模具型腔零件数控加工工艺的设计
2019-1-18 来源:江苏建筑职业技术学院 徐州市模具新技术 作者:黄继战 康力 范玉 李宪军 陈波涛
摘 要:在模具型腔零件工艺分析的基础上,设计了两种工艺方案,经分析、比较,选择了基于工序集中的工艺方案,详细设计了加工工序及走刀路线。结果表明,该加工工艺正确、合理,可有效缩短零件加工时间,保证加工质量,这对模具型腔类零件的数控铣削加工具有一定的参考价值。
关键词:模具型腔;数控铣削;工艺方案;走刀路线
0 引 言
数控加工技术在机械制造企业应用日益广泛,逐渐成为机械零件加工的主要方法。立式数控铣床是数控机床的一种,加上刀库和换刀装置即可构成加工中心,在实际生产中占有重要的地位,尤其在模具制造企业更为突出。
数控编程是数控机床加工的关键环节,编程质量的优劣直接决定零件的加工精度、加工效率和加工成本,而编程质量的好坏决定于数控加工工艺。因此,文中以模具型腔零件为载体,进行型腔零件的工艺设计、程序编制和切削加工,对型腔类零件的数控铣削工艺设计具有一定的借鉴意义。
1 、模具型腔零件工艺分析
某型腔零件如图1所示,毛坯长×宽×高为100 mm×100 mm×25 mm,生产批量为单件,技术要求如下:1)其余表面粗糙度为Ra3.2 μm;2)未注圆角R3~R5,去毛刺。由图1可知,该零件为型腔类零件,主要由平面、曲线轮廓、凸台及孔结构组成,结构较为复杂,由于为单件生产,故较适合采用立式铣床加工。
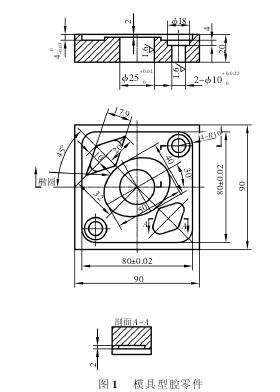
零件工艺分析如下:1)型腔内轮廓尺寸80±0.02,精度要求较高,需要粗加工、精加工。2)椭圆凸台外轮廓是数控铣削加工编程的难点,也需要粗加工和精加工,同时,编程需要采用高级编程手段宏程序或自动编程,椭圆凸台顶面采用粗加工、精加工合二为一,以节省加工时间。3)尺寸25+0.02(次方)的孔加工精度要求高,传统加工采用中心钻钻底孔、钻小孔、粗镗和精镗孔的加工方案,为减少刀具换刀次数,提高加工效率,充分发挥数控机床的优势,确定该孔25+0.02 (次方)精加工可采用以铣代镗的新方法,即确定该高精度孔 25+0.02 (次方)的加工方案为中心钻孔→钻孔→扩孔→精铣该孔。4)2-10+0.022 (次方)通孔的精度要求非常高,需要逐步加工到位,因此确定采用中心钻钻底孔→钻孔→铰孔的加工方案;两角落上的沉孔18先采用中心钻钻底孔,最后采用铣削加工的加工方法完成沉孔的加工。5)型腔内两角落菱形槽由于加工精度要求不高,在满足加工精度要求的前提下,确定采用粗加工→精铣切削的加工方案。6)该零件材料为45钢,为中碳钢,切削加工性能好,适合切削加工。
2 、工艺方案的确定
在上述图样有关分析基础上,即可拟定该型腔零件的工艺方案,主要包括定位基准的选择、粗、精加工阶段的划分、工序的分散与集中等内容。本设计确定以下2种工艺方案。
2.1 加工工艺方案一
1)下料。长宽高尺寸为95 mm×95 mm ×25 mm。2)铣侧边。普通铣床铣削95 mm ×95 mm ×25 mm长方体至长宽高为90 mm ×90 mm ×25 mm,满足对边平行,邻边垂。3)铣顶面、底面。普通铣床铣平顶面,后铣削底面保证高度尺寸为20 mm。4)钻中心孔、钻孔。使用钻床在3个孔位置上钻中心孔、钻9.8孔。5)扩孔25+0.02(次方)。使用钻床扩孔尺寸至20。6)型腔粗加工。采用普通铣床粗加工。7)型腔精加工。用数控铣床精加工方形型腔、椭圆岛屿轮廓及顶面的加工,以及铣孔18。8)铣菱形槽。采用数控铣床铣两菱形槽。9)铣25+0.02(次方)孔。采用铣床精铣25+0.02(次方)孔。10)铰2-10+0.022(次方)孔。手工铰孔。11)去毛刺。12)零件质量检测。
2.2 加工工艺方案二
1)下料。毛坯尺寸为95 mm ×95 mm ×25 mm。2)铣六面。使用立式数控铣床将毛坯尺寸加工至90 mm ×90mm ×20 mm,加工内容包括铣削长方体毛坯4个侧面和上、下底面。3)钻、扩孔。采用立式数控铣床,在型腔零件顶面3个位置上钻中心孔、钻3-9.8孔,并扩25+0.02(次方)孔,将其直径尺寸由9.8扩至20。4)型腔、椭圆凸台和孔加工。
采用立式铣床粗精加工型腔内轮廓、椭圆凸台轮廓,并加工椭圆凸台顶面。以铣代镗采用铣床使用立铣刀精铣25+0.02(次方)孔。5)铰孔。采用立式铣床,使用铰刀铰削2-10+0.022(次方)孔;6)铣沉孔及菱形槽。使用立式铣床铣加工直径尺寸18沉孔和两菱形槽。7)去毛刺、质量检测。
上述工艺方案一工艺路线长,划分工序时采用了工序分散的原则;工艺方案二工艺路线短,采用了工序集中的原则,且基本上以刀具为单位划分工序,以缩短换刀次数。考虑该零件为单件生产,比较适合采用工序集中的原则,同时要减少辅助换刀时间,因此,本设计确定采用工艺方案二。
3 、加工工序的设计
3.1 加工设备选择
根据零件毛坯长宽高尺寸90 mm ×90 mm ×25 mm以及数控车间设备的现状,数控车间立式数控铣床型号为VM600,该零件的尺寸加工范围完全在机床的工作行程范围内,满足要求,确定选择数控车间VM600型号数控铣床。
3.2 夹具选择
夹具分为通用夹具和专用夹具,专用夹具适合大批大量生产,该零件为单件生产,且主体形状为规则的长方体,故选择平口虎钳。
3.3 刀具选择
根据各道工序的加工表面形状、工件材料和机床,刀具材料选高速钢,各工序刀具选择如下:1)铣六面。侧面加工选用直径为16 mm的键槽铣刀,平面加工刀具一般选用端铣刀、立铣刀进行加工,考虑到该工件上、下底面加工面积小和减少换刀次数,也选用直径为16 mm的键槽铣刀。2)钻、扩孔。钻底孔选择直径3mm的中心钻,扩孔选择直径9.8和20直柄钻头。3)铣型腔、椭圆凸台及25+0.02(次方)孔。型腔圆角半径为R10,选择刀具半径值要小于R10,根据刀库现有刀具情况和粗精加工合一,确定选择半R8的两刃键槽铣刀。4)铰孔。选择直径为10 mm铰刀。5)铣沉孔18及菱形槽。选择直径为8 mm的键槽铣刀。
综合上述,共选择6把刀具:中心钻3、9.8和20直柄钻头、16槽刀、8槽刀、10铰刀。
3.4 切削用量的选择
根据切削用量的选择原则,铣刀切削用量选择步骤如下:首先确定切削深度;其次,根据刀具材料和工件材料查手册得切削速度Vc,将Vc代入式(1)即可计算出编程所需的主轴转速。
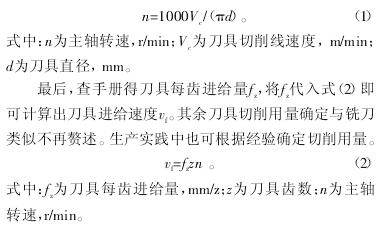
根据以上切削用量的选择步骤或生产经验,确定的各工序切削用量结果如下。1)铣六面。铣削4个侧面切削用量:切削深度约5 mm,主轴转速500 r/min,进给速度70 mm/min;铣削下面切削用量:切削深度约1 mm,主轴转速500 r/min,进给速度60mm/min;铣削顶面切削用量:切削深度约4 mm,主轴转速550 r/min,进给速度50 mm/min,保证工件高度。2)钻、扩孔。钻3-3中心孔,切削深度2 mm,主轴转速1600 r/min,进给速度35 mm/min;钻3-9.8孔,切削深度约4.9 mm,主轴转速750 r/min,进给速度40 mm/min;扩孔20孔,切削深度约5.1 mm,主轴转速500 r/min,进给速度30 mm/min。3)铣型腔、椭圆凸台及25+0.02(次方)孔。型腔、椭圆凸台粗铣切削用量。切削深度约4 mm,主轴转速500 r/min,进给速度60 mm/min;型腔、椭圆凸台精铣切削用量:切削深度约0.5 mm,主轴转速650 r/min,进给速度50 mm/min。25+0.02(次方) 孔精铣切削用量:每次切削深度4 mm,主轴转速650 r/min,进给速度40 mm/min。4)铰孔。铰孔切削用量:切削深度0.1 mm,主轴转速180 r/min,进给速度20 mm/min。5)铣两圆角菱形槽及18沉孔。铣两圆角菱形槽切削用量:切削深度2 mm,主轴转速800 r/min,进给速度40mm/min;铣18沉孔切削用量:切削深度4 mm,主轴转速600 r/min,进给速度40 mm/min。
4、 走刀路线的设计
走刀路线设计是加工工艺的进一步细化,是数控加工工艺的关键工作之一,关系到数控编程质量、机床加工效率和零件的加工质量。这里仅介绍型腔内轮廓、斜椭圆凸台轮廓走刀路线设计,其他工序走刀路线不再赘述。型腔加工分为区域余量加工和内轮廓加工,由于本工件型腔不大,在加工内轮廓和椭圆凸台粗加工时即可把区域加工余量去掉,椭圆凸台顶面采用手动操作加工,所以,区域余量去除和椭圆凸台顶面不再单独编制加工程序。
为了简化程序编制,编制型腔内轮廓和椭圆岛屿外轮廓的粗精加工程序采用刀具半径补偿功能,粗精加工仅需改变刀具补偿值设置即可。轮廓走刀路线的组成为刀具切入切出路径和零件轮廓,重点是切入切出路径的设计,切入切出路径一般有径向切入切出、切向切入切和混合切入切出,考虑零件轮廓加工精度和简化编程,此处设计选择径向切入切出路径。
刀具铣削轮廓侧面切削方式分为顺铣和逆铣,一般粗加工和硬皮材料选择逆铣,精加工选择顺铣切削方式。为粗精加工能使用同一个加工程序,本设计粗、精加工均选择顺铣切削方式,对应的刀具半径补偿指令为G41指令,使用G41指令作刀具半径补偿时,加工型腔内轮廓刀具轨迹为逆时针方向,加工斜椭圆凸台刀具轨迹为顺时针方向。
综上所述,设计的型腔内轮廓、斜椭圆凸台外轮廓走刀路线如图2所示,即方形型腔内轮廓走刀路线为A1→A2→A3→A4→A5→A6→A2→A1,斜椭圆凸台外轮廓走刀路线为E
1→E2→E2→E1。
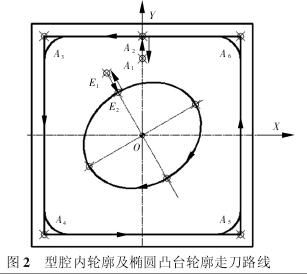
5 、结 语
在模具型腔零件工艺设计的基础上,将编制的加工程序录入数控铣床调试,并进行了试切削。结果表明,该工艺方案正确、合理,可有效缩短零件加工时间,保证加工质量,对模具型腔类零件的数控铣削加工具有一定的借鉴意义。
投稿箱:
如果您有机床行业、企业相关新闻稿件发表,或进行资讯合作,欢迎联系本网编辑部, 邮箱:skjcsc@vip.sina.com
如果您有机床行业、企业相关新闻稿件发表,或进行资讯合作,欢迎联系本网编辑部, 邮箱:skjcsc@vip.sina.com