汽车零部件加工中刀具的运用实践研究
2021-7-23 来源:安徽省小小科技股份有限公司 作者:程春利 江子杰
摘要:当前,汽车零部件加工标准显著提升,其精密制造不仅要保证加工质量,还要减小体积。汽车零部件加工技术含量高、工艺复杂,为了达到整车轻量化发展的需求,人们需要提高刀具的加工速度、精度与效率。本文简要分析了汽车零部件加工中数控刀具和特制刀具的选择及运用方式,以期为汽车零部件加工提供思路。
关键词:汽车零部件;加工;刀具;运用实践
汽车零部件加工属于精密制造技术,工艺流程比较复杂,零部件加工质量和体积要求较高。当前,人们要提高刀具加工速度、精度与效率,满足整车轻量化发展的需求。因此,本文重点研究了汽车零部件加工中刀具的运用实践。
1、汽车零部件加工中数控刀具的运用实践
数控刀具种类繁多,不同汽车零部件加工对于数控刀具有不同的需求,因此在选择数控刀具时,一方面要保证其符合实际加工情况,另一方面要注重数控刀具运用的经济性。在汽车零部件机械化加工过程中,要合理确定切削参数,以提高零部件加工的质量与效率。随着CAD/CAM技术的发展,可以将CAD设计数据直接用于数控加工中。值得一提的是,DNC微型计算机和数控机床之间的连接使整个设计、过程计划和编程过程都在计算机上完成,并且通常不需要输出特殊的过程文档。数控刀具实物图如图1所示。
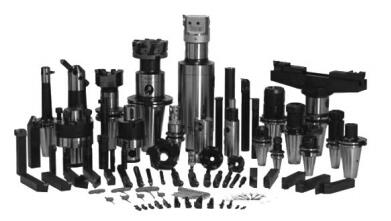
图1 数控刀具
部分汽车零部件外部结构较为复杂,工作面较多且呈现出不同的角度,因此要根据零部件表面的尺寸、外部轮廓、凹凸程度等选择最合适的加工刀具。比如,立铣刀通常用于加工平面零件的外围轮廓;球头铣刀、环形铣刀、圆锥铣刀和盘式铣刀通常用于加工某些实体轮廓和可变斜角轮廓。切割线间距一般采用顶部闭合距离,因此球头经常用于表面处理。通常情况下,平断面铣刀具有加工效率高、质量佳的优势,因此如果没有切割等特殊性的加工需求,一般选择平断面铣刀进行汽车零部件的粗加工。在选择数控刀具时,要严格考察刀具生产厂家的资质,主要包括产品合格率、售出产品的退货率、刀具加工精度等,虽然性能较好且使用寿命长的数控刀具价格较高,但它能够显著提高零部件加工质量及效率,从长期发展角度来看,长期所获收益远大于短期的数控刀具购进成本,因此要根据实际情况,尽量选择商誉度高、价格适中的刀具生产厂家。
在汽车零部件机械化生产中,刀库具有自动化、智能化的特点,能够根据工序自动更换刀具,检查刀具性能是否完好等。因此,编程人员需要深入了解实际加工工作,掌握每条生产线所生产零部件的特点,确定刀具参数,并根据生产线中不同的工序,确定刀具的功能,继而选择相应的刀具。当前,我国汽车零部件加工机床道具系统较为庞杂,每种刀具用途不同,编程人员还需要掌握刀具相关知识,以满足实际加工需求。
部分汽车零部件加工企业机械化程度不足,虽然引进了数控机床,但还没有实现智能化加工,当切换生产线或更换工序时,其需要人工进行换刀、调试等操作,不仅浪费时间,还会增加人力成本。对于此类加工方式,要合理布置切削刀具的顺序。首先,要尽量减少刀具使用数量,降低更换次数;其次,夹紧工具后,应完成所有可以执行的加工步骤,尽量提高刀具的利用率;再次,即使是相同尺寸和规格的工具,也应分别使用粗加工和精加工工具;最后,当前汽车零部件讲求“以车代磨”,即省略粗加工环节,直接使用车床上的刀具对零部件进行精加工或半精加工,降低生产成本。为此,应在保证加工质量的基础上对比粗加工、半精加工、精加工的成本,继而选择合适的加工模式。
刀具使用后,要将其合理保存在刀库中,如果刀库安装智能检测等装置,则只需要检查装置上显示的代码,以确定刀具数量及质量。如果刀库以人工管理为主。管理人员需要详细检查刀具是否有损坏、刀具性能是否完好等,当刀具不合格时,要及时更换,避免加工中刀具断裂而影响加工进度。
2、汽车零部件加工中特制道具的运用实践
在整车行业低迷的背景下,汽车零部件行业的发展面临着诸多困境。首先,国家加大对汽车零部件生产环保、安全的管控,因此加工企业需要更新加工技术与设备,经营成本增加。其次,汽车零部件加工行业竞争激烈,产品同质化问题严重,要想获得竞争力,汽车零部件加工企业需要不断创新生产技术,切实提高产量、生产效率及产品质量。基于此,汽车零部件加工企业要采取有效的生产成本控制策略。支承轴承是一种重要的汽车零部件,支承轴承孔的加工精度影响零部件的使用寿命,加工中所使用的刀具属于特制刀具。下面分析支承轴承孔加工刀具的应用。
2.1 机床中的特定应用
支承轴承孔加工包括粗加工及精加工两道工序。在粗加工工序中,要使用硬度大、使用寿命长的刀具,以适应快速粗加工速度和大量切削刀具的要求。精密加工应选择精度更高、强度高的刀具,以提高加工精度。在加工支承轴承孔时,要根据加工面的特点确定刀具参数,以免刀背与工件之间产生相互干扰。具体工具参数如表1所示。
表1 刀具参数
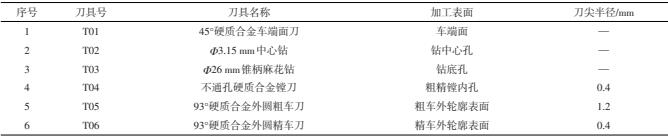
在进行特定处理之前,应先设置工具。设置刀具时,要进行定位操作,保证支承轴承孔加工位置的准确性。在设定换刀点时,有必要结合实际的加工需求,以避免换刀点位置过远或过近,影响加工效率及质量。
2.2 优化用于加工支承轴承孔的刀具
在传统的支承轴承孔机械加工方式中,将粗加工与精加工分为两道工序,分别选择加工刀具。一方面,此种方式需要使用数量较多的刀具,会提高生产成本;另一方面,两道工序需要更替,需要进行换刀,会延长加工时间。因此,要优化用于加工支承轴承孔的刀具,当前有两种优化方案。一是优化刀具的相关参数,如刀具的规格、刀具强度、刀具韧性等,以增强刀具的耐用性,继而满足不同工序的加工需求。二是使用组合刀具,即将粗加工与精加工两道工序合并,选择既能够满足粗加工需求,又能提高加工精度的组合刀具。例如,可以组合使用粗加工工具和铣削端面工具(见图 2),以确保刀片的稳定放置;精加工工具可以与下角刀组合使用,该工具由数个单头镗刀组成,如图3所示。
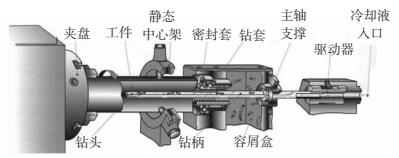
图2 粗加工刀具与铣端面刀具的合并
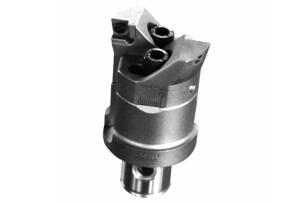
图3 精加工刀具与下角刀合并
2.3 使用新的支承轴承孔加工刀具
陶瓷刀具是一种耐磨性好、硬度高的新型刀具,可以加工不同的汽车零部件。根据试验数据,陶瓷刀具切削速度、耐用性等性能远高于普通的金属刀具,并能够解决普通刀具加工中消耗大、效率低等问题,在汽车零部件加工中具有广泛的应用前景,并且能够显著提高汽车零部件加工的效率与质量。支承轴承孔加工刀具如图4所示。
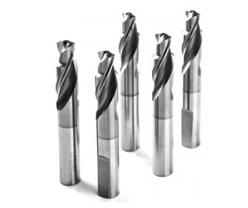
图4 支承轴承孔加工刀具
部分支承轴承直径较大,使用的材料硬度较高,普通加工刀具难以实现高精度、高质量加工。因此,要选择陶瓷刀具。同时,选择的陶瓷工具应具有较高的耐磨性、较高的硬度和良好的弯曲性能。然而,普通陶瓷工具的脆性较大,因此加工过程中的抗切割性较大。为了提高切削工具的强度,应选择负前角工具。确定切削刀具后,有必要选择科学合理的切削参数,以确保加工效果。要选择较大的切削深度,以减少加工时间并提高加工效率。
确定进给速度时,应综合分析加工表面的粗糙度、零件的刚度和刀片的强度。如果零件刚度和机床功率允许,则可以选择更高的速度。经过切削试验后,对零件的余量进行比较和分析。结果发现,该余量减少了0.5~3.5 mm,基本上达到了粗磨余量要求。
3、 结语
当前,机械加工已经成为汽车零部件的重要发展趋势,因此要注重数控刀具的选择及参数的确定。同时,要不断优化刀具的使用方案,比如,采用组合道具或优化刀具结构,以减少刀具使用数量,增加刀具的耐用性。此外,要加大对数控刀具的研发力度,运用新型加工刀具,比如,防震S-可换头SMSR刀具有不同的规格,锁紧部采用M螺纹形状,能够与硬质合金杆配套使用,采用正前角切削刃形状的42°~45°强螺旋角、不等分割及不等排屑槽设计。另外,人们要选择抗氧化性、抗热性高的材料,每个切削刃口需要设有内冷孔,给切削刃口提供充分的切削液,改善粘刀问题并一致加工振动,该方法可广泛应用于与钛合金、耐热合金等有关的汽车零件加工。
投稿箱:
如果您有机床行业、企业相关新闻稿件发表,或进行资讯合作,欢迎联系本网编辑部, 邮箱:skjcsc@vip.sina.com
如果您有机床行业、企业相关新闻稿件发表,或进行资讯合作,欢迎联系本网编辑部, 邮箱:skjcsc@vip.sina.com
更多相关信息