轴齿轮高效复合柔性加工机床研究
2021-2-2 来源:陕西秦川精密数控机床工程研究有限公司 作者:李瑞亮,刘 耀,车亚肖
摘 要:随着轿车和新能源汽车变速箱需求增加,对轴齿轮的加工提出了更高要求。研究了轴齿轮高效复合加工机床,组合了传统的轴齿轮热前加工工艺,将轴齿轮加工的全部工艺集成在一台机床内,对工件进行一次装夹,完成所有工艺加工过程。采用了床身立柱一体化设计理念,通过应用高速干切技术和柔性配置功能,大大提高了机床的加工能力和生产效率,实现了轴齿轮高效、高精度、绿色环保的加工需求。
关键词:轴齿轮;高效加工;复合机床
0、引 言
随着汽车工业的快速发展,传统轿车和新能源汽车变速箱对轴齿轮的需求大大增加。轴齿轮热前加工工艺形式复杂,工序繁琐。目前多数用户仍在采用工序较长的传统加工方法,即车削→滚齿→去毛刺→倒棱→铣键槽 (钻孔),加工的全过程时间较长,而且很多用户面临招工难、人力成本上升等难题,导致对于轴齿轮这种长工序加工忧心忡忡。本文针对这些问题设计了一种全新的轴齿轮高效复合柔性加工机床。
1、机床性能及布局
机床左边采用传统的七轴滚齿机床布局,为了合理利用空间尺寸,与传统滚齿机相比,进给轴 X 轴采用了倾斜设计,使Y轴与Z轴存在夹角。右边采用柔性设计单元,根据客户零件加工工艺柔性配置,下面以其中一种配置为例讲述复合机床的功能,具体结构如图1所示。在右边柔性单元里面配置了动力刀塔,通过刀塔的旋转可实现不同工序的加工,集成了轴齿轮车削、滚齿、倒棱、去毛刺、铣键槽 (钻孔)、自动上下料等柔性单元。
该复合机床共有11个数控轴:X轴、Y轴、Z轴、A轴、B轴、C轴、Z2轴、X3轴、Y3轴、Z3轴及C3轴。各轴在机床中的运动关系和作用如下:X轴是滚齿机滚刀的径向进给轴,X轴运动保证轴齿轮的齿深尺寸;Y 轴是滚齿机滚刀的切向进给轴,随着加工过程中 Y 轴的移动,可以改变刀具与工件的接触点位置,有利于刀具寿命的提高;Z轴是滚齿机滚刀的轴向移动轴,Z轴的移动保证轴齿轮的齿宽尺寸;A轴是滚齿机滚刀架角度旋转轴,根据工件的螺旋角和滚刀的螺旋升角确定A轴的角度;B轴是滚齿机主轴;C轴是工作台旋转运动,B轴和 C 轴保持一定的速比关系,两轴联动加工出轴齿轮,并保证轴齿轮的精度;同时 C 轴也是车削加工时的工件旋转主轴;Z2轴是尾座顶尖上下移动轴,实现对工件的自动顶持;X3轴是刀塔径向移动轴,用于车刀的径向进给;Y3轴是刀塔的对中运动轴,用于刀塔与工作台的中心重合;Z3轴是刀塔轴向移动轴,用于车刀的轴向进给,与 X3轴配合使用可加工出轴的圆柱面;C3轴的刀塔旋转轴,用于选择不同的刀位进行不同工序的加工;其中滚齿加工过程中 X 轴、Z 轴、B 轴、C轴四轴联动。
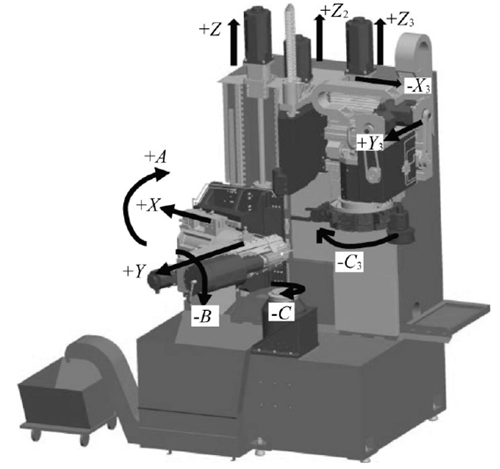
图1:轴齿轮复合加工机床结构图
机床设计将轴齿轮加工的全部工艺集成在一台机床内,对工件进行一次装夹,利用工作台的旋转,通过不同加工刀具的切换,以及对应刀具的轴向和径向进给来实现对不同规格的轴齿轮进行车削、滚齿、倒棱、去毛刺、铣键槽 (钻孔) 的热前加工。这种布局方式节省了工件上下料时间,确保了加工基准的统一,提高了加工效率和加工精度。机床是11 轴四联动高效复合机床,整机还采用高速干切技术,实现轴齿轮高效高精度、节能环保加工,而且自动化和柔性程度高。同时机床具有很好的扩展性,为齿轮生产线配置预留了接口空间及控制反馈接口,便于后期车间自动化产线的实现。
2、床身立柱一体化设计
此复合机床将床身和立柱进行了一体化设计,这样既保证了机床整体的刚性,又有利于机床装配质量的提高。对床身立柱整体进行了有限元受力分 析 。 床身立柱材料为HT300,使用通用结构分析软件 ANSYS Workbench Environ⁃ment (AWE) 15.0 多物理场协同 CAE 仿真件,建立了立柱有限元实体模型和床身立柱所受载荷情况如图2所示。
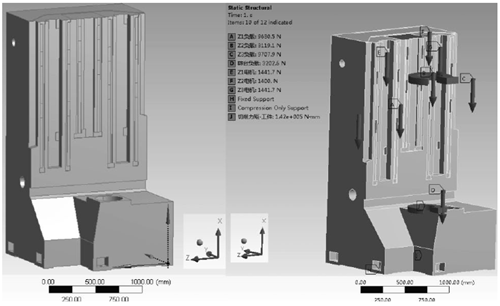
图2:床身立柱载荷分布
采用自动划分网格方法对有限元实体模型进行单元网格划分,由分析知,立柱的最大变形为沿着y轴负方向前倾,最大变形量为30 μm,加工区域变形量约20 μm,该变形符合设计要求,变形情况如图3所示。
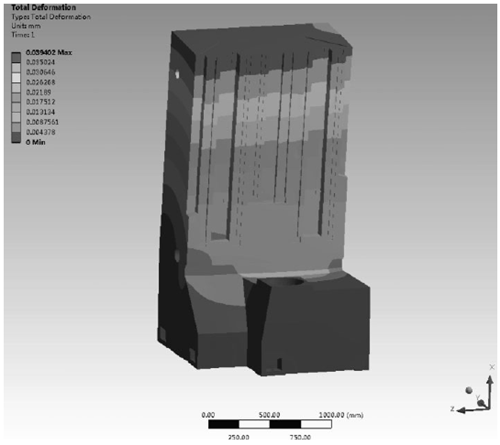
图3:床身立柱变形图
3、绿色环保高速干切技术应用
随着国家环境管理体系标准的实施以及车间环境污染相关法律法规的日益严格,机床设备的绿色制造已成为今后发展的重要方向,所以在机床设计时应用了绿色环保的高速干切技术。高速干切主要体现在以下几个方面。
3.1、排屑系统
随着国家对环保节能的重视,对生产企业的传统切削油管理越来越严格,地方政府甚至呼吁不使用切削油,所以高速干式切削是以后的发展趋势[4]。但是没有切削油,干式切削产生的铁屑不易排出,而且干式切削产生的铁屑速度快,温度高,若不能及时快速的使铁屑排出,对刀具、工件和床身带来的热变形巨大,从而影响轴齿轮的加工精度,因此必须采用有效的排屑系统。在干式加工中,铁屑是刀具和工件相互挤压产生,为了减少铁屑对刀具,工件和床身带来的影响,必须使铁屑快速离开刀具及工件,并通过排屑系统快速流走,减少铁屑与床身的接触时间。
在设计中改变床身结构,加大铁屑流道斜度,便于铁屑及时导出。同时在排屑流道面采用了不锈钢隔热罩,隔热罩与床身之间留有一定的小间隙,不锈钢材料表面光滑有利于铁屑排走,而且不锈钢的热传导系数小,可以减少铁屑热量的传递,同时设计隔热罩与床身之间没有完全接触,减少了床身的热变形,具体结构如图4所示。
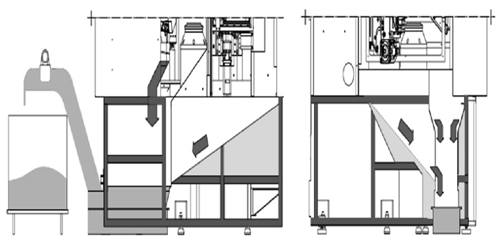
图4:干切排屑系统
3.2、高转速主轴和工作台
高速干切加工必须要刀具和工件的高速旋转才能满足干式切削的需求,干式滚切加工中滚刀线速度的要求为200 m/min甚至更高,目前一般涂层的高速钢滚刀可以达到这个速度,但是硬质合金滚刀线速度可以达到300~400 m/min,这就需要滚刀主轴达到高转速。而对于工作台面为了达到车削时干式切削,同样也要设计为高转速工作台。为了实现高速加工,对于刀具主轴通常采用电主轴或者直驱电机来实现;对于工作台,采用直驱电机来实现。这台复合机床刀具主轴设计转速4000 r/min,工作台面设计转速2000 r/min。
3.3、高速刀具
干式切削用的刀具材料发展初期采用硬质合金钢,但由于硬质合金钢滚刀成本昂贵,近几年发展的粉末冶金高速钢滚刀以及 TiAIN 涂层高速钢滚刀取代了硬质合金钢滚刀。最新研究报告和实际使用效果来看,干式滚切相对于常规湿滚而言,加工时间短,成本更低。采用粉末冶金高速钢滚刀甚至比采用硬质合金钢滚刀具有更好的干式滚切加工效果。目前我国汉江工具生产的涂层滚刀线速度已经可以达到240~300 m/min,国外格里森的涂层滚刀线速度已经可以达到300 m/min 以上。干式滚切加工机床的切削速度可达传统加工的 4 倍,生产效率可以提高 3 倍。与湿式加工相比,加工成本降低,能得到更好的零件质量,且无油污污染,车间工作环境更加洁净。
4、复合柔性功能设计
对于这台复合机床,图 1 所示的只是其中一种柔性配置,在这一种配置中,刀塔共有 12 个刀位,可以根据客户工艺需求配置不同的功能,可以配置车刀、倒棱、去毛细、铣刀、钻头、测头、手抓等功能,刀塔配置图如图 5所示。
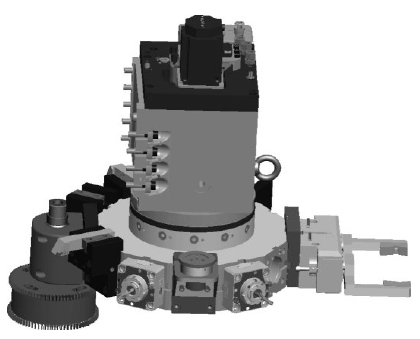
图5:刀塔刀位配置
除了图 1 的配置外,还有其他柔性配置结构,柔性单元配置部分可以采用去毛刺、倒棱和桁架上下料机构的形式,如图 6 所示。除了以上几种配置外还可以采取其他的配置形式,大大增大了机床加工的柔性功能。
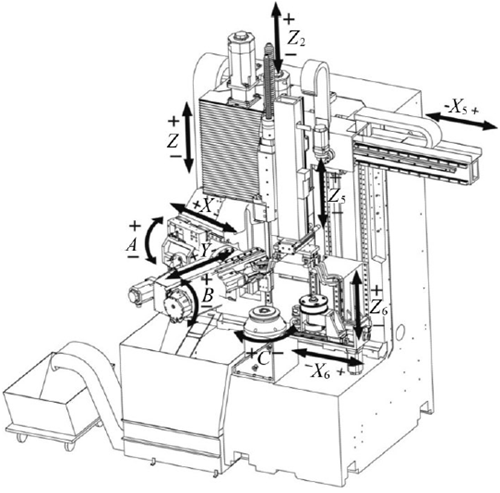
图6:机床配置形式
5、结束语
本文设计的轴齿轮高效复合柔性加工机床体现了以人为本、绿色制造的设计理念,特别适合于传统轿车和新能源汽车变速箱轴齿轮大批量、高精度加工。经过实际使用,滚刀平均滚切线速度可达200 m/min以上,复合加工效率为传统工艺的 2~3 倍,轴齿轮加工精度可达 GB/T10095.1-2008 的 6 级,配备自动上下料机械手可自动抓取和卸放工件,配备料仓后可实现 12 h 无人值守工作模式,提高产品加工效率,提高企业自动化水平。
投稿箱:
如果您有机床行业、企业相关新闻稿件发表,或进行资讯合作,欢迎联系本网编辑部, 邮箱:skjcsc@vip.sina.com
如果您有机床行业、企业相关新闻稿件发表,或进行资讯合作,欢迎联系本网编辑部, 邮箱:skjcsc@vip.sina.com
更多相关信息