钛合金舵芯高效加工技术研究
2021-11-2 来源:首都航天机械有限公司 作者:战祥鑫,张玉强,李涵,苏晓,杨春月等
摘要: 舵芯组件采用难加工材料钛合金制造,整体由舵芯骨架与舵芯蒙皮焊接而成,外形为一种靠空间复合面组成的楔形结构。针对多个型号舵芯加工过程中反复装夹、找正、测量与切削导致加工周期长和加工效率低等问题,通过对加工方法进行机理分析,从设计通用性较强的组合工装、完善加工流程以及合理选用刀具参数三方面出发,进行高效加工技术研究,大大缩短了舵芯产品的加工周期,进一步提升了产品加工质量稳定性。
关键词: 钛合金; 空间复合面; 组合工装; 高效加工技术
1、引言
舵芯是航空航天飞行器结构中的重要零件,在控制飞行姿态上起至关重要的作用,因此,其加工精度直接影响产品飞行的精度。钛合金舵芯凭借轻质化、高刚度的优势被广泛应用于航空航天领域。但是由于该材料硬度高、热传导率低,且产品结构复杂、不易装夹,在加工过程中局部余量去除大且易变形,难以保证较高的精度要求。为保证零件的加工精度,传统工艺采用反复加工的方法,导致其加工工序多、生产周期长,无法满足生产需求。
针对上述问题,本文从加工流程、工装和刀具等方面入手,优化原有的舵芯加工工艺,通过实际生产验证优化后的工艺方法大幅缩短舵芯的加工周期,成功解决了多项综合性难题,进一步提高了零件的加工质量稳定性。
2、 结构特点和加工难点
某型号舵芯产品零件如图 1 所示。舵芯结构形状特殊,是一种复杂的结构件,由舵芯骨架与舵芯蒙皮焊接而成,内部骨架上分布着一系列环向和辐射状的加强筋。两侧的蒙皮是由两个不同角度组合而成的复合型面,同时舵面两端厚度差大,整体呈楔形结构,对装夹定位造成了极大的困难 。
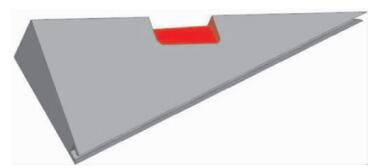
图1 舵芯结构
钛合金舵芯产品中骨架材料为铸造 ZT4 钛合金,蒙皮材料为锻造 TC4( Ti-6Al-4V) 钛合金,尽管钛合金存在诸多优点: 包括高比强度远超过强度高而密度大的钢,密度小但强度较低的铝合金; 抗腐蚀性强,多数情况下不需要附加表面保护层; 耐热性远高于铝合金,工作温度范围较大。但钛合金产品给机械加工带来极大地挑战: 热传导率低,仅15. 24W/( m·K) ,加剧刀具磨损; 弹性模量低,载荷作用下发生变形后产生极大的回弹,造成让刀现象;化学活性高,亲和作用大,在切削温度高时,切削及被切削表层与刀具材料咬合而产生严重的粘刀现象,引起剧烈的粘结磨损 。
舵芯的加工精度将直接影响飞行器的飞行精度,因此对产品配合安装面的加工精度有较高要求:两侧斜面的平面度和对称度要求较高,下陷尺寸公差为 0. 01 ~ 0. 025。加工过程中局部去除余量大且
不均匀,切削热不易散出,原材料残余应力较大,易变形; 同时受零件厚度不均、装夹不易和薄壁网格结构的影响,切削时易振动,造成打刀现象,难以保证舵芯的高精度加工要求。
3、工艺措施优化
针对上述加工难点,从全流程对产品辅助工装、加工流程及刀具切削参数进行了三方面的改进。
3.1工装优化
由于舵芯产品的外形面为复合结构,在铣削、陷时无法通过外形复合面来进行定位,传统工装在设计时考虑通过虎钳夹紧利用零件下陷定位,如图2 所示。
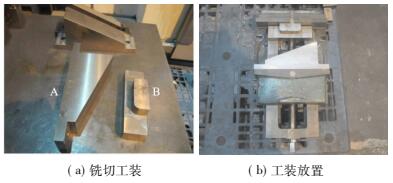
图 2 传统辅助工装
在加工下陷特征的过程中,需保证两侧的对称度,每次粗加工完成后都要反复测量外形不同位置的对称度并重新装夹找正。零件每装夹一次,铣切工装 A 也需要重新安装一次,以保证与零件斜边一致,整个加工过程中零件和工装装夹次数较多,过程繁琐,加工周期长。同时,不同型号产品对应的舵芯角度不同,在实际生产中需要针对不同角度设计各自专用的工装,导致辅助工装的通用性较差,无法进行互换,降低生产成本。
基于上述问题,从零件结构特点出发,设计了如图 3 所示的舵芯批产通用组合工装[4,5]。定位块两个面和舵芯两个面相互贴合,夹具体底面和舵芯底面贴合从而实现舵芯的快速定位。舵芯的夹紧主要是通过楔形压紧块和固定块共同完成的,通过定位销将固定块定位于夹具体上,并利用压板完成固定块的固定,将楔形压紧块沿固定块导槽放入,楔形压紧块另一面和舵芯实现紧密贴合,通过螺栓和螺母将压紧块连接到夹具底座上。由于舵芯与楔形压紧块接触面为斜面,受力分解得到三个方向的作用力,分别指向三个定位面,从而实现舵芯的压紧。改进后的工装见图 4。
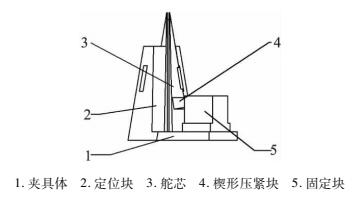
图3 舵芯组合工装结构
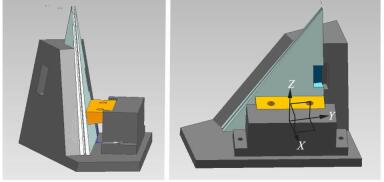
图 4 改进后的工装
工装结构主要由定位机构、夹紧机构和辅助支撑机构三部分组成,结构设计紧凑,操作方便,可靠性高。和传统的工装相比,改进后的工装不受零件复合面及斜边角度的限制,一套工装可完成多个型号舵芯的加工,通用性强,能满足多个型号舵芯批量生产的需要。
3.2 加工流程优化
舵芯产品是复杂结构件,在加工两侧下陷特征时,由于余量较大,精度要求高,需要进行粗铣和精铣,使用传统工装定位,边加工边测量校对,整个产品需完成 20 道工序,多次装夹找正导致整个产品生产周期长,加工效率低。而且过多的人为装夹、拆卸等操作使加工误差增大,降低了产品的一次加工合格率,经常需要返修,浪费大量人工和机床成本。
在新辅助工装的配合下,取消加工两侧下陷时的粗铣和精铣之分,在一次装夹状态下利用五轴设备的 C 轴回转功能完成对两侧下陷特征的精加工。改进后的方法不需要通过原有的两次协调来保证对称度,只需要通过机床 C 轴的精度来保证对称度,排除人为误差,保证产品一致性。合并传统流程中的多道重复工序,最终将加工流程优化为如图 5 所示的 11 道工序 。
3. 3 刀具及切削参数选择
刀具的选择不仅影响到数控加工的效率,还直接影响零件产品的质量。针对钛合金这种难切削材料,大多采用 PCBN( 聚晶立方氮化硼) 刀片、金刚石刀片、陶瓷刀具和硬质合金刀具等,都具备较高的硬度、耐磨性、耐热性及足够的强度和韧性。但是,前三种材料的刀具价格昂贵,且在加工薄壁零件时易产生振动现象,综合考虑经济性和切削稳定性等情况,最终选择 Y330( K30) 的硬质合金铣刀为刀具材料,其属于钨钴类硬质合金,亚细晶粒合金强度高韧性好、耐磨性适中且通用性强,适用于精加工高温合
金及钛合金等 。
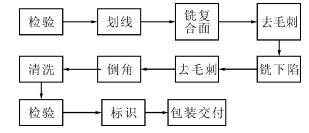
图 5 优化后的加工流程
由于钛合金材料自身的特性,使刀片刃口极易磨损,刀具磨损后会增大刀 - 件摩擦力,不仅影响工件表面粗糙度质量,还会使切削温度升高,导致零件变形,大大降低了刀具的寿命[9]。刀具磨损后需立即更换新刀片,易造成浪费。为了进一步提高加工效率,节省成本,采取对磨损刀片的重新刃磨方法,将同一把刀体上安装的若干刀片同时刃磨,保证刃口几何尺寸及精度的一致性,从而使得磨损后的刀片再次利用。通过大量试验确定的加工刀具参数见表 1。
表 1 加工刀具参数
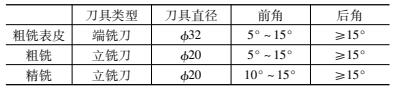
采用顺铣可以最大限度降低加工切屑瘤对铣刀的破坏以及切屑与切削刃的焊合程度,使用大量水溶性油以及气相亚硝胺型防锈液作为切削液可以达到较好的冷却效果。考虑到零件内部的薄壁网格结构,切削过程中冲击力较大时易产生振动造成打刀现象。经过多次试验得到钛合金切削参数见表 2。
表 2 钛合金切削参数
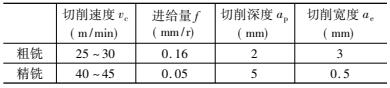
4、 结语
针对多种型号舵芯产品加工过程中的难点,基于加工全流程设计出了一种通用性较强的组合工装,节省了大量装夹、找正和测量时间; 针对钛合金内部薄壁网格结构的焊接件,优化工艺流程,合理选用刀具参数,有效提高了舵芯批生产效率,缩短生产周期,降低了工人的劳动强度,实现了产品高效、高精度的生产。结果表明,该方法不仅能够解决舵芯产品生产面临的诸多难题,而且对类似产品工艺流程设计具有重要参考价值,对新型产品的研制及批产提供了借鉴。
投稿箱:
如果您有机床行业、企业相关新闻稿件发表,或进行资讯合作,欢迎联系本网编辑部, 邮箱:skjcsc@vip.sina.com
如果您有机床行业、企业相关新闻稿件发表,或进行资讯合作,欢迎联系本网编辑部, 邮箱:skjcsc@vip.sina.com
更多相关信息