耗模型。如GUTOWSKI等[4]建立了机床加工过程的热动力学能耗模型框架。而工艺性能耗建模的研究主要通过分析加工参数对机床运行能耗的影响建立机床的比能模型。DRAGANESCU 等[5]通过试验建立了机床主轴的比能模型;DIAZ 等[6]通过试验将机床比能表示为材料切除率的函数;LI 等[7]将机床视为一个整体,通过测量不同切削条件下的功率获得了机床的比能模型。上述能耗模型都是将整个机床视为黑色或灰色系统,不能详细描述机床内部的能耗过程,并且需要开展大量试验。进一步开展的结构性能耗建模的研究是对机床及其各耗能部件的能耗特性进行分析建立机床的能耗模型。如文献[8]建立了数控机床主传动系统的率平衡方程;文献[9-11]采用参数化建模方法对机床各能量源进行了仿真。文献[12]建立了数控机床多源能量流的系统数学模型。
上述的基础性能耗、工艺性能耗、结构性能耗建模研究主要针对机床的能量消耗进行了静态的建模,无法对机床加工过程的动态能耗特性进行分析。目前,文献[1]建立了机床服役过程机电主传动系统的时段能量模型,该研究局限于主传动系统的能耗动态性分析;国外少数学者采用离散事件建模方法对机床动态能耗特征进行建模。DIETMAIR 等[13-14]提出了一种离散状态建模方法对机床能耗进行系统化建模。该研究主要对机床运行状态的动态性进行了分析,无法对机床耗能部件的能耗的动态性如受加工参数(切削条件、材料等)的影响进行分析。随着工业化的进程和基础装备制造业的发展,数控机床已成为机床装备的主流。与普通机床相比,数控机床的结构和能量特性发生了很大的改变。数控机床能量源增多、能量损耗复杂,主传动系统占整个机床能耗的比例相对普通机床越来越小[12]。因此,本文从数控机床能量源多、加工任务及加工参数动态变化等特点出发,基于数控机床及其多能量源的动态能耗特征分析,对数控机床多能量源的动态能耗模型进行建模与仿真。建立的数控机床能耗模型可用于分析数控机床及各耗能部件的能耗与其
运行状态的关系,并为加工参数节能优化、机床配置的节能优化以及能耗战略决策提供数据基础。
1 、数控机床的动态能耗特性分析
1.1 数控机床及多能量源的运行状态的动态性分析
在ISO 14955-1[3]标准中,将数控机床的运行状态划分为停机、待机、准备、空载以及加工等五个独立的状态。基于ISO 14955-1 定义的机床状态,本文以从某数控机床加工过程获取的功率曲线为例来分析数控机床及多能量源的运行状态的动态性。如图1 所示,该数控机床的运行状态随着机床加工的进行而发生变化,数控机床先处于准备状态,当主轴启动(功率曲线上出现尖峰)机床进入了空载状态,随着刀具接触工件,机床的运行状态又由空载状态进入加工状态;同时数控机床的多能量源运行状态也随着机床加工过程对不同能量源的需求而变化,如主轴系统在第一个尖峰之前处于关闭状态,为了满足加工需求,需要将主轴加速到给定速度,因此第一个尖峰后主轴系统处于开启状态来满足后续的加工需求。
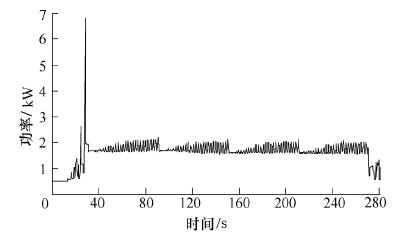
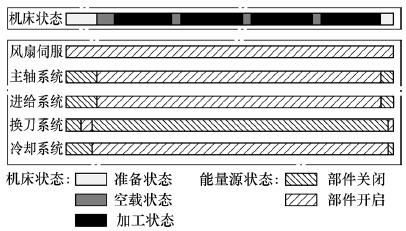
图1 能耗过程的动态性
1.2 多能量源受加工参数影响的动态特性分析
与普通机床相比,数控机床的结构和能耗特征有很大区别,数控机床能量源更多,能耗形式更复杂,数控机床的能耗涉及机电液领域[15]。数控机床能量源的能耗除了与自身的结构配置有关,还与其相应的加工参数(如切削参数、材料等)有关。作者所在的研究团队对HAAS机床的功率与运行参数的关系进行了试验研究,试验结果如图2 所示。HAAS机床粗铣槽、精铣槽以及点孔的空载功率分别为p1、p2和p3,由图2 可知机床的空载功率随主轴转速的变化而呈现动态变化。因此,即使数控机床的加工过程相同,由于能量源结构的差异或者加工参数的变化,也会导致机床能耗呈现动态变化性。
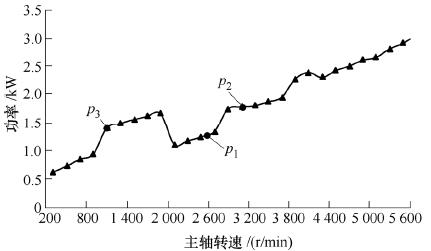
图2 HAAS 机床空载功率
2、 数控机床动态能耗特性的建模
根据上述分析,数控机床加工过程总是伴随着复杂的动态能耗特征。因此,为了分析数控机床的动态能耗特征,本文将数控机床的加工过程视为由多能量源触发的一系列离散事件,提出了一种数控机床多能量源的动态能耗建模与仿真方法,从全局的角度对机床能耗进行评估与分析。该方法结合面向对象着色赋时Petri 网(Colored timedobject-oriented Petri net,CTOPN)和虚拟部件方法建立数控机床多能量源动态能耗模型,其中CTOPN模型用于描述数控机床能耗过程的运行状态的动态特性,虚拟部件方法用于描述数控机床多能量源受加工参数影响的动态特性,最后通过CTOPN 中“变迁”蕴含的信息来驱动虚拟部件模型实现对数控机床多能量源的动态能耗特性的建模。
机床能耗建模与仿真框架如图3 所示,包含以下三个模块。
(1) token 生成模块:数控机床的CTOPN 模型由特定的着色赋时token 驱动,这些着色赋时token可由加工信息如工件的加工特征、工件的工艺卡片或工件加工的NC 代码等生成。
(2) 数控机床能耗模型模块:包括描述数控机床能耗过程运行状态的动态性的CTOPN 模型,述多能量源动态性的虚拟部件模型以及描述特定加工负载的负载模型。其中虚拟部件模型和负载模型由机床CTOPN 模型驱动;负载模型作为虚拟部件模型的加工负载源。
(3) 评估与分析模块:通过对机床能耗的能耗过程动态性的建模和仿真,可以获得全局的详细的机床能耗信息,并且可进行定量的原因-结果分析,为机床加工过程的能耗提供一种评估方法并为机床节能优化提供数据基础。
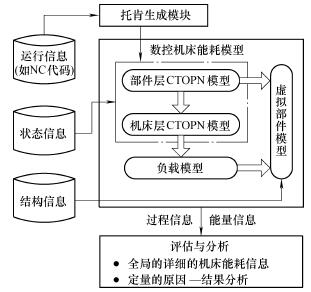
图3 数控机床多能量源的动态能耗建模与仿真框架
2.1 数控机床CTOPN 模型
为增强建模柔性并适应参数化、模块化的虚拟部件模型,本文采用面向对象着色赋时Petri 网(CTOPN)方法[16]。一个典型的CTOPN 模型是一个七元组
S=OPS,R,C,D, I,O,M0 (1)
式中,OPS 为对象库所集,R 为门变迁集,C 为与对象库所集和门变迁集关联的着色token 集, D 为着色token 的时间延迟属性集, I 为对象库所到门变迁的输入传递函数集,O为门变迁到对象库所的输出传递函数集,M0为CTOPN模型的初始标识。
为了建立机床加工过程的CTOPN 模型,首先可采用面向对象Petri 网(OPN)方法建立与机床状态和多能量源运行状态相关的状态特征模型,然后通过由token 生成模块产生的着色赋时token 及其相应属性来描述具体加工过程的运行特征。基于机床状态与多能量源运行状态之间的关系,建立机床层OPN 模型,如图4 所示。机床当前运行状态与即将执行的动作共同决定机床下一个运行状态。该方法具有一定柔性,不同生产参与人员可根据需要建立不同的机床状态与多能量源运行状态之间的关系。文献[17]根据数控机床各能量源的运行特征将其划分为三种基本类型:0-1 型、离散型以及连续型,其中连续型能量源是离散型能量源的特殊情况(切削力加载到离散型能量源上)。为了便于描述机床能耗过程的动态性,本文进一步将数控机床能量源划分为加工进度相关的能量源(如进给系统,换刀系统等)和加工进度无关的能量源(如冷却系统,主轴系统等)。结合文献[17]的研究,将能量源分成四种类型:① 0-1 型&加工进度无关能量源(如机床电气,冷却系统);② 0-1 型&加工进度相关能量源(如换刀系统);③ 离散型&加工进度无关能量源(如主轴系统);④ 离散型&加工进度相关能量源(如进给系统)。根据上述对能量源的分类,建立其通用OPN模型。对于①类能量源,运行状态的每一次转变总是基于相应的需求,如图5 所示。
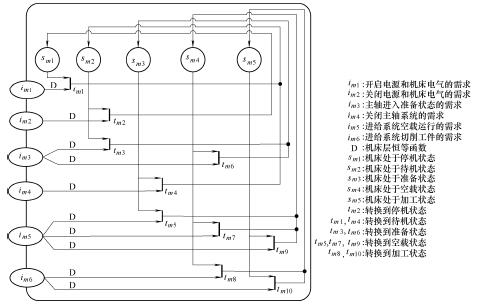
图4 机床层OPN
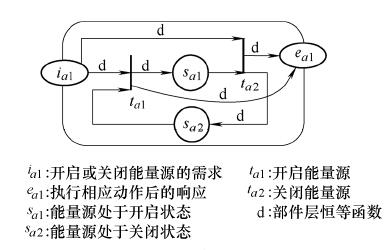
图5 0-1 型&进度无关能量源OPN
对于②类能量源,其处于开启状态的持续时间由库所sb1 (“能量源处于开启状态”)中着色token的时间延迟属性决定,一旦满足延迟时间,变迁tb2(“关闭能量源”)将发生,能量源进入关闭状态,如图6 所示。此外,在机床能耗的评估中应该考虑部分与机床加工过程相关的外部事件(如人工的装载和卸载工件,机床等待下一个工件到达等),这类事件自身不是能量源,但会影响机床的运行持续时间,从而影响机床能耗。根据这类事件的特点,可采用与图6 所示相同的OPN 模型。考虑了这类事件的机床能耗模型可为车间的调度提供一种基础支持。与0-1 型能量源不同,离散型能量源在开启之前将处于准备状态(如主轴系统的变频器、电动机等准备好),如图7 所示,用库所sc2来描述能量源的准备状态;并且离散型能量源在开启状态下可能动态地调整运行参数,这种情况用变迁tc2和tc3 (“离散型能量源调整运行参数”)来描述。③类能量源与①类能量源类似,其运行状态的每一次转变总是基于相应的需求。
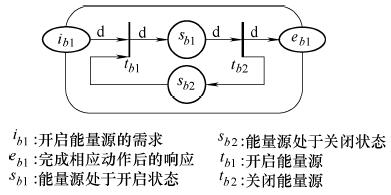
图6 0-1 型&进度相关能量源OPN
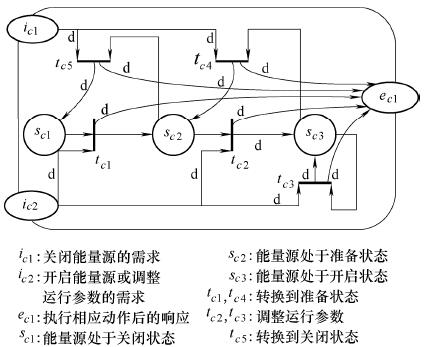
图7 离散型&进度无关能量源OPN
对于离散型&进度相关的能量源,其电动机频繁地加速、减速或者以恒定速度运行一定时间。这类能量源处于开启状态的持续时间取决于库所sd 3(“能量源处于开启状态”)中着色token 的时间延迟属性。值得注意的是,当时间延迟结束后,④类能量源的下一个运行状态还取决于其他条件(如加工过程的下一个进度周期是否在同一个④类能量源上执行)。因此,用库所sd 4“( 能量源处于预准备状态”)来表示能量源开启与准备之间的过渡状态,如图8所示。
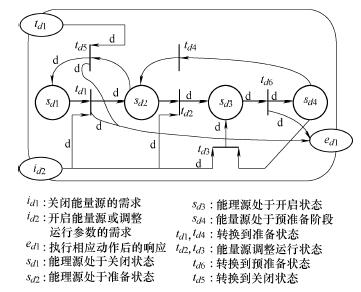
图8 离散型&进度相关能量源OPN
2.2 虚拟部件模型及负载模型
Petri 网方法适合于对复杂系统进行建模以及对控制顺序进行优化,但它在对子系统的参数影响分析方面不够详细。另一方面,虚拟仿真技术在机床开发等领域已经得到广泛使用,它能够详细描述参数的影响。由于仿真工具的使用,虚拟仿真模型变得越来越准确、快捷和可靠,而仿真所消耗的时间和成本却在降低。Petri 网和虚拟仿真技术都是已有的方法,它们都是针对特定应用建立起来的解决问题的方法。将这两种方法结合起来,更适于从全局的角度详细地评估机床动态的能耗。
首先,能量源的虚拟仿真模型必须保证适当的可操作性以及足够的准确度来评估机床能耗。精确地再现能量源的运行行为不是能耗仿真模型的目的,面向能耗的能量源虚拟模型只考虑影响机床能耗的主要因素。其次,基于文献[18]的假设可对虚拟能量源进行必要的简化:假设能量源被正确设计并且在恰当的运行条件下工作,这样就可以提前假设一系列物理参数(如电动机或传动系统内部的温度等),而不用搭建复杂的数值模型来评估这些参数。
虚拟部件模型可用公式或表格表示,这些公式或表格表达了运行参数及输入与部件能耗之间的关系[18]。作者所在的研究所的早期研究中,建立了数控机床多源能量流的数学模型[12],该研究描述了数控机床各个能量源的能耗环节以及影响能耗的因素,可以作为虚拟部件建模的基础。
加工单元动态地受加工负载影响。相对主轴系统而言,加工负载对进给系统的功率影响较小,可采用进给系统空载功率近似评估其在切削状态下的功率[20],因此本文忽略轴向力及径向力对进给系统功率的影响,主要考虑切向力Fc对主轴系统的功率影响。各加工类型的主切削力(切向力)模型已有文献进行了大量研究,本文以车削和铣削为例,车削中主轴所受的切向力模型如式(2)所示[19]
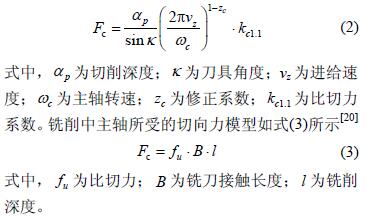
3 、CTOPN 和虚拟部件的驱动关系
在数控机床动态能耗建模与仿真框架中,通过CTOPN 中“变迁”蕴含的信息来驱动虚拟部件模型实现对数控机床多能量源的动态能耗特性的建模。其中,机床CTOPN 模型分为部件层和机床层,部件层CTOPN 直接驱动虚拟部件的运行,以及驱动机床层CTOPN 运行状态的变化,详细驱动关系如图9 所示。当Petri 网模型中的特定变迁满足发生条件时,变迁发生,并同时将着色token 携带的能量源运行信息发送至相应的虚拟部件。对于0-1 型能量源,其Petri 网模型只发送开启和关闭两种信号;对于离散型能量源,除了开启和关闭能量源的信号外,还将运行参数发送至虚拟部件。当机床进入加工状态时(即机床层变迁tm8或tm10 满足条件发生变迁),相应着色token 携带的切削条件被发送到负载模型,通过负载模型计算得到的切削力将加载到加工单元。
4 、应用实例
下面以一台C2-6136HK 数控车床加工棒料为例说明数控机床多能量源的动态能耗建模与仿真方法。本案例所用工件材料为45 钢,毛坯直径29.94 mm,车削长度80 mm,切削条件如表1 所示。本案例中采用的C2-6136HK 的能量源包括:风扇伺服系统、主轴系统、进给系统以及冷却系统。在机床运行过程中风扇伺服系统和冷却系统的功率大小与负载无关,且功率值基本保持恒定,因此采用额定功率值表示其虚拟部件模型。主轴系统为机械主轴,主轴与进给系统的功率均受加工参数动态影响,因此采用数学模型作为其虚拟部件模型,该模型基于作者所在研究团队的早期研究[21]。
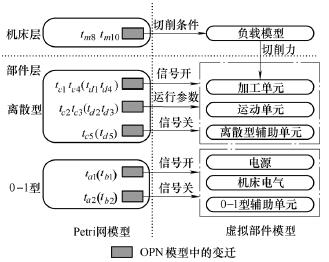
图9 Petri 网模型对虚拟部件的驱动关系
表1 试验1 切削条件
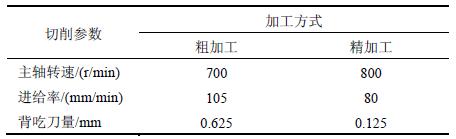
4.1 数控机床动态能耗模型建立
首先,将机床层OPN 表示为P0,部件层根据上述对能量源的分类,将装载与卸载工件事件表示为P1,将0-1 型&进度无关能量源冷却系统和风扇伺服系统分别表示为P2和P3,将离散型&进度无关能量源主轴系统表示为P4,将离散型&进度相关能量源进给系统表示为P5。然后,采用两个层级门变迁分别表示能量源运行需求和更新机床运行状态需求,每个层级门变迁由若干输入变迁和一个输出变迁组成。基于由相应NC 代码提取生成的着色赋时token,设置各弧上权函数,得到机床加工过程的CTOPN 模型,如图10 所示。最后建立各能量源Petri网模型中变迁与虚拟部件模型的映射关系。
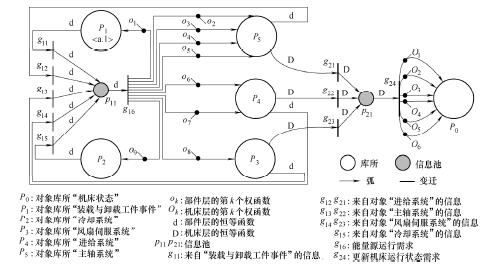
图10 机床加工过程的CTOPN 模型
4.2 能耗仿真与分析
构造的数控机床动态能耗模型通过Matlab/Simulink 仿真平台进行仿真。仿真获得的机床总能耗为37.95W h ,采用HIOKI3390 功率分析仪监测机床实际总能耗为39.5W h ,如图11 所示,仿真与监测结果之间的误差为4%,在可接受范围内,证明了该方法的可行性。仿真结果分别从数控机床运行状态角度和多能量源角度全面地展示了加工过程的能耗分布情况,可为不同的生产参与人员提供需求的机床能耗信息,如表2 和表3 所示。从机床状态角度可知机床在各个状态下的运行时间及能耗,主要时间及能量消耗集中在加工状态。从能量源角度可知数控机床各个能量源的运行时间及能耗情况,主轴系统及风扇伺服系统为加工过程中的主要能量消耗源。将各机床状态能耗分解到各个能量源,使加工过程的能耗分布情况进一步透明化,有利于从策略和技术上发现节能潜能,如图12 所示。例如在机床准备和空载阶段可考虑关闭冷却系统,在机床加工阶段,主轴系统能耗较大,可考虑采用高效主轴等。
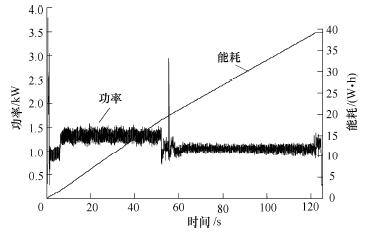
图11 棒料车削实际加工功率及能耗
表2 数控机床各运行状态能耗分析结果
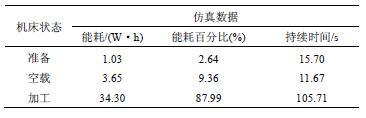
表3 数控机床各能量源能耗分析结果
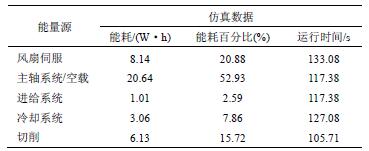
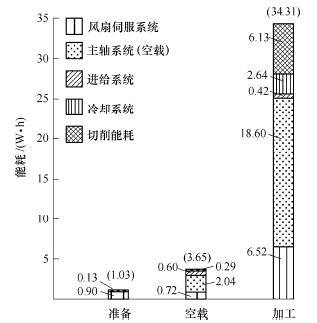
图12 数控机床各运行状态下的能耗详细分析
下面对棒料车削试验1 的切削条件进行调整,设置试验2,试验2 切削条件如表4 所示,其余加工条件同试验1。通过对机床能耗变化的原因-结果进行定量分析,提出节能建议。
表4 试验2 切削条件
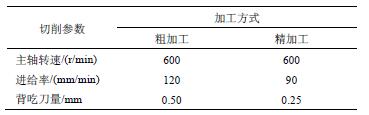
试验1 与试验2 中加工进度相关能量源对加工进度无关能量源能耗影响的变化如图13 所示。
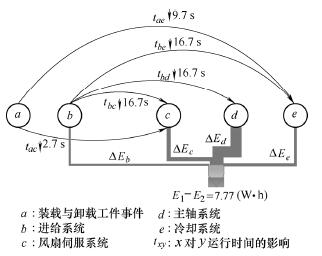
图13 能量源相互能耗影响定量分析
试验2 在装载工件时关闭了切削液,并且装载时间减少,这两个事件使冷却系统运行时间共减少12.4 s ,而在粗精加工阶段由于进给速度的提高,受进给系统运行时间影响的风扇伺服系统、主轴系统以及冷却系统的运行时间均减少16.7 s 。与试验1 相比,试验2 在加工时间及能量源运行功率变化的情况下,试验2 比试验1 加工时间减少19.4 s ,共节能7.77W h ,如式(8)所示。其中,进给系统能耗减小0.09 W h ,风扇伺服系统能耗减小1.13W h ,主轴系统能耗减小5.26W h ,冷却系统能耗减小0.54W h ,如式(4)~(7)所示。通过分析可知,适当降低主轴转速及提高进给速度有利于节能
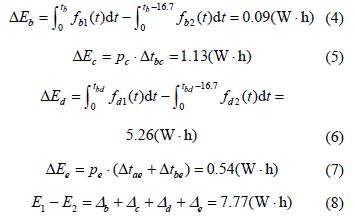
下面运用本文的动态能耗建模与仿真方法,对一个实际加工零件差动壳体的加工过程进行加工时间及机床能耗分析,差动壳体零件图如图14 所示,毛坯材料为经调质处理的45 钢,加工工艺及相应切削参数如表5 所示。
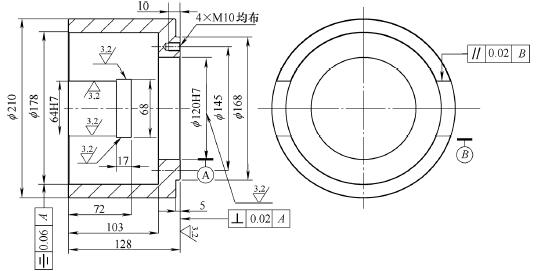
图14 差动壳体零件图
表5 差动壳体切削条件
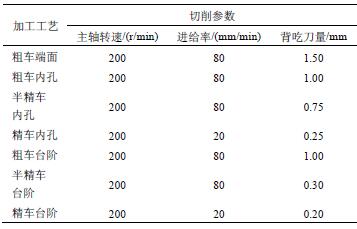
差动壳体零件在C2-6136HK 数控车床上加工,内孔的粗加工采用粗车循环方式,其余加工均为单次走刀。通过仿真可得该零件加工共耗时3 348.8s,总能耗为1 528.19W h 。各能量源能耗及总能耗的仿真值与监测值对比如图15 所示,监测总能耗为1 630.9W h ,仿真总能耗与监测值之间的误差为6.3%,在可接受范围内,证明了该模型的可行性。
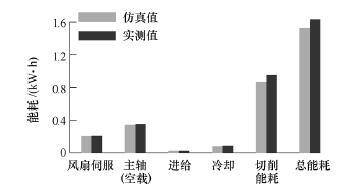
图15 差动壳体加工能耗仿真值与监测值比较
各机床状态及能量源的能耗分布情况如图16所示。机床在准备状态下只有风扇伺服系统开启,能耗为1.97W h ;在空载状态下,风扇伺服系统和主轴系统的能耗占到该状态下总能耗的73.5%,是因为两者的功率消耗较大;机床在加工状态下的运行时间为3 133.8 s ,其中2 648.25 s 机床在进行粗加工,进给速度和切削深度较大,作用在主轴系统上的切削力较大,导致机床加工状态下的切削能耗占到该状态下总能耗的56.8%,为868.65W h 。由上述分析可知,差动壳体加工过程中,粗车内孔所消耗的时间及能耗最大,考虑适当将粗车内孔的进给速度增大到100mm / min ,经仿真得到新方案与原方案的能耗比较如表6 所示。采用新方案,粗车内孔时主轴系统所提供的切削功率平均增大了206.43W,但零件加工总时间减少了550.8 s ,新方案比原方案共节能151.96W.h 。
综上所述,在零件实际生产加工前,应用本文模型可快速评估不同加工方案下零件的加工时间及数控机床能耗分布情况,分析节能潜能,提出节能建议。在节能策略方面,既可通过改变辅助部件启停策略来节能,如在棒料车削案例中,当机床处于准备状态时关闭冷却系统;还可以规范工人的装卸操作流程来减少机床处于准备状态的时间。在节能技术方面,可发现功率消耗较大的能量源,采用高效部件替换。在工艺参数优化方面,可在保证加工质量前提下,优化能量源运行参数,降低功率消耗或缩短加工时间。如在棒料车削案例中,降低主轴系统的运行参数以减小功率消耗;以及增大加工进度相关能量源进给系统的运行参数来减少零件加工时间及各能量源能耗;在差动壳体案例中,经分析适当提高粗车内孔进给速度,实现节能。未来研究可将本文建模框架与智能算法结合,探索加工方案的节能潜能并实现策略、参数方面的优化,以减小零件加工的时间及能耗。
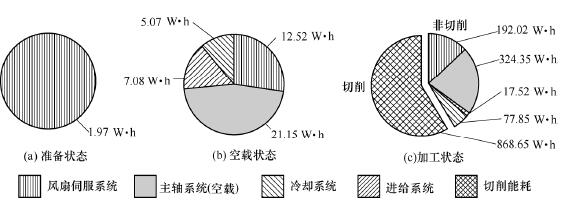
图16 差动壳体零件加工机床能耗分布
表6 差动壳体加工节能效果对比
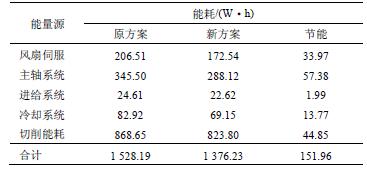
5 、结论
(1) 数控机床能量系统是一个多能量源系统,根据各耗能部件的运行方式以及与加工进度的关联性,数控机床多能量源系统可分为0-1 型&进度无关能量源、0-1 型&进度相关能量源、离散型&进度无关能量源、离散型&进度相关能量源等四类。
(2) 分析了数控机床能耗的动态特征,包括数控机床及多能量源的运行状态的动态性分析和数控机床多能量源受加工参数影响的动态特性分析。
(3) 基于数控机床能耗动态性分析,建立了数控机床多能量源的能耗建模与仿真框架模型,其中采用面向对象Petri 网(OPN)方法建立与机床及其多能量源运行状态相关的状态特征模型,然后通过由token 生成模块产生的着色赋时token 及其相应属性来描述具体加工过程的运行特征,建立机床层和部件层的CTOPN 模型;采用数控机床多源能量流的数学模型建立虚拟部件模型;最后通过CTOPN 中“变迁”蕴含的信息来驱动虚拟部件模型实现对数控机床多能量源的动态能耗特性的建模。应用实例表明,采用数控机床多能量源的动态能耗建模与仿真框架,可快速建立机床能耗的评估与分析模型,该模型可重用,可扩展,可为数控机床能量消耗预测和节能优化等一系列实际问题的解决提供支持。
本文的不足之处在于没有研究电主轴及其相应冷却单元的能耗特性,未来研究将进一步深入考虑高速数控机床这一特点。
投稿箱:
如果您有机床行业、企业相关新闻稿件发表,或进行资讯合作,欢迎联系本网编辑部, 邮箱:skjcsc@vip.sina.com
如果您有机床行业、企业相关新闻稿件发表,或进行资讯合作,欢迎联系本网编辑部, 邮箱:skjcsc@vip.sina.com
更多相关信息