基于CC—Link总线的FMS物流运输线控制系统设计木
2016-8-17 来源:顺德职业技术学院 广东锻压机床厂有限公 作者:王鸿博 罗勇武 阮卫平 王宝平
摘要:随着工厂自动化水平的提高,柔性FMs生产线在制造类企业中应用越来越广泛,基于各类现场总线技术的工厂网络化和自动化也逐渐普及。介绍广东锻压机床厂有限公司大型FMs柔性生产线的数控化改造及物流系统改造,重点介绍了cc—Link现场总线在FMs中的应用,给出了FMs的具体构成、工艺特点、控制流程及控制特点。改造后的FMs生产线运行效果良好,极大提升了锻压箱体加工效率,提高了产能。减少了劳动强度。
关键词:FMs;cC—Link;制造自动化;制造业信息化;数控化改造
随着制造业信息化管理与制造自动化技术的广泛应用,以多台数控机床组成的柔性自动化生产线(FMS)逐渐在装备制造类行业普及。广东锻压机床厂有限公司引进一条大型柔性FMS加工生产线,并对生产线中的5台数控加工中心进行数控化改造,改造后的数控系统均采用FANUCl8iMB和FANUC0iMC系统。该FMS生产线主要用于大型锻压设备箱体类加工,不同吨位的锻压机床箱体经过焊接成形后,需对箱体表面、导轨面、轴孔、基座平面等进行粗、精加工。传统的加工方法是通过大型吊车对待加工件通过吊装安装至加工工作台上,费时费力,且不同加工工艺需要更换机床时,需要二次吊装定位,造成二次装夹定位精度不准确现象,影响箱体整体加工精度。为此,该公司设计一条柔性物流输送系统,通过物流输送车对被加工箱体进行输送并转运到各加工工位工作台上,整个过程一次装夹定位,有效提升了被加工箱体装夹定位精度、提高了加工效率。
本文针对广锻柔性FMS物流系统的组成及工艺要求,详细介绍了FMS生产线物流系统的控制系统设计,并给出制造信息化管理与产品加工物流系统设备层的信息流关系。
1、FMS物流系统的构成
1.1 FMS物流系统的组成
广锻锻压FMS系统由一条物流输送线和五个数控加工工位组成,系统包含两台物流输送小车、4台大型落地镗铣加工中心及一台三坐标测量机,系统构成如图l所示。该FMS柔性生产线主要用于大型锻压设备箱体加工与测量,由于锻压设备箱体自重一般在10~40t左右,箱体在加工时需要在多台机床上进行加工,箱体在不同机床上装夹定位过去采用吊装方式进行,无论是安全性、定位精度还是装夹效率等方面都比较低下,因此采用FMS物流输送系统,通过在物流小车上一次定位后,由物流小车将定位托盘分别输送到各加工工位。为提高加工效率,各加工工位与物流输送线之间由待交换区和交换工作区两部分构成,如图1所示。
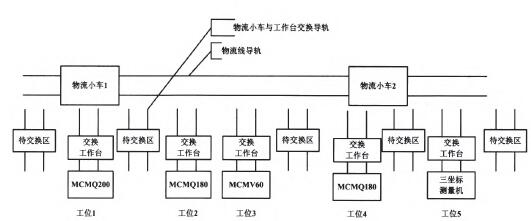
图l 广锻FMs柔性加工生产线系统组成
1.2物流运输小车
整条物流运输线长达120余米(如图2所示),两台物流运输小车运行于各工位之间;物流小车自重达lO t左右,装载的待加工箱体在10~40 t左右,小车由大功率变频器和减速装置驱动运行;小车定位由运输线两侧各设置的红外线测距仪进行准确定位,定位误差±0.5 mm,运行速度为500 mrIl/min。物流小车上有装备有导轨、两个液压缸和四个定位销(液压缸组成),四个定位销用于托盘工作台在小车上的锁紧;两个液压缸用于装载托盘工作台,如图3所示。当物流小车在运输线的装载区域时,由吊车将待加工箱体进行吊装至托盘工作台上,并进行定位锁紧,根据工艺要求,由物流小车输送至指定工位,再由装载液压缸推送托盘工作台至交换区,经交换区转载至机床工作台上。
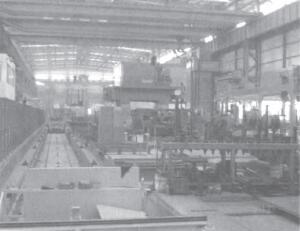
图2 物流小车及输送

图3物流小车结构
1.3物流交换工作台
物流交换工作台的主要作用是连接机床工作台与运输小车的过渡装置,如图4所示。当物流小车装载待加工箱体至指定工位后,由物流小车上装载液压缸推动托盘工作台移动至物流交换工作台区,物流交换工作台上装载液压缸1将托盘工作台移动至待交换区,装载液压缸2推动托盘工作台至机床工作台上;当托盘工作台移至机床工作台后,由机床工作台上四个液压定位销进行定位,并由四个液压锁紧销钉进行锁紧,至此托盘工作台及托盘上箱体固定在机床工作台上。交换后的托盘工作台如图5所示。
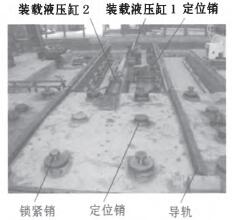
图4 托盘交换装置结构实幽
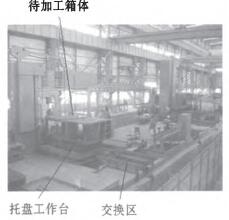
图5 装载箱体父换完成实幽
2、FMS物流控制系统设计
2.1物流系统的控制要求
根据广锻FMS生产线工艺要求,物流管理系统对五个托盘工作站,五台机床和两台物流车进行设备层联网,实现物流车、托盘工作站、加工机床之间的合理配合,完成工件的自动/手动物流。同时设置中控室对物流线状况进行监控和管理。系统的主要控制要求如下:
(1)系统具有下达生产工艺管理文件功能;
(2)系统组成网络化且运输线、各工位数控加工中心之间信息交换准确;
(3)物流输送小车运行高效、定位准确;
(4)物流输送小车与交换工作台、各数控机床工作台之间的上下料交换准确、效率高;
(5)设备层网络控制简单易行,整个运输线的运行可监控;
(6)整个物流系统可进行手动/自动运行控制方式。
2.2系统的硬件设计
2.2.1 CC—Link总线网络组成
系统设备层网络选用三菱Q系列CC—Link总线系统,是日本三菱公司主推的开放型现场总线㈣。cc—Link总线最高通信速度可达10 Mbit/s,该速度可在不影响机器控制速度的同时允许大量的数据进行通信:主站与从站之间的距离最长可达112 km。
系统CC—Link网络由主站(三菱Q系列PLC)和五个托盘从站(远程数字I/O站)组成;主站与从站由主从通信模块完成。由于系统各站点距离较远,主站与从站均连接在一根双绞线上,主站靠地点来辨识从站,每个从站编写不同站号地址,只有主站发送的信息在相同站号下方可接受;CC—Link现场总线有自动更新参数功能,即Q系列PLC内部原件区域的数据会被自动传输到所有远程I/0中,各从站远程I,O的数据也会被收入到指定的Q系列PLC中,从而保证了信息传递的准确性和实时性。系统的CC—Link网络拓扑结构如图6所示。
该FMs物流输送系统以Q系列PLC作为主站,通过CC—Link现场总线与各远程I/O站、运输小车PLC等进行数字通讯,协调控制运输小车至各工位,进行托盘装载和卸载,完成设备层的物流信息交换。
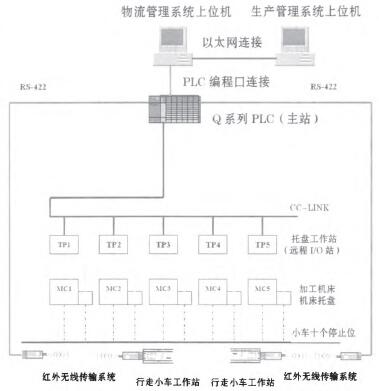
图6 FMS物流输送系统硬件拓扑图
2.2.2物流系统硬件改造方案
FMs柔性生产线的重点在于设备层各设备之间的协调控制与物流的准确定位。物流小车通过输送线将托盘工作区(远程I/O)上载有工件的托盘输送至加工工位,并通过托盘交换区与机床工作台进行交换;由于物流运输小车、待加工工件均属重载,系统要求物流运输小车运行平稳、定位准确。因此物流小车由单独从站PLC进行控制、各托盘工作站由远程I/O协调控制。生产线距离长达120 m,若采用常规方法,需要增大电缆敷设费用,因此采用现场总线方式与从站PLC和远程I/O进行连接,提高了系统的可靠性、减少了连接电缆的数量,同时采用CC—Link网络可方便系统的扩展。
本系统采用三菱Q系列PLC及扩展模块(如表l所示),由三菱Q系列PLC(Q02HCPU)组成主站,通过CC—LINK现场总线模块QJ61BTllN与五个托盘工作站通讯。每个托盘工作站为64点输入64点输出,组成远程I/0站,分别由两个远程I/O输入模块(AJ65sBTBl—32D)和两个远程I/O输出模块(AJ65sBTBl—32T)组成。每个物流车上安装三菱Fx2N一128MT—001 PLC,使用RS232一C通讯接口模块经过红外无线传输设备与主站PLC通讯。红外无线传输设备选用上海倍加福的数据传输光电传感器DAD30一RT/35。采用Rs一232传输方式分别连接主站PLC和小车站PLC,实现主站和小车站之间的通讯。上位机与主站通过编程口进行通讯。上位机选用研华工控机。上位机通过以太网与生产线控制系统上位机通讯,可从生产线控制系统数据库中调出加工流程。上位机编制用户使用界面,实时监控物流线状态(小车运动情况,托盘工作站情况,工件线内传送加工情况)以及生成、下发、保存、调出工件加工流程。
QJ61BTllN模块作为CC—Link主站模块,专用的AJ65SBTBl—32D和AJ65SBTBl—32T作为远程输入与输出模块,物流小车PLc作为从站PLC构成CC—Link网络。三菱Q系列PLC具有上电自动在线和自动屏蔽出错站等功能,能很容易实现总线连接及通信可靠性测试,为系统的设计和调试带来极大方便。
如图6所示,主模块QJ61BTllN负责与现场总线物流小车PLC从站通信,根据工序要求下达物流小车运输运动位置,并发送装载或卸载控制信号;AJ65SBTBl—32D和AJ65SBTBl—32T作为远程输人与输出模块,实现五个托盘工作位、托盘交换工作区、机床工作台装载I/O等各种开关量信号映射到主控PLc的映像寄存器中。
表1 控制系统硬件类型
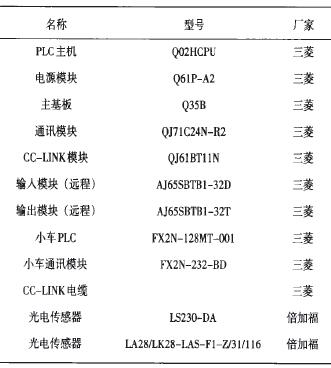
2.3 FMS物流输送控制系统设计
2.3.1 FMS物流系统框架结构
FMs柔性锻压设备生产线系统由加工系统、物流系统、管理系统组成。四台加工中心与一台三坐标测量机组成加工系统;输送线物流小车与托盘工作站组成物流系统;计算机及其上运行的调度管理软件组成管理系统。如图7所示。在FMS系统中,FMS调度管理是最困难的问题之一【3。1,FMS系统的物流调度要求实时性、准确性及高效性,要根据系统不同加工机床的特点、待加工零件的工艺要求、待加工零件的数量等实时合理安排,才能提高FMS调度管理效率。
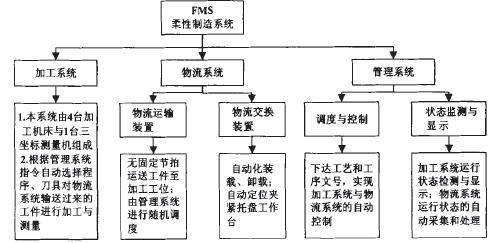
图7 FMS输送线物流调度策略架构
2.3.2 FMs物流输送控制流程设计
(1)物流系统上位机设计
物流系统上位机设置组态画面,动态实时显示物流线的状态。包括物流小车的当前状态,托盘工作站和机床的状态,上下料机构的动作情况,物流线上工件加工的进程和位置以及远程I/O站和小车站的工作状况。组态画面中设置物流线急停软键,物流线启动软键,上位机还应通过组态软件实现和生产管理系统上位机的必要通讯(如从生产管理系统上位机数据库中调取加工程序、加工流程等)。
(2)物流系统控制流程设计
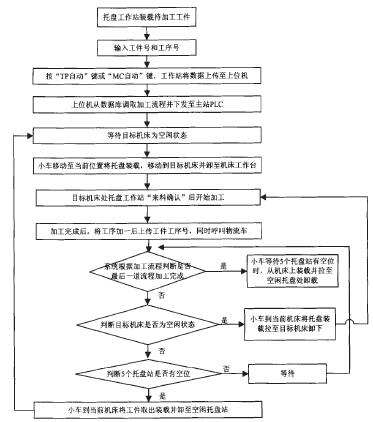
图8 物流系统控制流程
物流系统控制软件流程如图8所示。根据控制要求,系统具备自动和手动控制功能,手动功能用于系统各工位的调整与维护,自动功能用于全线自动运行。
3、结束语
各类现场总线技术逐渐应用到柔性化自动生产当中,提升了工厂自动化生产效率;本文介绍了CC—Link总线在锻压箱体FMS生产线中的实践应用,原有旧的FMS柔性自动线经过数控化改造及物流系统改造后,运行良好,缩短了箱体加工的周期,减轻了原来吊装、定位等作业中工人的劳动强度,提高了生产效率。
参考文献:
[1]林桂娟,宋德朝,陈明,等.基于CC—Link现场总线的远程智能监控系统[J].机床与液压.2010(8):84—87.
[2]王俊明,苏记华,薄昌盛,等.基于PI上和CC—Link总线的工业机器人控制的实现[J].自动化技术应用,2013(7):44—47.
[3]陈浩勋,韩崇昭,邵福庆,等.FMS的实时调度与控制方法研究[J].信息与控制,199l (2): 22—27.
[4]饶运清,李培根.FMS调度与控制的统一建模与集成设计[J].中国机械工程,2012(2):855—860.
[5]李德信,吕延军,贾杰,等.柔性制造系统(FMS)调度中的进化算法研究[J].组合机床与自动化加工技术。2002(8):23—28.
投稿箱:
如果您有机床行业、企业相关新闻稿件发表,或进行资讯合作,欢迎联系本网编辑部, 邮箱:skjcsc@vip.sina.com
如果您有机床行业、企业相关新闻稿件发表,或进行资讯合作,欢迎联系本网编辑部, 邮箱:skjcsc@vip.sina.com
更多相关信息