数控车工巧用刀偏进行切槽加工
2022-9-27 来源:茂名技师学院 作者:张太福
摘要: 数控车床作为现代化的机械设备,不仅可以提升企业生产的效率,更可以确保企业产品的精度。其中在数控车工中巧用刀偏,让传统上难以完成的零部件生产任务变得可以实现,主要表现在制造流程的简化以及各种制造需求的满足。在数控车工工序中切槽加工是重要的环节,是影响零部件加工效率和质量的关键因素。切槽加工的类型分为内沟槽、空刀槽、外沟槽等,加工过程极其复杂,需要工作人员具备极高的专业水平。
关键词: 数控车工;巧用刀偏;切槽;加工
0 引言
所有利用数控车床实施加工制造的工作都称为数控车工,具体涵盖数控编程、个别系统数控车床操控、数控工艺、数控车床操作等,一般情况下,技术人员的工作导向必须遵循企业机械的加工制造计划,对原有数控车工资源进行有效整合,对数控程序实施改进和优化,从而大大缩短机械制造时间,显著提升数控车床制造效率,真正将数控车工自动化、集约化、智能化、系统化、数字化的优势发挥出来,实现企业经济利益的最大化。
1 、数控车工巧用刀偏切槽加工的准备阶段
1.1 机床的合理选择
在没有开始数控车工切槽加工之前,准备工作是十分必要的。其要点之一是在刚性的基础上分析、选择最合适的机床结构。
具体地说,数控机床的主轴必须具备相应的刚性,必须在切槽加工前严格测定机床的刚性,要确保滑板和机床导轨之间合理的间隙。一般情况下,可以利用增加平衡装置或者支撑轴的方式提高机床的刚性。同时,要有效控制夹具的刚性、掌握好机床滚珠丝杠预紧力,以提高后续工艺过程的安全性。
1.2 切削刀具的选择
要想保障切槽加工的良好质量,切削刀具的合理选择是关键的因素。在生产制作期间,刚性和硬度最高的当属硬质合金材质,广泛应用在多数零件的切槽工艺中,具体标准可根据切槽的宽窄度和深度掌控切削力。最关键的一点,要根据切槽加工中的切削参数选择切削刀具,以保证高效安全地进行切削加工。
1.3 加工方式的选择
科学合理的加工方式是简化加工程序和降低加工耗量的有效途径。传统的加工方式可以直接切入,针对很深沟槽务必采用啄式循环手段进行断普通加工沟槽可采用直接切入的加工方式,较深沟槽需使用断屑处理,针对较宽沟槽可以利用数控机床子程序来控制,以保证以准确的角度切入磨削断面和切面。
因为可以多种方式进行数控车工切槽,所以,在切槽加工工序展开前,务必严格分析零件加工图纸的细节和参数,以此选择出最适合的加工方式,以此带动工作效率的提升。
2 、数控车工巧用刀偏进行切槽加工的流程
2.1 对刀方式
一般情况下对刀工艺技术人员会利用切槽刀左刀尖进行,以完成车槽工序,以完成数控车工切槽位置的精准性,通过对切槽刀宽度的掌控,设限车槽宽度。比如,如果想低于 5mm 的槽宽,技术操作者选择切槽刀必须采用小于 5mm 或者与槽宽相等,从水平方向进刀,直接取出槽车,如果槽刀的主切削刀与槽车的宽度不匹配,那么就需要技术人员按照匹配的标准打磨削刀,以保证符合生产加工标准的宽度,特别要严格控制切槽刀宽度,保证合理而精准的刀头尺寸,这些是保证加工精度的前提。
因为数控车工特殊的工艺特点,在应用过程中会造成切削刀的磨损,如果磨损程度突破安全范围,会对车槽精度造成影响,更会让刃磨难度加大,从而加大修磨时间和成本,最严重的状况还导致修改数控车工流程,严重影响综合制造效率。
2.2 槽刀模式
正常情况下,技术人员选择槽刀的标准是略小于槽宽或者与槽宽形同,应用稍小于槽宽的槽刀时,需要操作人员在合理控制槽宽的基础上反复进行扩槽加工,如果应用与槽宽相等的槽刀,只需要保持横向入刀直接取出车槽即可,不管利用哪种加工模式,都需要极高的加工精度,为了杜绝浪费原料现象发生,一般会利用小于槽宽的槽刀进行实际加工,该方式在大于 5mm 的机械制造工序中应用普遍,利用反复车削、操作接刀、借刀操作实现标准的槽宽。
例如,某制造企业在采用 HNC 数控系统操作时,在主轴正转是利用 2 号刀刀偏(#0002)实施车削,快速移动到等待削槽的外圆直径位置,在 30mm 径向处作2s 的停顿,径向退刀的同时向右 0.5mm 处偏移,再次移动向径向直径位置,到 30mm 处作 2s 停顿,同时径向退刀到换刀位置,此刻停止主轴的运动,暂停加工流程。
数控系统的型号不同对刀偏切槽加工流程的设计也各不相同,需要相关人员根据积累的工作经验,遵循相关的加工条件,进行加工程序的合理设计,以保证数控车工巧用刀偏加工切槽的精确度。
2.3 切槽刀二次车削编程
在上面的对刀方式里介绍了车削的方式,通常是应用相等于槽宽的槽刀进行一次车削或者应用稍小于槽宽的槽刀进行再次或者多次扩槽,直至满足要求的沟槽尺寸精度标准,在实际的操作工序中多数会应用后者。如果大于 5mm 的槽宽,就要进行多次车削,实施接刀和接刀的操作,实现宽槽的尺寸标准。例如图1 所示工件,其中设计 4.5mm 的切槽刀宽度。以华中世纪星 HNC 数控系统为例,程序编制如下:
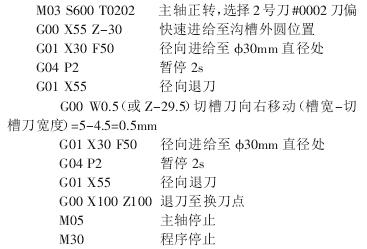
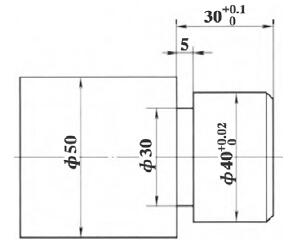
图1 工件示意图
2.4 试切法
在应用对刀的过程中最常用的是试切法,比如在某制造企业中应用 HNC 数控系统时,主轴在刀具、工件装夹完备进行驱动,对刀时控制左刀是标准的 02刀补,而右刀尖则是采用非常用刀补,如 08 刀补,对刀首选应用左刀尖,将刀架停置在原先试刀处,以保证结构外圆上切槽刀能够有一条亮线留下,切槽刀切削刀的现有位置是原工件外圆直径 50.00mm。在确保 X 坐标不发生改变的情况下移动 Z 轴,进行外圆直径的测量,并在刀具参数中录入测量数据,以保证试切直径的准确无误,与此同时,数控系统会自动选出刀具,利用 X 轴坐标与外圆直径相减,会求出工件的坐标原点以及与 X 轴位置的偏差。
3 、数控车工巧用刀偏切槽加工刀尖车削分析
3.1 选择刀偏方式
在应用刀偏进行切槽加工刀尖车削的过程中,必须采用适合的刀偏方式。基于零件加工要求、数控车工性能的制约,刀偏方法差异性很大。
第一,有效调整右刀尖车削程度,获得工件位置坐标,刀偏可在工件外圆直径处进行;
第二,在刀偏模式的基础上,有效调控其他切槽刀,刀偏在工件外圆直径 30mm 处;第三,径向退刀到换刀尖,切槽加工程序停止。切槽走刀路线如图 2 所示。
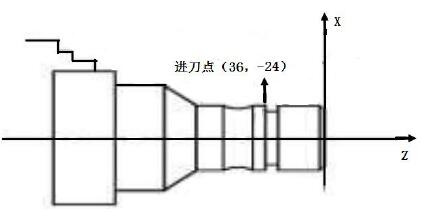
图 2 切槽走刀路线
3.2 选择车削模式
适当车削方式的选择要根据切槽刀磨损程度确定。切槽加工的精度会受到槽刀和车刀磨损情况的直接影响,要求相关技术人员对车刀进行刃磨,对槽刀和车刀磨损程度进行有效控制,确保槽刀精准运行。针对切槽刀刀刃磨损后宽度减少的情况,应对措施是在数控车工切槽加工程序中输入原有槽刀数值。
例如,在切槽宽度不足的状态下,操作人员必须对磨损部位进行准确判断,并根据槽宽以及槽位等相关数据,进行磨损数值的计算,同时在程序中调整磨损值。
3.3 构建车床模型
为了让数控车工巧用刀偏切槽加工水平得以提高,必须进行对应的车床模型构建,深入分析数控车床零件设计方案,生成相关数控代码模块、管理文件信息模块等,对数控车工切槽加工流程进行优化。
4 、结束语
综上所述,现代工业技术的突飞猛进让数控车床结构日趋完善,从而带动了切槽种类的迅速发展。数控车工技术的发展显著提升了企业零部件加工的精度,也提高了切槽加工的效率,压缩了产品制造的成本。但在具体的操作过程中,以上目标实现不是轻而易举做到的,技术人员必须根据零部件加工的实际情况,对加工工艺进行不断的创新,充分发挥数控车工具备的自动化、数字化的优势,合理简化数控车工制造流程和操作程序,切实保证数控车工的
科学性、合理性和可靠性,以推动我国数控行业的可持续发挥。
投稿箱:
如果您有机床行业、企业相关新闻稿件发表,或进行资讯合作,欢迎联系本网编辑部, 邮箱:skjcsc@vip.sina.com
如果您有机床行业、企业相关新闻稿件发表,或进行资讯合作,欢迎联系本网编辑部, 邮箱:skjcsc@vip.sina.com