基于刚度分析的机器人铣削加工刀具角度优化
2022-9-5 来源:商丘职业技术学院 徐州工程学院机电工程 作者:黄蓓 陈凤腾
摘要:为提高多轴机器人铣削的加工精度,提出一种新型的刀具方向角优化方法。 该方法综合考虑了串联机构的固有特性及其与机器人刚度的关系,从而在生成精加工刀具方向角时选择最佳的机器人姿势。 由于在不改变刀具轨迹的情况下,通过优化选择刀具的方向角来减少加工误差,该优化方法无需修改原始刀具轨迹以便补偿预测偏差。 在多轴铣削机器人系统上的实验结果验证了该方法的有效性。 研究结果表明,该方法能够加工出具有精细表面的三维形状,并减少了由于刀具向机器人刚度最低方向位移所引起的偏差。 相比基于体积刚度性能指标的刀具方向角优化方法,RMS误差减少了0.05mm。
关键词:机器人铣削;多轴铣削;刀具方向角;刚度
0 、引言
近年来,工业机器人在机械加工中的应用引起了广泛的关注。 尽管此类机器人主要用于焊接和搬运,但大量研究试图将其应用扩展到倒角、去毛刺、抛光甚至医疗手术等任务。 最近,主要由刚性数控机床处理的任务(例如机器人铣削) 已成为学术研究和工业研究的热点。
串联工业机器人机构的特殊性质使它们能够在相对较小的空间内以较低的成本加工各种大小的复杂形状。 尽管有这些优点,但在加工任务中使用工业机人仍有一些困难,例如定位精度低和刚度低。 尽管这些问题可通过改善其物理结构来解决,例如采用更好的编码器和连杆,但机器人刚度的姿态依赖性仍然是一个未解决的问题。最近,与机器人加工相关的研究试图通过在线和离线补偿方法来减少刀具变形,从而提高机器人的加工精度。
在线补偿技术通常需要昂贵且复杂的实时传感系统。 此外,当机器人处于低刚度的姿势时,该技术可能涉及机器人和工件的突然相对运动,这不可避免地会影响表面光洁度。 离线补偿技术依赖于刀具模型、刀具⁃工件接触模型、切削力预测算法以及所用机器人刚度模型的准确性。 此外,曲胜等的研究表明,由于需要完全修改原始刀具轨迹以补偿预测偏差,因此计算变得更加复杂。
虽然这些离线补偿研究在无需复杂、昂贵在线系统的条件下提高了加工精度,但是由于没有考虑主动刚度的影响,即,机器人刚度随机器人姿态的变化,因此它们仅能部分补偿加工误差。因此,在本研究中,提出了一种新的离线优化刀具方向角的方法。 利用机器人刚度相对于刀具方向角的变化,生成具有最大刚度姿态的简单" 之" 字形刀具轨迹,从而减少刀具的潜在偏差。 由于在不改变刀具轨迹的情况下,通过优化选择刀具的方向角来减少加工误差,因此该方法比传统优化方法具有更小的复杂度。
此外,由于计算是基于刚度性能指标,即更容易操作的标量测量,因此也减少了计算误差,并通过加工实验对该方法进行了验证。
1 、机器人加工系统
本研究采用的机器人加工系统包括一个 6 轴垂直关节式机械手(Motoman SV3X)、一个提供工件倾斜和旋转运动的 2 轴工作台、一个末端执行器及其外围部件。 末端执行器包括一个超精密的主轴部件(EM25N⁃5000⁃J4),用来支撑刀具。 所用 8 轴机器人铣削系统如图 1 所示。
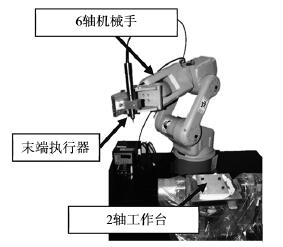
图18 轴机器人铣削系统
为了确保所提机器人系统的灵活性和定位精度,采取了两项主要措施。 首先,对刀架进行了设计,以便可以使用悬挂和指向两种配置。 但是,在这项工作中,由于其相对较高的灵活性,因此仅测试了悬挂配置。其次,按照机械手制造商推荐的程序对机器人进行在线和离线校准,以尽可能减少定位误差。 校准结果表明,与校准前的0.369mm相比,可以将定位误差降低到 0.203mm。
由于机械手的运动即使在没有切削力的情况下也会受到这种定位误差的影响,因此所提系统的加工精度最好也是相同的量级,或者略次于它。
2 、机器人刚度分析
2.1机器人刚度识别
通常,在整体机器人刚度的建模中仅考虑关节的刚度。 然而,为了更精确地表示机器人刚度,需要考虑机器人的姿势和作用在机器人上的外力,式(1) 则描述了这种关系:
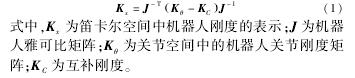
2.2刚度性能指标
体积刚度性能指标最早由 Lehmann C 等提出。该指标利用机械手的柔度矩阵,避免了与计算雅可比逆有关的数值误差。 最初,该指标用于钻井应用中的姿势优化,在其研究中的实验测试证明,该指标在增加机器人整体刚度和改善钻孔质量方面是有效的。本文提出了一种新的指标:单向刚度性能指标,其设计目的是减少在机器人铣削应用中观察到的非期望滑动运动。 该设计没有优化机器人的整体刚度,而是专注于机器人在垂直于刀具行进轴线方向上容易发生的变形。 单向刚度性能指标的数学公式是基于 Leh⁃mann C 等描述的柔度子矩阵。 将整体刚度计算替换为垂直于刀具行进轴线方向(单向)刚度计算,因此更有利于提升常规的“之”字型铣削加工精度。
其中,力的方向和位移是本研究的主要问题。 如果施加到机器
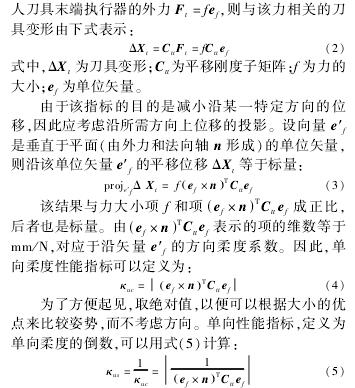
3、刀具方向角优化
刀具方向角优化过程针对的是粗加工后的精加工阶段。 首先将所有刀具位置的集合表示为一个高度阵列。 设置垂直分辨率和水平分辨率分别等于切削深度和步进量。 通过相对于所需形状偏移高度阵列来防止工件过度切削。 创建刀具位置的偏移高度阵列后,通过围绕刀具旋转机械手来选择每个刀具位置的机器人姿态。 机械手绕刀轴旋转如图 2 所示。
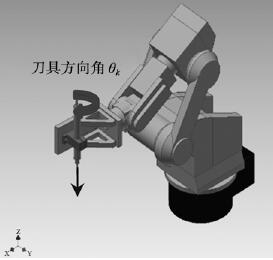
图 2 机械手绕刀轴旋转
从一个相对于 X 轴的初始角位置(θ0) 开始,机械手的角位置增加一个常数值(θk)。 在当前刀具位置为加工选择第一个不以碰撞结束的姿态。 这个过程在整个高度阵列中从上到下以之字形重复进行。 为了简单起见,该刀具在阵列所有点上保持垂直于水平面。精加工的目的是减少表面轮廓的缺陷,并生成尽可能类似于所需形状的最终结果。 这通常是通过在更适度的加工条件下加工工件来实现的,即在较低的材料去除速率下,从而将刀具偏差抑制到允许的水平。除此策略外,本文使用刚度性能指标值优化机器人姿态。 高度阵列数据结构用于生成刀具轨迹。 此外,加工切削中的刀具轨迹不是从顶部平面到底部逐层生成的" 之" 字形刀具轨迹,而是采用常规的" 之" 字形轮廓,其高度随刀具沿X 轴的位置而变化。 通过上述方法生成的精加工刀具位置集如图 3 所示。
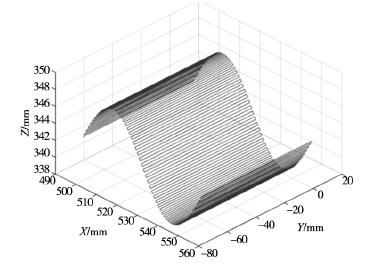
图 3 精加工刀具位置集
一旦生成刀具位置集,就对该集的每个点进行机器人姿态优化。 为简单起见,刀具应保持垂直于水平面。 然后,机械手以上述的方式沿刀具旋转,不同之处在于它现在考虑了机器人刚度,该刚度是针对所有刀具位置上所有可能的姿势计算得出的。 该计算将生成一张硬度指标图,显示其与刀具方向角的关系。 通过将刚度性能指标设置为零,可以将导致机械手碰撞的姿态从有效姿势集中移除。 刚度性能指标与刀具方向角 α 之间的关系如图4 所示。
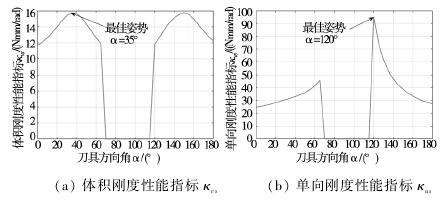
图 4 刚度性能指标与方向角
4、 实验结果与分析
4.1 实验装置
由于关节刚度通常是未知的,因此采用 Dumas C等提出的识别方法对机械手(SV3X)的关节刚度进行识别。 用于关节刚度识别的实验装置如图 5 所示。
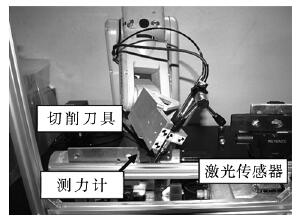
图 5 用于关节刚度识别的实验装置
考虑到旋转位移明显小于平移位移,因此只考虑力和平移位移。 用数字测力计(FGP⁃5,Nidec⁃Shimpo)将力施加在切削刀具上, 并借助激光位移传感器(LT9030M,Keyence)测量在所有三个轴上测量刀具位移。 由于激光位移传感器和数字测力计的精度均优于激光跟踪器和弹簧秤,因此这种方法得到的结果更准确。
此外,由于转动位移和扭矩可以忽略不计,从式(1)中可推导出,在计算中不需要第 6 个关节的连接刚度。 结果表明,用上述方法计算的机械手各关节刚度分别为[90.925, -2.869, -3.641,1.745,1.743] ×105Nmm /RAD。加工实验中工件的所需形状如图 6所示。
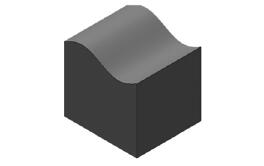
图 6 工件的所需形状
由于曲面上每个点的位置都可以用正弦函数计算。 因此,通过比较实际切削高度的值和用该函数计算的值,可以很容易地计算加工误差。
4.2加工结果对比
为了评估所提出的刀具定向角优化方法的精度,进行了一系列加工实验。 工件材料选择了主要由丙烯腈⁃丁二烯⁃苯乙烯(ABS)塑料组成的合成树脂。 因为具有良好的可加工性和快速成型优势,该材料在机器人铣削中的得到广泛应用。 采用了半径为 1mm 的球头立铣刀(SEC⁃PLBEM2S1)。 工件的材料是相同的合成树脂,加工条件如表 1 所示。
表 1 加工条件
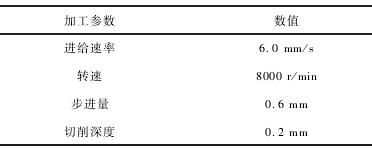
具体进行了三种不同类型的加工实验:①刀具方位角未优化;②以体积刚度性能指标优化刀具方位角;③以单向刚度性能指标优化刀具方位角。 选择刀具方向角的过程与第 3 节中描述的过程相同。 但是,在非优化切削中,除了需要避免碰撞的情况外,刀具方向角均保持恒定(α=0 )。 3个试验的加工结果如图 7 所示。
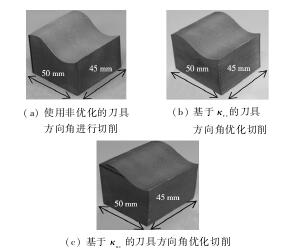
图 7 3 个试验的加工结果
加工后工件的表面轮廓也用 3D 扫描机( RolandMXD4)进行测量,一共进行了10次测量。 图8显示了所测轮廓与所需形状的比较。
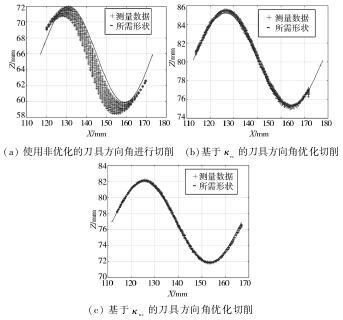
图 8 所测轮廓与所需形状的比较
在非优化切削的情况下,虽然图 7a 所示的表面轮廓形状表明加工后的表面是光滑,但图 8a 却表明该表面实际上与所需形状有较大差异。 这表明系统本身不足以实现更高的精度。相反,图 8b 和图 8c 表明表面轮廓中也存在这样的扭曲,但比刀具方向角未优化的情况要小得多。
实际上,通过比较加工误差的均方根(Root Mean Square,RMS)值可以看出,刀具方向角优化时加工精度最好,均在机器人定位误差的范围内。 此外,当使用单向刚度性能指标优化刀具方向角时尤其如此,因为体积刚度性能指标的 RMS 误差为 0.22 mm,而单向刚度性能指标的 RMS 误差为0.17mm,减少了0.05mm,即进一步提高了加工精度,验证了其有效性。
5、结论
本文提出了一种用于精密机器人加工的新型刀具定向角优化方法。 该方法利用机器人刚度随刀具方向角变化的特点,生成机器人姿态优化后的刀具轨迹。通过加工实验得如下结论:
(1)与刀具方向角不优化时相比,方向角优化方法能成功地生成更光滑、更精确的曲面轮廓;
(2)采用单向刚度性能指标比采用体积刚度性能指标更有效,两种情况下的加工误差分别为0.22mm和0.17mm,均在机器人定位误差的范围内,表明在加工合成树脂等软材料,该方法可以最大限度地提高铣削机器人的加工精度
。
投稿箱:
如果您有机床行业、企业相关新闻稿件发表,或进行资讯合作,欢迎联系本网编辑部, 邮箱:skjcsc@vip.sina.com
如果您有机床行业、企业相关新闻稿件发表,或进行资讯合作,欢迎联系本网编辑部, 邮箱:skjcsc@vip.sina.com
更多相关信息