PLC在数控系统中的应用研究
2020-4-15 来源:-- 作者:-
1 、PLC简述
早期的可编程控制器称作可编程逻辑控制器(Programmable Logic Controller,PLC),它主要用来代替继电器实现逻辑控制,为了和PC区别,简称PLC。PLC实质是一种专用于工业控制的计算机,其硬件结构基本上与微型计算机相同,基本构成为a:电源,b:中央处理器,c:处理器,d:接口电路,e:功能模块等。
2 、 PLC在数控系统中的应用
2.1 电气控制系统
电气控制系统是数控机床硬件控制的核心部分,数控机床的电气控制系统,主要由数控装置(CNC)、伺服系统(包括进给伺服和主轴伺服)、机床强电控制系统(包括可编程控制系统和继电器接触器控制系统)等组成。如图1:
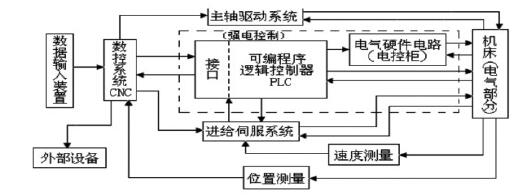
数控装置是数控机床电气控制系统的中枢,它可以自动地对输入到数控机床内部的所有数控加工程序进行处理,同时将这些数控加工程序分成两大类的控制量,分别输出。第一类为连续控制量,这一类的控制量将被输送到伺服系统;第二类为离散的开关控制量,这一类的控制量将被输送到数控机床的强电控制系统。
2.2 电控方式选择
如何选用电气控制方式,直接影响数控系统加工的质量和效率,性能优良的机床电气控制系统可以提高加工产品的质量。因此,需要通过现场的加工要求,选择性价比高的电气控制方式。根据加工对象的特点,合理编制编制程序,最后通过PLC控制系统选择合适的控制方式。数控机床电气控制性能最直接的表现就是运动控制。性能优良的控制系统能够让运动控制发挥更出色的性能、自主编辑性能和以后系统的优化升级。
3、 PLC控制系统常见故障分析
PLC控制系统主要由输入部分、CPU、采样部分、输出控制和通讯部分组成,如图1所示。输入部分包括控制面板和输入模板;采样部分包括采样控制模板、AD转换模板和传感器;CPU作为系统的核心,完成接收数据,处理数据,输出控制信号;输出部分有的系统用到DA模板,将输出信号转换为模拟量信号,经过功放驱动执行器;大多数系统直接将输出信号给输出模板,由输出模板驱动执行器工作;通讯部分由通讯模板和上位机组成。
因为PLC本身的故障可能性极小,系统的故障主要来自外围的元部件,所以它的故障可分为如下几种:
3.1 输入故障,即操作人员的操作失误
a 、传感器故障,b、执行器故障,c、PLC软件故障这些故障,都可以用合适的故障诊断方法进行分析和用软件进行实时监测,对故障进行预报和处理。
3.2 PLC控制系统的故障诊断方法
a、PLC控制系统故障的宏观诊断
故障的宏观诊断就是根据经验,参照发生故障的环境和现象来确定故障的部位和原因。PLC控制系统的故障宏观诊断方法如下:是否为使用不当引起的故障,如属于这类故障,则根据使用情
况可初步判断出故障类型、发生部位。常见的使用不当包括供电电源故障、端子接线故障、模板安装故障、现场操作故障等。
如果不是使用故障,则可能是偶然性故障或系统运行时间较长所引发的故障。对于这类故障可按PLC的故障分布,依次检查、判断故障。首先检查与实际过程相连的传感器、检测开关、执行机构
和负载是否有故障:然后检查PLC的I/O模板是否有故障:最后检查PLC的CPU是否有故障。
在检查PLC本身故障时,可参考PLC的CPU模板和电源模板上的指示灯。
3.3 总体诊断
根据总体检查流程图找出故障点的大方向,逐渐细化,以找出具体故障,如图2所示。
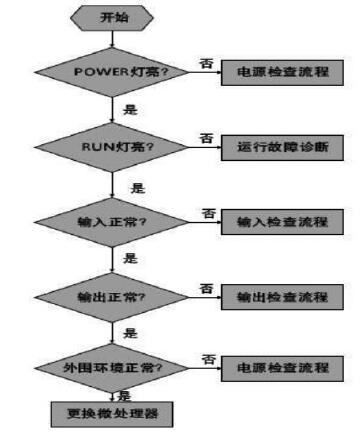
4 、结语
随着科技的不断发展,PLC控制系统在数控机床中的应用会越来越完善,程序也会越来越优化,功能也会更强大,减轻人的劳动强度,提升加工产品的性能,降低废品率,提高生产企业的竞争
力,使企业获得更好的效益。PLC作为当今数控机床中最长用的控制系统,在实际的加工中发挥了巨大的作用,减轻了劳动强度,增加了企业的效益。但是我国的工厂在实际的生产过程中,由于种种原因,自动化的工艺和加工技术水平还较低。因此,通过提高电气控制的设计方法,提高整个行业的加工效率,有着重要的意义。
投稿箱:
如果您有机床行业、企业相关新闻稿件发表,或进行资讯合作,欢迎联系本网编辑部, 邮箱:skjcsc@vip.sina.com
如果您有机床行业、企业相关新闻稿件发表,或进行资讯合作,欢迎联系本网编辑部, 邮箱:skjcsc@vip.sina.com
更多相关信息