PCKF1825 可逆双反击锤式破碎机回转部的优化设计
2020-4-3 来源:北方重工富勒( 沈阳) 矿业有限公司 作者:赵冬博 李乐
摘要:针对 PCKF1825 可逆双反击锤式破碎机在实际投入使用后发现的诸多问题,进行了深入的研究和分析,运用 Solidworks 软件对回转部建立三维模型,优化关键部件并对主轴进行仿真模拟校核,最终达到了降低设备维护成本、延长部件使用寿命、强化设备整体性能的目的。
关键词:可逆双反击锤式破碎机 回转部 锤头 锤盘 Solidworks 主轴
PCKF1825 可逆双反击锤式破碎机是一种新型的破碎设备,回转部是其关键部件,尽管该设备与传统 PC 型锤式破碎机相比有诸多优势,但在实际使用中也存在锤头、锤柄组件更换率高,锤盘磨损严重等问题,这给设备的使用效率和经济效益带来直接影响。为解决上述问题,运用 Solidworks 软件对设备回转部进行了优化设计和主轴校核。优化后的设备在投入使用后,提高了整体性能,满足了设计和工作要求。
1、 PCKF1825 可逆双反击锤式破碎机
PCKF1825 可逆双反击锤式破碎机( 以下简称:PCKF1825 锤破) 破碎原理是物料通过锤头组件的高速旋转将其打击,在经历两次破碎后进入主破碎腔,高速冲向左右两侧的锯齿形齿板,通过被锤头和齿板的反复破碎,最后从出料口排出,完成破碎。设备主要由破碎机主体、电动机、液力偶合器及液压站等组成。破碎机主体主要由中箱体、侧箱体、底座部及回转部组成。
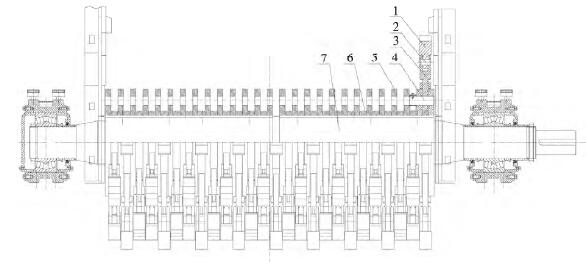
图 1 原回转部结构示意
1—锤头; 2—锤头销轴; 3—锤柄; 4—锤柄销轴; 5—锤盘; 6—隔套; 7—主轴
回转部( 见图 1) 是整台设备的核心部分,主要由主轴、锤盘、锤头组件及轴承座等组成。其回转部采用大转子多锤头,电机为高速度。同样的电机功率,当转子直径加大时,其线速度加快,从而可加大打击力度,提高破碎能力,节省能源。主轴的两端支撑在轴承座上,轴承选用专用轴承,可自动调心,能承受较大的动载荷和震动。轴上固定有许多锤盘,在锤盘之间通过锤柄销轴连接锤头组件,锤头组件由锤头、锤柄、锤头轴、锤柄轴等组合而成。锤头采用了特种耐磨合金材料制成,安装好的锤柄、锤头可正反两面使用。回转部是可逆的,当一侧锤头与反击板磨损过大时,可使转子反向旋转,利用锤头与反击板的另一面工作,尽可能的延长使用寿命。
2 、优化设计的必要性
尽管 PCKF1825 锤破与传统 PC 型锤式破碎机相比有诸多优势,例如采用由特种耐磨合金材料制造的锯形齿板和锤头,金属利用率高; 可逆的回部,具备高转速、大破碎比、能耗低的性能,可以正反转进行工作,提高了锤头和齿板的利用率,延长了其使用寿命; 左、右箱体下部的偏心调节器使破碎腔内左右箱体同步变化,克服了分点调节因错位而引起的同侧箱体间隙不均,保证出料细度均匀,提高出料细度百分率等特点; 但在设备实际投入使用后,尤其是在破碎铁矿石的过程中,出现了以下问题:
( 1) 锤头组件磨损很快。锤头组件( 见图 2) 是锤式破碎机最为关键的零部件之一,PCKF1825 锤破原设计所采用的是组合式的锤头,由锤头、锤柄和销轴等零件组成,其中锤柄是焊接件,是连接锤盘和锤头的重要部件。尽管锤头的材质是耐磨合金,在破碎物料过程中,尤其是破碎铁矿石时,即便矿石硬度为中等硬度,锤头组件的磨损率依然很高。按设备每天平均工作 16 h 计算,大概 4 ~ 5 d 就要将 1台份( 共计 104 个) 锤头组件全部更换 1 次,更换至少需要 1 ~ 2 d。在更换的同时还需要对锤头组件进行配装,个别锤头组件还需要打磨修整。
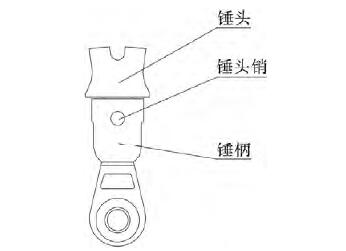
图 2 原锤头组件结构示意
锤头组件磨损率过高的主要原因是锤柄,因为锤柄是焊接件,耐磨性不高,而其本身又是连接锤盘和锤头的主要部件,所以在破碎物料的过程中,锤柄的磨损在所难免,而且锤柄的过度磨损直接影响锤头对破碎物料的使用效率及性能,同时也无法给锤头良好的支撑。尤其是当锤柄磨损率达到某一程度时,将无法固定和支撑锤头,在转子极大的惯性力作用下,锤头很可能受到离心力的作用,脱离锤柄,随惯性飞出,在破碎机腔内不规则运动,对设备生产安全和使用寿命产生严重影响。此外,锤头的磨损使其有效的打击面积变小,在运转中不能对物料进行充分的打击破碎和对锤盘及主轴进行有效的保护。
( 2) 锤盘磨损严重。对于磨损的问题不止于锤头组件,锤盘的磨损也同样存在,尤其是锤盘的外圆,PCKF1825 锤破破碎腔有效长度为 2 458 mm,在该跨度中均匀分布 27 个锤盘,锤盘直径为 800 mm,单个锤盘的厚度为 40 mm,两个锤盘之间圆周方向均布 4 个锤头组件,整个回转部的锤头交叉排列。虽然设备运行时回转部是高速运转的,物料在破碎腔内受到锤头的打击破碎,但也有部分物料在受到打击产生反弹之后会不规则的打击到锤盘外圆,锤盘外径与左、右箱体最小距离至少有 500 mm,给物料足够的势能和打击空间,再加上物料被打击到齿板之后所产生的反弹力,这对于普通碳钢材质的锤盘是极大的冲击,尤其对锤盘外圆更是造成严重的磨损。原设计并未充分考虑上述几点,也未针对锤盘外圆进行有效的耐磨保护,进而造成锤盘外圆磨损严重。原锤盘结构示意见图 3。
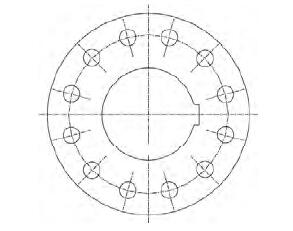
图 3 原锤盘结构示意
3、 改进方式及优化设计
通过对上述问题的分析、研究与总结,决定对PCKF1825 锤破回转部进行针对性的优化设计。在保证左、右箱体所组成的破碎腔空间尺寸不变的情况下进行改进优化。
3. 1 锤头的改进和优化设计
将原来的组合式锤头改为一体式锤头,取消不耐磨的焊接锤柄。同时,加大锤头的外廓尺寸,增加破碎的有效面积,提高锤头整体的耐磨性,通过对铸造工艺的研究,在铸造时加入磁性元素,使新型锤头表面呈弱磁性,这样在破碎铁矿石时,物料粉末就可被吸附在锤头上,对锤头进行有效的保护。通过理论设计和设备实际运行情况分析,新锤头( 见图 4) 采用整体铸造结构,锤头厚度由 90 mm增加到 110 mm,整体长度变短至 390 mm。将锤头设计变短的原因主要是: 降低锤头受到离心力和惯性力矩的影响,提高锤头的运转安全性; 降低更换锤头的时间和经济成本。通过计算和 SolidWorks 模拟分析,对锤头的质量和打击平衡中心进行了重新计算,同时保留原锤柄位置的限位块设计,锤头重量由39 kg 降至 29 kg。
改进后的锤头外廓尺寸更大,破碎物料的有效面积更大,取消锤柄、销轴等零件,也避免了锤柄的不耐磨和销轴因受到循环应力而产生松动或断裂[1]。使锤头的耐磨性、安全性、使用寿命都有所提高,同时对锤盘也起到了更好的保护作用。
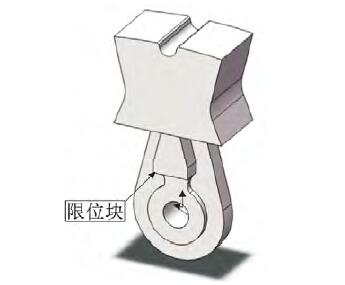
图 4 改进后锤头结构示意
3. 2 锤盘的改进和优化设计
在回转部整体外径保持不变的基础上,由于锤头整体变短,所以锤盘外径相应增加,由 800 mm增加到 1 125 mm,进一步减小了物料在破碎腔内对锤盘的打击空间,使物料在更合理的破碎腔空间内被高效破碎。改进后的左、右两端的锤盘( 见图5) 厚度由 40 mm 变为 45 mm,中间锤盘( 见图 6) 厚度由 40 mm 变为 33 mm,图 5、图 6 中锤盘圆周黑色边缘部分是在锤盘外圆堆焊耐磨层[2],堆焊厚度约为 5 mm,目的是为了保护锤盘,提高耐磨性。
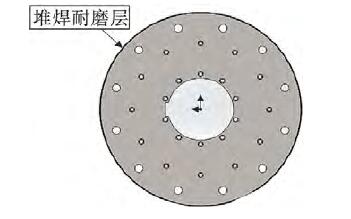
图 5 端部锤盘结构示意
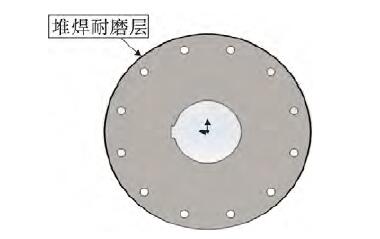
图 6 中间锤盘结构示意
3. 3 回转部整体改进和优化设计
在对回转部两个主要零件改进后,再将锤盘、锤头进行重新布置,由于锤头的外廓尺寸加大,锤盘的厚度也有所变化,所以在保证主轴整体装配长度不变的情况下,将锤盘间距由 53 mm 变为 61 mm,锤盘总数由原来的 27 件/台变为 26 件/台,锤头数量由原来的 104 件/台变为 100 件/台。其次,由于锤盘外径的增大,在装配过程中,为保证各锤盘之间的间距及垂直度,在每两个锤盘之间增加 1 个支撑隔套。支撑隔套的固定方式是将隔套一端采用断续焊的方式与锤盘焊成一体装配在主轴上[3]。改进后的回转部结构示意见图 7。
3. 4 利用 Solidworks 校核主轴
在对回转部优化设计后,虽然整体结构形式变化不大,但主要零部件的尺寸、重量、数量等参数均有所改变,这些参数的改变对主轴的强度产生了一定的影响,使主轴承受的总载荷有所增加。原回转部主轴上承载的部件总重为 8 143 kg,改进后总重增 加至9 583 kg ,总 载荷增加 了约18 个百 分 点 。
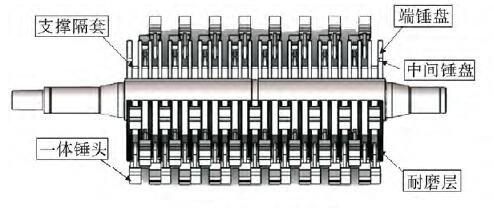
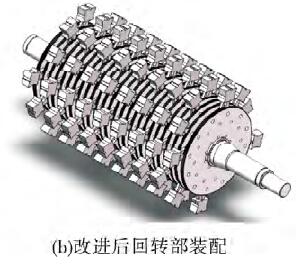
图 7 改进后的回转部结构示意
运用 Solidworks 对主轴进行模拟分析,在固定主轴两端轴承座位置的圆柱面后,对主轴的主要承载表面均布施加 一 个 100 kN 的 外部 载荷,然 后通 过Solidworks 对主轴进行强度运算得出结果。运算主要考察主轴的应力、位移及应变情况,看其是否仍满足设计要求。运算结果见图 8。由运算结果可知,主轴的最大应力为4. 56 MPa,最大位移量为 0.011 mm,最大应变为1.3 × 10- 5。由于主轴材质为 45 号钢,调质后的抗拉强度为 590 MPa,根据轴的材质和抗拉强度,查询机械设计手册[4]得其许用应力为 95 MPa。主轴的最大应力远小于其许用应力,最大位移和最大应变对主轴及回转部的整体影响也极小,基本可忽略不计,故主轴仍满足设计和工作要求。
4、 结 论
( 1) 通过对 PCKF1825 可逆双反击锤式破碎机回转部的性能研究,结合设备在实际运行中回转部锤头、锤盘等部件出现的问题,运用 Solidworks 三维软件建立模型,对回转部、锤头、锤盘进行结构分析和优化设计,对改进后主轴重新校核,确认仍满足设计和工作要求。
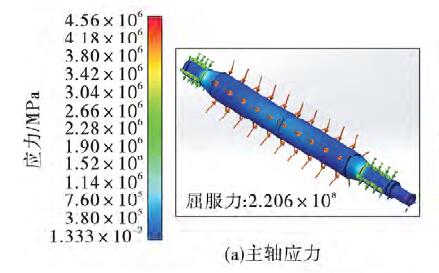
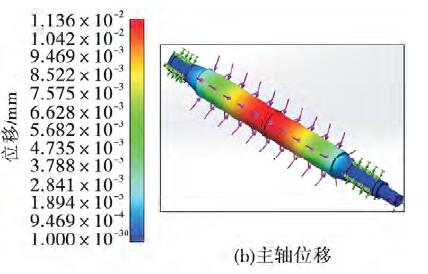
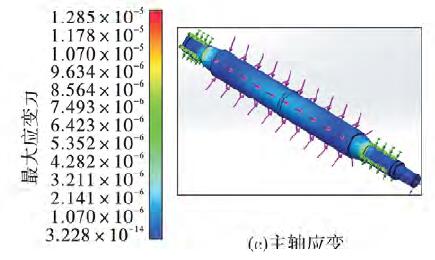
图 8 主轴强度校核
( 2) 采用一体化高强度锤头、锤盘堆焊耐磨层等设计方案使部件的耐磨性和抗冲击性均有很大改善,提高了 PCKF1825 可逆双反击锤式破碎机的技术性能。
( 3) 据现场实际应用情况反馈,改进后锤头平均使用寿命由 5 d 增至近 20 d,锤盘磨损情况有了根本性改善,更换锤头的次数和更换时长也明显降低,设备运行时间和使用效率明显提高,降低了维护成本和更换部件所产生的费用,提高了经济效益。
投稿箱:
如果您有机床行业、企业相关新闻稿件发表,或进行资讯合作,欢迎联系本网编辑部, 邮箱:skjcsc@vip.sina.com
如果您有机床行业、企业相关新闻稿件发表,或进行资讯合作,欢迎联系本网编辑部, 邮箱:skjcsc@vip.sina.com
更多相关信息