直角铣头在五轴加工中的刀尖点补偿技术
2015-8-14 来源:数控机床市场网 作者:北京卫星制造厂高立国 蒋疆 张佳朋
摘要:针对直角铣头在五轴数控加工中刀尖点位置线性补偿的技术难题,通过对直角铣头的安装方式及刀尖点补偿算法等研究,采用了刀具参考点偏置补偿法、控制器双向刀长补偿法,解决了直角铣头在不同机床结构、不同数控系统的加工中心上,对内部空间狭小的复杂结构进行加工时易出现主轴干涉和运动轴超程的共性瓶颈问题,大幅度提升了加工中心的加工范围与适应性。目前,直角铣头已在多个航天器型号的复杂结构研制中得到成功应用。
关键词:直角铣头;五轴加工;刀尖点补偿;刀轴方向
1 引言
直角铣头是一种重要的机床主轴附件,因其能够使刀具轴线与主轴轴线成 90°直角结构,所以通过与多轴加工中心的配合能够增加机床的加工范围。由于直角铣头的刀具轴线与主轴轴线位于不同方位,传统五轴数控加工中的刀尖点补偿方式已不再适用于直角铣头,因此需探索新的途径来实现直角铣头的五轴加工。直角铣头应用于五轴加工时,存在控制器参数设置复杂,数控编程难度大,加工过程操作繁琐等问题,严重影响了直角铣头的利用率和加工效率,并且存在新技术风险分析不到位,造成质量问题的隐患。
2 直角铣头的刀尖点线性坐标补偿
数控程序的主体部分是由机床刀尖点相对于工件的坐标点群构成的。在五轴加工中,刀尖点位置会随着机床旋转轴的旋转而发生变化,因此必须将刀具参考点通过线性偏置补偿到刀尖点处,实现刀尖点的实时跟随。图 1 是关闭和开启刀尖点补偿功能时的五轴转换效果图。在初始状态下,刀具参考点位于机床的主轴端面中心点处,因此刀尖点线性坐标补偿的本质是计算并补偿机床旋转后主轴端面中心点相对于刀尖点的线性偏置值。从图 1 可以看出,当关闭刀尖点线性坐标补偿功能时,机床将无法运动到正确的加工位置。
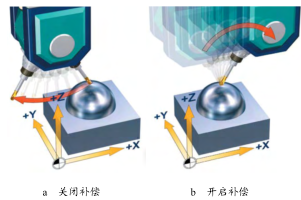
图 1 刀尖点线性坐标补偿的五轴转换[1]
由于直角铣头是由两段直角边构成,目前使用的常规刀具刀尖点线性坐标补偿功能并不适用。直角铣头的刀尖点线性坐标补偿算法主要有两种实现方式:
a. 对于没有开放五轴联动功能的加工中心, 可通过编制刀具参考点偏置补偿算法的子程序实现补偿;
b. 对于能够完成五轴联动的加工中心可通过控制器双向刀长补偿法完成补偿。
下面具体阐述刀具参考点偏置补偿法和控制器双向刀长补偿法这两种直角铣头的刀尖点线性坐标补偿方法。
2.1 刀具参考点偏置补偿法
刀具参考点偏置补偿法是通过在 NC 代码中调用外部子程序,实现对不同机床旋转角度下直角铣头刀尖点的线性轴补偿。其原理是将机床的旋转角度作为实参传递给子程序,在子程序中计算机床在不同旋转角度下主轴端面相对于刀尖点的线性轴位置偏置,并将该偏置值写入控制器的刀具参数表中,当主程序调用该子程序时,刀具参考点将自动补偿到刀尖点处。以五轴卧式加工中心为例,刀具参考点偏置补偿法根据刀轴的指向可分为四种初始安装方位(面向机床方向观察) :刀轴指向 12 点方向(垂直向上) 、3 点方向(水平向右) 、6 点方向(垂直向下) 、9 点方向(水平向左) ,如图 2 所示。若在五轴立式机床上,则应从机床俯视图角度进行观察。
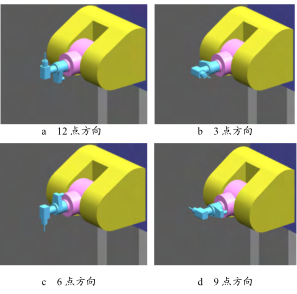
图 2 直角铣头四种初始安装方位
2.1.1 刀轴初始方向指向 12 点位置

图3 直角铣头刀轴初始方向指向12点位置 (右视图)
如图 3 所示,当直角铣头刀轴初始方向指向 12点位置时,以机床水平旋转轴中心 A 为参考原点,则初始刀具参考点 B 的坐标为[0 0 -La]T,初始刀尖点 C 的坐标为[0 Lc -La-Lb]T。当直角铣头绕 Xm轴旋转 °后,刀尖点 D 的坐标[Xd Yd Zd]T可由式(1)求得:
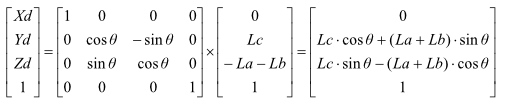
因此, 初始刀具参考点 B 相对于刀尖点 D 的线性偏差值为:
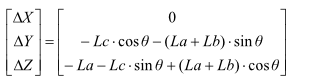
2.1.2 刀轴初始方向指向 3 点位置
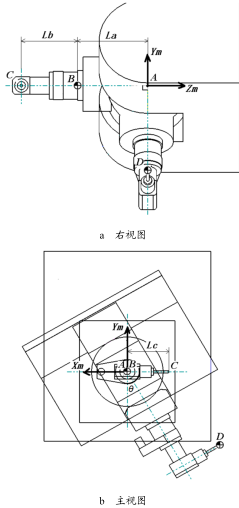
图 4 直角铣头刀轴初始方向指向 3 点位置
如图 4 所示,当直角铣头刀轴初始方向指向 3 点位置时,设机床水平旋转轴中心 A 为参考原点,则初始刀具参考点 B 的坐标为[0 0 -La]T,初始刀尖点C 的坐标为[-Lc 0 -La-Lb]T。此时机床先绕 Xm 轴旋转-90°, 再绕 Zm 轴旋转 °后, 刀尖点 D 的坐标[Xd Yd Zd]T可由式(3)求得:

因此, 初始刀具参考点 B 相对于刀尖点 D 的线性偏差值为:
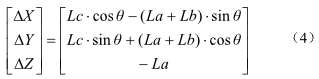
2.1.3 刀轴初始方向指向 6 点位置
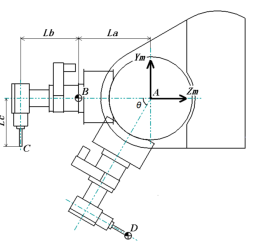
图 5 直角铣头刀轴初始方向指向 6 点位置 (右视图)
如图 5 所示,当直角铣头刀轴初始方向指向 6 点位置时,设机床水平旋转轴中心 A 为参考原点,此时铣头轴线平面位于机床的 YmZm 平面内,则初始刀具参考点 B 的坐标为[0 0 -La]T,初始刀尖点 C 的坐标为[0 -Lc -La-Lb]T。当直角铣头绕-Xm 轴旋转 °后,刀尖点 D 的坐标[Xd Yd Zd]T可由式(5)求得:

因此, 初始刀具参考点 B 相对于刀尖点 D 的线性偏差值为:
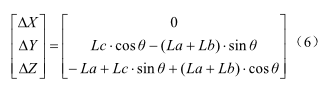
2.1.3 刀轴初始方向指向 9 点位置

图 6 直角铣头刀轴初始方向指向 9 点位置
如图 6 所示,当直角铣头刀轴初始方向指向 9 点位置时,设机床水平旋转轴中心 A 为参考原点,则初始刀具参考点 B 的坐标为[0 0 -La]T,初始刀尖点C 的坐标为[Lc 0 -La-Lb]T。此时机床先绕 Xm 轴旋转-90°, 再绕 Zm 轴旋转 °后, 刀尖点 D 的坐标[Xd Yd Zd]T可由式(7)求得:

因此, 初始刀具参考点 B 相对于刀尖点 D 的线性偏差值为:
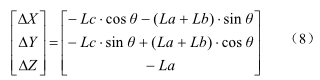
根据上文所述的四种刀轴初始安装方向,将其刀尖点的位置补偿算法封装在数控系统的用户子程序中,并将计算结果通过该程序直接写入到刀具参考点的基础偏置参数中。在应用直角铣头进行五轴加工时,将机床转动角度 作为实参传递给该用户子程序便可实现直角铣头刀尖点的实时跟随。
2.2 控制器双向刀长补偿法
普通铣头的刀具长度仅沿机床主轴方向,在进行刀具长度补偿时仅需补偿刀具的 Z 向长度值。而直角铣头包含主轴轴线和刀具轴线两个刀长方向,因此必须在机床控制器刀具表中设置双向刀长才能实现机床刀具参考点的偏置补偿。以五轴卧式加工中心为例, 按照图2所述直角铣头初始安装位置的四种方向,双向刀长数值的设置分成以下四组,每组两个刀长值,如图 7 所示。 以图 3 中所示的 12 点方向为例, 直角铣头中第 1段与刀柄同轴的直角边沿 Zm 轴正向,第 2 段与刀具同轴的直角边沿 Ym 轴负向, 因此需将刀长 Lb 值输入刀具表的 Length 1 中,将-Lc 值输入 Length 2 中,如图 7a所示。根据刀具表中设置的双向刀长补偿值,启动五轴联动模式,控制器将自动补偿由于旋转轴运动产生的线性偏差,实现机床刀尖点的实时跟随,该方法适合于具备五轴联动的五轴加工中心。
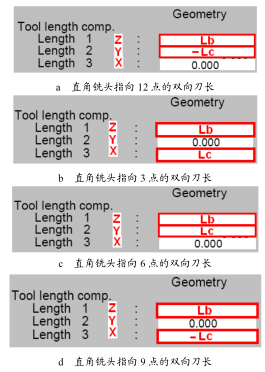
图 7 双向刀长数值的设置
3 直角铣头在五轴加工中心上的几何参数获取
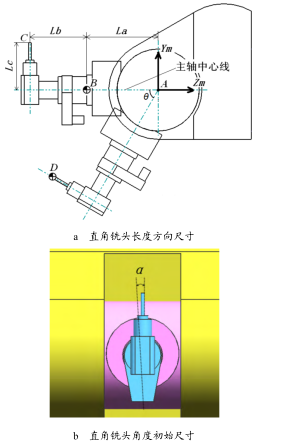
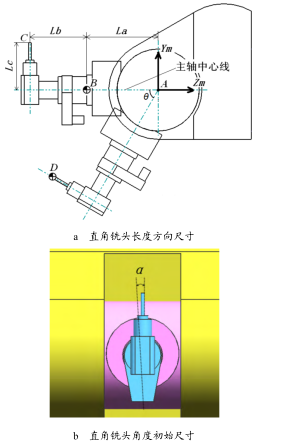
图 8 直角铣头几何参数示意图
直角铣头在五轴加工中心上的实际应用过程中,由于要参与五轴旋转和补偿,所以直角铣头的长度尺寸和角度尺寸的准确获取是保证刀尖点正确补偿的前提条件。以五轴卧式加工中心为例,如图 8 所示,对于长度方向尺寸需要获得 Lb 和 Lc 的准确数值;对于角度尺寸需要确保角度 α 等于零。 Lb 是直角铣头的固有参数, 可以通过配件参数表直接获得。
Lc 根据安装刀具长度的不同会实时变化, 需要通过测刀仪获取准确数值。由于主轴中心线无法获取,所以 Lc 数值无法直接测量,具体测量方法如下:切削刀具在直角铣头上安装完成后,将直角铣头放置于测刀仪工作台,使直角铣头绕主轴中心线进行回转,在测刀仪屏幕上找到刀尖位置,并测量最大回转半径,通过图 8 可知绕主轴中心线的最大回转半径即为Lc 值。
角度α是直角铣头的实际安装位置和理论安装位置之间的偏差,为了确保五轴旋转和补偿正确,需要确保 α 等于零。角度 α 的具体调零方法为:将百分表的触头与刀具外表面接触,采用机床手动模式沿竖直方向上下移动机床主轴,观察百分表的跳动值,根据跳动值调整直角铣头与机床主轴上的紧固螺钉,当跳动值为零时角度 α 等于零。
4 结束语
所采用的刀具参考点偏置补偿法、控制器双向刀长补偿法,很好地解决了直角铣头在五轴加工中的刀尖点补偿难题,进一步提升了五轴数控加工中心的加工范围与适应性。目前,直角铣头已在多个航天器型号的复杂结构研制中得到成功应用。
投稿箱:
如果您有机床行业、企业相关新闻稿件发表,或进行资讯合作,欢迎联系本网编辑部, 邮箱:skjcsc@vip.sina.com
如果您有机床行业、企业相关新闻稿件发表,或进行资讯合作,欢迎联系本网编辑部, 邮箱:skjcsc@vip.sina.com
更多相关信息