交流伺服电机性能测试平台设计与应用研究
2022-6-28 来源:武汉华中数控股份有限公司 作者:翟世欣 曾星
随着中国智能制造 2025 战略的提出以及电机工业的迅速发展,行业内对于交流伺服电机的性能指标提出了更多以及更高的要求,在电机厂商层面,除了对电机的磁路仿真设计、工艺路线进行研究以外,往往缺失的是对新产品样机大批量的关键性能与理论仿真的验证 ; 在配套主机厂层面,随着电机选型品种繁多、应用层面广、性能参数多、知识层面宽泛,且对应不同应用场合对性能的偏重点也不同,这些问题都对电机性能测试技术有了更高的要求。对此,需要形成全面的评价标准和准确的测试手段,因而,开发一套交流伺服电机性能测试平台显得尤为重要。
一、测试平台总体架构
基于高精度高响应自主研发高响应高精度伺服电机作为负载,采用高性能自主驱动控制单元的转矩、速度闭环控制策略,以及成熟稳定的电网回馈方案,既能实现零转速下的持续扭矩输出,又在节能环保方面独树一帜。具有其它测功机无法比拟的转矩动态响应以及优异的转矩转速控制特性,提升了电机性能测试的高效节能及高可靠性。采用浮动式转速转矩传感器,大幅增大转速转矩采样准确性。该测试平台实现了传统静态测功机无法进行的测控方案,如能量回馈、瞬态加载、反向拖动、转速控制等。测试台结构采用水平、垂直防震一体式台架,被测电机 L 型板与测试台面采用导轨安装及导轨定位技术,保障了被测电机与传感器间的同轴度。
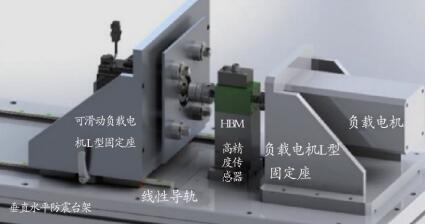
图 1 测试平台整体架构图
二、系统工作原理
测试系统由上位机软件给驱动单元发出转矩指令或速度指令空载负载电机加载,并由高精度传感器上传实时转矩转速信号、功率分析仪检实时输入输出电流、电压、功率、效率并通过PCI 数据采集卡上传至控制软件,软件通过负载电机编码器及采集卡数据信息进行闭环控制,并由控制软件绘制所需实验曲线,进行实验数据处负载电机通过回馈模块实现能源高品质回收再利用。详见图 2 所示工作原理。
三、硬件设计
1. 负载电机选择额定功率为 18.5Kw、额定转速 1500rpm,最高转速 10000rpm,额定电流为 43A 的异步电机 ;
2.选择高精度200Nm数字转矩转速传感器,转速精度 ±0.5,转矩精度 ±0.1,作为测量与控制系统的首要环节,传感器必须具有快速、准确、可靠的性能。
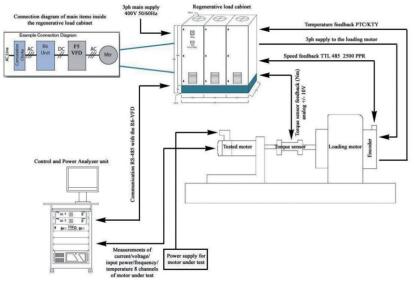
图 2 系统工作原理图
3. 联轴器选用高精度弹性联轴器,保障同轴度稳定性的同时,也能保障扭矩转速的准确传递。
4. 能量回馈单元选用大容量能量回馈单元,全自动负载系统选用自主研发驱动单元实现高精度、高响应的扭矩及转速输出。
5.PID执行单元选用自主研发PLC控制系统,提供更稳定快速的执行各种测试条件。
6. 采用军工级(6 通道)高精度多功能电力分析仪来进行电气参数测试。可同时测试驱动器前端和后端,保障实验数据的准确性。
四、软件功能
测试平台的软件开发与功能设计是十分重要的工作。根据测试需求,系统上位机控制软件系统可以实现下列功能 :
1. 数据采集 : 能与下位机系统建立通讯,实现扭矩、转速、功率、电流等数据互传。
2. 命令发送 : 能将各种测试命令下发至下位机,实现与负载系统、PID 控制系统、功率分析仪主动控制权。
3. 实时数据绘制 : 将采集到的数据进行分析并绘制出曲线。
4. 参数设置 : 对负载控制系统刚性进行 PID调节。
5.状态显示:显示当前测试扭矩、功率、转速、电流、电机实时温度等。
6. 测试项目 : 能够为测试者提供多种不同的测试项目及自动测试方案。
五、软件程序结构
基于以上功能,选择测试程序在 WINDOS系统下使用 Visual Studio 采样用面向使用者编程方法进行开发,软件结构如图所示 :
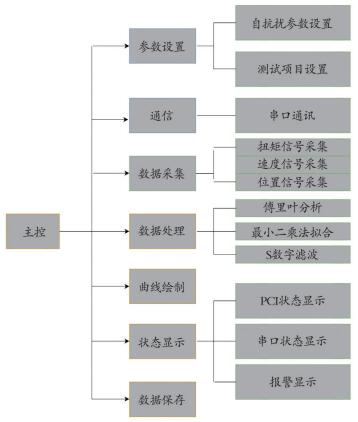
图 3 平台软件程序结构图
测试台程序运行过程如下 : 主程序启动,初始化 PCI 设置、PLC 设置,初始化串口 1、串口2 以及实验中所需的设置 ; 选择测试种类 ; 设置好所需数据和测试项目后开始进入测试阶段。由上位机发送指令给负载电机进行数据采集及曲线绘制。期间可人工停止测试或等待自动测试停止。
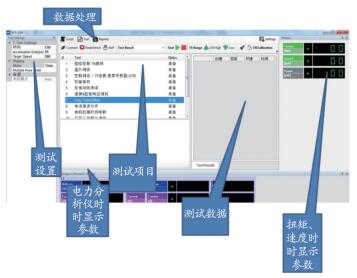
图 4 测试实验平台界面图
对所需数据进行分析,测试结束后选择保存,将本次数据保存。
六、测试项目
1. 手动 / 自动加载,测试负载特性,包括 :扭矩 / 转速 / 电流 / 电压 / 功率 / 效率,通过该测试可准确判定被测电机工作区间分布范围以及电机承受负载的情况,有效的了解电机性能指标。
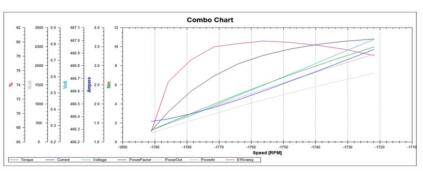
图 5 负载特性测试曲线
2. 驱动器的电流不同负载下的谐波分析测试,测量伺服驱动器输入输出三相电运行情况,能够定量分析伺服系统整体存在的谐波含量、有功使用、无功损耗、功率因数、电压变动、闪变干扰、三相不平衡等指标,能够准确反映整个伺服电机系统的 “健康” 状况。
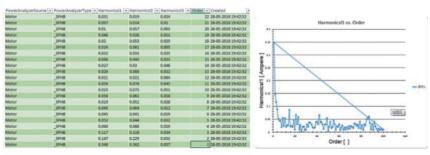
图 6 谐波分析测试曲线
3. 转矩波动测试,由于电机直接用于负载,在运转的过程中,其自身由于齿槽力矩,电磁效应和加工装配工艺等生产的转矩波动将直接传递到负载上,从而对整个伺服电机系统的平稳及控制精度产生影响。尤其在低转速低负载状态下,力矩波动占电机输出力矩比例较大,直接影响电
机控制精度,该测试可在电机出厂前对电机工艺进行精准控制。
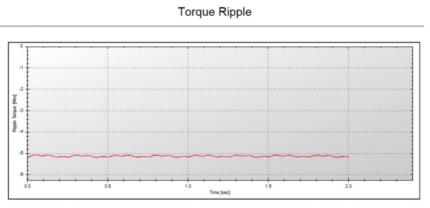
图 7 转矩波动测试曲线图
4. 反电动势测试,电机反电势设计好坏对于电机性能有着直观的影响,低反电势电机驱动器输出电流波形毛刺较大,高反电势电机通过自身电感来抑制磁势变化斜率,通过降低谐波达到降低铁耗,过高的反电势也会由于弱磁角度变化引起电机高速过载能力较弱。通过该测试可直观对比不同电机反电势的差异化。
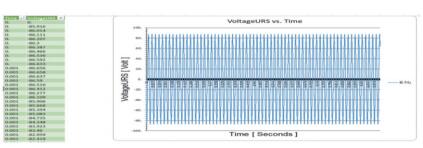
图 8 反电势测试曲线图
5. 交变工况测试,通过自动化编程加载方式模拟电机在不同工作区不同时间交替使用状态,也同时模拟电机在自身不同工作区交替工作时电机绕组温升以及控制精度的稳定性,通过该测试提升电机出厂前的可靠性。
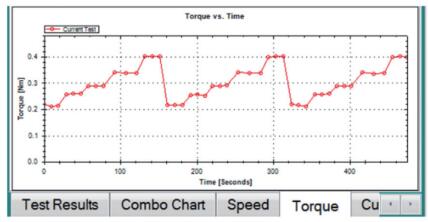
图 9 交变工况测试曲线
七、结论
本文设计并实现了一个用于测试伺服电机性能的自动化测试平台,该系统将计算机、采集卡、传感器等硬件与数据采集、分析以及图形用户界面的应用软件有效的结合,能充分发挥计算机的软件控制能力。利用此平台对特定的伺服系统进行了各种功能测试,测试结果证明,该平台能够按照测试系统设计功能要求,成功及准确的实现伺服电机的测试工作。
投稿箱:
如果您有机床行业、企业相关新闻稿件发表,或进行资讯合作,欢迎联系本网编辑部, 邮箱:skjcsc@vip.sina.com
如果您有机床行业、企业相关新闻稿件发表,或进行资讯合作,欢迎联系本网编辑部, 邮箱:skjcsc@vip.sina.com
更多相关信息