五坐标龙门加工中心加工零件表面粗糙度差的原因分析
2020-12-14 来源:昌河飞机工业(集团)有限责任公司 作者:林超青
摘要:公司一台五坐标龙门加工中心在加工时零件表面波纹严重,表面粗糙度严重超差,无法满足工艺要求。零件表面粗糙度差的成因比较多,解决难度大,本文对该机床零件加工表面粗糙度差的原因和处理措施进行一些探讨。
1、问题分析
某五坐标高速龙门加工中心前期进行了五轴头翻新大修,机械及电气部件均有更新,在零件试加工过程中发现,加工的零件表面波纹严重(见图1),表面粗糙度极差,完全无法满足工艺表面粗糙度的技术要求。
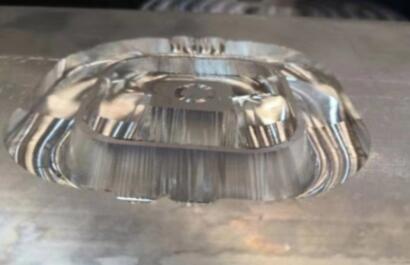
图1:表面波纹严重的零件
零件加工表面粗糙度差的原因比较多,零件加工程序编制不良或机械部件磨损,运动部件的间隙增大,机械刚性下降,龙门同步超差,电气参数与机械部件的机械特性不匹配,伺服优化不好等因素,都会导致坐标轴运动时无法快速准确定位。机床来回寻找定位位置导致伺服系统振荡或系统电气响应速度慢,造成零件加工表面出现波纹,表面粗糙度超差。电气调试和伺服优化主要是针对机床的三环控制系统进行(见图2)。
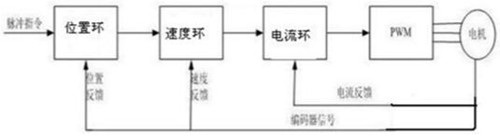
图2:机床三环控制
从图2可以看出,机床电气特性一般包括三环特性,由一系列电气参数设定,比如速度环、位置环增益等。如果速度环、位置环的增益设定值较大,系统响应就较快,能够较快达到稳定状态,机床加工时零件表面质量也会相应提高。但是如果速度环、位置环的增益设定值太高,就会造成系统振荡,无法达到稳定状态,机床出现抖动,电机啸叫,加工时零件表面出现波纹;速度环、位置环的增益设定值过小,则机床响应速度降低,零件加工时表面也会出现波纹。图3是指令响应及稳定过程。
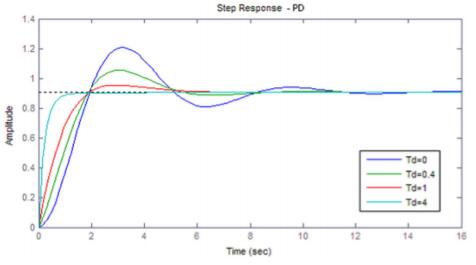
图3:指令响应示意图
因此,解决此类问题需要从电气和机械两方面综合分析,才能最终找到问题所在。
2、零件加工程序编制策略不符合机床加工特性
图1零件是用来检测机床五轴加工性能是否良好由使用部门自行制定的一个通用试切件,试切加工时没有针对本机结构及特性进行专门的程序编制和优化,该零件加工程序编制和加工参数是否符合本机特性,零件试切结果是否合适存在争议。为确认表面粗糙度差的原因是否由于零件加工程序编制策略造成,于是使用五坐标机床验收标准中通用的NAS试切件和程序、参数进行试切加工,加工结果如图4所示。从NAS试切件可以看到,零件表面粗糙度有显著改善,但是表面的波纹依然比较严重,所以可以认为零件程序编制和加工参数不是该机床零件表面粗糙度差的主要原因,而是机床自身问题导致零件表面粗糙度严重超差。
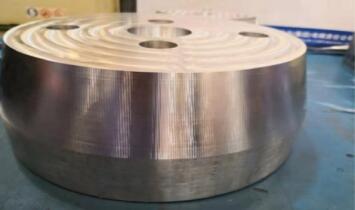
图4:NAS五轴试切件
3、五轴头机械特性与原电气
特性不匹配该机床的五轴头前期刚进行大修翻新,伺服电机、传动部件、轴承、编码器等全部更换,部件装配面全部进行刮研校正,如果该大修翻新的技术指标达不到要求或电气特性不匹配,零件加工也会相应出现各种问题。为确认表面粗糙度差是否是由五轴头造成,可进行一系列测试。
(1)A/C轴定位精度检测。数控机床坐标轴的定位精度和重复定位精度直接关系到零件加工的质量,该机床五轴头进行过翻新大修,如果A/C轴定位精度(P)和重复定位精度(Psmax)不好,坐标轴在快速运行中来回寻找定位点将造成机床振荡抖动,零件表面相应就会出现波纹,粗糙度下降。因此需要对A/C轴进行定位精度(P)和重复定位精度(Psmax)检测,结果见表1。

表1:A/C轴的定位精度和重复定位精度
从表1可以看到,该机床的A/C轴的定位精度和重复定位精度都满足机床的出厂精度要求,同时A/C轴的反向间隙也满足要求。因此表面粗糙度由A/C轴的定位精度和重复定位精度造成的可能性可以排除。
(2)A/C轴圆度测试。圆度误差是各种误差中非常重要的一项数据,圆度误差是回转体在正截面上的实际轮廓对比于理想圆的变动量,数控机床的圆度误差对数控机床的功能和精度有直接影响。该机床采用的是FIDIAC20数控系统,利用系统自带的圆度检测功能(ERCI)可以对坐标轴进行圆度检测。
按数控系统要求进行A/C轴圆度测试的相关设置,参数设置好后进行A/C圆度测试,测试结果如图5所示。
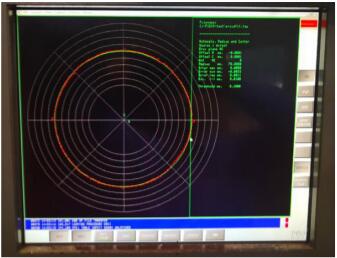
图5:A/C轴圆度测试
从A/C轴圆度测试结果看,A/C轴进行圆度测试时A/C的圆度曲线均匀,各象限图形没有明显的畸变或过冲,圆度测试满足要求,A/C轴运动时没有振动,机械性能没有明显缺陷,A/C轴机械性能满足要求。
(3)A/C轴伺服优化测试。如果速度环、位置环的增益设定值较大,系统响应就较快,能够较快达到稳定状态,机床加工时零件表面质量也会相应提高。为测试表面粗糙度超差是否是有A/C轴的速度环、位置环的增益设定值小,响应速度慢引起,可以增加A/C轴的速度环、位置环增益(见表2)。

表2:A/C轴的速度环、位置环增益
A/C轴的速度环、位置环的增益设定值为2.0、2.3时进行加工测试,加工的零件表面粗糙度没有明显改善;继续增加速度环、位置环的增益至2.3、2.8时A/C轴电机开始啸叫抖动,因此速度环、位置环的增益不能继续加大,要相应降低增益值,增益值的设定一般是机床轴开始啸叫抖动时增益值的80%为宜。因此,可以认为零件表面粗糙度问题不是由A/C轴的速度环、位置环的增益引起。
(4)NAS 三轴试件试切。A/C轴的定位精度、圆度和伺服优化测试结果没有发现问题,为确认零件表面粗糙度超差是否由五轴头引起,可以进行NAS三轴试件试切,把五轴头锁定加工。加工的三轴NAS试件结果如图6所示。
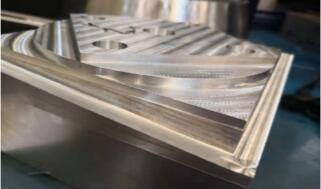
图6:三轴NAS件
从图6可以看到,三轴NAS的外圆、正方形的边波纹严重,表面粗糙度严重超差。由于三轴NAS加工时A/C轴不参与运行,但试件还是出现表面粗糙度严重超差,因此表面粗糙度严重超差由五轴头造成的可能性可以排除,五轴头的技术性能符合要求,表面粗糙度严重超差是由其他坐标轴运动引起。
4、X/X1轴龙门同步超差导致
表面粗糙度差大型数控龙门加工中心的龙门轴由主动轴(X)和从动轴(X1)组成,X/X1通过龙门(横梁(Y轴)机械连接,应用龙门同步技术进行控制。X/X1的同步误差一般要控制在0.015mm以内,如果龙门同步误差过大,X/X1轴运行不同步,会造成横梁扭曲,X/X1伺服电机过流,机床出现振动等后果。
机床运行中出现振动,加工的零件表面就不可避免会出现波纹等问题。为确认该机床的龙门同步是否在要求的误差范围内,进行龙门同步检测。利用数控系统的龙门同步功能,检测龙门同步情况,结果发现该机床的X/X1同步误差只有0.009mm,同步误差在容许的误差范围内。因此,该机床加工零件表面粗糙度超差的问题不是由龙门同步误差引起。
5、机械部件磨损,机械刚性
下降导致机床振动,零件表面粗超度差由于该机床的A/C轴情况良好,同时X/X1龙门同步误差很小,不会造成零件加工出现波纹,因此出现表面粗糙度差的原因可能是由X/Y轴的问题导致。为检测X/Y的插补运动情况,可以进行X/Y轴圆度测试,参数设置如下:进给速度:F=4000mm/min,圆半径R=100mm,插补轴:X、Y。X/Y进行圆度测试后,测试结果如图7所示。
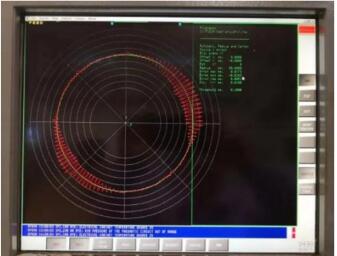
图7:X/Y轴圆度测试
从X/Y圆度测试的结果可以看到,在一、三象限(即X轴方向)有明显的振荡,同时在X轴运行时用手触摸机床,可以感受到机床有轻微的抖动,因此可以认为零件表面粗糙度超差是由X轴的问题导致。该机床各轴采用的机械传动是滚珠丝杠传动,滚珠丝杠是机械传动的关键部件,如果磨损大,将导致滚珠丝杠和丝母间隙增大,超过一定的范围就会导致坐标轴精确定位困难。当机床采用全闭环位置反馈时,数控系统是根据光栅尺的位置反馈进行数据处理,如果丝杠间隙过大,机械接触刚性下降,主轴加工受力后,那么机床无法精确定位,就会在定位的位置附近来回寻找位置。机床在高速运行状态下来回寻找定位位置必然会导致振动,形成系统振荡,表现在零件上就是零件表面出现波纹等。为确认X轴丝杠的磨损程度,可以人为地让X/X1的龙门同步误差加大,使横梁稍微扭曲,丝母和丝杠接触紧密,消除丝杠和丝母间隙。让X/X1轴同步误差分别是0.015mm、0.025mm、035mm进行测试,在同步误差在0.035mm时X/X1轴的振动消除,进行圆度测试(见图8),结果如下:
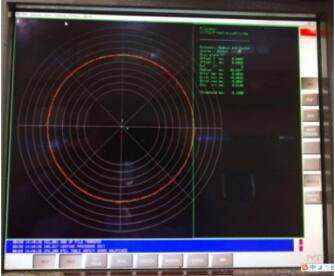
图8:X/Y圆度测试
从圆度测试的图形结果可以看到,人为使横梁(龙门)扭曲以后,消除丝杠与丝母间隙,圆度测试正常。因此可以最终确认该机床零件表面粗糙度超差是由于X/X1轴的丝杠磨损,间隙加大导致机械刚性下降导致。根据以上测试的结果,更换X/X1丝杠,速度环和位置环参数重新优化,使机床电气特性与新丝杠的机械特性匹配。同时因为更换了丝杠,丝杠与坐标轴的定位精度直接相关,所以要进行激光螺距定位精度校正和补偿。在做完X/X1丝杠更换、速度环、位置环优化调整以及定位精度激光螺距校正、补偿后,机床进行试加工,加工结果如图9所示,零件表面光滑,波纹消除,表面粗糙度符合要求。
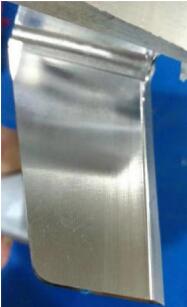
图9:试切件
6、结束语
造成零件加工时表面粗糙度差的原因比较多,解决问题难度较大,需要从编程、加工方法、加工参数、电气和机床机械结构分析入手,根据具体情况,分别对机床电气、机械、数控系统进行测试和调整,才能找到问题的根源,取得比较好的效果
投稿箱:
如果您有机床行业、企业相关新闻稿件发表,或进行资讯合作,欢迎联系本网编辑部, 邮箱:skjcsc@vip.sina.com
如果您有机床行业、企业相关新闻稿件发表,或进行资讯合作,欢迎联系本网编辑部, 邮箱:skjcsc@vip.sina.com