刀具表面织构对刀-屑界面摩擦学特性的影响
2020-2-27 来源:河南科技学院 机电学院 作者:逄明华,聂永芳,申福猴,马利杰
摘要:刀具快速磨损限制了金属切削的进一步发展,表面织构技术的提出为改善刀-屑界面摩擦提供了新思路,也是目前降低刀具表面磨损的有效方法之一。从刀-屑界面切削液存储与润滑、微/纳织构、织构方向、织构类型及形状、织构位置等五个方面,概述了现有刀具表面织构对刀-屑界面摩擦学特性的影响,总结了刀具表面织构的共性作用机理,并进行了分类归纳。相应分析结果表明,刀具表面织构改变了刀-屑界面内空体集团的数量及微通道分布,增加了界面内切削液的渗入存储,同时捕捉存储了界面内的磨屑颗粒,改善了刀-屑界面润滑摩擦;且在此过程中,润湿性因素对界面内切削液的渗入、存储及润滑油膜的形成等均存在影响。最后对刀具表面织构技术的发展进行了总结与展望,为刀具表面磨损的调控提供了参考。
关键词:刀具;表面织构;刀-屑界面;摩擦学特性;润湿性
金属切削过程中,刀具与工件之间的恶劣摩擦以及切削热的协同作用会引发刀具的快速磨损,尤其在高速切削难加工材料时,切削环境更为恶劣,刀具耐用度更低。此外,刀-屑界面摩擦也是刀具切削能量损耗的主要因素之一,因此,减小刀-屑界面摩擦是实现高效、绿色切削的关键。切削液的使用改善了刀-屑界面摩擦,降低了刀具的切削温度及能耗,究其原因为切削液渗入刀-屑界面,带走了大量的切削热,同时又改善了界面润滑。
目前常用的切削液供给方式为浇注式,尽管该方式的切削液用量很大(10~20 L/min),然而切削液仅能冷却润滑刀-屑界面滑移区,在高速切削难加工材料时,切削液对刀-屑界面的冷却润滑基本不存在。为此,增加刀-屑界面切削液的渗入,改善界面冷却及润滑,降低刀具磨损,对于提高刀具寿命和降低切削能耗均具有重要的意义。
表面及界面直接影响机械设备的能量交换、运动和信号传递,早在 1942 年 SCHLESINGER 就指出“表面的质量对于其正确的功能极其重要”[18-19]。这表明设计者们已意识到表面形态的重要性,并试图通过改变表面的纹理或织构来改善表面机械、物理及化学性能。为此,表面织构技术被提出并应用于工程表面。表面织构是指利用电沉积、电火花、激光及光刻等加工方法在平整材料表面加工出具有一定排列规律和形状参数的微细结构,从而得到具有某种特定性能的非光滑表面[18]。现有研究表明表面织构能够存储润滑 液及容纳磨屑,从而改善界面润滑、摩擦,提高其承载能力],已逐渐成为国内外学者研究的热点。近年来表面织构被应用于刀具表面,以此改善刀-屑界面的润滑及摩擦,减缓刀具磨损。目前学者们采用激光等加工方法在刀具表面制备了微/纳米级织构,研究了织构类型、形状及参数等对刀-屑界面润滑摩擦、刀具切削力及工件表面加工质量等的影响。
结果表明,刀具表面织构能够改变刀-屑界面切削液的渗入及存储,改善界面润滑及摩擦,降低刀具的切削力,提高工件表面加工质量。 尽管刀具表面织构的相关机理研究已取得较大进展,然而刀-屑界面作用剧烈,织构效果无法直接观察及测量,致使其内部机理还未完全清晰。鉴于国内刀具表面织构的作用机理综述较少,为此,本文从表面织构对刀-屑界面润滑摩擦的影响出发,综述了现有的研究成果,提取了刀具表面织构的内部共性机理,同时对刀具表面织构技术的发展进行了总结与展望,为改善刀具的切削性能,降低切削能耗奠定理论基础。
1、表面织构常用加工方法
表面织构是指借助于加工设备和技术手段,在固体表面生成具有相应规律和尺寸的微小结构(如图 1所示),以此提高表面或界面性能。随着表面织构技术的不断发展及应用领域的推广,加工方法逐渐丰富,常用加工方法如表 1 所示。

图 1 固体表面织构形貌
表 1 表面织构常用加工方法
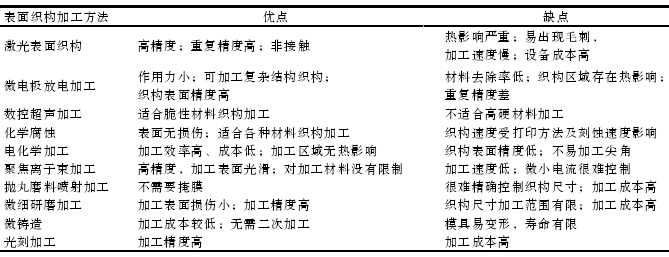
2、表面织构对刀-屑界面摩擦学特性影响
表面织构能够改善刀具的切削性能,澄清表面织构的作用机理是设计织构刀具的前提,综述现有的研究成果是系统化机理的基础。目前机械表面织构的四大机理已基本得到归纳、总结和验证,而刀具表面织构技术出现时间较晚、研究不多,从刀-屑界面切削液渗入及润滑摩擦影响方面进行机理综述目前鲜有报道。为此,本文从刀-屑界面切削液存储与润滑、微/纳织构、织构方向、织构类型及形状、织构位置等五个方面,综述了现有刀具表面织构对刀-屑界面摩擦学特性影响的研究结果,并以此为基础归纳、提取刀具表面织构的共性作用机理。
2.1 刀-屑界面切削液存储与润滑
表面织构引入刀具表面,改变了刀-屑界面的接触特性,影响了切削液在界面内的渗入,从而改善了刀-屑界面润滑及摩擦。KAWASEGI 等利用飞秒激光技术在 WC/Co 硬质合金刀具表面加工了微米(深1.3 μm、宽 2.2 μm)和纳米(深 150 nm、宽 800 nm) 沟槽(见图 2),并进行了铝合金(A5052)车削实验。结果表明,微量切削液润滑条件下,刀具表面织构增加了刀-屑界面内切削液的渗入及存储,减小了刀-屑界面摩擦与粘结,进而降低了刀具的切削力。ENOMOTO 等利用钛宝石飞秒激光加工技术在硬质合金(K10)刀具表面加工了微/纳米沟槽阵列织构(深度 100~150 nm、间隔 700 nm),端面铣削铝合金实验表明,湿切削条件下,微/纳沟槽织构刀具的抗粘附特性得到明显改善,其原因为刀具表面织构的“储油”特性。
随后,ENOMOTO 等[37-42]又进行了微/纳米织构刀具切削碳素钢实验,结果发现纳米级织构刀具的减磨效果不如微米级织构刀具。其原因为,当织构刀具切削软金属时,微米级织构尺寸较大,切屑很容易陷入刀具表面,因此刀-屑界面抗粘结特性改善较小;而纳米级织构尺寸较小,切屑很难陷入刀具表面,因此刀具抗粘结特性提高明显。当织构刀具切削硬金属材料时,刀具切削力较大,而刀-屑界面粘结较轻,故润滑对金属切削过程的影响更明显。纳米级织构尺寸较小,切削液的渗入及存储能力较差,故润滑能力有限;而微米级织构尺寸较大,切削液的渗入及存储能力较强,因此,微米织构的减磨效
果优于纳米织构。
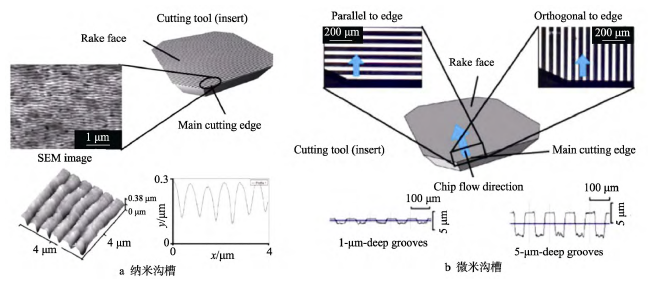
图 2 刀具表面微/纳沟槽织构
LEI 等在钛合金刀具(WC)前刀面加工了锥形凹坑织构(见图 3),45#钢切削实验表明,湿切削条件下,刀具表面锥形凹坑织构降低了刀具的切削力及刀-屑界面接触长度,同时也改变了切屑的形态。其原因为刀具表面织构增加了刀-屑界面切削液的渗入存储,改善了界面润滑摩擦,从而降低了刀-屑接触长度及刀具切削力。
ZHANG 等 对不同润滑状态下刀具表面织构的效果进行了对比研究。结果表明,在润滑油充足的情况下织构的减磨效果最好,在乏油润滑状态下织构的减磨效果变差。主要原因为润滑液充足时,刀具表面织构能够存储更多的切削液,进而更好地冷却润滑刀-屑界面,降低刀具的切削力。国内的戚宝运等利用激光打标机在钨钴类硬质合金刀具(YG8)表面加工了凹槽织构(宽 27 μm、深 12 μm、间距 100 μm),钛合金切削实验表明,湿切削条件下,刀具表面织构改善了刀-屑界面摩擦及粘结,降低了刀具的切削力及温度。
其原因为表面织构增加了切削液的渗入,改善了界面润滑与摩擦。杨超等 在硬质合金刀具(WC/Co)表面加工了圆形离散凹坑织构(直径 80~ 200 μm、深 7 μm、织构面积比10%~30%),并进行了 45#钢切削实验。分析发现,刀具表面织构增强了切削液的铺展及存储,改善了刀-屑界面润滑及摩擦,进而降低了刀具的切削力。由上述研究结果可得刀具表面织构有两个作用:首先,刀具表面形貌是刀-屑界面微通道的来源,而刀具表面织构的存在影响了界面内微通道的存在、分布及几何尺寸等,改变了界面内切削液的渗入;再者,切屑沿刀具前刀面快速滑移,带走了界面内已渗入的切削液,而刀具表面微凹坑单元能存储切削液,并提供二次润滑。
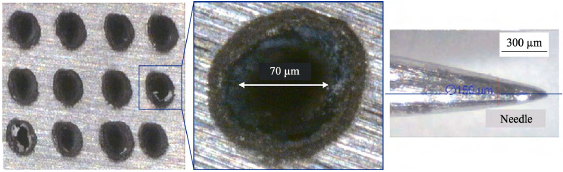
图 3 刀具表面锥形凹坑织构
2.2 微/纳米尺度织构
织构尺寸对表面织构的效果有显著影响,合理调控 织构的尺度能明显提高刀具的切削性能。KAWASEGI等对微米/纳米级织构硬质合金刀具的抗粘结特性进行了对比研究,铝合金(A5052)切削实验结果表明,微米级织构刀具的抗粘结特性较差,而纳米级织构刀具的抗粘结特性较好。究其原因为,微米级织构的尺寸较大,铝合金切屑硬度较小,切削过程中切屑很容易陷入到织构内部,致使刀具表面织构快速被掩埋,刀具切削效果迅速变差。而纳米级织构尺寸较小,切屑不容易陷入到织构内部,刀具表面织构不易被掩埋,刀具切削效果较好,其切削后的形貌如图 4 所示。 在此基础上,ENOMOTO 等[23,37-42]利用微米/纳米级织构硬质合金刀具分别切削了铝合金(A5052)及碳钢。结果表明,切削铝合金时纳米级织构刀具的效果较好,而切削碳钢时微米级织构刀具的效果较好。究其原因为,切削铝合金(A5052)时,切屑是否陷入刀具表面是影响刀具效果的主要因素;而切削碳钢时,刀具表面切削液的存储能力至关重要。这表明刀具表面织构尺寸对刀具切削效果影响明显,当切削硬度较高的金属材料时,刀具表面织构的尺度不易太小;而切削软金属时,刀具表面织构的尺度不易太大。
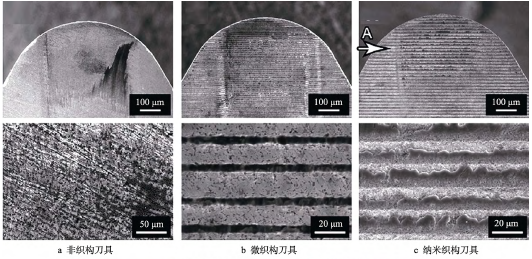
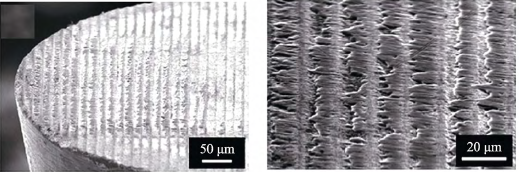
图 4 金属切削后刀具表面 SEM 形貌
2.3 刀具表面织构方向
表面织构能够增加切削液在界面内的渗入存储,那么沟槽织构的方向就不能忽略。沟槽织构的方向不仅决定界面内切削液的渗入情况,也决定切屑与界面内切削液之间的相互作用。KAWASEGI 等 的研究结果表明,沟槽织构方向对刀具的切削性能有着重要的影响。其中,垂直切屑流出方向的沟槽织构刀具效果最佳,其原因为该方向的沟槽能有效保持渗入的切削液,并形成良好的润滑(见图 5 所示)。ENOMOTO等[23,40]的研究结果表明,平行主切削刃方向的微/纳米沟槽织构刀具的抗粘结性能最好。OBIKAWA 等利用光刻方法在硬质合金刀具(K10)表面制备了垂直/平行凹槽阵列、方凸/凹阵列,并涂覆了 DLC 涂层。干/湿状态下的铝合金(A5052)切削实验表明,刀具表面平行切削刃方向的沟槽织构润滑减磨效果最优。由此表明刀具表面沟槽织构方向对刀具的切削效果影响明显,其中平行切削刃方向的织构刀具效果最佳。
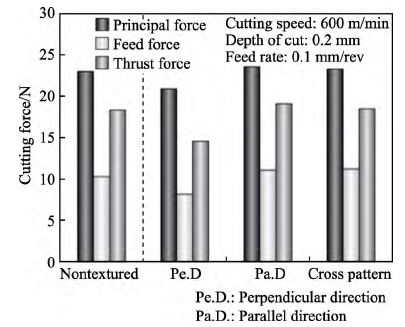
图 5 刀具表面沟槽织构方向与切削力关系
2.4 刀具表面织构类型及形状
织构类型及形状是表面织构的一个常用表征参数,目前刀具表面织构类型及形状的研究较少,仅限于沟槽、离散凹坑等织构类型。KOSHY 等利用电火花加工技术在刀具的前刀面加工了离散和连续两种织构类型(见图 6 所示),并对其效果进行了研究。结果分析发现,两种类型织构均促进了切削液在刀-屑界面内的渗入,改善了刀-屑界面摩擦,降低了刀具的切削力,但其作用效果存在差异,面织构的效果优于离散织构。而 OBIKAWA 等[48]的研究结果表明,平行切削刃方向的沟槽织构及正方形凸织构的润滑减磨效果最优。从上述结果可以看出,织构形状确实对刀具表面织构的效果存在影响。根据 KOSHY 的研究结果可判定,面织构的效果好于离散织构,而离散织构中沟槽与方/圆阵列织构的效果各有其特点。沟槽织构在其切削液供给方面更具有优势,而离散方/圆阵列织构在界面流体动压承载方面更具优势]。
这表明研究刀具表面织构的作用机理时,织构形状因素应该给予考虑,合理选择织构类型及形状能更好地发挥刀具表面织构的效果。
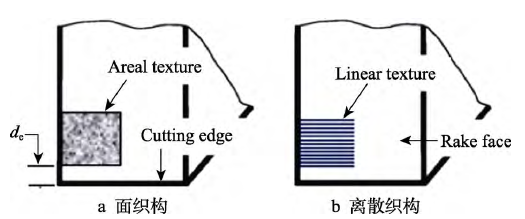
图 6 刀具表面织构
2.5 刀具表面织构位置
织构加工在刀具表面上时,织构在刀具表面的位置就成为织构加工中必不可少的一个参数,其中织构区域相对刀具主切削刃的距离是最重要的参数之一,直接影响织构刀具的效果(甚至使刀具表面织构呈现反效果 。刀具切削过程中,刀-屑界面接触长度一般很小(约 1 mm 左右,具体与工件材料、切削参数 等因素相关 ) , 且又分为两 区—粘结区(1/2~2/3)与滑移区(1/3~1/2)。在粘结区内,刀-屑界面具有较高的应力(1 GPa)、温度(700~1200 ℃)及化学活性,且界面材料相互粘结。在滑移区内,刀-屑界面应力、温度及化学活性大大降低,界面材料相对滑动,仅在峰点接触处才存在粘结现象[4-5]。刀-屑界面粘结区内切削液不能进入 ,刀具表面织构也不能改变该区切削液的渗入,相反还容易造成刀具表面织构的切屑嵌入,增大了界面的相互作用(见图 7)。

图 7 刀-屑界面接触特性及织构区域位置
为此,KOSHY 等研究了织构的位置对刀具切削效果的影响,研究发现当织构位置距离刀具切削刃 2~3倍进给量时,刀具表面织构的效果最优。究其原因为织构的位置直接影响刀-屑界面内切削液的渗入及润滑油膜的形成,织构区域距离刀具的主切削刃太近,这不但不能形成润滑油膜,反而增加了界面粘结。OBIKAWA 等[48]的研究结果表明,刀具表面织构位置对织构效果有明显的影响,当织构区域距刀具主切削刃 100 μm 时,织构刀具的切削效果最好。目前关于刀具表面织构位置的研究结论见表 2
表 2 刀具表面织构区域相对主切削刃的最优位置

3 、刀具表面织构共性作用机理
刀具切削过程是一个多因素耦合的复杂系统,在此系统中,刀具表面形貌与刀-屑界面切削液的渗入、润滑效应、界面接触力学行为及刀-屑界面摩擦相互关联。切削液的渗入途径为界面微通道,而微通道的来源为刀具表面形貌的刮擦和犁耕作用。织构改变了刀具表面的形貌,影响了刀-屑界面切削液的渗入存储、润滑效应,进而影响刀-屑界面摩擦。
3.1 刀-屑界面切削液渗入存储
刀具切削过程中,冷却润滑对刀具切削力及刀具表面磨损具有重要的影响,尤其在高速切削难加工材料时,润滑比冷却更为重要[9,10,32]。刀具表面织构能影响刀-屑界面切削液的渗入存储,改善界面润滑及 摩擦。由图 8 可以看出,刀具表面织构影响了刀-屑界面内空体集团的数量及分布,更多的切削液能进入界面内,从而改善了界面润滑及摩擦。而刀具表面织构的形状及参数又与刀-屑界面内空体集团的数量及分布改变程度相关,所以合理设计刀具表面织构的形状及参数能提高刀具的切削性能。再者,由刀-屑界面原位观测得出,切削液不能进入界面粘结区[53-54],此区域内的织构虽然改变了刀具表面的拓扑结构,但不能增加切削液的渗入,并且还加重界面粘结,增加了刀具的切削力及刀-屑界面摩擦。对于刀具表面沟槽织构,该织构类型为切削液渗入提供了微通道途径,也增加了界面内切削液的存储。而切屑与刀具前刀面存在相对运动,垂直切屑流出方向的沟槽织构其内部的切削液能形成流体动压效果,改善界面内的润滑[23,36,40]。为此,与切屑流出方向垂直的刀具表面沟 槽织构效果最好,而与切屑流出方向平行的刀具表面沟槽织构效果较差。综上分析,在刀-屑界面滑移区合理设计织构类型、参数及位置,能有效增加界面内切削液的渗入及存储,进而在切屑滑移时形成流体动压,改善刀具的切削性能。
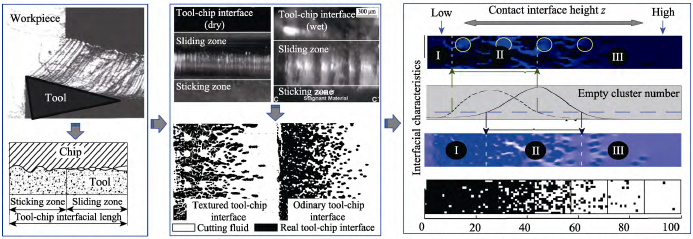
图 8 刀-屑界面切削液渗入机理及与空体集团数量的关联
3.2 刀-屑界面织构磨屑存储
切屑沿刀具前刀面滑移时,刀具表面微结构对切屑有划擦和犁耕作用,此时界面内必然产生大量的磨屑,致使界面润滑及摩擦恶化 。刀具表面织构能够储存和容纳磨屑[22-23],减少了界面内磨屑的数量;此外,表面织构还能够减少摩擦副间的实际接触面积,降低界面间的粘着摩擦、磨损,如图 9 所示。
3.3 织构表面润湿性对刀-屑界面润滑的 影响
切削液与刀-屑界面的物理/化学吸附是界面润滑、减磨的基础,润湿性直接影响微通道内切削液的 渗入、存储及界面油膜的形成。杨超等[34]的研究结果表明,刀具表面织构能够影响切削液的铺展,织构表面切削液的铺展速度越快,刀-屑界面的润滑效果越好,刀具切削力越低,表明织构刀具表面的润湿性与刀具切削性能存在关联。宋晓路等[55-56]的研究结果表明织构刀具表面的润湿性对刀具切削性能存在影响,微量切削液润滑条件下,无织构刀具的表面磨损严重,并出现了冷焊现象。亲油微/纳织构表面的引入减缓了刀具表面磨损,而疏油微/纳织构表面的引入则进一步降低了刀具表面磨损。究其原因为亲油微/纳织构能增加刀-屑界面内切削液的渗入及存储,改善界面润滑及摩擦;而疏油微/纳织构能进一步加快切削液在刀-屑界面内的聚集速度,使刀-屑界面的润滑状态由边界润滑转化为流体润滑,如图 10。由此可知,表面形貌、润湿性、界面微通道及切削液铺展等因素相互耦合并存于刀-屑界面,为此,澄清刀具表面织构的作用机理必须从宏观系统的角度来澄清它们之间的耦合作用。
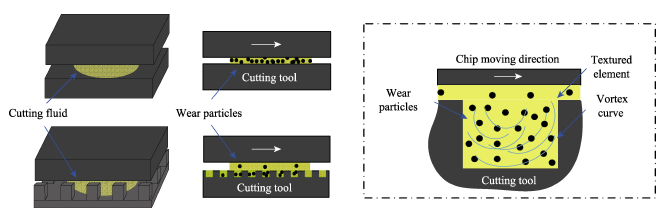
图 9 刀-屑界面织构磨屑存储机理
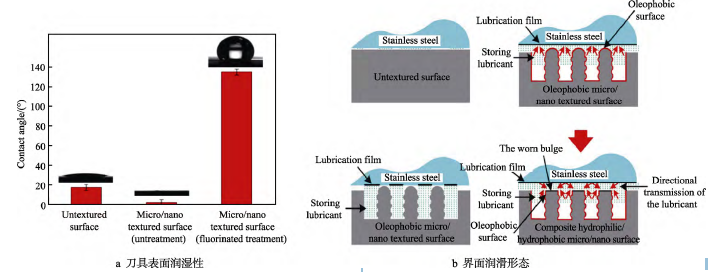
图 10 刀具表面织构润湿性与界面润滑形态关联机理
4 、结论与展望
表面织构技术的提出为改善刀-屑界面摩擦提供了新思路,成为目前降低刀具磨损的有效方法之一。实际刀-屑界面不能直接观察及测量,致使刀具表面织构的具体作用机理不够清晰,这限制了该技术的发展。基于刀-屑界面润滑摩擦的表面织构影响研究结果及共性机理分析,在此指出刀具表面织构技术的未来发展方向,为刀具表面织构技术的发展提供参考。
1)润湿性直接影响界面内流体的渗入、润滑及界面摩擦学特性,而在目前摩擦学的研究中往往忽略了该因素的影响。将润湿性与刀具表面形貌、界面内液体渗入及润滑摩擦相结合去阐明表面织构的作用机理更具有实际意义。
2)刀具切削过程是一个多因素耦合的复杂系统,刀具表面形貌影响刀-屑界面切削液的渗入、润滑效应及界面接触力学行为,进而影响刀-屑界面摩擦。为此,刀具表面织构的研究必须放入到刀具切削系统中,建立数学及计算机动态模拟模型,从系统的角度去分析刀具表面织构的机理,优化表面织构参数。
3)应采用定量探索与定性分析相结合的方法去研究典型耐磨表面织构的耐磨机制及影响规律,建立刀具表面织构的仿生评价依据和量化计算模型,从而定量评价刀具表面织构的效果。
投稿箱:
如果您有机床行业、企业相关新闻稿件发表,或进行资讯合作,欢迎联系本网编辑部, 邮箱:skjcsc@vip.sina.com
如果您有机床行业、企业相关新闻稿件发表,或进行资讯合作,欢迎联系本网编辑部, 邮箱:skjcsc@vip.sina.com