基于直线电动机和滚珠丝杠驱动的应用对比
2019-9-12 来源:东风日产乘用车公司 作者:唐行虎
摘要:本文从功能原理、技术参数、应用实例方面对滚珠丝杠和直线电动机驱动的加工中心性能进行了全面的对比,展现了直线电动机的优越性能和发展态势。
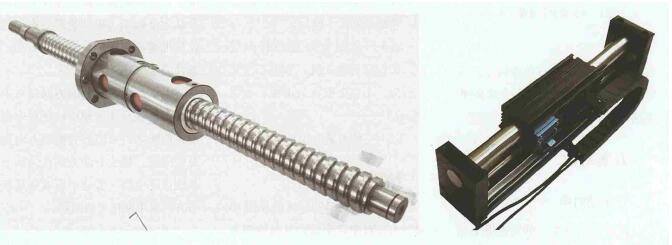
滚珠丝杠在机床行业的普遍应用,推动了加工机床行业的快速发展,但机械式传动的局限性,已无法应对日益高速化、高效化切削的发展趋势。直线电动机式就是在这种趋势的需求下产生的一种高速高效传动方式,特别是机床的高速传动发展跨上一个新台阶。德国作为世界先进机床的先驱,20世纪80年代就开始了高速铣削和车削技术的研发。1993年,德国EXCELLO公司推出了世界上第一个由直线电动机驱动的工作台HSC-240型高速加工中心,机床主轴最高速达到24 000r/min,最大进给速度为60n/min,加速度达到1g。
当进给速度为20m/min时,其轮廓精度可达0.004mm。美国的Ingersoll公司紧接着推出了HVM-800型高速加工中心,最大进给速度达到75.20m/m i n。
1996年开始,日本相继研制成功采用直线电动机的卧式加工中心、高速机床、超高速小型加工中心、超精密镜面加工机床、高速成形机床等。从此以后,直线电动机在高速数控机床的应用如雨后春笋般地迅速发展起来。近十年来,世界上各工业发达国家纷纷投入巨资,大力研究、开发成功不少直线电动机驱动的高速数控机床,并逐渐有抢占传统滚珠丝杠市场的态势。
直线电动机加工中心在国外的宝马、通用等著名汽车公司已经有成熟的应用,在国内上汽通用、东风雪铁龙、昌河铃木、海马汽车等也有整线的应用实例。本文从技术分析和应用实例上进行了直线电动机和滚珠丝杠驱动加工中心的对比。图1为Comau Urane25直线电动机高速加工中心。
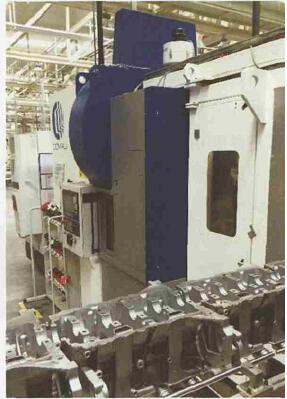
图1
传动原理分析对比滚珠杠副存任的问题如下:
(1)“旋转电动机+滚珠丝杠副”的直线驱动方式存在着多个弹性环节,当整个系统在高速运动时,会出现刚度下降,同时弹性变形使系统的阶次变高,系统的鲁棒性降低,从而使伺服性能下降。弹性变形是数控机床产生机械谐振的根源。
(2)中间传动环节的存在,增加了运动体的惯量,使得位移和速度响应变慢。
(3)间隙死区、摩擦、误差积累等因素,使进给速度和加速度受到限制。
(4)动转平稳性较差,在高速运动下噪声易发热。
(5)精度保持寿命相对短。
而直线电动机以—个运动部件实现直线运动,则具有以下优点:直接驱动中力是无接触传递的,因此无磨损,使用寿命长,维护简单;传动刚性高,推力平稳,直接驱动,弹性环节减少,系统刚性提高,传动效果高;定位精度和重复定位精度高,可达亚微米级,比伺服电动机及滚珠丝杠副传动的加速度和重复定位精度提高7~10 倍。
性能指标对比直线电动机的特点如下:
(1)快速响应性。一般说,机械传动件比电气元件的动态响应时间耍大几个数量级。由于系统中取消和响应时间常数较大的如滚珠丝杠等机械传动件。使整个闭环的控制系统动态响应性能大大提高。
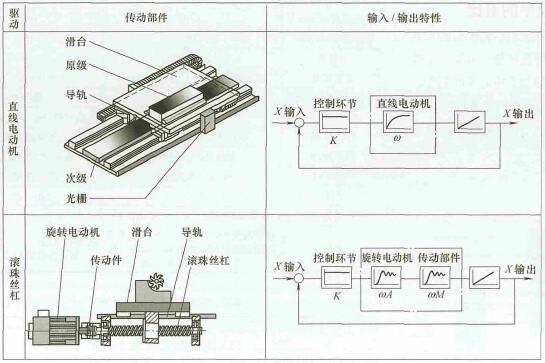
图2 机床驱动轴原理对比
(2)结构简单,以—个运动部件实现直线运动。直接驱动中力是无接触传递的,因此无磨损,使用寿命长,维护简单。
( 3 ) 传 动 刚 性 高 , 推 力 平稳,直接驱动,弹性环节减少,系统刚性提高,传动效果高。
( 4 ) 精 度 和 重 复 定 位 精 度高,可达亚微米级,比伺服电动机及滚珠丝杠副传动的加速度和重复定位精度提高7~10 倍。
(5)速度高,加速度大。最大速度可达90~180m/min,最大加速度可达10g。
(6)行程不受限制。在导轨上通过串联直线电动机的定子可任意延长动子的行程长度,这是滚珠丝杠所望尘莫及的。结构简单、运动平稳、噪声小,运动部件摩擦小、磨损小、使用寿命长、安全可靠。
加工效率的对比现 以 某 发 动 机 气 缸 盖 的 8 个φ11H7 的导管孔精加工为例,分别用滚珠丝杠的加工中心A和直线电动机加工中心B加工,两机床的参数如图3所示,工艺参数及节拍见表2。
表1 两种设备的优缺点对比
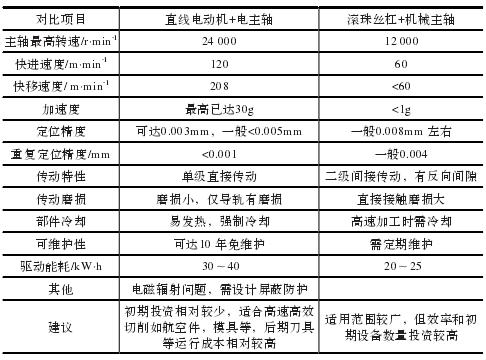
表2 加工参数节拍对比表

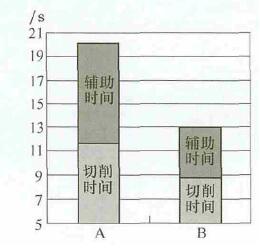
图3 工艺参数及节拍表
数据表明,同样的加工内容和切削参数下,直线电动机的加工中心节拍比滚珠丝杠加工中心降低近40%。直线电动机驱动产生的高速进给,配备高速的电主轴,大大提高了切削效率;同时,直线电动机极高的快移速度也大大降低了空行程时间,这就是直线电动机加工中心生产效率高于滚珠丝杠加工中心的原因。如果生产线编排要求工序集中化、频繁重复多个同样的加工内容、加工时空行程较长、设备安装空间小、生产效率高、人员配备少,这些情况下,建议采用直线电动机加工直线来组成生产线;如果工艺编排分散化、刀具性能不能满足高速加工、需要强力切削、工件装夹转换频繁,则建议采用滚珠丝杠加工中心来组件生产线。加工精度试验对比两种传动方式,从原理上存在根本的精度控制差异,直线电动机的定位精度基本能控制在0.003mm以内,重复精度控制在0.001mm以内,且能保持长期的稳定;
而丝杠传动初期基本在0.005mm,在后期磨损后精度逐步降低到0.01mm左右,精度会越来越差,需频繁的维护和更换。行业内一般用插补加工来对比圆度差异,分别用直线电动机加工中心和滚珠丝杠加工中心插补铣φ 50mm的孔,丝杠传动的设备加工出来,微观上的形状是锯齿状,且圆度较大,而直线电动机驱动加工的孔形状基本保持比较圆滑的过渡。圆度结果分别为:滚珠丝杠加工中心13.4μm(见图4), 直线电动机加工中心3.1μm(见图5)。
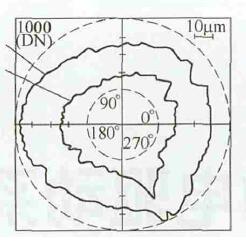
图4
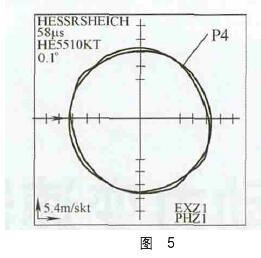
图5
由此可见在进行圆弧插补加工时,直线电动机加工中心加工出来的孔圆度远远优于滚珠丝杠中心,更适合用于加工精度要求较高的曲线、曲面特征,如用于高精度模具的加工。
以上是结合工作原理与试验验证结果,对直线电动机高速加工中心与传统滚柱丝杠传动的机械主轴加工中心的对比,最终应用时需结合自身产品、工艺、技术要求和投资的理念,择期适者而用之。
投稿箱:
如果您有机床行业、企业相关新闻稿件发表,或进行资讯合作,欢迎联系本网编辑部, 邮箱:skjcsc@vip.sina.com
如果您有机床行业、企业相关新闻稿件发表,或进行资讯合作,欢迎联系本网编辑部, 邮箱:skjcsc@vip.sina.com
更多相关信息