利用车床钻削小孔的工艺研究
2021-11-16 来源: 中国空空导弹研究院 作者:翟建伟
摘要:以实际加工案例为基础,对车削加工中钻削 准1.5 mm 小孔的加工工艺进行分析,找出钻削过程中影响加工质量和加工效率的主要因素,并根据案例中的加工经验,提出了一种对钻头改进的方法,为小孔加工提供了解决方案,同时也为其他小孔加工提供参考。
关键词:机械加工;车削;小孔
0 前言
在航空产品中,结构重量是衡量产品性能的一个非常重要的指标。为了提高产品的指标,设计人员在设计产品时,在满足其他性能指标的前提下,会尽可能的压缩结构尺寸以追求更轻的产品。压缩结构尺寸可以有效地减轻结构重量,但带来的问题就是产品零件变小,更小的零件意味着零件上各种特征的尺寸也会变得更小,对于传统机械加工来说,尺寸过大或过小的零件特征都是加工中的难点。
在零件的各种特征中,孔是较难加工的一种。由于孔本身的特殊结构,在加工中存在排屑不畅、冷却润滑不及时等各种问题,容易在加工中出现孔内壁糙度差、孔轴线直线度差、孔横截面圆度差、孔直径尺寸精度差,孔定位尺寸精度差等各种问题,常常成为零件质量问题的高发点,尤其是对于长径比比较大的孔,加工难度较一般孔更大。
由于产品的各种限制,实际设计出的零件往往是上面两种加工难点的叠加,即长径比大的小孔。当前,国内外已经发展出了很多新的加工方法可以完成此类小孔的加工,如激光、电腐蚀、高能粒子束等加工方法,均可以比该孔直径更小、长径比更大的孔的加工。但这些加工方法均存在加工效率低和加工成本高的问题,传统的机械加工虽然没有新方法的加工能力强,无法完成许多有极端要求的特征的加工,但在加工成本和加工效率方面相比较于这些新方法却占有很大的优势。因此如果可以发掘传统机械加工的潜力,拓展传统机械加工的适用范围,就可以完成一些要求比较苛刻的零件的加工,为零件生产降低加工成本和提高加工效率提供了有效的解决方法。
车削加工是一种传统的机械加工方法,其最大的优点就是加工回转体时圆度特别好,因此很适合加工孔或轴等回转体特征。本文以实际加工案例为范例,讨论了如何使用车削加工完成长径比为 12.3的 准1.5 mm 小孔的加工,并据此探讨在加工大长径比的小孔时需注意的事项以及可采用的一些方法。
1、加工难点分析
零件结构示意图如图 1 所示。
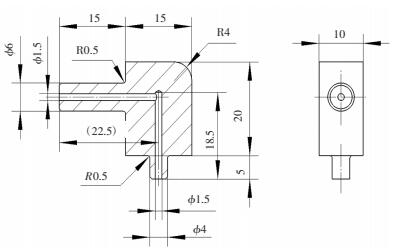
图 1 零件结构示意图
从图 1 中可以看出,该零件为接头类零件,中间有贯穿孔用于工作时介质流动。由于零件尺寸很小,因此零件上各特征的结构尺寸也很小。零件材料为17-4PH,材料出厂时进行过热处理,材料硬度在HRC40 左右。由于该零件从结构上并不是回转体,适合在数控铣床上进行加工,因此主要特征均是在数控铣床上完成的加工。但由于两个孔的加工难度较大,数控铣床的无法满足加工要求,因此孔的加工选择在数控车床上完成。而零件的装夹则是通过设计专用镶嵌式夹具来完成装夹(关于夹具的设计这里就不在详细说明)。
所需加工孔孔直径均为 准1.5 mm,其中一个较浅的孔深度为 18.5 mm,长径比为 12.3;另外一个孔要求和这个孔贯穿,因此深度至少要达到 22.5 mm,即长径比至少为 15。
长径比值大的孔在加工时可以选择从两端向中间对向加工以变相的减小孔的长径比值。但这个零件上的孔是盲孔,因此加工时必须从孔口加工,这就对加工工艺提出了较高的要求,在面对批量生产的情况时,使用普通的加工工艺无法完成零件的稳定加工,需要对加工工艺进行改进。
1.1 排屑问题
排屑是机械加工中的一个重要问题,及时排出切屑,可以方便刀具继续对零件材料进行切削,提高加工效率。机械加工行业经过长期发展,绝大部分加工过程,如车、铣、刨等,无论是刀具的排屑槽,还是机床断屑器,加工过程中都有了比较完善的排屑措施,日常加工中基本可以不用单独考虑排屑的问题。但在此次孔的加工过程中,排屑不畅的问题非常严重。主要原因是钻孔加工与其他加工,如和车削外圆相比最大的不同,就是孔的直径限制了刀具的尺寸。对于该孔的加工,使用钻头的直径只能选择准1.5 mm。钻头直径限制了钻头上的排屑槽深度很小,再加上钻头钻孔过程中钻头和孔内壁紧密贴合,钻进过程中产生的切屑必须完全依靠排屑槽排出,如果孔内的切屑不能及时排出,不仅影响钻进效率,严重时还会发生孔内事故。主要是因为由于钻头直径太小,导致钻头的强度小、刚性差,加工过程中产生的切屑如果不能及时排出,切屑夹在钻头和零件之间,会对钻头产生挤压,由于钻头刚性差的原因,稍微对钻头产生的挤压就会造成钻头折断,轻则造成钻头报废,重则会使断掉的钻头与零件“咬死”而造成零件报废。
机械加工过程中,切削液的冲洗对排屑也起了非常大的用处。但在该加工过程中,切削液也无法有效冲洗到加工面。该情况将在 1.2 切削热问题部分进行详述。
1.2 切削热问题
机械加工过程中,切削液的冲洗有两个作用,一是对加工刀具和材料进行降温,二是冲走加工后产生的切屑。一般条件下,机械加工过程中会使用尽可能大流量的切削液对加工部位进行直接冲洗,但在该零件加工钻孔过程中,切削液无法有效冲洗到加工部位。主要原因是因为孔的直径很小,钻头直径也很小,该尺寸的钻头没有中央出水的类型,而在加工过程中钻头紧密贴合孔内壁,因此切削液要进入加工部位必须通过排屑槽进入。但由于钻头直径太小,钻头上的排屑槽深度也很浅,导致冷却液很难进入小孔内部,无法实时对切削刃进行冷却,容易造成切削刃升温过快造成钻头刀刃磨损甚至烧毁钻头。
1.3 钻头强度问题
钻头的结构为细长型,长径比很大,所以钻头的强度一般都不高,并且在实际使用过程中强度会随着刀具伸出长度的增加而进一步下降,钻削加工又属于切削力较大的加工方式,所以在加工前选择钻头时要特别注意钻头强度是否能够满足加工要求。
钻头的强度和钻头的直径正相关,小钻头直径小,并且钻头上还有排屑槽,会使钻头的强度进一步降低,使钻头在加工过程中无法承受较大的切削力或其他冲击力,如果使用不当,比如钻孔过程中进给速度过快,很容易在加工过程中发生钻头折断的情况。
1.4 精度问题
在车床上钻削小孔的过程中,零件轴线和钻头轴线的同轴度对加工的影响很大,如果因为精度的原因,造成零件轴线和钻头轴线不在同一条线上,加工过程中钻头会承受很大的径向力,尤其是钻头刚钻入时,此时不同轴会造成钻头接触零件不均匀,会给钻头施加很大的径向力,而此时钻头悬空长度是最长的,也就意味着此时钻头的结构强度是最弱的,这也成为钻孔时钻头折断的高发点。
2、 改进方法与措施
2.1 多退刀,勤排屑
切屑对加工过程影响很大,由于钻头直径小,钻头上的排屑槽也很浅,排屑能力弱,如果光靠排屑槽进行排屑无法满足稳定加工的要求,加工过程中必须通过退刀的方式,使钻头完全退出孔以彻底排出切屑。数控车床可以通过编制数控加工程序对加工过程进行精确控制,以哈挺数控车床为例(数控系统为 FANUC),控制系统中内置了一种点钻的加工方式用以解决此问题。该程序语句为:G1101 W()F()Q()P()B()L(),在钻孔程序中使用该语句进行加工,机床就可以每次步进一定深度后自动退出刀具进行排屑[1]。
需要注意的是,由于刀具排屑槽排屑能力弱,切屑很难在产生的同时被同步排出孔外,实际过程是切削产生的切屑被储存在钻头前段的排屑槽内,等钻头退出孔时再完全排出孔外。由于排屑槽储存切屑能力有限,所以每次步进的深度不能过深,否则产生的切屑过多,排屑槽无法储存,多余的切屑就会堆积在孔底或孔壁处,对加工过程造成影响,退刀排屑的意义就失去了。但步进深度也不宜过小,否则进退刀次数过多,会严重降低加工效率,从加工经验得到的参考值每次步进深度均保持在 0.5 mm 左右为宜,钻孔时进给速度也不易过快,但可提高退刀的进给速度以保证整体加工效率。
2.2 改造钻头,增强强度
在批量加工零件的过程中,单纯采取退刀的措施并不能完全解决钻头折断的问题,为保证钻头的强度,此次加工过程中在普通钻头结构的基础上进行了修改,制作了专用钻头用于孔的加工。改进后的钻头结构示意图如图 2 所示。
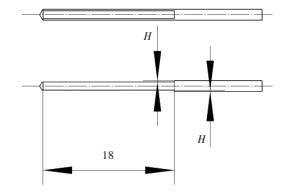
图 2 钻头结构示意图
钻头制造原料的选择上可以选用与孔直径一样的高速钢或硬质合金棒,在需要钻孔的深度范围内将钻头磨扁,一般 H 值可选择在 0.1 ~ 0.2 mm 之间,这样的结构取消了排屑槽,极大地增强了钻头的强度,同时磨扁的部分也可以兼顾排屑的功能,前端切削刃的刃磨与普通钻头保持相同结构即可。经实际加工测试,按此方法改进制作的钻头比普通商用钻头强度更高,在相同的切削参数、排屑情况和冷却条件下,不但加工出的零件质量更好,而且能避免折断钻头,保证了整批零件加工的顺利进行,提高了整批零件的加工效率。
从改制钻头的结构示意图上看,钻头应该只满足深度 18.5 mm 孔的加工需求,加工另一个孔则面临长度不足的问题。需要强调的是,零件中贯穿的两个孔,在加工顺序上必须严格分先后,深度为18.5mm 的孔先加工,然后再加工另一个孔。这是由于两孔相互贯穿,在加工第二个孔时,很难保证孔的轴线和第一个孔轴线相交,因此钻头在钻破第一个孔时有可能存在钻头受力不均衡问题而导致钻头折断。为避免该问题,在加工时钻头仅钻入 19 mm 就不再继续钻进,最后的 3 mm 改用 1.5 mm 铣刀进行加工,即将 1.5 mm 铣刀装夹在刀盘上,利用铣刀完成最后两孔钻透的加工过程,由于铣刀强度较高且铣刀侧齿可用于切削,因此可有效避免折断情况的发生。
2.3 检查中心轴线是否重合
该零件加工时,零件是通过夹具装夹在机床卡盘上,而刀具装夹在机床刀盘上,机床本身、夹具、装夹过程都会存在误差,这些误差累计起来会造成零件与刀具的装夹误差,这误差会对零件加工造成影响,因此加工前必须检查校正。
检查装夹精度时,必须检查在零件和钻头装夹好的情况下,钻头轴线和零件轴线是否重合,本次加工过程中使用的是一种比较简单的检查方法[2]:第一步用磁吸式固定器将千分表固定在机床刀盘上,千分表表头接触零件外圆表面,然后沿机床 X 轴方向前后移动刀盘,观察千分表数值变化,要求要将零件调整到千分表数值变化不超过 0.02 mm,这样的检测要在零件圆周上选择均布的三条线进行测量,三条线的测试都合格才算合格。第二步,使千分表表头接触零件外圆,用手搬动机床主轴,使零件按机床 A 轴
旋转,观察旋转过程中千分表数值变化,同第一步一样,变化范围不超过 0.02 mm 才算合格。如果发现误差过大,则需要进行调整校正,调整的循序按照难易程度安排,先零件、再夹具、最后机床;如果对零件和夹具的调整都无法修正误差,而在对机床进行调整后依然无法达到加工要求,则说明机床精度以无法满足加工要求,必须更换机床进行加工,否则将无法保证加工效果。
3、加工结果验证
通过数据对比来验证了改进方法和措施的有效性,改进前后两种工艺方案的加工结果如表 1 所示。
表 1 加工结果对照表
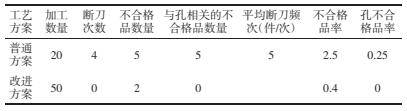
从表 1 的数据可以得到质量对比的折线图如图3 所示。
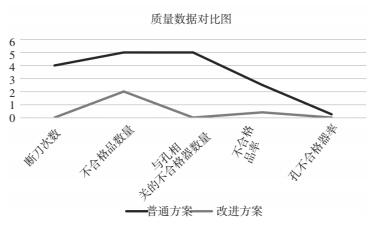
图 3 质量数据对比图
从图 3 中可以很清晰地看出,虽然没有定量的计算,但改进后的工艺方案的有效性还是非常明显的,零件质量有非常大的改善,证明了改进方法和措施解决了孔加工过程中存在的问题。
4、 结束语
本文提出了一种对钻头改进利用车床钻削小孔方法,为小孔加工提供了解决方案。对类似的小孔加工本文中的工艺方案可以借鉴,但需要根据具体的情况不同采取的对应措施,不能照搬,但在制定工艺方案时,一些共同点必须要考虑:
(1)要加强退刀排屑,不能简单依靠钻头的排屑槽排屑;
(2)商用钻头不一定满足所有加工工艺方案的要求,要根据具体情况考虑自制钻头;
(3)要对零件装夹后的位置精度进行测量并调整,否则会影响零件的加工。
投稿箱:
如果您有机床行业、企业相关新闻稿件发表,或进行资讯合作,欢迎联系本网编辑部, 邮箱:skjcsc@vip.sina.com
如果您有机床行业、企业相关新闻稿件发表,或进行资讯合作,欢迎联系本网编辑部, 邮箱:skjcsc@vip.sina.com