数控重型卧式车床主轴锥孔研伤后的修复方法
2019-4-25 来源:中国一重设备能源管控中心设备维修厂 作者:雍强龙
摘 要: 分析归纳粗加工重型数控卧式车床主轴锥孔研伤的原因。以200 t粗加工数控卧式车床为例,介绍了主轴锥孔研伤后的修复方法。为今后粗加工重型卧式车床主轴锥孔研伤后的修复提供了一种既便捷又高效的方法。
关键词: 粗加工;数控卧式车床;锥孔;顶尖;修复
目前,重型卧式车床所使用的顶尖主要分为无法兰式长尾锥和法兰式短尾锥两大类,普通重型卧式车床采用的顶尖为无法兰式长尾锥顶尖,而数控重型卧式车床采用的则是法兰式短尾锥顶尖。由于无法兰式长尾锥顶尖与主轴锥孔的接触长度较长,承载的力大,稳定性好,这就决定了普通重型卧式车床在粗加工活件的过程中很少出现主轴锥孔研伤现象;而法兰式短尾锥顶尖与主轴锥孔的接触长度短,使用此种顶尖的数控重型卧式车床只适用于活件的半精和精加工,为了适应于当前市场和生产等因素,使用法兰式短尾锥的数控重型卧式车床越来越多参与活件的粗加工,当出现主轴锥孔与顶尖尾锥接触率达不到要求时,一旦顶尖法兰上的把合螺栓剪断或者缺失后,在加工活件的过程中操作者不能及时发现,时间一长,就会造成数控重型卧式车床主轴锥孔和顶尖尾锥研伤,在重载下一旦出现研伤,两者的研伤面比较严重,最终造成顶尖报废,主轴锥孔需要修复。
1、机床所用顶尖的分类
1.1 无法兰式长尾锥顶尖
普通重型卧式车床采用的顶尖为无法兰式长尾锥顶尖,如图1所示。此类顶尖尾锥常用的锥度有1∶7、1∶8和1∶10,尾锥长度按照机床吨位不同在200~400 mm不等,尾锥大端直径也随吨位逐渐增大。由于顶尖尾锥比较长,与主轴锥孔接触率大,承载力大,稳定性好,在安装时只要保证尾锥的接触率达到75%以上,大端接触良好即可,无需专项维护保养。在粗加工活件过程中顶尖和主轴锥孔出现研伤的概率极低。
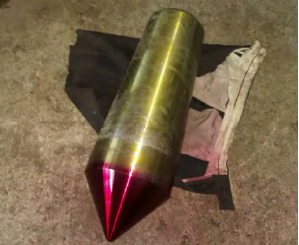
图1 无法兰式长尾椎顶尖
1.2 法兰式短尾锥顶尖
数控重型卧式车床采用的顶尖为法兰式短尾锥顶尖,如图2所示。此类顶尖尾锥的锥度为1∶4,尾锥长度按照机床吨位不同在50~180 mm不等,尾锥大端直径也随吨位逐渐增大。由于顶尖的尾锥比较短,安装过程要求比较严格,必须保证尾锥接触率达到75%以上,大端接触良好;在紧固法兰上螺栓对顶尖产生预紧力后,顶尖法兰端面和主轴端面之间间隙必须消除。如果以上两方面不能同时满足,数控重型卧车在粗加工活件的过程中由于诸多因素就会造成顶尖法兰螺栓被剪断,操作者不能及时发现,在重载下就会造成顶尖尾锥和主轴锥孔大面积研伤。
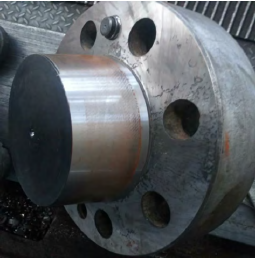
图2 法兰式短尾椎顶尖
2、主轴锥孔研伤原因分析
2.1 顶尖自身结构
数控重型卧式车床采用的顶尖为法兰式短尾锥顶尖,此类顶尖只适应于机床对活件的半精和精加工,不适用于机床对活件的粗加工。
2.2 中心孔同轴度
粗加工活件两端中心孔同轴度相差过大。锻造的活件表面不规矩,划线工划线的辅具、业务水平等诸多因素造成毛坯上加工出来的两端中心孔同轴度相差过大,这样的活件一旦上机床,就会对主轴顶尖产生一个额外的力矩,加之顶尖尾锥接触率较小,时间一长,就会对主轴锥孔产生挤压变形。
2.3 顶尖的维护和保养
机床操作者对顶尖的维护保养不到位。在粗加工活件过程中,顶尖法兰上的把合螺栓易松动,甚至有时丢失,要求机床操作者在上卸活和活件调头时补齐缺失的螺栓,并紧固螺栓。在机床粗加工活件过程中顶尖螺栓缺失和松动时常出现。顶尖法兰上的把合螺栓一旦松动,顶尖和主轴之间的预紧力就会消失,由于顶尖尾锥很短,顶尖与主轴就会发生相对转动,最终造成顶尖尾锥和主轴1∶4锥孔大面积研伤。
2.4 装卡面要求
对于粗加工活件,在上机床粗加工之前,必须铣至少两个合理的装卡面。由于不铣装卡面或者只铣一个装卡面,活件时常与主轴产生相对转动,极易造成顶尖和主轴锥孔出现研伤。
2.5 维修方面的因素
2.5.1 主轴顶尖法兰上把合螺栓全部被剪断后,如果不能从根源上分析问题和解决问题,而是忙于取出断在主轴上的螺栓,螺栓取出后重新换一批新螺栓把合顶尖,让机床重新加工活件,久而久之,造成故障进一步扩大,最终造成顶尖尾锥和主轴锥孔出现研伤。
2.5.2 当机床主轴顶尖前端75°/90°锥面出现严重研伤或者损坏后不能满足机床生产需要时,需要更换新顶尖,在更换新顶尖时如果所换顶尖达不到顶尖所需的检验标准也会造成顶尖尾椎和主轴锥孔出现研伤。
以上五方面因素是造成粗加工数控重型卧车主轴1∶4锥孔出现大面积研伤的主要原因。
3、主轴1∶4锥孔研伤后的修复方法
200 t粗加工数控卧车主轴锥孔大端大面积研伤,如图3所示。主轴顶尖尾椎大端大面积研伤,如图4所示。
粗加工数控重型卧式车床虽然是数控机床,但机床一直承担着大型轴类零件毛坯的粗加工序,由于毛坯表面的不规矩性、加工过程中大走刀量和切削深度,造成机床各部精度严重下降,尤其是刀架各部间隙比较大。一旦主轴锥孔出现严重研伤后,需拆卸主轴上精度比较高的精加工机床车磨主轴1∶4锥孔,拆卸主轴必须先拆掉主轴箱和主轴上的各种附件,拆卸过程既费时又费力,还会对机床主轴造成二次伤害;对于静压结构的主轴,在拆卸和安装过程极易造成静压轴瓦研伤。
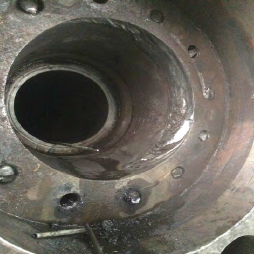
图3 200 t粗加工数控卧车主轴锥孔大端研伤
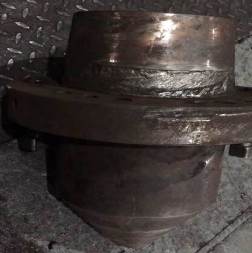
图4 主轴顶尖尾椎大端研伤
为了既省时又省力,避免对机床造成二次伤害和提高维修进度,采用不拆卸主轴,机床利用自身刀架完成对主轴1∶4锥孔的车磨序。由于粗加工机床刀架X、Z轴间隙较大,编程后理论轨迹与实际轨迹相差甚远,这对加工主轴锥孔带来了一定困难。这就要求采用的加工方法在机床运行编程前必须消除X、Z轴的反向间隙,此种加工方法加工出来的实际轨迹才能逼近理论轨迹,降低在磨削过程中的改锥度次数,提高维修进度。
3.1 主轴锥孔检验标准
合格主轴锥孔的检验标准为:
(1) 涂色检查,在圆周和长度上接触率均需达到70%以上,且锥孔大端接触良好。
(2) 顶尖和主轴两端面之间预留0.10~0.15mm间隙,加力后消除。
3.2 研伤后的修复方法及工艺
以200 t粗加工数控卧车为例:
3.2.1 加工前的准备工作
拆卸机床卡盘上四个卡体等附件,使用稀油擦拭干净新顶尖尾锥和端面上的防锈油。
3.2.2 焊序
(1)条件允许的情况下使用氩弧焊或者气保焊补焊研伤的机床主轴锥孔,单边补焊量需大于3 mm。反之,使用J507普通焊条补焊。
(2)使用电焊取出所有断螺栓。
3.2.3 车序
上加长刀杆找正中心高后:
(1) 以最小量平主轴上安装顶尖的端面见平即可。
(2) 按1∶4锥度车补焊后的主轴锥孔,要求锥孔大端尺寸车至254 mm(主轴顶尖尾锥大端尺寸为256 mm,留2 mm磨量)。
3.2.4 攻丝
使用丝锥重新逐个攻主轴上把合顶尖的丝孔。
3.2.5 磨序
车序完成后,上磨头,找正中心高后,按1∶4锥度磨主轴锥孔,采用从锥孔小端到大端编程磨削(即采用倒磨),这种磨削方法在走程序前可以尽量排除刀架X、Z轴反向间隙。当主轴锥孔在整个长度和圆度上粗糙度达到Ra0.8μm后,顶尖尾锥涂色配研主轴锥孔。安装顶尖后,必须对称把合顶尖上12个螺栓,并紧固到位。
3.2.6 检验与判断
螺栓紧固到位后,测量顶尖端面和主轴端面之间的间隙,测完间隙后,拆卸顶尖,检查顶尖尾锥与主轴锥孔的接触率。
(1)当主轴锥孔接触率达到检验标准,且两端面之间间隙在0.10~0.15 mm之间时,即可达到要求,停止磨序。
(2)当主轴锥孔接触率达到检验标准,而两端面之间间隙大于0.15 mm时,即采用原程序(不改变任何数值和锥度值)和原方法重复磨主轴锥孔直至两端之间间隙达到要求停止磨序。在磨削的过程中需要多次上顶尖测量。
(3)当主轴锥孔接触率达不到检验标准时,按照着色情况小值(一般改动0.05~0.10 mm)改动锥度值(即改动程序中的X轴数值,其它数值和磨削方法不变),重复磨主轴锥孔直至接触率达到检验标准,且两端面之间间隙在0.10~0.15 mm之间,停止磨序。改动锥度值之后,当锥孔在整个长度上均磨削到后,需要及时安装顶尖配研主轴锥孔,并测量两端面之间间隙。
3.2.7 顶尖的安装
使用稀油擦拭顶尖和主轴锥孔各部,安装顶尖,对称紧固顶尖上所有把合螺栓,采用外力消除顶尖和主轴两端面之间的间隙,再重新对称紧固所有顶尖把合螺栓,上卡体加工活件。在日常上卸活的空余时间,需要勤检查顶尖把合螺栓,并及时紧固和补齐螺栓。
3.3 修复过程中的数值采集
采用的磨削方法虽然在走程序前排除了X、Z轴反向间隙,但在磨削的过程中刀架各部还是有间隙存在,再加之在磨削过程中砂轮的磨损和磨头自身误差等原因,需要多次改动锥度值重复磨序才能达到要求。
4、结论
经过一周时间,完成了200 t粗加工数控重型卧式车床主轴1∶4锥孔的修复工作,修复后主轴锥孔与顶尖尾锥在长度和圆周方向的接触率均达到了80%以上,且大端接触良好;两端面预留0.15 mm间隙,并在加压的作用下完全消除。为今后重型卧式车床主轴锥孔研伤后的修复提供了一种既便捷又高效的方法,具有很大的推广价值。
投稿箱:
如果您有机床行业、企业相关新闻稿件发表,或进行资讯合作,欢迎联系本网编辑部, 邮箱:skjcsc@vip.sina.com
如果您有机床行业、企业相关新闻稿件发表,或进行资讯合作,欢迎联系本网编辑部, 邮箱:skjcsc@vip.sina.com
更多相关信息