基于ABAQUS固有振动频率模态分析的车床床身结构优化设计
2020-7-18 来源:1. 西安航空机械工程 2 中达电子江苏 作者:王鹏 1,王莹 1,曹敏 1,2
摘 要:利用 UG 对车床床身进行三维建模,在 ABAQUS 环境下对床身添加约束,进行模态分析,获得床身固有振动频率。通过计算获得精密车床工作时的齿轮啮合振动频率和主轴回转振动频率。 结果表明,齿轮啮合振动频率是引起床身共振的主要因素。 根据改变床身结构而改变固有振动频率的原理,对床身提出增加床身型腔数量、增加筋板厚度、改变排泄孔几何形状等 3 种结构优化方案,对优化后的床身再进行模态分析。 将床身排泄孔设计为六边形结构,可使床身固有振动频率与机床齿轮啮合振动频率相差最大,并有效地避免了共振。
关键词:车床床身;固有频率;模态分析;优化设计
车床是一种广泛应用的机械加工设备,车床床身结构的动力学特性与车床整机性能之间有着密切的联系,研究床身结构的动力学特性,对了解掌握车床整机性能及其加工精度具有重要的意义
[1]。机床上出现的振动问题有 40% 以上源自于机床的主要零部件。
床身是机床上最重要的基础零部件,尤其它的动态特性直接关系到零件的加工精度和表面粗糙度,影响着车床能否可以安全可靠地连续工作及整机的使用寿命[2,3]。机床工作时,整台设备会
处于高频率低振幅振动状态。首先,床身应具有较大的动刚度。 其次,为了避免床身振幅过大,固有频率不能与主轴, 变速箱激振频率相同, 否则发生共振。 共振效应会影响车床本身的加工精度以及疲劳寿命。
自20世纪50年代起,前苏联学者就率先对机床的结构、 振动特性及其影响因素进行研究,20 世纪 60 年代至 70 年代英国的 TOBIAS 和 KOENIGS-BERGER 对机床零件结合部进行了深入研究[4,5]。近年来, 国内外对机床床身优化设计进行了不少的探索与研究。 倪晓宇[6]等使用渐进结构优化算法对床身结构进行基于基频约束和刚度约束的拓扑优化;陈叶林[7]等以某型磨床床身为例
,对床身进行了拓扑优化和尺寸优化, 探讨了床身的筋板布局和厚度对床身刚度的影响;孙守林[8]等以 DL32M 斜床身式车床床身为研究对象,对床身结构进行优化设计研究了斜床身卧式车床的床身结构轻量化设计方法。
综上所述,目前国内外研究主要讨论了机床的尺寸、机构的布局、刚度、质量进行优化。 本文以卧式精密车床床身为研究对象,根据改变床身结构从而改变自身固有振动频率的原理,提出优化
3 种方案,通过模态分析,完成床身的结构优化设计。
1 、车床床身三维建模
利用三维软件 UG NX 8.0 对床身进行三维建模。 在模态分析时,为了提高分析运算速度,对床身模型进行简化,除去影响整机性能的尾架、主轴箱、溜板箱等,这里主要就床身进行建模。 假定床身模型为焊接件,忽略工艺圆角和螺栓孔,因为这些细微的结构不会对床身的质量及刚度产生较大的影响,同时不会影响分析计算的准确性。 图 1 为精密车床床身的三维模型。
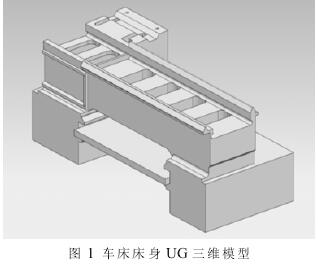
床身材料为灰铸铁铸造。 床身材料质量密度为7.8~7.9 g/cm3。 杨氏模量为 210 000 MPa,泊松比为0.3, 压缩屈服强度为 250 MPa。 通过 UG NX8.0 与ABAQUS 软件接口导入, 工作时床身定 ,给四脚添加约束。 对床身的网格使用四面体单元划分为 12 299 个单元,如图 2 所示。
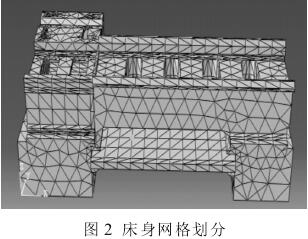
2、未优化床身的模态分析
车床加工工件时,床身会受到各种力的作用,车床上的每个零部件都会产生振动, 当振动频率与床身的固有频率相近时,容易与床身产生共振。进而产生较大的位移,降低加工精度。为了尽量避免共振现象的发生,对床身进行模态分析。
在 ABAQUS 环境下,对未优化的传统床身进行六阶模态分析,结果如图 3 所示,相应的振动频率数据列于表 1。
表1 未优化前车床床身各阶模态固有振动频率表
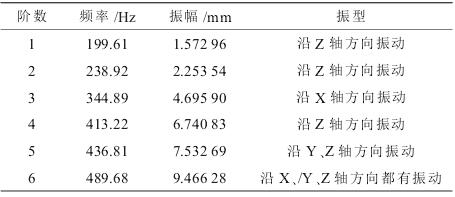
可以看出,床身变形大致在导轨、型腔、肋板和两床脚之间。 易破坏程度在图片中由颜色鲜艳至颜色暗沉依次下降,即红色最易破坏,依次黄色、绿色、蓝色递减,模态阶数越高,形变量越大
。 由表 1 可知床身固有振动频率为 199.61~489.68 Hz。
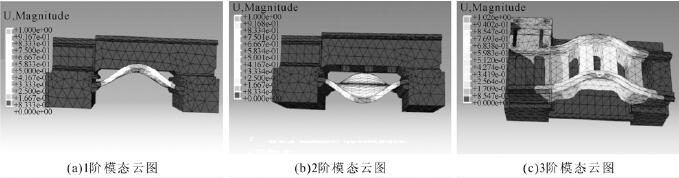
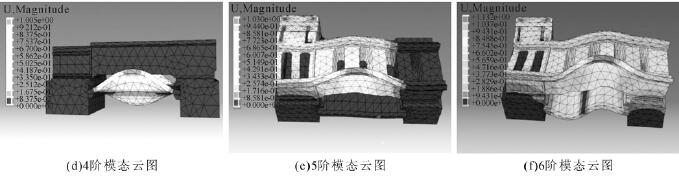
图 3 未优化车床床身 6 阶模态分析图
3 、主轴回转振动频率和齿轮啮合振动
频率分析床身振动特性的好坏直接影响整机的稳定性,机床工作时的振动频率可以避免其与自身的固有频率相同而发生共振, 进而提高机床的加工精度。机床工作时振动来自各个零件,如机床各个电动机的振动、带轮的振动、轴承形状误差和尺寸引起的振动等。
但振动频率主要来源于机床主轴回转振动频率和机床齿轮啮合振动频。 机床主轴回转振动频率是机床中不可避免的,也是引起机床振动中的主要振动之一。 卧式车床变速箱级数为 12 级,传
动副 Z=2(3)×3(1)×2(6)组合[10],齿数及各齿轮转速选择如表 2 所示。
表 2 各级齿数及齿轮转速

表 3 机床主轴回转振动频率

表 4 机床齿轮啮合振动频率

则主轴回转振动频率计算公式:
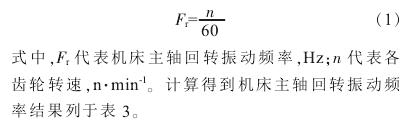
引起机床振动的另一个主要原因是变速箱齿轮啮合振动。进一步分析机床齿轮啮合振动频率,计算公式:

由式(2),得机床齿轮啮合振动频率列于表 4。由表 3, 表 4 可知机床工作时主轴回转振动频率在 1.867~15(Hz)之间变化,齿轮啮合振动频率在57.5~585(Hz)之间变化。综上所述, 由于未优化床身固有振动频率在199.61~489.68(Hz)之间变化 ,主轴回转振动频率及其变化范围较小,与床身的固有振动频率相差较大,主轴回转与床身之间不会产生共振。 而机床工作时齿轮啮合振动频率的变化范围包含了床身固有振动频率的变化范围,容易产生共振。因此需要对床身结构进行优化设计。
4 、床身结构优化设计
由表 1 可知,进行模态分析时,阶数越高,振动频率越高,振幅越大。为了避免机床床身固有频率与齿轮啮合频率的数值接近产生共振。 根据改变床身结构从而改变自身固有振动频率的原理, 本文提出了增加床身型腔的数量、增加筋板的厚度、改变排泄孔的几何形状的 3 种优化方案,如图 4 所示。
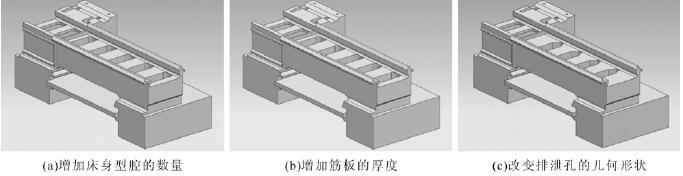
图 4 三种优化方案模型图
针对 3 种优化方案的床身结构分别进行 6 阶模态分析。 对方案一, 在原床身其他参数不变的前提下,增加床身型腔的数量。 分析可得,1、2、5 阶模态形变量大致在两床脚之间,主要形变方向在 Z 轴方向。 3、4 阶模态形变量大致在导轨之间,3 阶主要形变方向在 Y 轴方向,4 阶主要形变方向在 Z 轴之间。6 阶模态变形量几乎遍布整个床身,在 X、Y、Z 方向均有形变。 优化方案一床身 6 阶模态分析图见图 5,模态振动频率与振幅数据见表 5。对方案二, 在原床身其他参数不变的前提下,增加筋板的厚度。 1、2、3 阶模态形变量大致在两床脚之间,主要形变方向在 Z 轴方向。3、5 阶模态形变量大致在导轨之间,3 阶主要形变在 Y 轴方向,5 阶主要形变方向在 Y、Z 方向都有。 6 阶模态变形量几乎遍布整个床身,在 X、Y、Z 方向均有形变。
优化方案二床身 6 阶模态分析图见图 6, 模态振动频率与振幅数据见表 6。
表 5 方案一 床身6阶段模态固有振动频率结果表
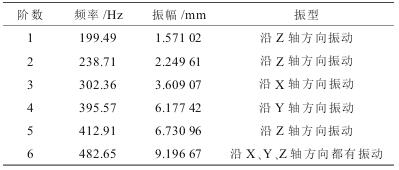
表 6 方案二床身 6 阶模态固有振动频率分析表
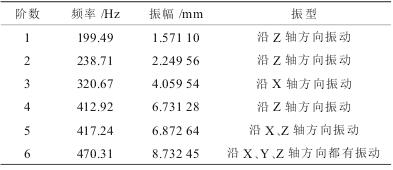
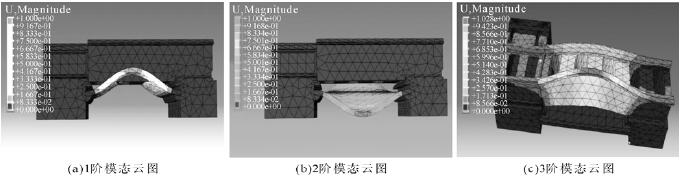
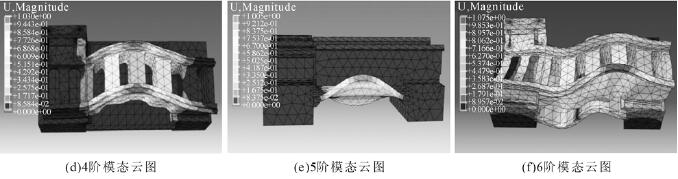
图 5 优化方案一 6 阶模态分析图
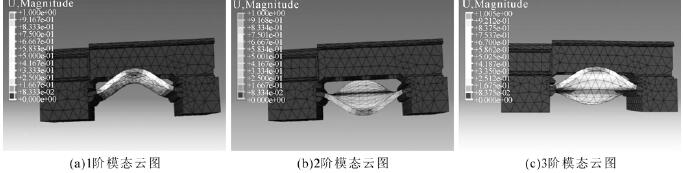
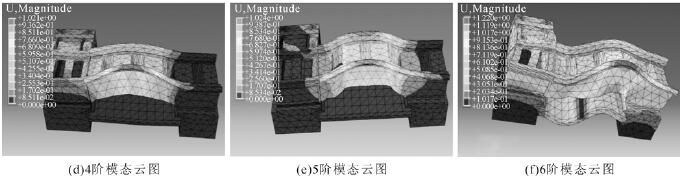
图 6 优化方案二 6 阶模态分析图
对方案三,在原床身其他参数不变的前提下,改变排泄孔的几何形状为六边形。由模态分析可知:1、2、3 阶模态形变量大致在两床脚之间 , 主要形变方向在 Z 轴方向。 4、5 阶模态形变量大致在导轨之间,四阶主要形 变在 Y 轴方向 ,5 阶主要形变 方 向 在Y/Z 方向都有。 6 阶模态变形量几乎遍布整个床身,在 X、Y、Z 方向均有形变。优化方案三床身 6 阶模态分析图见图 7,模态振动频率与振幅数据见表 7。
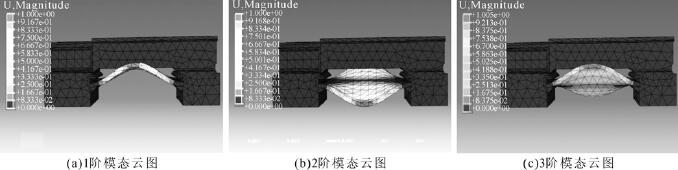
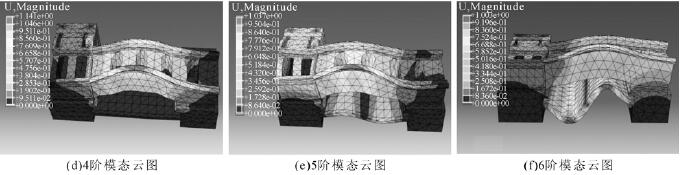
图 7 优化方案三 6 阶模态分析图
表7 方案三床身6阶模态固有振动频率分析表
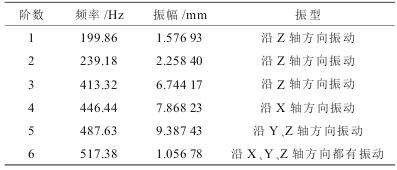
5 、模态分析结果对比
通过主轴回转振动频率以及齿轮啮合振动频率的数据 , 可知机床主轴回转振动频率在1.867~15.000 Hz 变化 , 齿轮啮合振动频率在57.5~585.0 Hz 变化 , 主轴回转振动频率与齿轮啮合振动频率曲线如图 8 所示。
根据 3 种优化方案的振动频率数据可得到优化后的床身固有振动频率曲线,如图 9 所示。
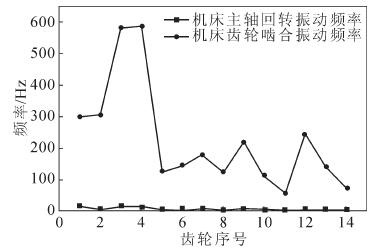
图 8 主轴回转振动频率与齿轮啮合振动频率曲线
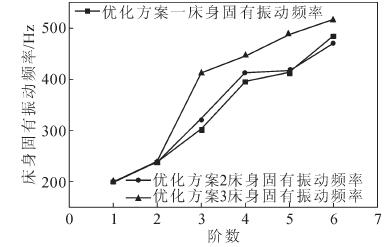
图 9 三种优化方案床身各阶模态固有振动频率变化曲线
可以看出 , 机床齿轮啮合振动频率在 57.5~585.0 Hz 进行变化。 频率范围与床身固有频率非常接近,对比如下:(1)齿轮 Z2 齿数 58 的齿轮啮合回转振动频率304.5 Hz 与方案一中的 3 阶振动模态 302.36 Hz 非常接近;(2)齿轮 Z7 齿数 34 的齿轮啮合回转振动频率178 . 5 Hz 与方案三的固有频率 199 . 86 Hz 差值最大;(3)齿轮 Z9 齿数 42 的齿轮啮合回转振动频率220 .5 Hz 与方案 三的固有频率 239 . 18 Hz 差 值最 大;(4)齿轮 Z12 齿数 91 的齿轮啮合回转振动频率 242.697 Hz 与方案三的固有频率 239.18 Hz 差值最大;综上对比结果进行分析,当车床低速工作时,齿轮啮合振动频率与 3 种优化方案下的床身固有振动频率都相差很小,共振不明显;当车床高速切削时随着齿轮转速增加,啮合振动频率也随之增加,前两种优化方案下的床身固有振动频率与齿轮啮合振动频率相差较小,容易引起床身共振,而与方案三相差最大。
因此。 采用优化方案三将床身的排泄孔设计为六边形结构。
6 、结语
通过 UG 对 床床身进行三维建模 , 在ABAQUS 环境下对床身固有振动频率进行 6 阶模态数值分析计算, 得到未优化床身的固有振动频率为 199.61~489.68 Hz。 计 算了主轴回 转振动频率以及齿轮啮合振动频率, 可知机床主轴回转振动频率为 1.867~15 Hz, 齿轮啮合振动频率为57.5~585.0 Hz。 主轴回转振动频率与床身的固有振动频率相差较大,不会产生共振,齿轮啮合振动
是产生共振的主要因素。
通过改变床身结构从而改变自身固有振动频率,提出结构优化 3种方案,对各种优化方案下的固有振动频率进行有模态分析和对比。结果表明将排泄孔设计为六边形结构,可使得床身固有振动频率与机床齿轮啮合振动频率相差最大, 有效地避免齿轮啮合振动频率与床身固有振动频率接近而产生共振, 为床身铸造时的结构设计提供了一种参考依据。
投稿箱:
如果您有机床行业、企业相关新闻稿件发表,或进行资讯合作,欢迎联系本网编辑部, 邮箱:skjcsc@vip.sina.com
如果您有机床行业、企业相关新闻稿件发表,或进行资讯合作,欢迎联系本网编辑部, 邮箱:skjcsc@vip.sina.com
更多相关信息
- target=_blank>雷尼绍——完美应对复杂繁多的零件
- target=_blank> 2020产品推介:海克斯康公司 BX 坐标测量机、3D玻璃检测系统
- target=_blank>感应淬火机床与上下料机械手控制系统的设计
- target=_blank>台车中深孔采矿中的测量方法研究
- target=_blank>TC4 钛合金深孔钻削试验研究与机理分析
新闻资讯
| 更多
- target=_blank>MB2120B型数控内圆磨床电主轴变频器的改造
- target=_blank>【雷尼绍】RESOLUTE™与MELSERVO-J5强强组合,实现更快速、精确、可靠的运动控制
- target=_blank>NSK开发低摩擦轮毂单元轴承 可增加电动汽车续航里程
- target=_blank>T68卧式镗床进给系统的数字化改造
- target=_blank>AGV+协作机器人在零件数控机床加工上下料中的应用
- target=_blank>2020年7月高端装备制造业、工业机器人,行业运行简述
- target=_blank>浅谈线切割机床中走丝与慢走丝
- target=_blank>ANCA整体PCD铣刀 —— 提高生产效率带来新的发展机遇
- target=_blank>伊斯卡,不止专注于金属加工
- target=_blank>EMAG成功收购Scherer Feinbau(舍勒公司),极大扩展了公司产品范围以及客户群体