数据引发了第四次工业革命
2016-10-8 来源:山高 作者:Patrick de Vos
上海, 2016 年 10 月 - 单从加工角度来看,制造业坚持追求在一定时间内以一定的成本生产出正确精加工的工件,但这种做法已经难以为继。除非出现突破性的刀具解决方案,否则只注重提高金属切除率的传统方法最多只能将产量增加几个百分点。
要想在将来显著提高金属切削的生产率、质量和可靠性,需要仰仗由数据驱动的第四次制造技术革命。新近取得的发展代表着这场漫长革命的最新阶段。制造业的第一次革命使得以家庭为基础的手工制作活动转变为能够利用集中能源为制造机械提供动力的工厂生产。机械轴和皮带将水车或蒸汽产生的动力分配给工厂的机械。接下来,人们又使用了更加便捷、高效的电能。
最初的工厂逐件生产产品。在第二次革命中,单件产品生产演变为批量生产,产量随之扩大。装配线和连续生产线等集成系统的发展以及自动化加速了同种零件的大批量生产。随着数字化机床控制以及后来的计算机化控制和自动化的涌现,制造技术的第三次革命随之到来,不但实现了更高的精度和灵活性,还有利于开展小批量且种类繁杂的零件制造业务。
现在,制造业正在经历第四次革命(在欧洲被称为“工业4.0”),这次革命将当今的数据采集、存储和共享技术整合到了制造工艺中。联网的网络物理系统会分析正在进行的操作,并收集和比较数据以及将信息发送给中央服务器或云服务,以便将其与现有的加工模型进行比较。然后,这些系统利用所得的结果来指导如何调整参数以优化加工工艺。
早期监控系统
数据导向型制造这一概念已经诞生了很长一段时间。在 20 世纪 80 年代,金属加工领域的研究人员就曾设法制造自适应性的刀具监控系统,以测量切削条件、将数据与所设定的工艺标准进行比较并在随后调整加工参数,从而实现工艺的稳定性并最大限度减少意外加工事故的发生。
这些系统采用传感器和探针来测量切削力、功率、扭矩、温度、表面粗糙度及声发射等工艺因素。不幸的是,当时的传感器技术非常落后,无法提供必要的速度和精度以确保完全有效;计算机的处理速度慢,而且需要更大的存储器来实时处理大量的数据。此外,先进的数据采集和管理技术在当时也极其昂贵。
这些缺陷导致几乎不可能在加工期间调整参数。这样就造成了一种鱼和熊掌不可兼得或非此即彼的情况。如果收集的数据超过所设定的最大限值,加工工艺会直接停止。最大限值是在并未充分了解和洞察切削工艺的情况下设定的。除了缺少足够先进的数据处理技术外,还未掌握一个关键的概念,那就是在加工工艺的众多物理现象中,大多数现象—温度、力、负载—都并非静态条件,而是不断变化的动态条件。
例如(图 1.1/1.2),某种加工中的切削力的平均值可能达到 1000 Nm。但在大约一半的时间中,这些力要高于 1000 Nm,并在其余的时间内低于这一水平。如果将系统的停机阈值设置为 1000 Nm,当力看起来过高时,系统将停止加工。(请注意,这些图形显示的是在 8 微秒内执行的测量,以展示力的变化速度有多快。)在 20 世纪 80 年代是不可能进行如此快速的数据处理的。
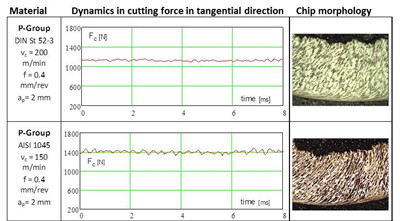
图 1.1:HQ_ILL_chip_morphology_cutting_Part1.jpg
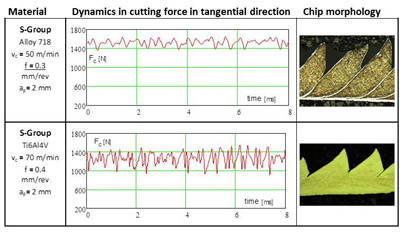
现如今,在将近 40 年之后,传感器和计算机技术在精度、速度和价格方面都有了很大的改观。制造工艺研发本身历经四十个年头,已经积累了丰富的经验并能够非常深入地了解关键的加工要素。
收集和关联加工要素
了解各种工艺要素的作用非常重要。事实上,有 80 多种可测量的要素会影响到加工操作。实现所有这些要素的收集、关联和互动至关重要。如果忽略了某个要素,可能会造成意外且不可控制的影响。
在收集和分析之后,还必须根据每种要素对加工的影响来确定数据的优先顺序。很明显,刀具会产生非常重要的影响。在金属切削中,会搭配使用一组生产工具:机床、CAM 系统、切削刀具、固定和夹紧装置以及冷却液,而在工业 4.0 中,还包括传感器以及数据检索和传输系统(图 2)。
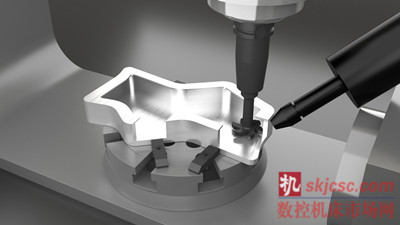
图 2:HQ_ILL_Industry4.0_workpiece_milling_.jpg
金属切削的核心是切削刀具与工件的互动。不过,在传统的加工工艺开发方法中,通常将切削刀具放在最后一位去考虑。当制定工件生产计划时,用户通常首先选择机床,然后是夹具、冷却系统和其他设备,最后才是切削刀具。这就造成了这样一种情况:切削刀具必须弥补其他并非最佳选择的工艺要素的不足。
例如,如果选择了不太稳定的机床,则需要使用切削力较小的切削刀具来补偿稳定性的不足。不过,这种刀具在加工特定的工件材料时可能无法实现最高的生产率。这样,在最后选择切削刀具最终会导致制造系统低于正常水平,虽然能够运行得很好,但无法发挥最大潜力。
幸运的是,制造业中的很多人现在意识到按相反的顺序进行选择更为合适。在考虑成品的形状、特性、工件材料和所需的质量水平之后,车间应当首先选择切削刀具。切削刀具,也就是具体的材料和形状,应当能够实现最高的生产率并满足具体的加工要求。接下来,在选择其他工艺要素时,即可侧重于创造一种环境,让切削刀具充分发挥性能。
平衡的加工
车间选择了加工工艺要素之后,必须平衡这些要素之间的互动,以实现最高的生产率和最低的成本。此外,在加工产量和成本方面,制造业还面临着一些始终没有解决的问题(图 3)。
显而易见的工艺因素包括刀具性能以及刀具成本和加工成本。隐性成本包括由于不可靠的加工工艺生产出质量欠佳或不合格的零件而产生的成本,还包括导致意外停机时间的成本.
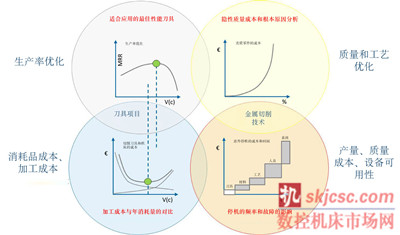
图 3:HQ_ILL_productivity_quality_cost.jpg
尽管编程和维护等计划活动都发生在加工时间以外,但其他因素,例如操作员犯错、刀具破损、工件损坏以及系统问题,都会无谓地导致加工时间变长、成本增加。在损失的时间中,切削刀具只占很小的比例,工件材料和工艺异常情况也是如此。工作人员和系统耗费的时间所占据的比例要高出许多。
工业 4.0 非常重视数字化数据采集、互联网和云存储,但这些元素只是解决方案的一部分。最后,必须分析所收集的数据并制作物理模型或示意图,以说明存在问题的工艺。
在网络物理系统中,会将所收集的数据与示意图进行比较,系统会生成反馈以执行工艺修改,从而产生所需的结果。工艺控制由工作人员以及能够在很短的时间内实时分析数据并将其与模型进行比较的计算机共同完成。
因此,采用云存储技术的模型必须准确说明加工要素。要制作这样一个模型,需要充分了解加工。不幸的是,加工代表着一种很难准确描述的现实情况。例如,模型必须能够识别工件材料的动态属性,因为工件硬度的变化会产生不同的切削力。不过,要测量每个工件的硬度是不可能的。在某些情况下,工件的硬度可能比材料的标称硬度高 10%,导致切削力也要高 10%。
保持人工控制
为了解决这一工艺控制难题,需要在解决方案中建立一个既能够在加工期间学习,也能够自行修正以便越来越准确地说明工艺的模型。不过现在的技术还没有发展到这种程度。
因此,制造工程师必须知道如何设计和制作模型,以确定它是否能够为管理切削工艺奠定坚实的基础。随后,如果通过模型与切削参数进行的互动而选择的参数有问题,工程师需要知道应当基于哪些因素作出选择并确定是否能够将其否决。网络物理系统或许能够控制金属切削工艺,但制造工程师必须保持对网络物理系统的控制。
凭借数十年来积累的丰富现场经验和研究经验,山高制作和提供了极其精确的工艺模型。这些模型在形式上并非是一个封闭的盒子,而是具备为工艺提供指导的内外测试能力,原因在于人们的思想、经验和观点对于制造业新掀起的工业 4.0 革命最终能否取得成功至关重要。
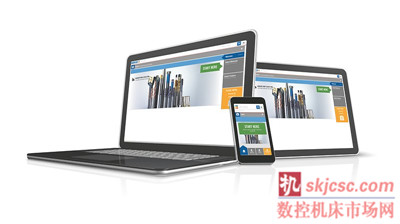
图 4:015644_HQ_IMG_My_Pages_Suggest_Launch_Devices
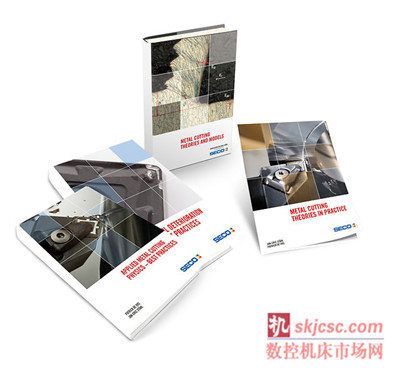
图 5:016538_HQ_IMG_STEP_library_overview_without_background.jpg
(附注)
制造业的循环演变
制造技术在过去的三个世纪取得的进步不但显著提高了生产率,还在近年来大大增强了满足客户特定需求的能力。第一批制造商是在家中为自家人制作衣服、玻璃器具、盆碗和家具的工匠。每件产品都是定制的而且独一无二。那些并不满足于维持生计并具有企业家精神的工匠还会为其他人制作多件他们自制的产品。此后,工匠们开始在公共资源所提供的铁匠铺或玻璃窑等机构中搭伙工作,不但将生产效率提高了很多倍,还
提供了其他的好处,例如技术共享。由于在整个工厂内分配水车动力、蒸汽或电力等集中能源,因此还提高了产量。
早期的工厂每次生产一个零件。装配线的发展揭开了重复生产同种产品的序幕。当装配线将产品从一个工作站送到下一个工作站时,每个工人重复执行单独的一道工序,直到生产出成品为止。这是批量生产的开始:可靠地生产出大量的同种产品—至少符合当时的制造公差。最能体现装配线这一概念的或许是汽车4/5连续生产线,它们每次都生产出数以千计的同种零件,而且夜以继日地持续运转多年。
产品营销的兴起颠覆了批量生产方案。在资本主义竞争进入白热化期间,营销商力求提供经过改造的产品以满足小型细分市场的需求,从而扩大自己的客户群。
一个完美的范例是,早期的汽车制造商摒弃了福特 T 型汽车“你想要什么颜色都可以,只要它是黑色”的营销理念,转而为客户提供越来越丰富的颜色和选择。为了满足这种个别客户的需求,制造商必须机动灵活,并设法高效地在不同的制造工艺之间切换。通过穿孔纸带实现的数字化机床控制以及后来的计算机化数控可以快速、可靠地更换工艺和刀具。与此同时,加工能力更强的自动化系统能够缩短零件的处理时间和降低人工成本。
在过去的几十年间,能够通过按几下按钮就生产出不同的零件或零件特征的 CNC 制造车间基本上取代了可靠但难以改造的连续生产线概念。
消费品营销领域的趋势清楚地表明了计算机为制造业带来的灵活性优势。只需对生产线的要素进行重新编程,营销商即可实现很多的品牌延伸。向个性化发展的趋势并非只限于制造业。例如,大型零售商在开设更加小型化的专卖店,以满足个别客户对便利性和产品偏好的需求。
制造业产品的个性化只会变得越来越普遍。与工业 4.0 的实施过程类似,采用云服务的模型可能会利用营销信息来管理产品更迭、自动化和库存水平。与采用云服务的切削工艺系统的运行方式类似,营销人员也依然需要密切关注这些营销驱动型制造系统,并确保这些系统作出的决策合情合理。采用最近新涌现的制造技术,个人在家中就能够生产出定制的零件。因此,就像几个世纪前的工匠们所制作的产品一样,在数字信息的推动下循环演变的制造业现在能够在工厂之外生产出独一无二的产品,但在精度、质量和速度方面已经不可同日而语。
投稿箱:
如果您有机床行业、企业相关新闻稿件发表,或进行资讯合作,欢迎联系本网编辑部, 邮箱:skjcsc@vip.sina.com
如果您有机床行业、企业相关新闻稿件发表,或进行资讯合作,欢迎联系本网编辑部, 邮箱:skjcsc@vip.sina.com
更多相关信息