数控车轮车床的改进设计
2015-2-20 来源: 青海华鼎重型机床有限责任公司 作者:张剑
摘要: 由于客运的高速化发展,加工带齿轮箱的车轮是必然趋势,因此改进设计千斤顶来满足轮对加工要求,新增设计齿轮箱定位装置来解决轮对加工时齿轮箱定位问题,改进是成功的。
笔者公司生产的CK8011 系列数控车轮车床主要用于加工、维修轨距为1 435 mm,轮对直径为600 ~1 100 mm的铁路车辆解体轮对的轮缘、踏面及内侧面。适用于铁路运输部门的各个车辆生产、维修工厂、车辆段等单位。
近年来随着高速铁路的快速发展,市场对带有齿轮箱轮对的加工、维修需求量不断增大。由于轮对齿轮箱的规格各有不同,数控车轮车床在加工过程中难免会遇到机床主要部件千斤顶与轮对齿轮箱发生干涉的问题。以往的轮对有少量带齿轮箱的,因为齿轮箱可以拆卸,所以数控车轮车床能保证轮对正常加工,但随着客运的高速化发展,铁路行业的更新,现在高速客车用的轮对直径较小,而且轮对上的齿轮箱不允许拆卸,这就必须对原有数控车轮车床进行结构改进。
1、 改进方案的确定
数控车轮车床必须能加工带齿轮箱的轮对,而且要解决此类轮对上、下料及其加工中齿轮箱的定位问题。
1. 1 轮对上、下料的实现
轮对的上料过程: 轮对由料库滚至转盘,经过转盘后,沿车间轨道和机床输入轨道滚入千斤顶,千斤顶抬升轮对到位,然后进行装卡。下料过程则与此相反。由于千斤顶与大部分轮对齿轮箱发生干涉,导致机床无法进行正常的上、下料工作,现有机床在加工新型带齿轮箱的轮对时,只能用行车进行吊装,再进行装卡,加工时轮对的齿轮箱部分由行车吊起固定。通过对现有车轮车床的结构分析,以及用户现场的仔细调研,再综合考虑通用性、设计成本低和加工效率等因素,最终确定改进设计千斤顶部件,来实现轮对的上、下料要求,最终保证轮对的车削加工。
1. 2 齿轮箱的定位
现有结构的齿轮箱大部分不允许拆卸,加工时多数用户利用行车吊起固定齿轮箱,不然齿轮箱会在车轴上转动,导致无法正常车削轮对。
针对该问题,决定设计齿轮箱定位装置来解决轮对带齿轮箱加工,而且在加工中不必用行车吊起固定。
2 、千斤顶部件的改进设计
2. 1 改进前结构
改进前千斤顶结构见图1 所示。横梁左右两侧上顶面与轮对齿轮箱发生干涉。
2. 2 改进后结构
改进后千斤顶结构( 获省级和国家级QC 优秀成果奖) 见图2 所示。通过改变横梁的结构形式来降低横梁左右两侧上顶面的高度,消除了与轮对齿轮箱发生干涉。
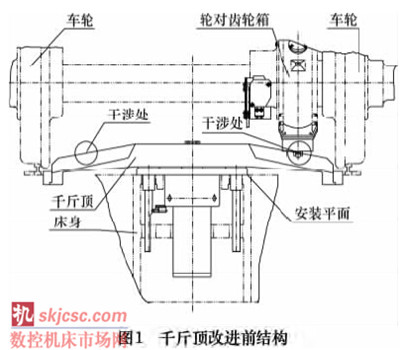
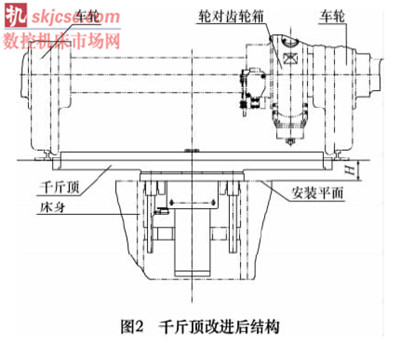
2. 3 相关结构的改进设计
只改进设计千斤顶横梁结构形式,是不可能同时保证原机床中心高、床身高度和加工直径范围三者不变的。因为千斤顶的行程必须大于最大轮对加工直径与最小轮对加工直径差的1 /2,即( 1 100 - 600) /2 = 250mm,而改进设计使千斤顶横梁上顶面下降后,若千斤顶的行程不变,支撑直径范围一定会减小。
最后局部改进设计床身部件,将千斤顶与床身的安装基面下降H ( 图2) ,同时增加千斤顶的行程。这样的结构处理,可以在提高机床通用性的同时又保证低成本改造。
3、 齿轮箱定位装置的设计
3. 1 齿轮箱定位装置的结构
齿轮箱定位装置( ZL201120528691. 4) 的结构见图3 所示。本定位装置由螺钉7、定位销8,将支座11 固定在床身上,丝杠12 拧入螺母1 中,再一同装入支座11中,螺母1 与推力球轴承3 接触,推力球轴承3 由支座11 定位,螺母1 与深沟球轴承4 配合,装配时调整垫5,装配调整完由弹性挡圈6 定位。再将螺母15、螺栓16 与支架14 装配好,用圆柱销13 将支架14 与丝杠12 固定联接,通过手柄2 使丝杠12 旋转,抬升支架14到达定位位置。
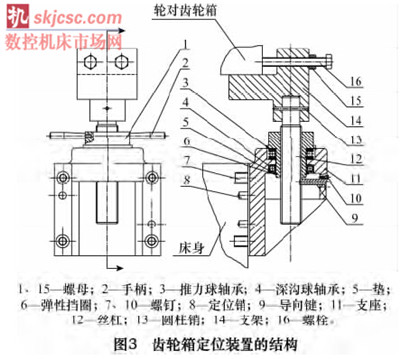
3. 2 结构特点
该定位机构为新结构,具有安装快捷、操作简单方便,定位安全可靠等特点。轮对加工为批量生产,所以在加工前先利用手柄2 调整好垂直方向行程,将预调行程定在3 ~ 6 mm,丝杠2 旋转1 ~ 2 圈即可达到最终定位位置,这样可减少辅助工作时间。再利用螺栓16 水平定位齿轮箱,通过螺母15 锁紧,定位完成。
4 、结语
改进后的数控车轮车床提高了机床的适用性,扩大了机床的加工范围,可完全满足高速铁路动车组轮对轮缘和踏面的加工修理需要,同时大幅度缩短加工及修理时间,降低修理成本。投放市场后不仅得到用户好评,而且获得了省级和国家级QC 优秀成果奖,并成功申报国家实用新型专利一项( ZL201120528691. 4) 。随着国内客、货运输的提速及运输量激增,该产品的市场前景非常看好。
投稿箱:
如果您有机床行业、企业相关新闻稿件发表,或进行资讯合作,欢迎联系本网编辑部, 邮箱:skjcsc@vip.sina.com
如果您有机床行业、企业相关新闻稿件发表,或进行资讯合作,欢迎联系本网编辑部, 邮箱:skjcsc@vip.sina.com