基于云制造的数控机床自动化生产系统设计
2021-6-7 来源: 南昌大学 科学技术学院 作者:罗永洪,胡小兵
摘要:传统的数控机床存在自动化程度差、系统集成度低的问题,为了提高数控机床的信息资源自动化程度,文中设计资源元数据粒度模型,剔除了机床生产中的冗余信息并提高其控制效率。针对解决数控机床控制难以集成的问题,文中设计基于软 PLC 的数控机床控制方案。通过硬件与软件分离技术提高自动控制系统的可移植性,实现云端上位机的集中控制。为了验证该方案的可行性,文中建立基于三轴作动器的数控机床验证平台,相比于两种传统方案,该方案耗时减少了50%,能耗更低,且准确性提高了 12% 以上。
关键词:数控机床;自动化生产;系统设计;云制造;粒度模型;自动控制
0 引言
传统数控机床在生产上仍较大程度地依赖于人的参与程度,主要是通过人为设定控制器与主轴装置并驱动机床的作动器与电机来完成。而嵌入式数控机床在正常工作时,只能控制驱动装置与主轴,不能控制液压冷却系统等辅助装置,从而大幅降低了数控机床生产系统的自动化水平。在云制造技术蓬勃发展的背景下,通信频带大幅拓宽,且控制延时显著降低。本文基于云制造技术,使用软 PLC 设计的方法设计了一套数控车床自动生产方案。通过云端上位机的开发环境更改数控机床的相关配置,从而达到自动化生产的目的。
1 、数控机床控制结构建模
由于粒度结构具有可拓展且便于分解的特点,能够精确地分析车床的信息资源,且准确检测元数据的相关信息。因此,可以对车床控制系统建立其元数据粒度结构模型,如下所述。
1.1 粒度结构建模
定义三元组(X,F,T)表征车床资源的元数据:元数据集合为 X;数据间映射集合为 F;欧氏空间中的元数据集合为 Y;粒度结构为 T,用于描述数据粒度间的关系。对于车床元数据粒度结构模型,分析器的元数据对象与特征信息处理步骤如下:
1)获取数控机床的制造信息中所包含的元数据对象及其特征信息。其中,R 代表元数据对象集合;Ri为资源类型,包括产品、人力与管理资源;Rij代表不同类型中含有的资源对象。
2)定义数控机床的信息制造元数的特征映射体系F(R)。通过对其表征的信息资源数据对象与生产周期中映射关系的研究,对于主要特征的加工进行处理,从而获取资源数据对象的主要特征。
3)定义数控机床的资源元数据特征集合{ C1,C2,…,Ck,…,Ckn}。其中,Ck 代表元数据集合 R 所对应的对象 Rij,Ckn代表元数据对象的具体特征。该数据通过生产过程中的各种映射关系被获取,是元数据各项指标的集中检测。
通过对数控机床信息资源的精准建模,采集关于数控机床的所有信息。但由于采集到的信息存在冗余重复现象,故依据实际情况对数控机床制造信息资源内部信息数据进行关联。定义 OEM:Xg→< Rg,其中,第 g粒度层元数据定义为 Rg,数控机床采集到的相关信息表示为 xR。g=1 时,R1= { R1,R2,…,Rm}。通过对于粒度模型的建立,有效筛选掉数控机床的制造信息模型并建立自动化控制模型,如下:

式中,X 为数控机床数据中的信息平均值。当采集到的数控机床数据量大于阈值 X 时,模型记录本机采样值;否则,输出上一粒度层次的元数据记录 Rg - 1。
2 、基于 PLC 的控制系统设计
本次设计使用软 PLC 系统与硬件独立的策略,提高了软件设计在不同程序间的复用率,降低了系统集成成本。在设计时,使用成熟的通信协议建立模块式架构与非线性控制的控制系统。控制系统中使用共享交互内存机制,在对 CNC 执行器发送指令的周期内,同步硬件的信息交换与中央处理单元的数据,进而达到控制系统全局数据更新的目的。通过对 CNC 嵌入式电路中的物理与逻辑地址序列进行依次比对,然后逐一计算出数据矩阵中输入/输出端口的各项配置参数。在前期开发设备时,对硬件进行确认;在云制造环境下,高速工业网络选择具有唯一 ID的模块。PLC 输入/输出配置结构如图 1 所示。
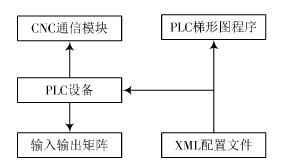
图 1 PLC 配置结构
系统的运作流程如下:
1)对连接到 CNC 系统的所有 PLC 及周边设备进行初始化,各设备发送包含制造商信息与产品型号的初始化数据至控制系统核心的程序启动模块。
2)将上述信息转换为矩阵形式,输入/输出设备组由通信模块与内部总线组成。物理信号在输入槽转换为逻辑信号,逻辑信号在后续运行中进入软件控制的共享存储单元与数据处理器中。
3)计算硬件配置。假定任意模块 i 的第 j 个插槽存储器存在一个数据包,对任意第 i 个模块所有插槽共享储存单元数据量( S)Di的计算公式如下:

对于任意模块 i,存储区域的偏移量( O)Di为之前按模块 i-1 个数据包偏移量的总和。任意字节偏移量计算公式为:
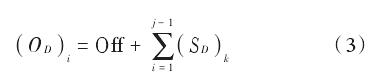
对于任意插槽 j,相对于数据模块 i 的初始字节偏移量(0s)ij计算公式为:

计 算 式(3)与 式(4)之 和 的 初 始 字 节 总 数 Nij =( OD)i +( SD)i。
4)建立插槽每个字节与插槽数据包间的逻辑地址关联性。Ixy与 Qxy分别表示输入变量池和输出变量池中字节 X 的第 Y 位;IBx与 QBx分别表示输入和输出变量区域的字节数 X ( B)x。在控制程序设计方案中,对于基于模块类型的输入/输出假设是合理且可执行的。在软 PLC编译中可执行代码并不绑定至特定平台,而是在执行时以 XML可扩展语言的形式介入硬件间的通信协议。
3 、实验验证
本文基于 PLC 的机床自动生产平台在嵌入式 Linux系统的基础上搭建。Linux 系统中使用 CODESYS 开发环境,CNC 硬件主板为 OK335x S 开发板,数控机床从站为 3 组 Omron 伺服驱动器,通信总线使用 Mod Bus 协议。人机交互系统 GUI 如图 2 所示。在系统 GUI 中,能够实现对配置文件的操作,右侧窗口可以对三轴伺服系统的状态进行实时监控。
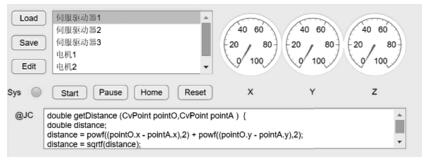
图 2 CNC 系统 GUI
系统硬件的控制系统如图 3 所示。所用的主轴异步电机实物如图 4 所示。
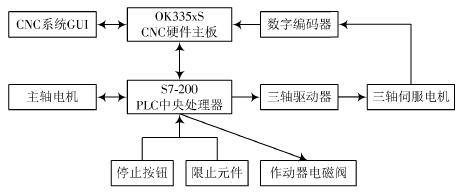
图 3 系统控制结构
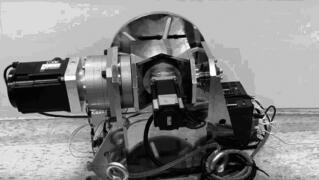
图 4 主轴异步电机实物
验证 CNC 自动控制系统各项性能,在云端控制器的 CNC 编辑器中建立相应的 PLC 代码。生成代码后,通过编译形成伺服系统控制器的执行代码,上传至车床PLC 系统运行测试,其结果如表 1 所示。
表 1 PLC 运行参数
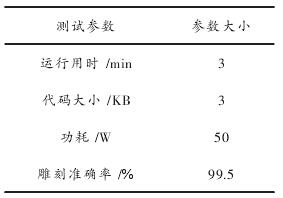
为了对数控机床的信息资源可靠性进行检测,分别从检测准确性、检测时间与能量消耗方面对本机床系统与常用的两种方案进行测试,结果如表 2 所示。
表 2 自动化机床系统对比
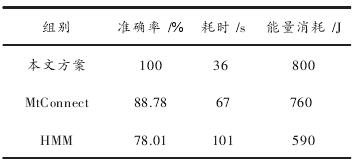
表 2 中,数控机床系统中的能量消耗定义为:

式中:s 为制造资源个数;j 为单位制造所需的能量消耗。分析表 2 可知,本文方案在准确性上优于 Mt Connect 方案 12%,优于 HMM 方案 28.1%;制造用时低于两种常用方案 50%;能量消耗上低于 Mt Connect 方案 5%,低 于HMM 方案 35.6%。因此能够证明本数控机床自动化生产系统的优越性。
4 、结语
本文首先建立基于粒度结构的数控机床信息资源自动化检测方案。通过对元数据的分析建立数控机床的结构模型,剔除冗余信息并建立完整的自动化检测系统。同时在此基础上,建立硬件与控制相独立的 PLC 自动控制系统。通过硬件配置 XML 的方案,将控制程序与嵌入式硬件分离,提高调用复用效率。经实验证明,本数控机床自动化生产系统的可行性较高,相比于两种常用方法具有耗时少、耗能低且准确性高的特点。
投稿箱:
如果您有机床行业、企业相关新闻稿件发表,或进行资讯合作,欢迎联系本网编辑部, 邮箱:skjcsc@vip.sina.com
如果您有机床行业、企业相关新闻稿件发表,或进行资讯合作,欢迎联系本网编辑部, 邮箱:skjcsc@vip.sina.com