切削参数对金属切削刀具磨损与寿命的影响
2024-7-25 来源: 四川职业技术学院 作者:蒋俊飞
摘要:切削参数是影响切削过程中刀具磨损和寿命的重要因素,对其进行合理调整和优化能够降低刀具磨损和延长刀具寿命,提高加工效率和产品质量。该文对切削参数对金属切削刀具磨损与寿命的影响分析与优化。首先,建立了切削动力学模型,包括切削速度、进给量和切削深度是常用的切削参数。然后,对切削参数进行了影响分析和优化探究,详细阐述了切削参数对刀具磨损和寿命的影响机理,它们的变化会对刀具产生不同程度的磨损。切削速度过高会使刀具表面温度升高,引起刀具磨损加剧;进给量过大则会增加刀具的侧向冲击和摩擦力,导致磨损加剧;切削深度过大会增加刀具受力和磨损面积,进一步加速刀具磨损。通过实验研究和统计分析,得出了不同切削参数下刀具磨损和寿命的关系。基于这些关系,本文提出了一种优化算法,可以帮助工程师选择最佳切削参数组合,以最大程度地延长刀具寿命并降低磨损。在实际应用中,通过合理调整切削参数,可以降低刀具磨损和延长刀具寿命,提高加工效率和产品质量。
关键词:切削参数;金属切削刀具;磨损;寿命;影响分析
0、引言
切削加工是金属加工领域中常用的加工方法,切削刀具的磨损和寿命问题一直是制约切削加工效果和生产效率的重要因素。合理的切削参数选择是降低切削刀具磨损和延长刀具寿命的关键。因此,研究切削参数对刀具磨损与寿命的影响,并通过优化选择最佳切削参数组合,具有重要的理论和实用价值[1]。在切削加工中,切削速度、进给量和切削深度是常用的切削参数。这些切削参数的选择将直接影响切削过程中刀具的磨损程度和寿命。切削速度过高会引起刀具表面温度升高,加速刀具磨损;进给量过大会增加刀具的侧向冲击和摩擦力,导致刀具磨损加剧;切削深度过大会增加刀具受力和磨损面积,进一步加速刀具磨损[2]。因此,通过合理调整切削参数,可以降低刀具磨损和延长刀具寿命。
目前,相关研究已经在切削参数对刀具磨损和寿命的影响方面取得了一定的研究成果。然而,由于切削加工过程的复杂性,刀具磨损和寿命受多种因素共同影响,因此仍存在一些问题有待解决[3]。将通过对切削参数对金属切削刀具磨损与寿命的影响进行深入分析与优化研究,为加工领域提供重要的理论指导和技术支持。通过实验研究和统计分析,本文将量化不同切削参数下刀具磨损和寿命的关系,建立优化算法,以帮助工程师选择最佳切削参数组合,以最大程度地延长刀具寿命并降低磨损。
1、切削动力学模型
在进行切削加工时,刀具的刀刃会同时承受径向和切向切削力,如图 1 所示。传统切削模型认为,切削力主要来自于切削变形以及刀具与工件之间的摩擦[4],其表达式为:
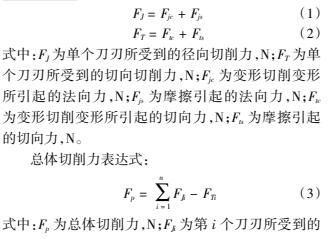

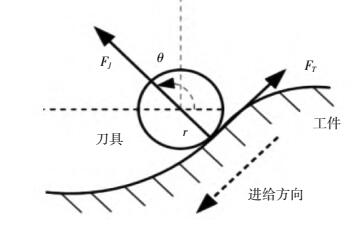
图 1 刀具的受力分析
目前,大多数研究都是通过控制法向切削力来改变切削振动的情况,进而使切削过程变得平稳。但是,在进行切削加工时,切削深度和切削进给速度的改变会导致刀具与工件接触的弧线长度发生变化,从而影响实际参与切削加工的刀刃数量以及切削力的大小。
因此,表达式(3)就不能直接应用于实际加工过程中的切削力分析。切削力会受到多种因素的影响,如切削深度、切削进给速度、刀具转速等,目前常用的求取切削力的经验公式为:

2、切削参数对刀具磨损与寿命的影响机理
切削速度、进给量和切削深度是常用的切削参数,它们的变化会对刀具产生不同程度的磨损。切削速度过高会使刀具表面温度升高,引起刀具磨损加剧;进给量过大则会增加刀具的侧向冲击和摩擦力,导致磨损加剧;切削深度过大会增加刀具受力和磨损面积,进一步加速刀具磨损。因此,合理调整切削参数对刀具磨损和寿命具有重要意义[5]。
切削力是衡量切削加工性的重要指标,对切削加工变形、加工表面质量等均具有不同程度的影响,切削力的研究分析对于良好切削工艺的制定有重要的意义,国内外学者对切削力的研究产生了浓厚兴趣。切削参数及润滑方式均为影响切削力的重要因素。对铝合金进行了干切削加工,经方差分析可知,切削参数对切削力的影响主次顺序为:进给量>切削深度>切削速度,并且建立了切削力线性回归模型,取得较好的预测效果。张平等人探究了极端环境下切削参数对铝合金切削力的影响,并且建立了三向切削力预测模型,切削参数对切削力的影响。仲为武探究了润滑方式对铝合金铣削力的影响,通过单因素实验方案对干切削、湿式切削和空气喷射辅助微量润滑切削所产生的切削力进行对比,发现切削力大小顺序依次为:干切削>湿式润滑,并且金属切削条件下的切削液用量仅为湿式润滑条件下的 3%。一些专家学者利用不同的方法来模拟与预测铝合金加工过程产生的切削力。Mali 通过 Deform 软件模拟了铝合金的切削力,对比实验切削力发现,主切削力和进给力的相对误差分别为 16.40%和 13.79%,模拟效果较好。
3、面向金属刀具磨损与寿命的切削参数优化算法
3.1 PID 切削力控制器的设计
PID 控制是一种将比例环节(P)、积分环节(I)与微分环节(D)结合为一体的自动控制算法,原理简单、易于实现、适用面广、调整方便,故得到广泛应用,其工作原理是根据输入的误差值,依照比例项、积分项和微分项来进行运算,然后利用运算结果来控制输出,广泛应用于工业自动化、机器人控制、汽车控制、飞行器控制等领域[6]。
如果目标切削深度、有效切削面积与刀具转速保持不变,切削加工精度的主要影响因素是切削力以及切削进给速度。为了方便后续研究,将机器人切削到目标深度时所需切削力设为 F(d ti),力传感器所测的
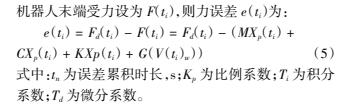
3.2 基于 PID 的切削参数优化算法
因为常规的 PID 控制系数 Kp,Ti,Td 为恒定的,不会根据切削系统状态的改变来进行实时调整,一旦机器人的切削加工状态发生了改变,常规的 PID 控制模型则无法快速适应这种变化,从而导致切削力出现波动,影响椎板切削加工质量。为了解决这一问题,以PID 控制模型为基础,加入模糊规则来对切削加工状态进行推理与判别,该方法可以根据实际的切削加工状态来调节 PID 控制模型中的参数,从而使实际的控制模型可以适应切削加工状态的改变。
切削加工系统为非线性、时变的系统,其实际加工情况会随着切削参数的变化而发生改变,因此一般的 PID 控制器很难达到切削加工过程中力控制的要求。此处采用模糊自适应 PID 控制策略来控制的切削力,这种策略的优点是控制器能够根据机器人切削状态的变化来实时调节 PID 控制参数 Kp、Ti、Td,从而对切削力进行分段控制,其控制结构见图 2。
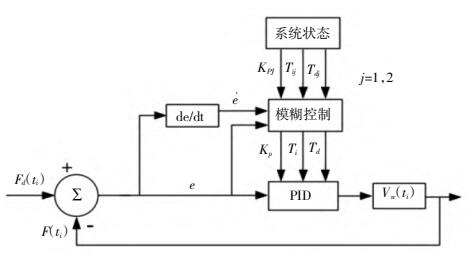
图 2 模 PID 控制系统
4、实验结果与分析
仿真的目的是观察模糊 PID 策略对切削力的控制效果。首先要根据切削动力学公式 MATLAB 软件中建立仿真模型,然后进行 PID 控制仿真,最后将三种控制方法仿真结果进行对比。仿真参数中的切削深度设置为 1 mm,起始进给速度设置为 2 mm/s,根据前期切削实验测得的切削力结果,将目标切削力设为5.6 N,刀具转速设置为 5000 r/min。
由于 PID 的各控制参数的变化会对控制系统产生巨大影响,所以在仿真前需要对 PID 控制器的各控制参数进行整定,确定最佳参数,本文用的参数整定方法为临界比例度法。首先在闭环的控制系统中,将控制器置于纯比例作用下,然后在控制系统中施加一个干扰,从小到大逐渐改变比例系数直至出现等幅振荡,如图 3 所示,此时 Ku = 3,Tu = 13.86。
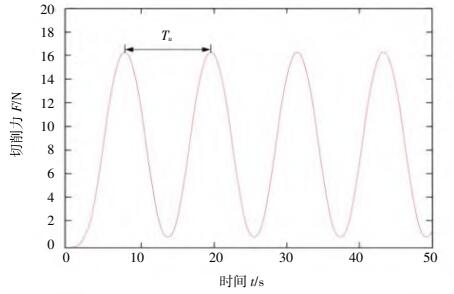
图 3 等幅振荡
各控制方式的仿真结果如图 4 所示,观察可知,模糊 PID 控制策略和 PID 控制策略在切削力峰值的控制方面表现相似,都低于开环控制时的切削力峰值。切削力从峰值回落后要经过振荡过程,在模糊ID 控制时切削力振幅在 1.9 N 左右,比在 PID 控制时减小了 1 N,比在开环控制时减小了 4 N。此外,切削力的振荡周期也得到大幅缩短,实现了切削冲击振荡的快速收敛。
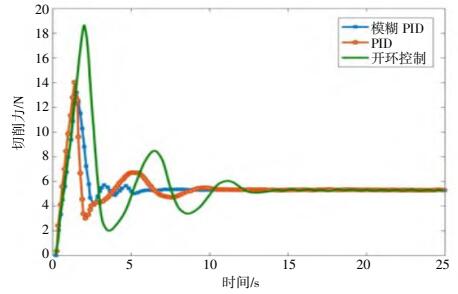
图 4 切削力控制仿真
5、结果应用
切削动力学参数在机器人建模方面应用,从人机生物系统融合的角度去研究机器人系统的建模、分析和优化考虑得不够深入,尤其在机器人切削加工的轨迹精度和动态稳定性方面存在不足,这必然导致机器人与各种领域结合得不够紧密,提升机器人的控制精度和稳定性尤为必要。研究大多侧重于如何进行机器人加工轨迹的规划并取得了较多的成果,但对机器人加工过程中切削变形与振动对切削轨迹精度带来的影响缺少深入研究,造成机器人切削轨迹精度和稳定性较差,无法充分发挥出机器人操作平稳、加工精度高的优点,因此研究切削动力学参数对金属切削刀具磨损与寿命非常重要。
投稿箱:
如果您有机床行业、企业相关新闻稿件发表,或进行资讯合作,欢迎联系本网编辑部, 邮箱:skjcsc@vip.sina.com
如果您有机床行业、企业相关新闻稿件发表,或进行资讯合作,欢迎联系本网编辑部, 邮箱:skjcsc@vip.sina.com