一种用于新能源电池托盘的复合加工机床
2025-1-6 来源: 南京宁庆数控机床制造有限公司 作者:蔡 晶 陈建杰
1. 序言
新能源汽车电池模组主要由电池及承载电池的托盘构成,电池托盘通常采用多块铝板进行拼接、焊接而成,然后根据装配需求继续对电池托盘进行一系列钻孔、铣削等加工,从而实现电池托盘的高精度、高平整度,满足电池模组装配及汽车装配的需求。目前,电池托盘的加工工艺基本都需要二次搬运、多次装夹并重新对刀,导致加工流程工序繁杂,加工效率较低,针对此我公司研发了一种用于新能源电池托盘的复合加工机床,托盘在机床上可以一次完成各种钻、铣等加工工艺,既保证了加工质量,又大幅提高了生产效率,并且便于实现自动化生产。
2. 典型电池托盘加工工艺分析
如图 1 所示典型托盘,其正面周边和筋条上分布有孔,且筋条分为 4 列。托盘上孔比较多,φ5mm 孔 66 个,φ6mm 孔 2 个,φ7mm 孔 6 个,φ8mm 孔 38 个,φ9mm 孔 52 个,11mm 六角孔 82 个,φ12mm 孔 6 个,反面 φ7mm 孔 38 个,φ9mm 孔 1 个。
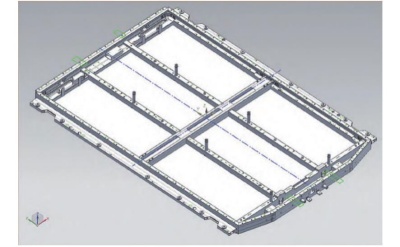
图 1 典型托盘
如果采用现有 LQI2520 高速龙门移动机床(见图 2)加工,需要 17min,并且侧面有 11mm六角孔 13 个、穿线孔 3 个,还需要单独使用侧铣头进行加工。
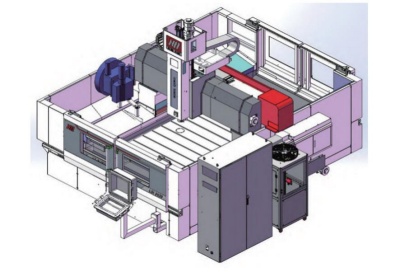
图 2 LQI2520 高速龙门移动机床
采用图3所示新式加工机床, 由机型HSC3036 Ⅲ和机型 HSC3217、桁架系统、自动上下料系统和装夹系统组成。正面、反面和侧面同时加工,加工时间就降低到 1/3,效率提高了3 倍。正面采用三工位卧式机床,如图 4 所示,反面和侧面用一台卧式五轴机床加工,以此大幅度提高加工效率。
3. 电池托盘机床主体结构
图 3 所示新式加工机床由四大部分组成 : 三单元卧式加工单元、卧式五轴单元、工作台底板及夹具、桁架自动化送料系统。
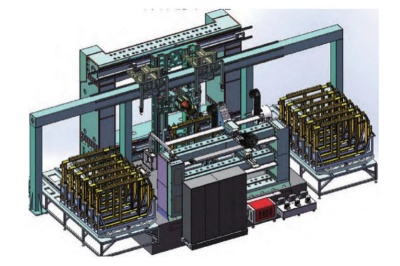
图 3 新式加工机床
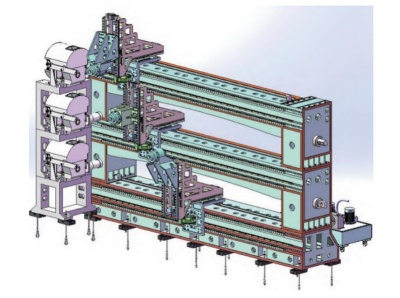
图 4 三工位卧式机床
3.1 三单元卧式加工单元
三单元卧式加工单元有 5 个显著特点。
1)轻量化设计,参与进给部件均在保证强度的基础上,尽可能减轻质量,以确保移动部件的高速与高加速度运行。
2)三组进给轴通过三通道控制,可互不干涉协同运作,上下行程叠加可使加工范围无空白区域。
3)为保证移动速度,X 向大行程采用齿轮齿条驱动,其余两向采用高精度滚珠丝杠驱动。
4)机床可同时加工 3 片区域,理论上效率可提升 2 倍。
5)3 组主轴配置 3 台圆盘刀库,换刀效率高。
3.2 卧式五轴单元
卧式五轴单元如图 5 所示,其特点主要有以下几方面。
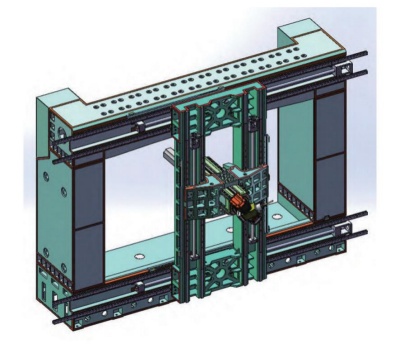
图 5 卧式五轴单元
1)采用箱中箱式结构,抗冲击载荷能力强,可重切,可高速,稳定性高。
2)X/Y 向双丝杠驱动,可以保证高速高精加工需求。
3)三向均配置四线轨,可以保证运行精度与稳定性。
4)X/Y 向大行程可覆盖市场上大多数电池盒尺寸,配置五轴可对斜侧面进行铣削和打孔,有效避免二次装夹。
3.3 工作台底板及夹具
工作台底板及夹具如图 6 所示,其设计特点主要有以下三方面。
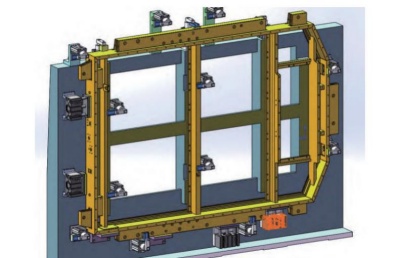
图 6 工作台底板及夹具
1)工作台底板采用镂空式设计,将电池托盘反面需要加工的区域露出,以方便后方卧式五轴 HSC3217 机床对其反面及侧面进行加工。
2)夹具全部采用气缸形式进行夹紧,柔和的夹紧力可避免对工件表面造成损伤或变形,其中旋转气缸的选用,为自动化上下料创造条件。
3)增加的定位挡板,可使批量化生产的每个工件,都可以准确地被装夹在预定的加工区域,实现自动化装夹。
3.4 桁架自动化送料系统
桁架自动化送料系统如图 7 所示,其结构特点如下。
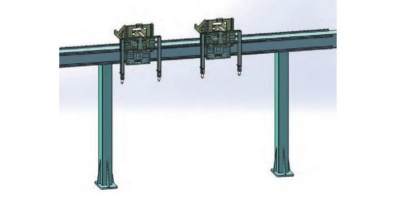
a)悬臂式结构
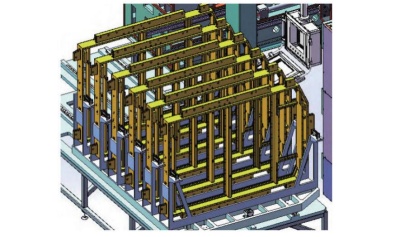
b)料框内设有定位挡板
图 7 桁架自动化送料系统
1)桁架采用悬臂式结构,占用空间小,快捷高效。X 向采用齿条传动,Y、Z 向采用丝杠,为工件的精准取放提供保障。
2)两组进给轴分别用于上料和下料,独立控制互不干涉。
3)采用大规格型钢作主体,以提供较高的刚性和强度。
4)整体式底板上方的独立料框内设有定位挡板,人工将工件放至料框内,同样采用标准气缸固定夹紧,通过齿轮齿条驱动,使毛坯件按顺序分层前进,配合桁架机械手进行抓取,转运至被加工区域。
4. 机床工作方式
电池托盘工件加工时的运行方式如下。
1)人工将毛坯工件装夹至料框内,起动气缸,将毛坯件固定于每个料框内,如图 8 所示。
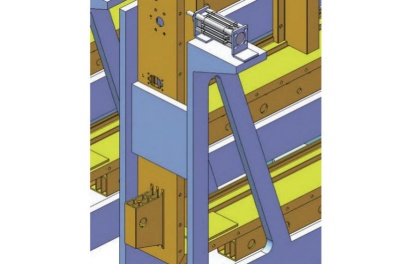
图 8 毛坯工件装夹至料框内
2)运用桁架将毛坯件抓取、提升,运送至加工区域,沿定位挡板向下放置,夹紧气缸开始运行,将工件固定。第一组桁架返回至毛坯区,第二组桁架移至右侧成品区。
3) 三横梁机床 HSC3036 Ⅲ和五轴机床HSC3217 协同运行,对工件正反面及侧面进行加工,期间无需二次装夹。如图 9 所示
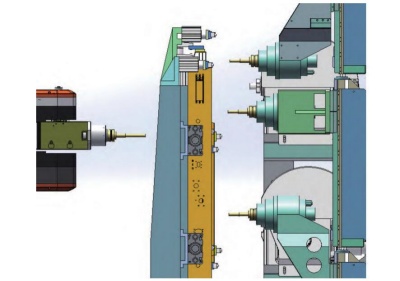
图 9 机床协同运行
5. 系统控制
此机床采用定制化数控系统界面,仅需要输入孔的位置,即可调整规格品种的程序,钻孔攻螺纹的参数可以在后台程序调节。该系统可实现多通道控制,每个卧式通道负责加工产品的一部分。通过定制化软件,有效将工件分成 3 部分,每部分由1个卧式通道完成,大大提高了加工效率。
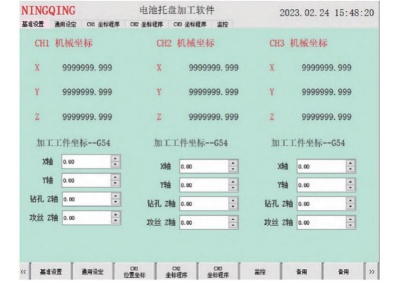
图 10 加工坐标系设定
5.1 加工坐标系设定
加工坐标系设定如图10所示。其特点主要有:可以将三通道的加工工件坐标系放在一起,用来比较以及反复确认 ; 增加微量调整,避免输错,并且调整速度快 ; 此外,系统可提供钻孔和丝锥专用的 Z 轴尺寸,互不影响。
5.2 通用设定画面
通用设定画面如图11所示,参数化编程包含:刀具号、刀具长度、刀具直径、钻孔深度、钻孔/ 攻螺纹转速、进给速度、牙距、快移速度、快移定位、逐钻工艺、抬刀量及一攻到底。
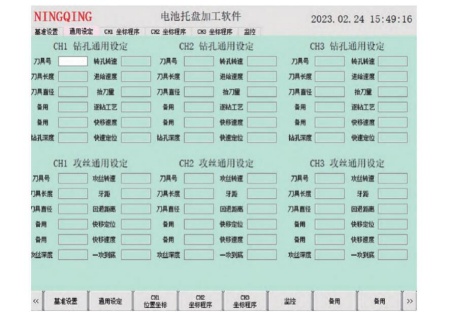
图 11 通用设定画面
5.3 加工工件的坐标程序
加工工件的坐标程序如图 12 所示,以第一通道为例,提供了两套方案。①有规律的孔位加工 : 圆形以及矩形排列。②不规则孔加工方案 :可以定制孔加工的工艺程序,进行固化。
5.4 加工统计
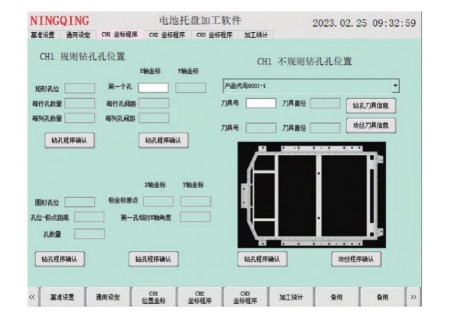
图 12 加工工件的坐标程序
加工统计主要是给机床使用情况做统计,如图 13 所示。
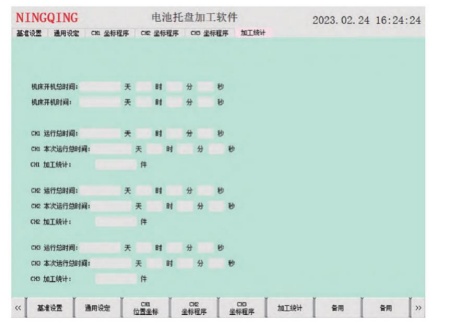
图 13 加工统计
可以看出,通过统计开机时间、运行时间、加工件数等,可以有效地对生产管理所需信息进行统计,引导生产管理人员进一步优化加工工艺和提高加工效率。
6. 结束语
该机床大大提高了电池托盘加工的自动化水平和加工效率,现有的单机生产效率低,采用本组合自动化机床,效率可以提高 2 倍。除了加工效率,更重要的是提高了工件的加工质量。电池托盘是型材焊接件,定位基准误差大,工件自身变形大,采用多次定位极易导致孔位偏差,因此应尽量采用一次性加工,使用该机床解决了原有单机生产多次装夹所导致的孔位误差问题。
该机床还有一种使用方案,即减去 1 个卧式五轴单元,采用自动线单元,仍然能够达到效率和质量的大幅提高,而且采用自动线,1 人可操作多条线,使车间实现少人化生产。
投稿箱:
如果您有机床行业、企业相关新闻稿件发表,或进行资讯合作,欢迎联系本网编辑部, 邮箱:skjcsc@vip.sina.com
如果您有机床行业、企业相关新闻稿件发表,或进行资讯合作,欢迎联系本网编辑部, 邮箱:skjcsc@vip.sina.com
更多相关信息