转向助力器扭杆自动压拔校直设备研制
2014-3-19 来源:数控机床市场网 作者:
摘要:根据转向助力器扭杆压拔校直工艺的要求,研制出一种自动压拔校直设备,采用专用夹具提高系统精度,克服了传统工艺工效低、装配精度低等缺点。该设备在自动压拔校直时,以PLC为控制系统核心,与HMI协调作用,可修改、设置相关参数,确保扭杆压拔、校直的效率及合格率。
扭杆压拔校直设备是用来将扭杆压入连接轴,并对其进行拉拔测试,与此同时,对完成压拔工艺的扭杆组件进行测量、校直的设备。此前,扭杆与连接轴通过圆柱销连接,扭杆为光杆,连接轴为光孔,为过渡配合。因此,在将扭杆压入连接轴后,应再打孔用销子贯穿以达到固定的作用。如此工艺较为繁复,且不易实现自动化作业。目前的工艺为扭杆与连接轴之间采用过盈配合,且扭杆在连接处被加工成花键,将原来的弹性变形改为塑性变形,通过过盈配合产生足够的过盈力来起到牢固连接的作用,省去打孔穿销的工艺,使工艺简化,提高效率。需要进行压拔校直的扭杆、连接轴及压装好的扭杆组件如图1所示。
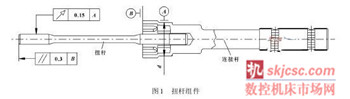
1 扭杆压拔校直设备机械系统
扭杆压拔校直设备分为压拔工位和测量校直工位。拉拔工位完成扭杆的压装工艺和拉拔测试工艺,测量校直工位完成扭杆组件的检测工艺和校直工艺。虽在同一设备上,压拔工位与检测校直工位却可以同时工作,而不影响系统精度。该设备的机械结构见图2。
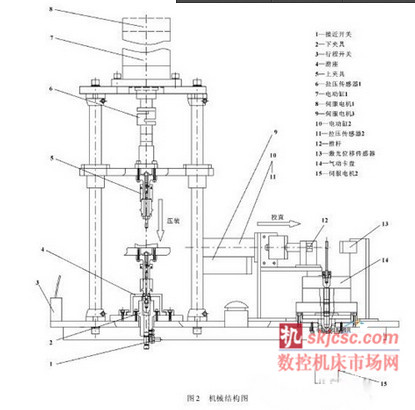
1. 1 扭杆压拔系统
扭杆压拔系统由伺服电机1、电动缸1、拉压传感器1、上夹具、下夹具、滑座、接近开关、行程开关等组成。
扭杆压拔系统的动力由伺服电机1提供,通过电动缸1将旋转运动转化为直线运动,安装在电动缸1端部的拉压传感器1则及时向PLC传递受力信号。上夹具用于装夹待压装扭杆,下夹具用于放置待压装连接轴。接近开关用于检测连接轴是否装夹到位,若无装夹正确信号则无法进行压拔工艺。滑座则是在完成压装工艺后、进行拉拔测试之前伸出,挡住连接轴,使得拉拔测试得以进行;并在完成拉拔测试后退回,使拉拔测试后的工件得以取出。行程开关是在工件装夹都完毕且全部正确时的一个开始开关,拨动行程开关设备开始自动进行压拔工艺。
1. 2 扭杆测量校直系统
扭杆测量校直系统由伺服电机2、电动缸2、拉压传感器2、顶杆、伺服电机3、气动卡盘、激光位移传感器等组成。
扭杆测量校直系统由测量系统和校直系统两部分组成。压拔结束的扭杆组件都需测量其跳动量,检查是否在合格范围内,测量系统正是为了实现这一功能而设计的。若所测量得的跳动量大于指定值X,则由校直系统进行校直,使扭杆组件合格。
测量系统由伺服电机2、气动卡盘、激光位移传感器等组成。气动卡盘用于装夹待测扭杆组件,卡盘的高精度保证了测量数据的可靠性。激光位移传感器用于测量待测组件到传感器的距离。在装夹完组件后,激光传感器自动检测该距离,若在指定范围内则自动夹紧,并由伺服电机2提供动力带动卡盘旋转一周。激光传感器始终自动检测组件距离并及时传递到PLC,通过PLC中一系列的运算得到组件的跳动量。
若是超过指定值X则需进行校直。校直系统由伺服电机3、电动缸2、拉压传感器2、顶杆等组成。伺服电机3提供动力,电动缸2将伺服电机的旋转运动转化为直线运动后带动推杆对扭杆组件进行校直。安装于电动缸2端部的拉压传感器2用于检测推力的大小并及时传递到PLC,这个力是校直工艺结束与否的一个判断条件。
2 扭杆压拔校直设备的电控系统
2. 1 控制系统硬件设计
该扭杆压拔校直设备可实现手动和自动功能,它由可编程逻辑控制器( PLC)、伺服电机及人机交互界面( HMI)等组成。其中PLC是整个控制系统的核心,遵循经济、可靠、安全、合理的原则,选用欧姆龙CP1H系列CP1H - XA40DT - D[1]。HMI选用欧姆龙NS系列的NS12 - TS00B - ECV2,此款HMI的屏幕尺寸为304. 8 mm ( 12英寸),且满足人机交互的需要[2 -3]。激光位移传感器选用欧姆龙ZX - LD40,微米级的测量精度,确保整套系统数据的准确性。伺服电机选用三菱系列。其他硬件根据性能可靠并遵循经济、安全、合理的原则适当选取。根据控制扭杆压拔校直的具体要求,其系统框图设计如图3所示。
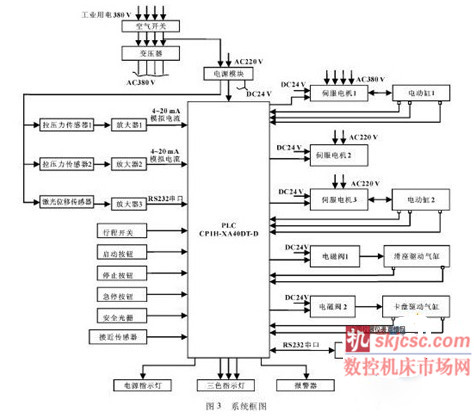
2. 2 控制系统软件设计
2. 2. 1 压拔控制原理
压拔开始之前需先使各部件复位,即使电动缸1回到零位,滑座回到零位。复位完成后装夹好工件,拨动行程开关开始自动压拔。系统复位可通过点击HMI上的“停止复位”按钮来完成。在做拉拔测试时,将判断能承受8 kN以上的力变换为判断拉拔至8 kN力时扭杆的位移量不超过指定值。判断拉拔力的大小是为了确定压装后扭杆与连接轴之间的松紧程度,力越大则越紧;反之,力过小,则在使用过程中容易松脱,存在安全隐患。用相同的力拉拔,连接越是紧凑的扭杆拉拔位移越小。由此可知,将力判断方式改为位移判断方式可行。具体的位移阈值则通过试验得到。该设备的自动压拔流程图如图4所示。
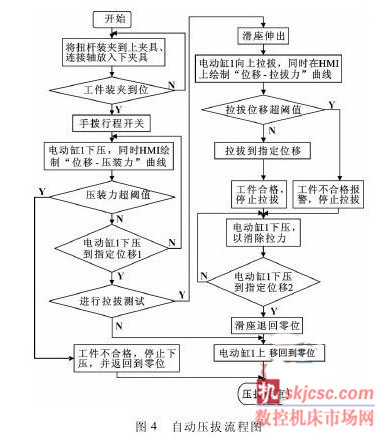
2. 2. 2 测量校直控制原理
测量校直开始之前需先使各部件复位,即使电动缸2回到零位,气动卡盘处于松开状态。系统复位可通过点击HMI上的“停止复位”按钮来完成。复位完成后将压装好的扭杆组件放入三爪卡盘中,激光传感器将自动检测扭杆组件的距离,在指定距离范围内则卡盘自动夹紧,同时伺服电机2开始旋转,即系统自动夹紧并测量。测量完成后,会根据一圈内所测得的距离数据计算工件的跳动量。比较工件的最大跳动量Xmax与指定值X,若Xmax< X,则扭杆合格;否则判为不合格,系统自动开始校直。校直完成后系统开始第二轮测量,并判断合格与否。如此反复,直至校直到合格范围,或者校直次数超过指定次数N。经过试验并调整不同跳动量区间所对应的校直力,目前可稳定在3次以内将所有扭杆校直,即该设备加工出来的扭杆组件合格率达到了100%。该设备的自动测量校直流程图如图5所示。
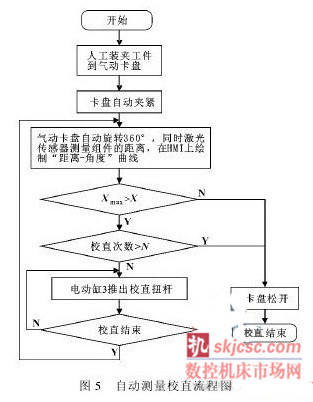
3 结束语
该扭杆压拔校直设备以PLC为控制核心,通过HMI进行人机交互,依靠伺服电机达到精确定位,通过激光传感器完成微米级的测量。扭杆压拔的合格率达到设计要求,并能在指定次数内将所有扭杆校直到合格范围,生产出的扭杆组件合格率达到100%。该设备实现了扭杆压拔及测量校直的自动化,极大地减轻了压拔校直的劳动强度。目前,该设备已投入使用,使用效果很好。
投稿箱:
如果您有机床行业、企业相关新闻稿件发表,或进行资讯合作,欢迎联系本网编辑部, 邮箱:skjcsc@vip.sina.com
如果您有机床行业、企业相关新闻稿件发表,或进行资讯合作,欢迎联系本网编辑部, 邮箱:skjcsc@vip.sina.com