基于嵌入式PLC的数控机床自动控制系统
2020-11-2 来源:陕西机电职业技术学院 智能制造学院 作者:孙钊
摘 要:随着科技不断进步,PLC控制器在数控机床得到了广泛地应用。以控制器框架结构为基础,研究数控机床的自动控制系统,计算并比较系统内重要的运行参数,并结合硬件结构的不同属性,对嵌入式 PLC系统方案进行分类。研究结果显示,PLC自动化控制系统具有较高的抗干扰能力,可提高系统运行的准确性和稳定性;滚动轴的导程由电机运转速度和移动杆的转动速度决定,当电机运转速度越高时,导程的数值越小,反之则越大。研究结果为数控机床自动控制系统性能提升提供了科学依据。
关键词:PLC;数控机床;自动化;控制系统
0、引言
现在工业的自动化、集成化以及柔性化是提高劳动生产率、提升产品质量的基础。而随着科技的不断进步,使 得 数控机床的 控 制 电 路 由 传 统 的 继 电 器 逻 辑 电 路 RLC(RelayLogic Circuit-RLC)逐 步 升 级 为 可 编 程 逻 辑 的 控 制 器 PLC(Programmable Logic Controller-PLC),其 PLC 控制系统的发展是以传统的继电器、接触器控制为基础,采用特殊的存储介质,为特殊的用途而设计出来,主要实现内部介质存储、运算过程分析、程序结构控制等功能,控制各种类型的机械或生产过程,其在数控机床中常以内装式和独立式两种形式存在。在机械 行 业 的 应 用 过 程 中,可 以 大 大 的 节 省 人 力 劳动,提高工业生产效率,因其逻辑编程操作简易,具有较高的抗干扰能力,提高了系统运行的准确性和稳定性。本文就针对于在 PLC的基础之上研究数控机床的自动控制系统的设计。可编程逻辑控制器是一种以微处理器为基础的数字运算电子系统,该系统在数控机床自动化控制中的应用,使得整个系统的运行稳定性和有效性大大提高。PLC 是一种可编程控制器件,其存储器类型属于可编程存储器,完成系统指令下达、数据逻辑运算、计算顺序控制等功能,通过数字式的信息处理方式实现输入输出方式对相关机械的自动化生产控制。该控制器属于新型的工业控制器,既能控制开关量,也能控制模拟量,也可以将计算机与自动化控制技术相结合,同时利用大量的集成电路技术,大大的提高整个系统运行时的抗干扰性,使得系统持续不断的工作,从而提高生产效率,PLC集成体积小,编程简单,适应性强等特点,使得 PLC在机械工业中的使 用 范 围 越 来 越 广,同 时 对 复 杂 的系统进行综合梳理并对系统实现控制。
1、PLC数控系统
1.1、PLC硬件框架
PLC数控系统相较于传统的计算系统具有对周围环境适应性强、程 序 语 言 识 别 速 度 快 和 系 统 编 程 稳 定 性 好 等 特点,同时 PLC数控系统在实 际 的 生 产 过 程 中 对 硬 件 接 口 具有较高的适应性。因此,对于数据控制单元由系统内的硬件组成和用户使用环境构建,二者相互联系,组成了 PLC 数控系统的基础单元结构,如图1所示。
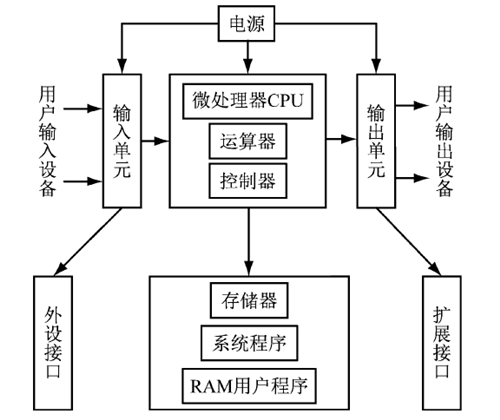
图1 PLC硬件组成框架
PLC硬件组成框架主要由内设接口和外部接口两大部分构成,其中内设接口包括用户输入单元、用户输出单元、微处理器 CPU、运算器和控制器,当输入单元和控制单元接通电源后,输入单元采集用户的设备的基本信息,以电信号的形式传输到控制单元,经过微处理器 CPU 对接收信号分析和运算器综合计算,以数字信号的形式传输到控制单元,对传输信号进行编码解析,最后输出至用户设备;系统内的输入单元对应外设接口,输出单元对应扩展接口,同时,在外设单元中还包含存储器、系统程序、RAM 用户 程 序。以上单元接口在系统程序的控制下,可以将用户的信息进行及时存储,在运算的过程中对程序的正确性对照检查,保障内部构件的准确性和完整性,最后将运算的程序存储于系统的结构单元,并将用户的信息在存储设备识别并读取,通过编译器将程序信号转化为数 据 信 号,以 此 实 现 PLC 数 控 系 统 的全部功能。
1.2、数控系统构成
数字控制(Numerical Control)对于以数字化的信号对机床的运行和使用实现控制。其数控机床的主要构成部分由程序介质、数控装置、伺服系统以及机床主体四部分组成,如图2所示。
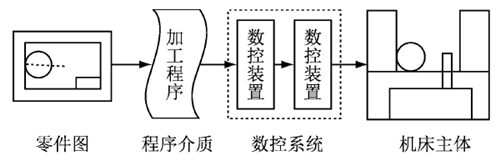
图2 数控机床的组成
加工编码是将零件加工程序使用相应的格式和代码存储在一种程序载体上,同不同类别数控机床进行对比,将这些程序 信 息 输 入 到 CNC(Computer Numerical Control)单元。数控系统包括数控装置和伺服系统。其中数控机床的主要组成部分是主控装置,采用多个微处理器的 CNC 装置,根据输入数据,对所有需要输出的零部件采用编码处理;伺服系统是 PLC系统中处 于 核 心 位 置,实 现 数 控 机 床 的 进给伺服控制和主轴伺服控制。机床主体就是为了加工零件,是数控机床的主要部分,包括机体、主轴箱、刀架等机件。其作用是处理各 种 原 材 料,按 照 预 设 的 零 件 构 图 进 行 加 工 设计。在实际的数控机床运行过程中,很有可能会发生紧急突发的状况,操作人员的失误可能导致整个生产的失误。在数控机床的自动控制系统中,为了避免突发事件,会增加图书的设计结构,比如紧急按钮和导程等部件。
2、系统参数计算
机床运动参数计算是系统正常运行的保障,针对机床的参数计算需要掌握其重要的部件,机床中的滚动轴是正常稳定运转不可或缺的部分,常规滚动轴的轴心分别朝向固定面板的两端,从而确保运行平稳,PLC 系统的机床涉及的参数种类多,需要对重要的参数进行计算并比较,为机床及时检修提供数据支撑。
机床滚动轴的重要指标是导程,在机床设计过程中根据接触表面的光滑程度来制定适合的机床部件,例如结合材料力学选取符合要求的物理参数,将参数类型进行归整,作为PLC的数控机床生产的重要指标。滚动轴的导程由电机运转速度和移 动 杆 的 转 动 速 度 决 定,当 电 机 运 转 速 度 越 高时,导程的数值越小;当机床移动杆的转动速度越大时,导程的数值越小。滚动轴导程的计算公式如式(1)。
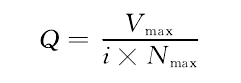
式中:Nmax为电机运转速度,单位为 m/s;Vmax为移动杆转动速度,单位为 m/s;i为传动比,这里取值为1;Q 为滚动轴的导程。
数控机床滚动轴不同的安装方法,其在接触面的受力也不尽相同,结合机床构造和工程力学,最小安装直径受电动机的运转速度、使用材料的伸缩程度、转动杆的承受荷载和固定端到自由端的距离决定的,其计算公式如式(2)。
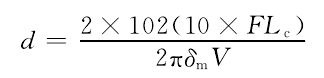
式中:V 为电动机的运转速度,单位为 m/s;δm为材料的伸缩程度;F 为转动杆 的 承 受 荷 载,单 位 为 N;LC为 固 定 端 到 自由端的距离,单位为 m。
数控机床在运行过程中,需要对其运行荷载 进 行 计 算。如果接触面的承受荷载远大于它的运行荷载时,就会出现不平稳运行,甚 至 产 生 安 全 事 故。因此计算数控的运行荷载非常重要,该荷载主要由转动轴的稳定系数、材料的弹性模量、移动杆的惯性矩、转动轴的移动距离决定,数控机床运行荷载的计算公式如式(3)。
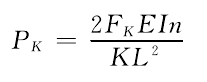
式中:PK为 运 行 荷 载,单 位 为 N;FK为 转 动 轴 的 稳 定 系 数(双轴时为2,单轴时为1);E 为材料的弹性模量,单位为 Pa;I为移动杆的惯性矩,单位为 m2;L 为转动轴的移动距离,单位为 m。
3、嵌入式PLC控制系统
嵌入式 PLC系统 的 内 部 硬 件 结 构 有 着 较 大 的 差 别,结合硬件结构的不同属性,嵌 入 式 PLC 系 统 按 照 组 成 结 构 不同可分为:传统 PLC控制方案、内置控制器运行方案和计算机通信接口控制方案,根据方法和过程不同控制方案如下:
(1)传统 PLC控制方案
传统 PLC控制方 案 中 是 以 计 算 机 为 基 础,将 运 算 程 序以系统的组成部分为单元,固定在系统的硬件结构中,如图3所示。

图3 传统 PLC系统结构框架
PLC运行系统与 PLC开发系统以信号交互形成通信体系,结合系统的使用要求对在计算机平台编写的程序代码,以数据信号的形式传输到下一个接口处,并实现系统数据控制和程序运行。
(2)内置控制器运行方案
内置控制器是 PLC 系 统 独 立 的 组 成 部 分,该 系 统 的 重要组成部分为微型处理器,主要实现在指定系统中完成信号接收、数据分析及代码编译,以系统硬件组成的方式嵌入在系统结构中,实现控制系统信号交互及数据通信等功能,如图4所示。

图4 内置控制器结构框架
在 PLC运行系统中嵌入式控制器与 PLC开发系统实现数据通信功能,根据开发系统和运行系统分析,在标准的通信协议下完成交互信号与运行系统和数据接口准确对接,实现数据信号实时交互。
(3)计算机通信接口控制方案
在计算机通信接口控制系统的硬件部分主要由控制计算机、系统总线 接 口 和I/O 接 口 组 成。PLC 开发系统和运行系统根据网络I/O 接口 进 行 数 据 交 互,同 时 PLC 运 行系统与I/O 接口和系统总线接口实现信号传递,以上结构单元组建控制计算机与网络接口完成信号控制。计算机通信接口框架结构,如图5所示。
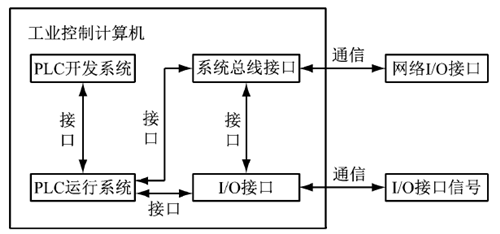
图5 计算机通信接口结构框架
4、基于PLC的控制系统设计
4.1、基本功能
PLC技术相对于传统的控制技术拥有特殊的功能,在系统组成部分拥有多项的基本功能,其基本功能如下。
1)PLC技术以强化逻辑运算功能为目标,功能介于中心主要数据控制和配电装置核心功能相互转化;
2)有专一的存储用户程序的存储器,对复杂的控制对象以及控制逻辑更灵活,其用户程序采用的逻辑顺序关系和传统的继电器电路十分相似的梯形图形编辑;
3)PLC可以和多种外部的设备进行连接,更方便的实现程序的显示、编辑等功能;
4)PLC具有较高的抗干扰能力,体积小,摒弃了传统继电器的接触不良、磨损等特点;
PLC技术 在 实 际 的 生 产 中 起 到 了 重 大 的 作 用。采 用PLC的数控机床机构更加紧凑,功能更加丰富,在自动化程度较高的生产制造系统和加工设备中,PLC是一种不可或缺的控制装置。
4.2、PLC控制系统组成
PLC采用典型的计算机结构,由 CPU、输入、输出接口电路、读写存储器等,该系统可以看成由变量的信号输入和信号输出变量组成,此时的 PLC 相当于一个中间处理器,将输入的 变 量 经 过 一 定 的 编 程 程 序 的 处 理 以 得 到 输 出 变量。其控制结构图,如图6所示。
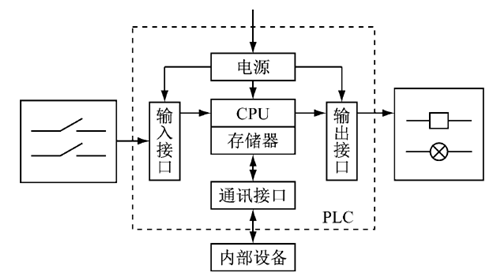
图6 PLC系统基本功能框架图
输入部分 此 部 分 的 输 入 端 子 与 按 钮 开 关、液 位 报 警 开关、压力检测开关等连接,主要用来收集系统中的各种实际数据,以重复扫描的方式进行用户程序的执行,并按照程序事先编写好的地址将输入信号读入输入映像寄存器中并执行,程序执行过程中,以扫描周期为周期进行获取输入数据。控制部分此部分按照被控对象的实际控制要求所编写的用户程序进行反复执行,并按照顺序进行扫描执行,并将执行结果写入有关输出映像的寄存器中。输出部分该部分的输出端子与接触器、三色警报、驱动使能等连接,是电路的输出状态,用于控制被控制对象的动作操作。根据所设计需要的输出模式,完成指定的操作,并将输出映像寄存器中的状态转移到输出锁存寄存器中,实现外部负载。
4.3、PLC模块化设计
本次设计中,将 PLC模块划分为5个模块,公共信号模块、基本控制 模 块、刀 架 模 块、主 轴 模 块 和 报 警 模 块。其中公共信号模块的主要作用是将 PLC 和 NC 之间的信号进行相应的处理;基本控制模块的主要作用是程序的启停、紧急处理等;刀架模块主要是实现选择合适的刀架、以及对刀架的定位等逻 辑 控 制 功 能;主 轴 模 块 主 要 是 对 主 轴 的 正 反转、主轴定位等进行控制,并通过 PLC 的编程实现参数的修改等;警报模块主要是机床的故障、人为误操作等进行检测并同时给以反馈警报信息等。该模块的功能实现可以通过一个主程序以及若干的子程序一起完成,实现对机床的各种控制作用,其主要的子程序结构,如表1所示。
数控机床中 PLC 技术 的 实 现 的 基 础 就 是 程 序 指 令,相应的指令会将信号和程序纳入控制体系中。PLC 技术的运用,可以实现整个控制系统的升级以及改进,在实际的运行过程中实现高效率的数控机床控制,并对该系统结构进行不断地优化,从而升级数控机床的控制性能。
表1 主要子程序库结构
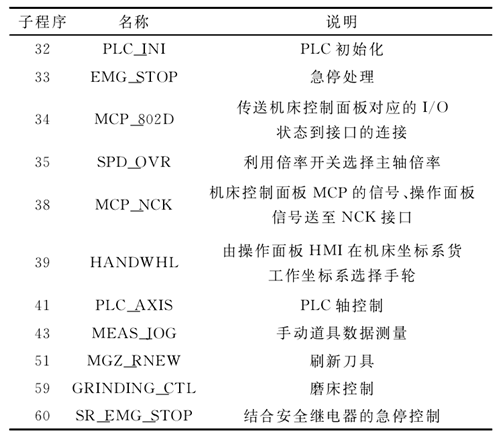
5、总结
在我国经济和社会的快速发展中,对数控机床的需求不断的提高,而 PLC在数控机床中的应用,不仅大大的提高了整个系统的生产效率,而且有效的实现数控机床的自动化控制,对提高企业的经济效益有很大的益处。结合当今数控系统的特点,要不断地改善 PLC的功能,特别是完善和改善上位机软件的功能,以及对数控系统编程语言的进一步统一,这些问题的解决,会使得我国数控系统性能得到很大的提升。
投稿箱:
如果您有机床行业、企业相关新闻稿件发表,或进行资讯合作,欢迎联系本网编辑部, 邮箱:skjcsc@vip.sina.com
如果您有机床行业、企业相关新闻稿件发表,或进行资讯合作,欢迎联系本网编辑部, 邮箱:skjcsc@vip.sina.com
更多相关信息