IMS 系列伺服控制器和TSM 系列交流异步伺服电机在齿轮机床上的应用
2015-4-5 来源: 天津第一机床总厂 作者:杜鸿起
摘 要 本文介绍将IMS系列伺服控制器和TSM系列交流异步伺服电机的新技术应用到齿轮机床,做为刀具主轴驱动的新方法。由此使数控铣齿机和数控插齿机刀具主轴的控制技术升级。1.实现了数控铣齿机用手轮脉冲发生器(简称“手脉”)控制刀具主轴调整找正刀具的功能,解决了铣齿机长期以来机械手动找刀的问题,提高了机床自动化程度和工作效率,降低了工人劳动强度。2.利用强劲转矩特性、过载能力强的优点,取消铣齿机原有的刀具主轴驱动挂轮箱,缩短机械传动链,解决了机床噪音大、加工精度偏低的问题,降低了机床成本。3.利用低速大转矩输出、零速力矩锁定、电机准停功能实现数控插齿机刀具主轴上停功能和工件的准确对刀,解决了插齿机机械抱闸装置上停不可靠、机床维修不方便、工件对刀不准确的问题。
一、引言
设计数控铣齿机、数控插齿机时考虑到机床成本,刀具主轴驱动一般不采用NC伺服模块主轴驱动,而采用交流变频器和变频电机驱动。由于变频电机的特性软,需要靠机械传动的升降速来满足刀具主轴的转速和带载能力,造成机床的传动链长,噪音大,累计误差大,加工精度偏低。交流变频器没有”手脉”输入接口,实现不了刀具主轴的“手脉”控制功能。变频电机没有零态转矩和准停功能,数控插齿机只能靠机械抱闸实现刀具主轴上停动作。现在急需一种新型低成本的控制元件做齿轮机床的刀具主轴驱动。
二、交流变频控制与交流异步伺服控制做刀具主轴驱动的分析比较
1.控制功能的分析比较
从表一可以看出交流异步伺服电机安装编码器,控制器可对其位置、速度、加速度、转矩进行高精度控制,控制系统可实现低速大转矩输出,零速力矩锁定功能,这些控制功能都是齿轮加工机床需要的,而交流变频器无法实现。
2.交流变频器与交流异步伺服的转矩特性比较
从图一可以看出,变频驱动电机转矩特性软,需要靠机械传动来满足刀具主轴的运动要求。变频器在低于5HZ时,电机有转动死区,而交流异步伺服电机转矩特性硬,低速大扭矩输出,电机没有转动死区,最大转矩可以达到电机额定转矩的3倍。
3.成本分析比较
通过表二看出使用国产交流异步伺服控制器降低了机床成本。
三、IMS系列伺服控制器与TSM系列交流异步伺服电机在齿轮加工机床上的应用实例及效果
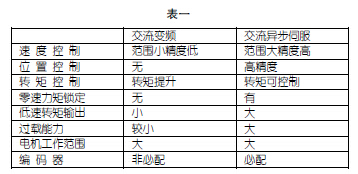

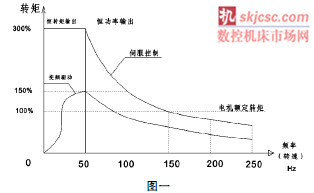
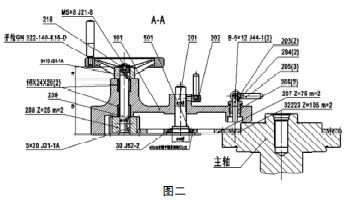
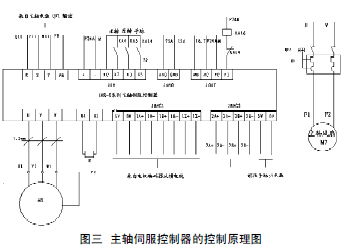
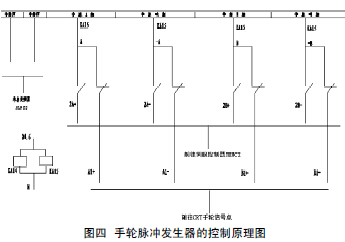
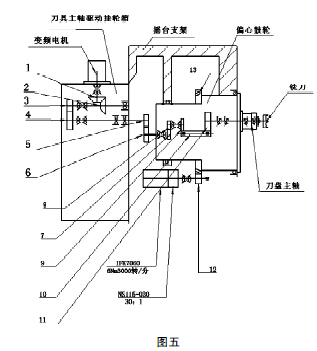
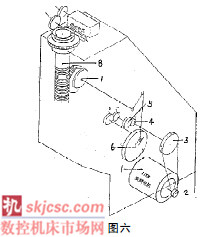
1.实现数控铣齿机“手脉”控制刀具主轴调整找正刀具的功能数控铣齿机在精铣齿轮时,为保证齿轮加工精度,必须找正铣齿刀头的刀高和径向跳动在0.002以内。
使用交流变频器作刀具主轴驱动,没有“手脉”输入接口,低速转动有死区,只能用机械手动调刀装置实现调刀。以YK2232A机床为例(见图二),转动机械手轮,经过208 — 207 — 32223齿轮传动使刀具主轴转动。人工手摇机械传动部件找正铣齿刀,劳动量大,需要多半天时间,费时费力,效率低。再加上齿轮传动间隙大,手摇有撞击,运动不平稳,调刀精度差,影响零件加工精度。
IMS 系列伺服控制器有“手脉”输入接口,利用控制器的“脉冲控制”功能,用“手脉”控制刀具主轴的转速及方向,还能准停到位,实现铣齿刀的找正调整,调刀只需要1-2小时,效率高,劳动强度低。
(1)“手脉”功能的控制原理(图三)、(图四)
A.使用刀具主轴“手脉”功能进行调刀时,接通操作面板按键,使输出信号Q4.6=1,这时中间继电器KA14、KA15同时吸合,KA14接通“手脉”使能X5,同时断开速度到达信号Y3(为防止“手脉”摇动时,速度到达控制继电器频繁通断损坏),中间继电器KA15吸合,其开点使手轮脉冲发生器与主轴伺服控制器的JENC2端子连接。这样就可以实现手轮脉冲发生器控制主轴的正反转及转速。
B.不使用刀具主轴“手脉”功能进行调刀时:断开操作面板按键,输出点Q4.6=0,KA14、KA15 断开,KA14 使“手脉”使能X5 复位,速度到达信号Y3有效,主轴使能由主轴伺服控制器JIN的端子X2、X3控制,主轴速度由系统给出的(0-10V电压)的模拟量到主轴伺服控制器的JANO端子的AN0 和GND控制。这时KA15的闭点使手轮脉冲发生器与数控系统连接,从而控制系统的NC轴的运动。
(2)“手脉”调刀功能取得的效果
A.结束了铣齿机靠机械传动手动调刀的历史,实现了机床的自动化,增强了机床功能特性。
B.降低了工人劳动强度,提高工作效率5-6倍。
C.提高了找刀精度,保证了零件加工精度。
D.取消了机床原有的机械手动调刀装置,降低成本4000元/台,实现了机床的降本增效,提高了机床的市场竞争力。
E.刀具主轴“手脉”调刀功能已推广到各系列的数控铣齿机上,为企业创造了可观的经济效益。
2. 取消YK2212A数控铣齿机刀具主轴驱动挂轮箱机械结构,解决机床噪音大、加工精度偏低的问题
(1)原有刀具主轴机械传动结构
YK2212A机床为满足1.1吋~3.5吋铣齿刀盘的使用,保证变频电机有很好的转矩特性,克服变频电机速度控制范围小精度低的缺点,设计了刀具主轴驱动挂轮箱结构(见图五)。运动由变频电机输出, 经弧齿锥齿轮1、2 和圆柱齿轮3-4-5-6-7-8-9-10-11 传动,使刀具主轴旋转。转速的改变由交换齿轮3和4及变频电机的调速来完成。刀具主轴高速旋转时,机床燥音很难控制到83dB以下,用户意见大。而且传动链长,故障率高,传动累计误差大,切齿精度不易保证,机床市场竟争无优势。
(2)改进后的刀具主轴机械传动结构
选用TSM-1P5C22伺服电机和IMS-SCT41P5WG-NN伺服控制器做刀具主轴驱动,利用电机转矩特性硬,低速大转矩输出,过载能力强,速度控制范围大精度高的特点,取消刀具主轴驱动挂轮箱结构(取消弧齿锥齿轮1、2和圆柱齿轮3-4-5-6传动)。由伺服电机输出, 经圆柱齿轮7-8-9-10-11 降速传动,使刀具主轴旋转,达到转速要求。机床经过重切试验,,电机带载能力完全满足机床使用要求。
(3)取得的效果:
A.大大降低了机床噪音(800rpm运行时,由83dB以上降到70dB以下;400-500rpm运行时,机床燥音在65dB以下),改善了机床工作环境。是机床技术的重大突破。
B.机床切齿精度容易达到GB/T 11365-1989标准的5-6级,比原来提升1—2级,解决了原有机床切齿不容易合格的问题。
C.每台机床降低成本2万元,实现了机床的降本增效,提高了机床的市场竞争力。
D.成功经验正在推广应用到同类产品。
3. 实现数控插齿机刀具主轴上停动作和准确对刀功能数控插齿机刀具主轴往复插削运动中一个特殊动作就是刀轴上停,其作用使插齿刀停在高出加工工件端面的固定位置,保证加工工件安全退出。尤其是插内齿工件,上停动作更为必要。
(1)刀具主轴结构的改进
YK58A刀具主轴运动(见图六),由变频电动机1输出, 经皮带轮2、3 —齿轮4、5 —交换齿轮a、b(两档,满足刀具主轴不同冲程要求)—曲柄连杆机构6—扇形轮7传动,使刀具主轴8上下往复运动。在皮带轮3处安装电磁离合器机构(机械抱闸)。上停动作通过控制机械抱闸实现。机床传动皮带是易损件,定时要更换,更换皮带必须将电磁离合器机构先拆下再装上。工人工作量很大,需要一天多的时间,不便于机床机械维修。切削工件时由于刀具主轴传动惯性大,不易使刀具准确停在对刀位置上。使用主轴伺服控制器后,取消了电磁离合器装置,利用伺服控制器的电机准停和准停到位功能实现了刀具主轴上停动作。并且利用伺服控制器的零速伺服和零速到达的功能,使切削刀具能够准确停在工
件的对刀位置上。
(2)取得的效果:
A.实现了刀具主轴准确上停动作,解决了机械抱闸上停不可靠的问题。
B.便于工件对刀,解决了因传动惯性大不易使刀具准确停在对刀位置上的问题。。
C.解决了机床的装配和机械维修不方便的问题,降低了工人的劳动强度,提高了工作效率。
D.降低了机床制造成本8000元/台,实现了机床的降本增效,提高了机床的市场竞争力。
四、结束语
通过以上3个改进实例说明,应用IMS系列伺服控制器和TSM系列交流异步伺服电机新技术做齿轮机床的刀具主轴驱动,为数控铣齿机、数控插齿机的刀具主轴控制带来了飞跃性的技术升级。不仅增加了机床功能特性,提高了机床自动化程度和工作效率,解决了机床的噪音大、零件加工精度偏低、机械维修不方便等问题,而且降低了机床制造成本和工人的劳动强度,实现了机床的降本增效,提高了机床的市场竞争力。
投稿箱:
如果您有机床行业、企业相关新闻稿件发表,或进行资讯合作,欢迎联系本网编辑部, 邮箱:skjcsc@vip.sina.com
如果您有机床行业、企业相关新闻稿件发表,或进行资讯合作,欢迎联系本网编辑部, 邮箱:skjcsc@vip.sina.com
更多相关信息