三坐标测量机测量同轴度的方法讨论
2023-7-14 来源: 上海航天控制技术研究所 作者:邹昊生 冯加印
【摘 要】: 三坐标测量机作为一种先进的检测设备 , 具有自动化、高效率、高精度的特点 ,在科研生产活动中发挥着重要作用。然而在同轴度测量中 , 经常出现测量值与理论值偏差大、测量重复性差的问题。本文分析了同轴度误差产生原因 , 介绍了直接测量法、公共轴线法、直线度法、投影法等测量方法 , 指出了每种测量方法的特点和使用环境 , 并对同轴度标注、检测提出了建议。
【关键词】: 同轴度 ; 三坐标测量 ;
测量误差同轴度检测是尺寸测量的重点之一。针对不同类型的零件,GB/T1958—2017给出了不同的解决方案 , 详细介绍五种典型同轴度检验操作示例。但 GB/T1958-2017给出的方案均为传统的形位误差测量方法 , 测量过程中需要借助直板尺、平板、芯轴等辅助工具进行。传统测量方案不仅需要额外硬件投资 , 还耗时耗力 , 测量误差影响因素较多 , 对于一些大型或不规则零件 , 采用常规方法测量同轴度更难以实现。
三坐标测量机可以在保证检测工作效率的前提下 , 检 测不同零件的具体尺寸、精度 , 而被广泛的应用在各个行业。 但在实际测量过程中 , 由于设计意图传递不准确 , 操作人员对三坐标测量原理不到位 , 难以正确地选择测量方法 , 容易造成测量误差大、测量重复性差等问题。针对这一现象 , 为保证检测结果真实、准确、有效 , 本文对三坐标测量方法的原理进行分析 ,并对已有检测方法进行说明、改进 , 力求得到更加科学合理的检测结果。
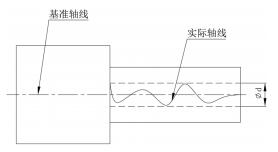
图 1 同轴度误差
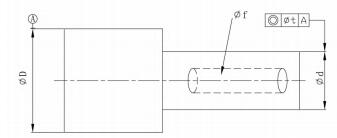
图 2 同轴度公差
1. 同轴度坐标测量原理
1.1 同轴度定义
同轴度误差 : 要求在同一直线上的两根轴线 ,实际生产加工过程中会发生偏离 , 它们之间偏离量的值 , 如图 1 所示 ,Φd 为同轴度误差。
同轴度公差 : 公差值前标注符号 Φ, 限制被测轴线在 以基准轴线为轴线、以 Φf 为直径的区域内 , 如图 2 所示 , Φf 为同轴度公差。
1.2 同轴度误差解析模型
实际测量中 , 首先应确定基准轴线。基准轴线是通过测量基准圆柱面上的轮廓要素 , 拟合出的具有理想形状的直线。 具体方法如下 :
(1) 在基准圆柱面上取多个与基准轴垂直的截面 , 采集截面数 n ≥ 2;
(2) 对各截面进行测量 , 每个截面上均匀采集 m 个离散点 , m ≥ 3, 采集点数越多 , 截面越接近于实际轮廓形状。
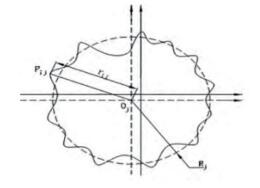
图 3 第 j 个截面上的采样点
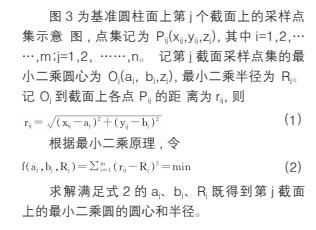
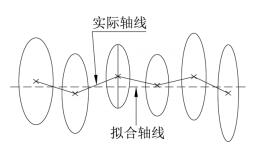
图 4 各采样截面拟合圆心与最小二乘轴线
(3) 连接各截面上的圆心 Oj 行成一条 3D 折线 , 如图 4 所示 , 选取截面数越多 , 则该折线越近似基准圆的实际轴线 , 记其最小二乘轴线L的方向向量为 ,L与XOY的交点为J0(x0,y0,0), 记 Oj 到 L 的距离为 dj, 则

(4) 在被测圆柱面上取 w 个截面 , 记各截面最小二乘拟合圆心为 ck,k=1,2,……,w。各圆心 ck 到基准轴线 L 的距离为 distk, 则同轴度误差 ε 为

1.3 三坐标测量同轴度误差的实现
使用三坐标测量机时 , 一般首先测量基准元素 , 并以此为基础 , 建立工件坐标系 ; 然后测量其他几何元素 ; 最后得出测量结果。三坐标测量机进行测量时 , 一般按如下步骤进行 :首先 , 建立零件基准 , 并按此基准建立零件坐标系。同轴度基准的建立 , 应根据零件的图纸标注来确定,可参考 GB/T1958—2017的规定。一般情况下 , 同轴度测量时选择内孔或外圆柱面的轴线作为基准轴。建立坐标系时 , 至少需要采集两个截面圆 , 每个截面圆至少选取 3个 点 , 各点应均匀分布 , 三坐标测量机软件根据内部算法 , 自动生成一条轴线 , 然后作为坐标系的基准轴。
其次 , 采用同样的方法测量被测要素 , 被测要素各截面应均匀分布 , 并尽可能覆盖被测要素。测量完毕 , 最终生成一条被测轴线。最后 , 得出测量结果。测量结果一般由三坐标测量机软件自动计算 ; 还可以按最小条件 ,通过被测要素与基准要素的关系手动计算。
按上述三坐标测量步骤 , 当被测要素与基准要素相距较远、两者又比较短时 , 理想值与测量值会有很大偏差 , 测量重复性也很差。
2. 测量误差源探究
测量结果会受到人为因素、设备系统误差因素、测量方法因素等的影响 , 从而导致测量结果与真实数据之间存在差值 , 即测量误差。一般情况下极限测量总误差允许占给定公差值的 10%~33%。测量误差越小 , 测量结果越接近真值。因此 , 在确定测量方案前 , 首先应评定测量 误差来源 , 采取措施消除、减小测量误差至合理范围。
产生测量误差的主要原因包括 : 测量设备本身的系统性误差 ( 如设备结构误差、软件计算误差等 )、测量条件引起的误差 ( 如地面振动、装夹方式、温度条件等引起的误差 )、测量方法引起的误差。由于三坐标测量机各部件有较高的刚度 , 变形小 , 测量环境要求较高等原因 , 测量机系统误差、环境条件引起的误差可以忽略不计。本文主要研究测量方法引起的误差。在实际测量过程中 , 直接采用测量软件进行计算 , 测量结果往往与理论值有很大差距。
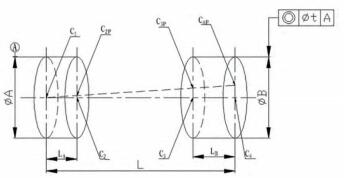
图 5 基准轴线延长至被测要素时引入测量误差示意图
如图 5 所示 , 在基准 A 两端覆盖最大基准范围的位 C1、C2 两个截面圆作为基准轴线 ; 同理 ,在被测圆柱面上取 C3、C4 两个截面圆。理想状态下 , 基准轴线 C1C2 和被测轴线 C3C4 应为同一条直线 , 同轴度理论值为 0。但是 , 由于测量机的系统误差、人为因素、环境因素等的影响 , 基准轴线存在测量偏差C2C2P, 在计算同轴度时 , 根据同轴度定义 , 基准轴为 C1C4P, 同轴度为 C3C4 与 C1C4P 之间的最大距离 , 由三角形相似性原理得 :
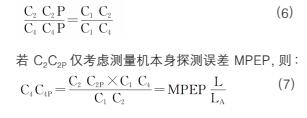
上述分析说明 , 当被测要素与基准要素本身较短、距 离较远时 , 测量误差会被放大。 因此 ,某些情况下 , 使用三坐标测量软件直接测量、计算同轴度时 , 应对测量误差进行评定 , 确保测量误差不会被放大。
采用 GB/T1958-2017 中所述的传统测量方法 , 可借助芯棒 , 若芯棒与孔 A、孔 B 正确装配 ,则孔 B 的同轴度合格 , 若不能正确装配 , 则同轴度超差。但借助芯棒 , 无法确定同轴度具体数值 ,只能给出合格与否的结论。
在实际测量过程中,为减小三坐标测量误差,一方面 , 应尽量增加基准要素、被测要素截面数、截面间距、增加各截面的取点数、各点之间尽量均匀分布 , 以减小基准轴线、被测轴线偏离程度 ,逼近实际形状 ; 另一方面 , 当图纸与技术条件中无特殊要求说明时,则以尺寸较大的方向为基准。
3.合理选择测量方法
实际测量过程中 , 同轴度公差各不相同 , 在采用三坐标测量时应根据基准要素作用范围、零件设计意图、零件具体形态等具体条件 , 从以下方案中选择合适的测量方法。
3.1直接测量法
当基准要素作用范围较长 ( 如图 6 所示 ) 或基准作用范围延长引起的误差较小 , 即公式 (7)的值较小 , 在可接受范围内时 , 可由三坐标测量机直接计算同轴度误差。
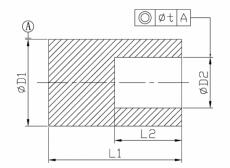
图 6 被测要素在基准要素作用范围内
3.2公共轴线法
当被测要素法和基准要素相距较远时 , 如图5 所示 , 可以采用公共轴线法。
具体检测方案 : 在被测要素、基准要素上选取多个截面圆 ; 然后模拟零件装配状态 , 将这些截面圆心拟合成一条 3D 公共轴线 ; 最后以该 3D公共轴线为基准 , 分别计算 基准要素和被测要素同轴度 , 取最大值作为该零件的同轴度误差。当被测要素与基准要素距离较远时 , 该方案效果非常明显。
公共轴线法是模拟零件实际装配状态。 在公差标注时 , 为准确传递设计意图 , 可以参考GB/T1182-2008 的 标注方式 , 如图 7 所示。
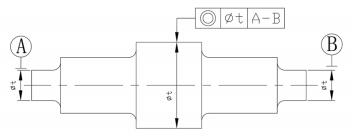
图 7 基准标注为公共轴线
3.3测直线度法
实际测量工作中 , 会遇到由 3 个及以上截面孔构成的孔系 , 尤其当单个孔工作截面较短时 , 同轴度误差测量更加困难。此时可以用直线度公差值代替给出的同轴度的公差值。
具体检测方案 : 根据各孔轴线长度 , 确定该孔采集截面圆的数量 , 轴线越长 , 截面圆越多 ;所有孔元素截面圆采集完成后 , 把所有截面圆心拟合成一条 3D 轴线 ; 计算该 3D 轴线的直线度 ; 直线度值的 2 倍作为孔系同轴度误差。图 8可按照此评价方法进行检测。
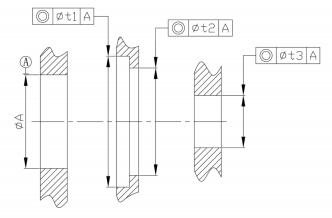
图 8 孔系同轴度测量示意图
从本质上来说 , 直线度法与公共轴线法都是模拟芯轴穿过孔的零件装配状态 , 能较好地反应零件装配性。轴心连线的直线度能控制各孔轴心的偏移量 , 进而影响零件的装配性能 , 因此 , 孔系各轴心连接线的直线度能反应零件同轴度。截面孔轴线越短 , 各孔间距越大 , 该测量方案效果越好。
3.4 投影法
实际生产过程中 , 孔轴装配也会用零件端面进行定位 , 若轴间距 ( 只有一个轴或孔时 , 则是轴长或孔长 ) 大于端面尺寸时 ,则以轴线为基准 ;反之 ,则以端面为基准。如图 9 所示 , 基准要素与被测要素轴长均小于端面尺寸 , 此时可以将端面作为基准平面 , 将被测要素、基准要素投影到基准平面上 , 取其圆心距离的两倍作为零件的同轴度。
这个基准平面必须与被测要素、基准要素垂直误差不大于 0.02。可以将基准要素、被测要素上任一截面圆投影到基准平面上 , 以同心度代替同轴度。
针对这种端面定位的同轴度公差 , 为避免不必要的理解差异、更准确的传递设计意图 ,在公差标注时可以参考 GB/T1182-2008按两基准体系标注 , 如图 9 所示。
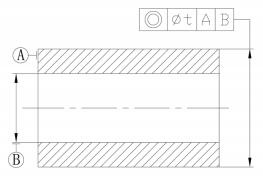
图 9 两基准体系标注
4. 结语
检测方法多种多样 , 应根据不同零件的结构、图纸设计要求 , 来确定合理的测量方案。确定测量方案时 , 还应充分考虑并减小各种因素造成的测量误差 , 保证测量的准确性。在进行零件设计时 , 应遵守相关标准的要求 , 准确表达设计意图。只有这样 , 才能更准确的把握设计意图 , 得到精确的检测结果 , 真实反映被测件的状态。
投稿箱:
如果您有机床行业、企业相关新闻稿件发表,或进行资讯合作,欢迎联系本网编辑部, 邮箱:skjcsc@vip.sina.com
如果您有机床行业、企业相关新闻稿件发表,或进行资讯合作,欢迎联系本网编辑部, 邮箱:skjcsc@vip.sina.com
更多相关信息