快速经济的瓦尔特非标刀具,燃气轮机零件加工的首选
2016-6-13 来源:瓦尔特 作者:
在工件上钻反沉孔
快速经济的瓦尔特非标刀具,燃气轮机零件加工的首选
时间就是金钱,事实上并非完全如此。越来越多的公司发现赢得业务的唯一方式是比竞争对手快。因此,他们采用一些非标刀具,加快生产工艺过程。由西门子发电与天然气集团经营、总部位于柏林的燃气轮机厂采用这种方法后,大大缩短了燃气轮机零件的加工时间。这家公司原来钻16个燃气轮机转子轴法兰沉孔需要10小时,而使用全自动Walter MODCO®反转沉孔法后,同样钻16个孔仅需要90分钟。
柏林燃气轮机厂技术团队负责人Markus Zapke说:“我们一直在为加工某些零件的沉孔需要较长时间而苦恼,由于交货时间长,机床利用率高,因此它们对消除加工过程瓶颈越来越关键。”2012年,负责寻找解决方案的员工将与他们合作长达25年之久的合作伙伴换成精密刀具制造商瓦尔特。
大型燃气轮机的大件加工
柏林燃气轮机厂由车间工人用镗床和铣床生产出的轴和外罩有公共汽车那样大。这些零件安装在输出功率高达400 MW的燃气轮机上,然后再销往全世界的发电厂和工业部门。例如CD-1转子轴重量在13吨以上,长度超过3.5米,最宽点直径在1.5米左右。这种中空轴构成世界上最大燃气轮机400 MW SGT5-8000H型燃气轮机压气侧转子的端件。这种零件用法兰安装在与发电机连接的中间轴上,共有16只法兰连接螺栓,法兰开有相应数量的通孔,通孔直径为75毫米,法兰厚度约175毫米。螺栓用螺母紧固,因此必须在钻孔的难以接近的进口加工反向沉孔,以便为它们留出空间。这些反向沉孔深56毫米,直径98毫米。
单项加工任务花费的时间太长
CD1轴在柏林燃气轮机厂加工,分四班运行,采用一台驱动装置输出功率为100千瓦Skoda HCW 3镗铣床或一台驱动装置输出功率为50千瓦的Pama Speedram 3F机床加工。这些稳定的机床全部用于加工大件,切削效率高,精度大。尽管如此,但是加工一个沉孔仍然需要在37分钟以上。轴采用26NiCrMoV14-5材质制作而成。这种低碳低合金钢具有很好的机械特性和热特性,通常用于能源行业及通用机械工程的高应力零件。柏林燃气轮机厂的工艺人员Ralf Hohendorf说:“因为这种材料经过热处理后,含镍量相对较高,特别难加工,更难加工孔和沉孔。”Siemens PG长期使用需要用手安装的双刃高速钢铣刀加工的反沉孔法进行这种工作。这种刀具加工一个沉孔的时间不到16分钟,还包括非生产时间(例如除屑时间),要求的总时间在37分钟以上。按每件工件16个沉孔计算,总加工时间需要整整十小时。
自动化工艺过程
主管人员不愿意接受这种浪费时间的现实。他们咨询了瓦尔特德国(Walter Deutschland)的负责技术支持大客户销售的专家Michael Hartsch和大客户应用工程师Stefan Rißmann。这两名专家对加工非常熟悉,很快就拿出了解决方案:Walter MODCO®的反向沉孔钻采用了可转位刀片。Hartsch说:“在250毫米时,这种全自动非标刀具与以前使用的刀具具有相同的伸出长度,但是与之不同的是,这种刀具采用了内冷方式。”
在这种刀架通过法兰孔后,选择反向沉孔工艺过程便开始。这种工艺过程通过装在刀架前部凹槽位置处的两根臂完成,并自动向外延伸到两侧。这两根臂直接相对定位,并各自装有双刃硬质合金非标刀片。其侧面伸缩由内冷冷却液的压力控制,无需手动干预。Rißmann说:“对于以前的刀具,操作人员必须笨拙地将双刃高速钢铣刀插入刀架内,然后用手固定到位。”
省时省力,非同凡响
瓦尔特刀具最初在铸造外壳上试验,然后在CD-1轴上试验。Zapke说:“2015年底以来,我们的加工工艺过程投放市场,一直受到用户的好评,采用这种工艺工程,可无缝且可靠地加工轴,无需另外人工监督,刀具得到认可,广泛用于生产。”
这种整体硬质合金反向沉孔钻加工一个沉孔的时间为67秒。在考虑非生产性时间后,现在整个工艺过程所花的时间约5.5分钟,只有以前所需时间的15%。Hohendorf说:“我们并不期望仅达到如此的省时水平,由于其较好的性能,使用瓦尔特刀具后,在1.5小时内即可完成单件16个沉孔的加工。按此计算,整个加工时间大大缩短,只有以前加工时间的15%,而且还节省了大量的成本。
需要的切削刀具数量少
柏林燃气轮机厂还特别看重了瓦尔特硬质合金可转位刀片的长寿命。Hohendorf说:“由于瓦尔特的这种非标刀具,我们现在可同时加工两件产品(精准的最小批量大小)。”这与以前反向沉孔钻使用的高速钢铣刀刚好相反,以前的刀具在加工一道沉孔工序后,便已全部磨损而需要换刀。因此,以前在生产16件零件的过程中,共需要重磨256把高速钢刀具,而现在仅需要8张可转位硬质合金刀片。哈奇说:“与高速钢铣刀相比,我们的可转位刀片磨损率很低,投资回报快。”西门子电力和天然气公司还看到了刀具带来的巨大成本节省:每次外部刀具夹装需要约十分钟,新刀具使用八张可转位刀片,需要的总时间仅有80分钟,比以前使用256把高速钢铣刀的刀具所需的时间要短得多。瓦尔特的这种方案的成本相对较低,与以前的刀具需要数千欧元的小时费率相比,现在的小时费率只有50欧元左右。
更加便捷、更加高效
瓦尔特的这种复杂刀架设有全自动化机构,实际成本比以前的手动刀架要高,但是附加成本在不到一年的时间即可收回。Zapke说:“此外,这种刀架还经久耐用,平时只需有更换导衬。”但是,他还说新刀具的夹装、操作和维护需要全面培训,倍加小心。
Zapke视这次转换为重大成功:“全新的自动化系统比以前的解决方案更加易于管理和操作,从而大大缩短了交货期。此外,其表面质量也比以前的刀具要好得多。Zapke补充说,整个项目进展十分顺利,该公司现在正在研究将瓦尔特的此刀具用于其它零件的加工。工程师也说:“我们与瓦尔特专业人员的通力合作正是我们所要的。”
图片1:应用场景
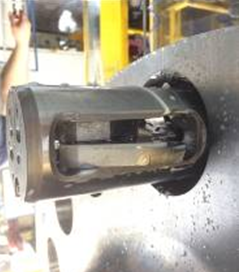
图文说明:正在使用Walter MODCO® 的内冷整体硬质合金反向沉孔钻加工CD-1燃气轮机轴的一个法兰沉孔。图片:西门子
图片2:(同时显示操作人员的)夹装在机床上的工件
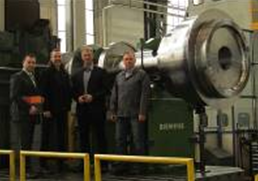
图文说明:站在已安装好的CD-1中空轴正前方的合作伙伴(左前起):瓦尔特的Michael Hartsch、西门子电力和天然气公司的Markus Zapke 和Ralf Hohendorf 以及瓦尔特的Stefan Rißmann
图片:莱辛巴哈
图片3:夹装在机床上的刀具
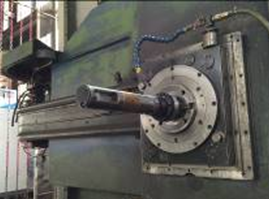
图文说明:夹装在镗铣床上的整体硬质合金反向沉孔钻的伸出长度为250毫米
图片:西门子
图片4:开有法兰孔的零件
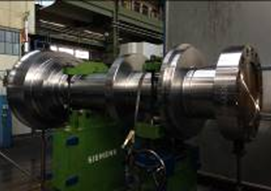
图文说明:CD-1燃气轮机轴的法兰上共钻有16个孔和沉孔。
图片:西门子
图片5:法兰沉孔
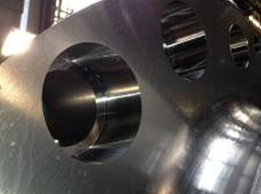
图文说明:CD-1轴法兰后部沉孔深56毫米,直径98毫米。
图片:西门子
图6a和图6b:刀具的3D模型
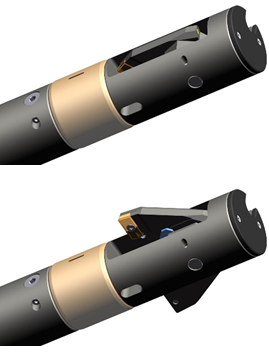
图文说明:采用伸缩铣刀的刀具描述
图片:瓦尔特
投稿箱:
如果您有机床行业、企业相关新闻稿件发表,或进行资讯合作,欢迎联系本网编辑部, 邮箱:skjcsc@vip.sina.com
如果您有机床行业、企业相关新闻稿件发表,或进行资讯合作,欢迎联系本网编辑部, 邮箱:skjcsc@vip.sina.com
更多相关信息