任务顺序刀库更新策略对加工中心换刀频率的仿真优化
2019-10-17 来源:广东省计算机集成制造系统重点实验室 作者:李泽龙,焦勇清,鲁一凡
摘要:针对含有单个自动加工中心的自动生产线,利用Plant Simulation仿真平台建立仿真模型,根据不同的情形设计和实施一系列试验,通过调整相关参数和使用不同刀库更新策略,统计换刀相关系统性能指标,最后提出一种在随机条件下的多任务多工序加工的刀库更新策略。
关键词:加工中心;仿真建模;刀库更新;随机任务
0 引 言
随着工业 4.0、智能制造在国内的兴起和推广,越来越多的企业在向无人化车间、无人化生产线转变。对于待成形产品的减量式加工,一般会采用加工中心。但现在客户定制化越来越普遍,订单的个性化、任务达到时间的随机性、个性化质量要求的多样性等,对加工中心的制造系统提出了更高的要求,比如加工中心刀库设计要求、系统刀具多样性要求、系统刀具调度策略合理性要求以及刀具使用寿命控制等。在车铣复合加工中心的自动生产线中,刀库更新无法避免,特别是对于加工零件类型多样性、加工工序多样性、刀库刀位有限性以及任务到达顺序不确定的情况下,刀库刀具更换会更加频繁。
目前国内外对可以处理多类产品、多道工序的车铣复合加工中心刀库更新的策略研究不多,对于刀具使用寿命研究也过于理论化,难以适应具体的工程应用。曹乐等分析刀具预防性更换与故障性更换之间的差异,对故障性刀具更换时间的不确定性进行描述,建立刀具更换的时间成本模型,最后以单位产品平均成本最小化为目标,建立一种刀具更换周期决策模型;DENG Y H和JEANG A等人基于刀具更换成本和加工过程中刀具更换决策,通过研究分析提出一种最优刀具更换决策方法[2,3];王新刚等以刀具失效率为判据,建立了如何确定被更换刀具的工序及换刀时间的方法;张敏等提出了刀具磨损的过程能力指数计算方法,将过程能力与成本相结合,提出了用于确定最佳刀具初始状态和维修周期的模型。一些学者从刀具可靠性分析研究刀具更换决策问题,如LIU P H等针对柔性制造系统建立了刀具更换周期的优化决策模型。
以上参考文献主要是对单一刀具使用寿命的研究,刀具达到使用寿命或刀具故障导致的换刀。现以典型的单加工中心制造单元为研究对象,运用Plant Simulation 仿真软件对单加工中心制造单元进行仿真建模,在多任务、多工序且任务随机到达的情况下,采用不同的刀库更新策略研究系统换刀频率,从而提出启发式改进方法。1 问题描述在包含车铣复合加工中心的自动化生产单元中,生产过程中由于加工中心刀库的刀位有限,刀具更换无法避免。刀具更换时加工中心必须暂停工作,且刀具更换时间不可忽略,所以刀具更换对加工中心的生产效率有一定影响,必须在生产过程中合理安排刀库刀具,使加工过程中刀库的更新次数减少,且每次刀具更新时刀具更换数量少,使完成给定加工任务时刀库刀具变更所耗费时间最少。由于实际应用过于复杂,现将问题抽象描述,预设一些条件或参数以便于研究。在建立仿真模型之前先假设:
①任务总量和任务类型已知、每个任务零件数量和加工工序已知、所用刀具种类和数量已知;
②同系统各种刀具使用寿命因加工任务不同而不同,存在公用与专用刀具;
③所有刀具更换时间。单加工中心自动生产线如图1所示。
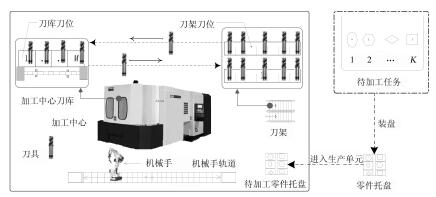
图1 单加工中心自动生产线
2 、仿真模型设计与实现
2.1 仿真流程分析
(1)系统刀具初始化:根据系统刀具及各自数量生成相应刀具。
(2)任务到达与装盘:任务到达之后,申请对应的托盘装载零件,等待加工。
(3)加工中心刀库更新:由预设定的刀具调度策略,根据不同的任务对刀库进行更新。
(4)系统刀具更新:将达到使用寿命的刀具送至装载中心进行刀具更换。
2.2 换刀流程分析及刀具调度策略
系统刀具可分为 2 类:专用刀具和公用刀具。专用刀具指定的某一种零件的某一道工序的加工,该刀具的特点是刀具使用寿命容易控制;公用刀具至少能够加工某一种零件或某一道工序,该刀具的使用寿命不容易控制,因为加工不同零件工序时的损耗不一样。
刀具调度策略首先获取要加工的任务类型,其次根据系统信息获取要加工的任务所用的刀具,当前一类任务加工完成以及对刀库刀具使用寿命进行更新完毕之后,开始对刀库进行更新,对刀库更新有两部分:
①将达到使用寿命的刀具移至刀具装载站进行刀具更换,在系统中补一把全新的刀具,并将其放在刀架对应的位置;
②根据要加工的任务配置刀库刀具,这时需要扫描刀库刀具信息,把要用到的刀具留下,如果存在没有的刀具,从刀架找到要用的刀具并通过机械手移至加工中心刀库,若
刀库没有空刀位,从刀库移除一把不用的刀具至系统刀架,直至加工任务所用的刀具全部备齐至刀库。刀具调度策略如图2所示。
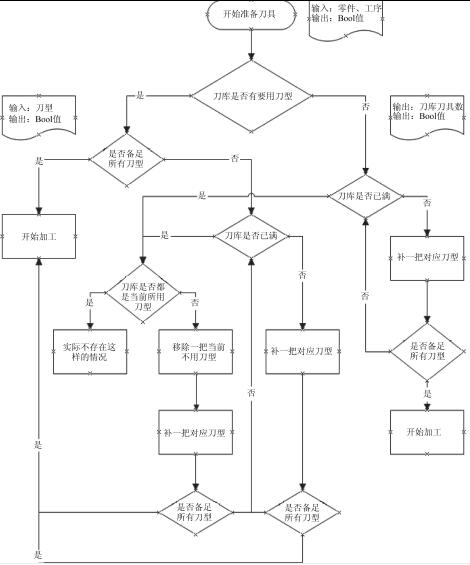
图2 刀具调度策略
2.3 仿真模型实现
由于研究内容只涉及刀具更换,不模拟机械手取放刀动作,在建模时除去机械手,模型中只是用相关对象及其组合模拟刀具更换对系统进行补刀,
仿真模型主要包括以下7个模块。
(1)系统参数信息模块:包括刀具基础数据表,如刀具类型、综合使用寿命等信息;系统刀具对应的刀架位置信息;公用刀具与专用刀具信息;加工任务种类及其数量信息等;不同任务的刀具配置信息等。
(2)订单、刀具、零件生成模块:订单生成按照任务表顺序到达,该到达是按任务比例随机到达;刀具生成按照系统刀具配置信息顺序生成至系统刀架;零件生成包括两部分:
①零件按订单到达顺序生成;
②生成零件对应的零件托盘,并且将零件装载至对应的零件托盘,装载数量由系统参数确定。
(3)加工中心及刀架模块:该模块包含1台加工中心、1 个刀架和 2 个缓存台(上料托盘零件缓存台和下料零件缓存台),负责零件的加工,加工时间由不同零件、不同工序预设的加工时间确定。
(4)刀具调度方法模块:该模块主要负责加工过程中刀具的调度问题,包括换任务后刀库的更新、加工同种任务时达到使用寿命的刀具的更换和系统中达到使用寿命的刀具更新等。
(5)加工中心刀库及刀架控制模块:该模块负责零件托盘上、下缓存台,根据不同零件及其工序设置其技工时间和零件上、下机床控制等。
(6)刀具更换模块:主要模拟装载站的刀具更换,包括旧刀具的回收、新刀的生成和刀具信息传递,如刀具、刀架位置和综合使用寿命等信息。
(7)刀具统计模块:该模块负责加工过程中刀具使用情况的统计,包括不同刀具的使用数量、刀具的更换总次数和不同刀具的更换次数及其更换频率。单加工中心仿真模型如图3所示。
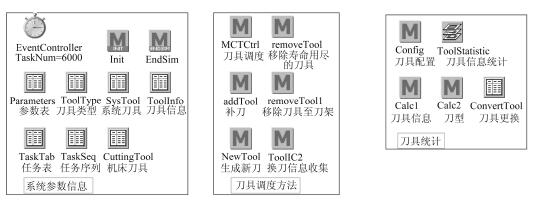
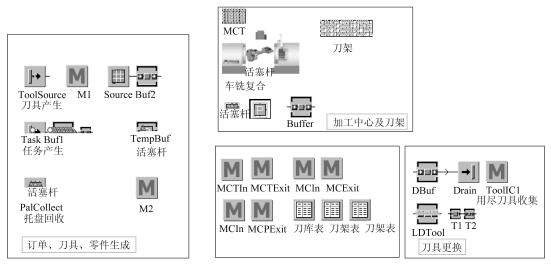
图3 单加工中心仿真模型
3 、仿真试验与结果分析
应用Plant Simulation 离散系统仿真软件对上述单加工中心的自动生产线进行仿真,分析在不同刀库更新策略及任务随机到达的情况下,通过对刀具使用信息的统计,找出影响换刀频率的原因,并提出降低换刀频率的方法。
3.1 仿真系统基本参数
仿真中零件的加工是按工序加工时间进行,但对刀具使用寿命的损耗折算是按已加工零件数目进行统计,零件及其工序加工时间如表1所示,仿真试验设计如表2所示
表1 零件及其工序加工时间
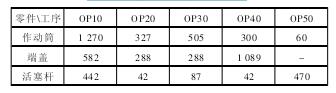
表2 仿真试验设计
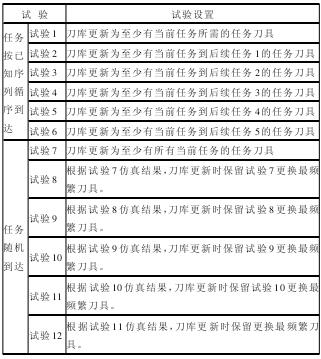
仿真试验结果及其分析对换刀的统计是由于新的任务到来,这时加工中心刀库中的刀具没有对应的刀具导致换刀,并不是因为达到使用寿命导致的换刀,因达到使用寿命导致的换刀不予记录和统计。任务顺序给定时,不同更换策略下更换频率的最高10类刀具如表3所示。
表3 任务顺序给定时更换频率最高的10类刀
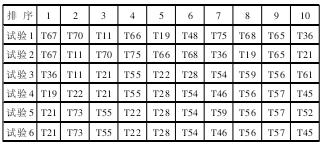
从表3可以看出,在给定加工任务顺序时,不同刀库更新策略下的不同试验中,有的刀具更换频率在不同策略中都比较高,如 T67、T70、T11、T21 和T22 等刀具,所以在进行刀库更新时,这些刀具尽量保留在刀库中,可以减少总的刀具更换次数。对于给定任务顺序下的不同刀库更新策略,不同刀具的更换频率如图4所示。
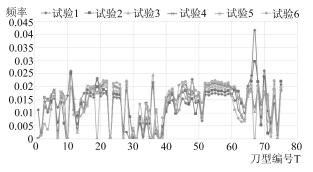
图4 任务顺序给定时的刀具更换频率
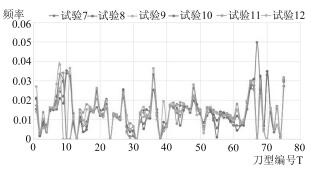
图5 任务顺序随机时的刀具更换频率
从图 4 可以看出,刀具编号在 30~40 的大部分刀具更换频率比较低,刀具编号在52~60的刀具更换频率比较接近。对于任务顺序随机时的不同刀库更新策略,不同刀具的更换频率如图5所示,从图5 可以看出,刀具编号在 50~64 的刀具更换频率比较低,也有比较多的刀具更换频率为0。
任务顺序随机时,不同更换策略下更换频率最高的10类刀具如表4所示,从表4可以看出,在加工任务顺序是随机给定时,不同刀库更新策略下的不同试验中,有的刀具更换频率在不同策略中都比较高,如 T66、T70、T11、T36 和 T68 等刀具,所以在进行刀库更新时,这些刀具尽量保留在刀库中。
表4 任务顺序随机时更换频率最高的10类刀
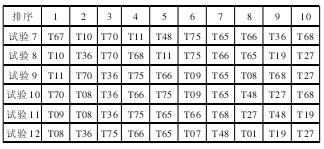
综合上述的试验结果可知,在不同任务顺序的情况下,更换频率较高的刀具并不完全一样,所以要根据实际的加工情况合理安排刀库中的刀具,使刀库更新时总的刀具更换次数减少。
4 、结束语
通过对含有车铣复合加工中心的刀库刀具更换问题进行描述,对其进行仿真建模,在不同任务到达顺序的情况下,通过一系列的仿真策略得出相关的仿真试验数据,经过对试验数据的分析,可以发现哪些刀具类型的更换比较频繁,然后在生产过程中,着重对相关刀具进行优先配置,可以有效减少总的换刀次数,从而减少由于刀具更换带来的时间损耗,提高生产效率。
投稿箱:
如果您有机床行业、企业相关新闻稿件发表,或进行资讯合作,欢迎联系本网编辑部, 邮箱:skjcsc@vip.sina.com
如果您有机床行业、企业相关新闻稿件发表,或进行资讯合作,欢迎联系本网编辑部, 邮箱:skjcsc@vip.sina.com
更多相关信息