精密机床主轴主动冷却方法研究
2025-1-9 来源: 陕西国防工业职业技术学院 作者:郭 力
【摘要】: 针对精密机床主轴的热误差控制问题,设计了基于螺旋盘管的主轴主动冷却的热误差控制方案。通过搭建主轴热特性测试系统,完成了基于 PT-400H 精密机床的主轴主动冷却系统。通过在不同冷却液温度下的主轴主动冷却的热特性实验,表明了冷却液温度对热平衡时间没有显著影响,但冷却液温度对于稳态热误差有较为明显的影响。其次,热流固耦合仿真模型可以准确反映主轴内部的生热和变形情况,预估一定实验条件下的热平衡时间和稳态热误差值,可以为工程应用提供参考。
【关键词】: 精密机床 ; 主轴 ; 热特性 ; 稳态误差
前言
大量研究表明,机床热变形所引起的加工制造误差占机床总误差的 40%~70%,主轴作为机床精密部件,它所产生热误差更是影响机床加工精度的关键。机床热误差问题已经成为影响我国精密机床发展的关键因素。
目前解决热误差主要有热误差防止、热误差补偿和热误差控制 3 种方法。热误差控制法是要控制热量的传导,减少或避免机床内部不均匀的温度分布。对于 PT-400H 精密数控机床,机床主轴内部结构,尤其是生热部件如轴承等的生热及热耗散过程造成的不均匀的温度场和变形场分布是导致主轴热误差产生的主要原因。基于螺旋管的精密机床主轴主动冷却方案可以通过冷却液循环系统液带走机床主轴系统产生的热量,改善机床主轴系统的温度分布不均匀导致的热变形问题,可以弥补机床主轴系统冷却不足的缺陷。该方案还可以针对不同的机床结构进行开发设计,满足工程实际应用的需要。
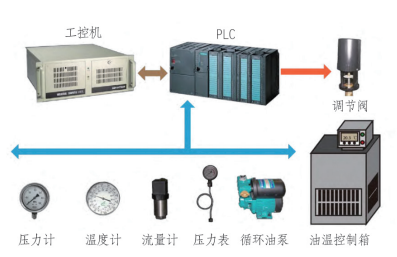
图 1 单回路的主动冷却循环系统示意图
1. 精密机床主动外冷却系统
在硬件系统搭建上,单个回路主动冷却系统由冷却循环回路、工控机、PLC 控制模块、冷却器和冷却油箱组成,如图 1 所示。
冷却循环回路的冷却液从冷却油箱出发,通过循环油泵增压,依次经过压力表、流量计、比例调节阀、进口温度计、压力计,进入到冷却器,在冷却器中与热源进行换热后,依次通过出口温度计、压力计回到冷却油箱 ;PLC 控制模块负责采集循环回路上的传感器数据和输出指令控制比例调节阀开度,同时与冷却油箱、工控机进行数据交互 ; 冷却油箱作为油箱调节的执行机构,根据输入的油温指令通过内部的 pid 控制器控制内部的电热棒和压缩机动作来调温,油温调节精度±0.1℃,冷却油箱具有实时温度屏幕显示、串口通信、PID 参数设置和自整定等功能 ; 工控机作为上位机,是控制和显示终端,进行整个系统数据的读取、存储、写入,运行控制算法。
2. 基于螺旋管的主轴外置冷却系统
螺旋流道中的二次环流在层流状态下具有增强换热的作用,同时适合主轴的柱状结构,因此主轴的外置冷却器采用螺旋式铜管的结构,结构示意图如图 2 所示,最终缠绕安装于主轴的外壳后端位置,同时主轴外壳与螺旋盘管之间填充白色导热硅脂并用卡箍锁紧以提升换热效率,在螺旋盘管的外部包裹有隔热层以尽量避免空气自然对流对螺旋冷却器内冷却液的影响,实物如图 3所示。
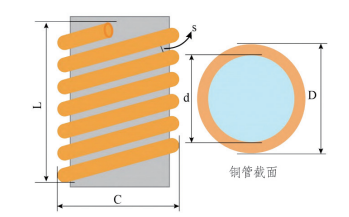
图 2 螺旋冷却器结构参数示意图
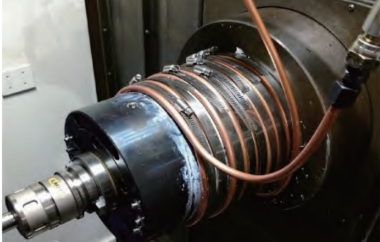
图 3 冷却器实物图
螺旋盘管的主要形状参数按照尽可能地增大换热面积,增强换热效率的原则进行设置,其中对于管径的选择,在市面上供选择的铜 管 外 径 中,6mm 比 8mm 以及更大的管径具有更好的换热效率,管径选择 6mm 的外径 ; 缠绕长度受机床实际尺寸限制,尽可能长一些,管间距则尽量小一些,螺旋盘管的参数选择见表 1。
表 1 螺旋冷却器的形状参数设置

基于螺旋盘管的主轴主动冷却系统实物如图 4 所示,冷却液选择为 4 号主轴油,针对主轴循环回路,除了上述回路中通用的传感器外,在主轴顶部(Y+)开孔在靠近轴承的地方安装了一个温度传感器,通过 PLC 采集至力控数据库,从而可以实时监测主轴系统内部温度。此外,主轴电气回路上串联了功率计以实时监测该回路的电压、电流、功率等参数。
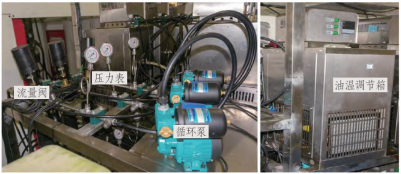
图 4 主轴主动冷却系统实物图
3. 热特性测试系统
机床热特性测试分为温度和位移测量,温度测量的主要方式是采用接触磁吸式温度传感器吸附于待测测点进行测量,同时为了得到整个温度场的全貌,采用红外热像仪测量进行补充 ; 位移测量对于主轴而言,采用非接触式的位移涡流传感器,测量的是主轴在运行过程中相对于初始位置的各个方向的偏差。
①主轴热特性测试原理
精密机床主轴的热误差通常采用五点法进行测量,通过在主轴的周围布置电涡流位移传感器,测量得到主轴的轴向和径向位移,进而通过计算可以得到主轴的空间姿态,本文仅关注主轴的轴向位移,测量示意图见图 5。主轴在多热源的综合影响下发生变形,主轴的轴向位移 ΔL1 为 :
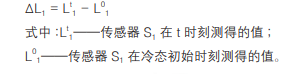
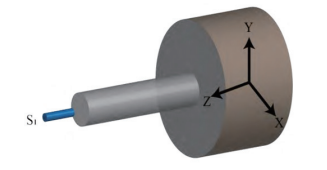
图 5 主轴轴向位移测量
②主轴热特性测试系统
主轴热特性测试采用的设备为开发的基于 NI SCXI-1600 采集卡的温度位移同步采集系统,系统内各硬件参数指标见表 2。传感器的温度和位移信号通过温度变送器及位移调理模块转变为电压和电流信号最终送入基于SCXI-1600采集卡的采集模块,工控机通过 USB 与该模块相连,工控机上建立采集程序对信号进行显示和存储,温度 / 位移同步采集系统外观见图 6。
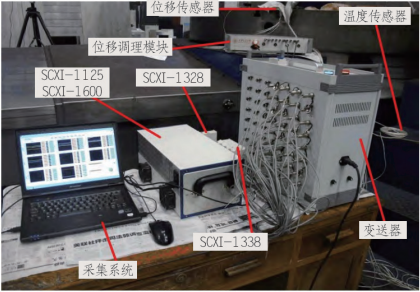
图 6 温度 / 位移同步采集系统实物图
系统的软件页面基于 Labview 搭建,实现对最多 64 路信号进行数据显示、存储,记录实验信息,软件采集界面如图 7 所示。每 8 路信号置于一个示波器中显示,可以根据实验需要随时调整,隐藏不需要的通道。Lab view 采集频率设置为 1Hz,即每隔 1s 对所有通道数据进行一次采集,将采集数据实时地采用插入指令导入至 SQL Server 数据库,每一次实验对应一条实验记录以及相应时间段内的实验数据,采用数据库存储的形式便于实验数据的备份、查询、处理、与其他设备采集数据的混合处理以及与其他软件进行数据交互。
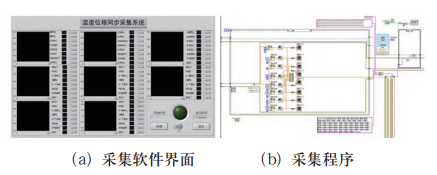
图 7 温度 / 位移同步采集系统界面
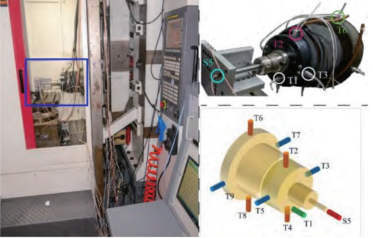
图 8 精密机床主轴温度 / 位移传感器位置
表 2 温度位移同步采集系统参数
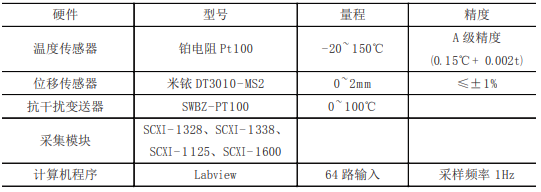
本研究中对于精密机床主轴热特性测试的位移传感器布置在主轴末端,温度传感器布置如图8 所示,通过磁吸附的方式主要安装在了法兰表面和主轴外壳表面,具体位置分别为 :T1——法兰、T2——前 Y+(深入主轴内部,靠近主轴前轴承)、T3——前 X-、T4——前 Y-、T5——前 X+、T6——后 Y+、T7——后 X-、T8——后 Y-、T9—— 后 X+。
4. 实验与仿真分析
机床的热平衡对保证机床的加工精度具有重要意义,在无冷却下机床运行时,热误差缓慢上升直至稳态非常缓慢,热平衡时间常常会达到数个小时甚至更多,采用热误差值的变化规律作为热平衡的判定依据,定义热平衡时间为热误差达到稳态值 90% 的时间。针对机床加工中常见的主轴恒速工况(1000r/min),在 Ansys 仿真平台上建立了主动冷却下的 PT-400H 数控机床热流固耦合仿真模型,对 19℃环境下主动冷却的主轴热特性进行热流固耦合仿真。不同冷却液温度下的主动冷却的主轴热特性进行仿真实验 ,仿真时间为 0-300min,图 9 是不同温度下的实验结果和仿真对比。
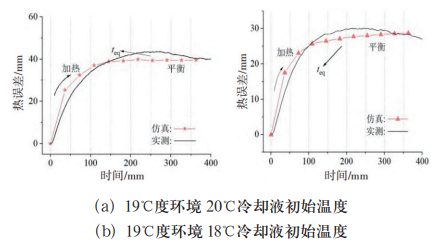
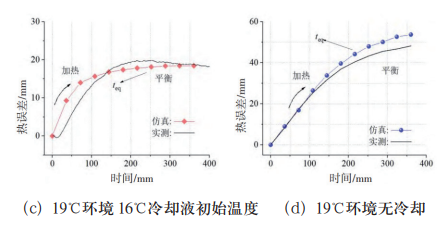
图 9 19℃环境的仿真与实验对比
从上图中可以发现,在 20℃恒温冷却下的实验热平衡时间为 150min,热误差稳态值为 43.4μm; 在 18℃恒温冷却下的实验热平衡时间为 123min,实验热误差稳态值为 30.1μm; 在16℃恒温冷却下的实验热平衡时间为 154min,实验热误差稳态值为 19.8μm; 在无冷却下的实验条件下,可以看到在 300min 后仍未达到热平衡。
同样的,在 20℃恒温冷却下的仿真热平衡时间为 147min,仿真热误差稳态值为 38.1μm;在18℃恒温冷却下的仿真热平衡时间为155min,仿真热误差稳态值为 27.6μm; 在 16℃ 恒温冷却下的仿真热平衡时间为 135min,仿真热误差稳态值为17.4μm;在无冷却下的条件下可以看到仿真数据在 300min 后仍未达到热平衡。
5. 结论
文章以PT-400H精密数控机床为研究对象,针对主轴结构设计了主动冷却螺旋管,搭建了主动冷却的主轴冷却系统,通过不同冷却液温度下的主动冷却的主轴热特性实验可以得到以下结论 :
①对不同冷却液温度下的主轴实验与仿真结果对比,对于恒温冷却实验,冷却液温度对热平衡时间没有显著影响。
②在 19℃环境下主轴常用 1000r/min 工况对不恒温冷却温度下热特性仿真,几组仿真与实验对比结果显示,热平衡时间最大误差率大约为 26%,稳态热误差最大误差不超过 15%,; 相比于 20℃恒温冷却,18℃、16℃的稳态热误差值分别下降了 27.7%,54.3%,说明冷却液温度对稳态热误差有较为明显的影响。
③热流固耦合仿真模型可以准确反映主轴内部的生热和变形情况,预估一定实验条件下的热平衡时间和稳态热误差值。在此基础上,对于不同的环境及工况下的热误差闭环控制实验,可以针对实验环境进行仿真,从而为热误差控制目标值和初始油温设定值提供参考。
投稿箱:
如果您有机床行业、企业相关新闻稿件发表,或进行资讯合作,欢迎联系本网编辑部, 邮箱:skjcsc@vip.sina.com
如果您有机床行业、企业相关新闻稿件发表,或进行资讯合作,欢迎联系本网编辑部, 邮箱:skjcsc@vip.sina.com
更多相关信息