SL50 型数控车床主轴回转精度的可靠度研究
2017-4-1 来源:南通职业大学 机械工程学院 作者:张丽萍,李业农,周开俊
摘要:通过以 SL50 型数控车床的主轴组件为例,深入分析了产生主轴回转误差运动的原因,提出该数控车床主轴轴承的预紧力界定范围。对该数控车床主轴轴承磨损情况做了可靠性统计分析,建立了主轴回转精度寿命的可靠度模型,主轴轴承磨损量与其工作小时数几乎成线性关系。在该数控车床工作 15000 小时和 20000 小时后,分别检测了主轴径向跳动的误差、主轴轴向窜动误差和卡盘端面跳动误差,对主轴回转精度的下降情况做了统计分析,并进行了回转精度可靠度计算。
关键词:数控机床;主轴;轴承;磨损;回转精度;统计分析;可靠度
1.引言
要提高数控机床的加工精度,除了要提高机床的刚度、抗振性和热稳定性外,首要的是提高主轴组件的几何精度和回转精度,在制造过程中可通过先装配后精加工提高主轴的回转精度[1] 。从统计分析结果看,轴承的主要失效形式是接触疲劳磨损、磨粒磨损、粘着磨损和微动磨损[2-3],鉴于此,笔者以 SL50 型数控车床的主轴组件为例,就影响主轴组件的回转精度的因素,尤其是主轴轴承磨损对主轴回转精度寿命影响的程度做了深入的探讨。
2.产生主轴回转误差运动的主要原因分析
SL50 型数控车床的主轴部件,前支承为三个角接触球轴承,前面两个轴承大口朝向主轴前端,以承受轴向和径向切削力;后面轴承大口朝向主轴后端,三个轴承的内外圈轴向由轴肩和箱体孔的台阶定位承受轴向负荷。后支承由一对背靠背的推力角接触球轴承组成,只承受径向载荷,并由后压套进行预紧,结构如图 1所示。
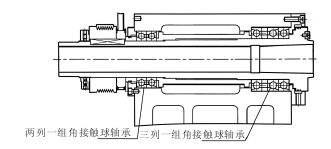
图 1 SL50 型数控车床的主轴部件结构
一般数控车床而言,主轴的瞬时回转轴线是经常变动的。根据相对运动的原理,在任何瞬时,一方面主轴绕自己的瞬时回转轴线旋转,另一方面,该瞬时回转轴线还相对理想回转轴线作轴向的、径向的和倾角的运动[4-5]。SL50 型数控车床的主轴部件也不可避免存在上述误差运动。其主要原因有:
(1)主轴支承轴颈的圆度误差,如椭圆、棱圆及较大的波纹,会造成主轴周期性径向跳动误差运动。主轴前后支撑的不同轴及它们径向跳动的大小和方向的不一致性,会造成主轴的摆角误差运动。
(2)主轴轴承,特别是前轴承的缺陷,如轴承套滚道的圆度误差和波纹,滚动体直径的不一致性及圆度误差等,会造成主轴的径向误差运动。轴承的支撑端面对主轴回转中心线的不垂直,轴承的滚道及滚动体的误差,会造成主轴周期性的和非周期性的轴向误差运动。滚动轴承的摩擦和磨损,使主轴部件的各部分产生不同的热变形,会造成主轴的径向误差运动和轴向误差运动。
SL50 型数控车床是精密级机床,除了主轴支承轴颈、主轴前后支撑的不同轴等先天性误差外,主轴轴承的自身误差和安装误差也是引起主轴回转误差运动的主要因素之一。只有经过严格的生产工艺过程控制,使上述的 2 项误差降到最小值。
3.主轴轴承的预紧及磨损情况分析
由于滚动轴承内部存在游隙,适当预紧使各个滚动体都承受一定的预负荷,参加工作的滚动体数量增加,直径略大的滚动体变形较大,使直径较小的滚动体也承受载荷,从各个方向支承内圈,故可以提高轴承的回转精度、寿命和刚度[5-6]。SL50 型数控车床在主轴刚起动时,箱体和轴承座还处于常温状态,直接受摩擦热作用的滚动体和内外圈的温升最快,内部元件和外部元件的温差最大,当轴承各部分与箱体温度相对稳定后,预紧力达到最大值并趋于稳定,实测表明,预紧力的工况最大值以达到装配预紧力的 2 倍左右为宜。预紧力过大,会导致轴承发热剧烈,加速轴承的磨损。
SL50 型数控车床的主轴部件前支承为三个角接触球轴承,前两个轴承串联,与第三个背靠背组配。通过计算这种组配其轴承预紧力应不小于额定轴向载荷的四分之一,其次,这种高精密主轴前轴承允许温升为 10℃,轴承生产厂商建议其应预紧力可控制在(1100~1300)N,这样可有效提升轴承的回转精度。预紧力再增大,轴承温升会增大,反而会降低回转精度。SL50 型数控车床的主轴轴承为高精密角接触球轴承,滚动体与座圈采用高质量的滚动轴承钢制造,具有很高的硬度 HRC(60~65),很高的加工精度和很低的表面粗糙度。该主轴轴承的接触疲劳强度是足够的,不会产生接触疲劳磨损。轴承主要是由于磨粒磨损、粘着磨损和微动磨损而导致轴承的回转精度下降,直至精度失效,故这种轴承的寿命主要为精度寿命。
这种角接触球轴承由于离心力和陀螺力矩的作用,滚动体钢球的自转会产生微滑动。当转速越高或接触角越大,微滑动会越大。再者滚动体钢球与保持架是纯滑动接触,二表面之间的相对滑动摩擦,提高了轴承温度,加大了轴承磨损。造成轴承磨损的因素是多方面的,多种因素作用下的轴承磨损更加难以预测的防止,轴承磨损使轴承的径向游隙和轴向游隙增大,从而使主轴回转精度降低。在跟综了 SL50 型数控车床主轴的工作情况,主轴在工作10000 小时后,主轴回转精度有一些下降,由于机床具有一定的精度储备,故机床没有超出允许的回转误差范围;工作 15000 小时后,回转精度继续下降,比出厂时的误差加大了 20%,少量用户提出更换主轴轴承的要求;工作 20000 小时后,回转精度有较大下降,比出厂时的误差加大了 35%,部分用户委托厂方或自行更换主轴轴承。究其原因,85%是由于主轴轴承磨损所致,轴承磨损量与主轴工作小时数几乎成线性关系。
4.主轴回转精度寿命的可靠度模型
主轴回转精度可靠度 R(t)指主轴回转运动误差落在最大允许范围内的概率。
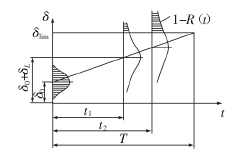
图 2 主轴轴承的回转精度寿命可靠度
由于主轴回转运动误差随着时间 t 的增大而增大,使主轴回转运动误差的中心发生漂移,散度增大,可靠度下降。当主轴工作了时间 t 后,主轴轴承的精度失效概率 F(t)=1-R(t)明显比初始时间增大了,如图 2 所示。且平均误差与主轴工作时间成线性关系[9]。当规定主轴轴承精度寿命可靠度的大小后,便可由式(1)反推出主轴轴承的精度寿命。
5.主轴回转精度可靠度计算
以 SL50 型数控车床为例,主轴的误差运动的 3 种基本形式:即纯径向误差运动、轴向误差运动和摆角误差运动。这些基本形式很少独立存在,往往是同时并存的。纯径向误差运动和轴向误差运动并存时的误差运动称为径向误差运动,它是指主轴回转中心线 O1-O1在某一指定位置垂直于其理想中心线 O-O 线方向上的误差运动。主轴径向跳动的测量位置,如图 3 所示 SL50 型数控车床初始工作期间,主轴 a 点径向跳动均值为 0.006,均方差为0.0010;b 点:主轴径向跳动均值为 0.011,均方差为 0.0021。主轴工作 15 000 小时后,a 点:主轴径向跳动均值为 0.007,均方差为 0.0018;b 点:主轴径向跳动均值为 0.014,均方差为0.0035。主轴工作 20000 小时后,a 点:主轴径向跳动均值为0.008,均方差为 0.0021;b 点:主轴径向跳动均值为 0.016,均方差为 0.0043。a 点:主轴径向跳动允差为 0.010,b 点:主轴径向跳动允差为 0.020。
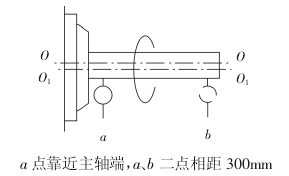
图 3 主轴径向跳动的测量位置
轴向误差运动和摆角误差运动并存时的误差运动称为端面误差运动,它是指回转主轴的端面在规定的径向位置上平行于理想回转中心线的方向上误差运动。SL50 型数控车床初始工作期间,主轴中心轴向窜动误差均值为 0.006,均方差为 0.0010;d 点(距主轴回转中心 125mm 处):主轴卡盘端面跳动误差均值为0.011,均方差为 0.0020,如图 4 所示。图中:c 为回转中心,卡盘上d 点的回转半径为 125mm主轴工作 15000 小时后,主轴中心 c 点:轴向窜动误差均值为 0.007,均方差为 0.0016;d 点:主轴卡盘端面跳动误差均值为0.014,均方差为 0.0036。主轴工作 20000 小时后,主轴中心 c 点:轴向窜动误差均值为 0.008,均方差为 0.0019;d 点:主轴卡盘端面跳动误差均值为 0.016,均方差为 0.0042。
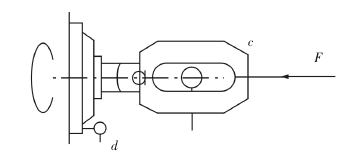
图 4 主轴轴向窜动误差和卡盘端面跳动误差的测量位置
主轴轴向窜动误差允差为 0.010,d 点:卡盘端面跳动误差允差为 0.020。主轴初始工作期间,由式(1)计算,a、b、c、d 四点的精度可靠度:Ra(0)=Rb(0)=RC(0)=Rd(0)≈1运用可靠度的计算方法[10-11],主轴工作 15000 小时后各点的精度可靠度:
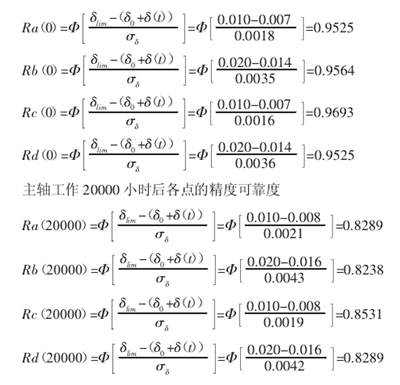
通过上述计算分析,主轴工作 15000 小时后,各项误差的均值和均方差均加大,离散度增大,说明主轴轴承有一定的磨损,导致精度可靠度下降,但仍保持在 95%以上,该机床已不适宜加工一些重要的精密的零件。主轴工作 20000 小时后,主轴轴承磨损进一步加剧,精度可靠度下降很多,该机床只能用于精度要求不高的加工,若想恢复精度,可考虑送回机床生产厂进行大修,更换主轴轴承。
6.结论
主轴组件是数控机床的重要组成部件之一,它的精度寿命可靠度是数控机床的工作能力的一项重要指标。
(1)主轴轴承误差是引起主轴回转误差运动的主要因素之一。
(2)通过控制这种高精密主轴轴承的预紧力,可有效提升轴承的回转精度,降低轴承温升。
(3)当规定主轴轴承精度寿命可靠度的大小后,可反推出主轴轴承的精度寿命。
(4)主轴工作 15000 小时后,各项误差的均值和均方差均加大,离散度增大,精度可靠度仍保持在 95%以上。
(5)主轴工作 20000 小时后,主轴轴承磨损导致精度可靠度下降到 82%,建议进行更换主轴轴承的机床大修。
投稿箱:
如果您有机床行业、企业相关新闻稿件发表,或进行资讯合作,欢迎联系本网编辑部, 邮箱:skjcsc@vip.sina.com
如果您有机床行业、企业相关新闻稿件发表,或进行资讯合作,欢迎联系本网编辑部, 邮箱:skjcsc@vip.sina.com