五轴联动叶片加工中心发展现状及其结构特点
2017-12-19 来源: 韶关市技师学院 作者:赵伟宜 曾燕玲
摘 要:五轴联动叶片加工中心是加工汽轮机、航空航天发动机等专用的叶片的机床,在机械制造业具有不可替代的核心地位。现今叶片的形状和结构更加复杂,为保证叶片的精度和质量,在叶片加工过程中必须达到高标准、高精度,叶片的加工设备和加工方法也不容忽视。因此,只有研究分析叶片加工中心的基本结构和特点,才能为加工高质量的叶片提供有效的参考依据。
关键词:五轴联动叶片 加工中心 发展现状 结构特点
引言
现如今加工制造业在国家的地位不言而喻,五轴联动就是其中至关重要的一部分,在加工中心的发展中五轴联动有着划时代的意义。加工中心可以分为两类,一类是卧式加工中心,这类加工中心比较局限,即使是和回转工作台共同工作的情况下,也只能加工工件的四周轮廓,无法加工工件其他部位;另一类是立式加工中心,这种加工中心也并不完美,只有在加工工件顶面时才有效率。而五轴联动简易高效,在加工工件时只需装夹一次,就能对工件的五个面全部加工,其效率和精度水平在加工中心非常之高,是加工中心发展的里程碑。
1 、概述五轴联动叶片加工中心
叶片式汽轮机、燃气轮机、航天发动机等的核心部件,是轮船和飞机十分关键的部位,叶片的形状非常复杂,叶根圆角结构是由数个圆弧共同组成,在空间中呈曲面形状,一些特殊的叶片叶身中部还会有阴尼台的设计。在我国的叶片设计发展史上,不同时代叶片的加工设备和方法也在逐渐更新变革。早期国内采用的是三轴机床加工叶片,由于设备比较简陋,技术也不太成熟,大多数是加工制造一些形状比较简单的叶片,而且工序比较复杂,效率也不高。通常是加工叶片的其中一个面,之后翻面加工另一个面,依次加工叶片的各个面。三轴机床加工叶片的方法应用较早,在长时间的加工中也得到了丰富的经验,技术相对成熟,因此目前国内仍有采用这种方法加工叶片的。经多次改革更新,四轴机床开始应用,建立在三轴机床的基础上,四轴机床延续了三轴机床的优点,也在相对低效率的手动翻面上有了改进,其配置的 A 轴不用多次的手动翻面,生产效率也随之提高。最终有了五轴联动叶片加工中心的出现,加工效率也突飞猛进,这也正顺应了叶片加工的发展潮流,是叶片加工中心的必然发展趋势。现今社会是发展科技和加工业的时代,国内国外都需要大量的叶片发展本国的机械制造业,叶片的形状逐渐复杂化,对叶片加工的设备要求也越来越高。目前我国的五轴联动叶片加工应用的时间较短,加工经验不够丰富,技术也不成熟,而以往的三轴联动和四轴联动已不再适用如今复杂的叶片加工,因此,本文在现有的五轴联动加工设备和技术上,设计一种能加工复杂叶片的五轴联动加工中心。
2、 五轴联动叶片加工中心的发展现状
五轴联动叶片加工中心并非加工所有机床零件,而是会选择性地加工航空航天发动机和汽轮机等叶片,此外也会加工一些形状窄长的空间结构复杂的曲面零件机床。这些机床通常都由 X、Y、Z、A 和 B 轴组成,X、Y、Z 轴是三条直线轴,空间结构和立式加工中心的布置比较相似,不同的是 X 轴较长,Y、Z 轴较短,如果 X 轴较长的话就可以直接用于加工长叶片,B 轴是刀具摆动轴,A 轴是叶片回旋轴。目前我国的各种叶片加工中心的生产厂基本被国外的五轴联动叶片加工中心厂家垄断,因为国内的五轴联动叶片加工中心还处于初级阶段,起步较晚,技术也不太成熟,而国外知名的生产五轴联动叶片加工中心的厂家占据着我国机床加工市场。
3 、五轴联动叶片加工中心机床的结构特点
3.1 B 轴的回转中心与刀具主轴的回转中心成 45°
五轴联动叶片加工中心对机床的规格非常严格,要求 B轴的回转中心与刀具主轴成 45°,刀具主轴的刀尖还必须在轴的回转中心上,机床的结构特点显著明确,如图 1 所
示为五轴联动叶片的加工。直线轴 Y 通过刀具移动实现,直线轴 X 和 Z 则通过工件移动实现。这种结构不但可消除 X、Z 轴的插补运动,有效提高工件的表面加工质量,还能阻止切削力产生的扭矩传输到 B 轴。
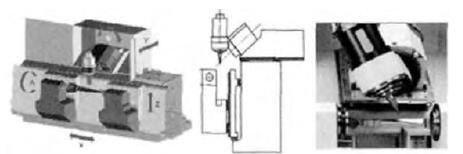
图 1 五轴联动叶片加工
3.2 B 轴的回转中心与刀具主轴的回转中心成 90°
五轴联动叶片加工中心要求 B 轴的回转中心与刀具主轴的回转中心成 90°,可通过两个方法实现,一是使 B 轴回转中心与刀尖部位基本重合,尽可能偏离刀具主轴中心,二是 B 轴回转中心刀具主轴重合,然而这两种方法都有各自的优点和局限性。方法一的优点比较明显,刀尖的位置离轴回转中心非常近或基本在轴回转中心上,这使 B 轴在摆动时不会影响刀尖位置的改变,需要插补的量也很小。
如果 B 轴摆动的角度出现误差,这种几乎可以忽略的误差也不会对刀尖的位置产生比较大的影响,X、Y 轴频繁的插补运动会大大降低,提高了加工的精度,对轴的要求也有所降低。不足的是 B 轴在摆动时会产生偏心力矩,如果要在设计时平衡掉偏心力矩,这也加大了机械设计的困难度。方法二中刀具主轴的重心基本都在摆动中心上,在摆动时比较平衡,误差较小,有利于机械设计的简单化,然而实际中 B 轴的摆动往往伴随着 X、Z 轴的插补,摆动角度的误差带动着 X、Z 轴的插补误差,在在摆动角度误差较大时刀尖位置的误差也就不容忽视。要想机床加工比较准确,对 B轴的摆动要求就要非常准确,不能有偏离的误差现象,这也给设计制造带来了困难。
3.3 多主轴叶片加工中心
在占地面积有限的情况下可以选用多主轴叶片加工中心,即加工时同时加工多个叶片,可大大提高了加工效率,也能节约加工成本。对规格较小的叶片加工中心,可以采用双刀具主轴结构,最大的加工长度不会超过 262mm,刀具主轴转速可以达到 30000r/min;有一次能同时加工两个叶片的五轴联动叶片加工中心 g-mill550twin,主轴带有两个刀具和 A 轴;还有能一次同时加工四个叶片的五轴联动叶片加工中心,NX 系列带有多个主轴,其生产效率非常高。
3.4 其他结构
HSTM 系列五轴联动叶片加工中心的 Y、Z 轴运动通过刀具实现,B 轴为“T”型结构,X 轴运动通过工件实现,采用 45°斜床身,具体结构如图 2 所示。
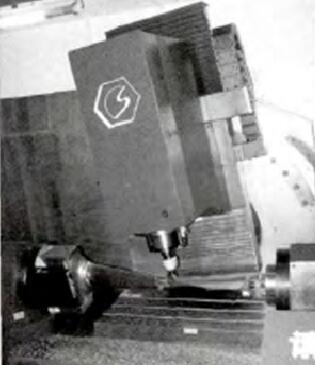
图 2 1V5X1800
3.5 并联叶片加工中心
轴联动叶片加工中心在叶片质量较轻时可依据刀具轴的运动方向和工件划分。有的机床是刀具主轴实现 Y 轴运动,工件实现 X、Z 轴运动;有的机床 X、Y、Z 轴运动是靠刀具主轴通过立柱和滑板等实现;还有的是工件实现 Y轴运动,而刀具主轴实现 X、Z 轴运动。
4 、五轴联动叶片加工中心的应用
加工叶片的叶身型面时加工中的重中之重,叶身型面在一定程度内可以弯曲,虽然不规则,却有一定的规律可循,在五轴联动叶片加工中心叶身型面的加工有一定的优势。
螺旋加工方法使在刀具顺着 3 个坐标方向连续进给时,加工的轨迹是一条环着叶身的螺旋线,通常用这种方法加工叶片。由于五轴联动叶片加工中心的刀具主轴的角度可以在一定范围内转动,而且主轴有高速回转的功能,在加工时型面的圆角刀可以完全垂直于曲面,这时再用适当的前倾角方式走刀,最终加工出的型面不会有切合死角的存在,而其他的设备无法完全达到这种加工效果。虽然加工效果比较完美,但对编程算法的要求也相当高,若是编程算法的程度不够,就无法达到预期效果,若有专业的 CAM 软件编程算法,可这一解决问题。本文所述的机床可以配备叶片编程专业软件 Hypermill,此款软件使用各种层次的叶片用户,能有效缩短编程时间,还能提供优质的参考模板。
5、 结语
现代社会经济水平和科学技术发展迅速,在制造业领域机床水平的高低能直接反映一个国家的工业发展水平,五轴联动机床系统更是机械制造业的高新技术发展标志。机械制造业在现代社会中有着举足轻重的地位,汽轮机和航空航天发动机的需求也在逐渐扩大,五轴联动叶片加工中心的地位也越加重要。要实现叶片行业对叶片的大量需求,就要大力发展国内的五轴联动叶片加工中心,设计并制造出优良品质的五轴联动叶片铣削设备,在降低成本的同时能高效率生产加工出高质量的叶片,为我国的机械制造业创造出更加广阔的未来。
投稿箱:
如果您有机床行业、企业相关新闻稿件发表,或进行资讯合作,欢迎联系本网编辑部, 邮箱:skjcsc@vip.sina.com
如果您有机床行业、企业相关新闻稿件发表,或进行资讯合作,欢迎联系本网编辑部, 邮箱:skjcsc@vip.sina.com
更多相关信息