数控机床进给轴位置精度的测量与优化
2021-3-8 来源: 武警海警学院机电管理系 作者:杨少兵 陈忠维
摘要 数控机床进给轴位置精度对加工精度具有重要影响。通过使用雷尼绍XL-80型激光干涉仪测量某型数控车床X、Z轴的定位误差数据,利用软件分析得到反向间隙补偿值和螺距误差补偿值,并在西门子840D sl数控系统中进行反向间隙补偿和螺距误差补偿;两进给轴误差补偿前后位置精度的实际测量结果表明,其定位精度和重复定位精度得到了显著的提高。
关键词 数控机床;进给轴位置精度;激光干涉仪;反向间隙补偿;螺距误差补偿
数控机床加工精度主要由加工刀具与工件间稳固的相对位置决定,而进给轴位置精度是刀具与工件相对位置的基本决定因素。因此,提高机床进给轴的位置精度,对提高工件的加工品质具有重要意义。机床进给轴的位置精度主要表现在滚珠丝杠反向间隙、直线运动轴定位精度及重复定位精度 3 个方面。在机床装配调试与运行管理维护过程中,通常使用数控系统软件补偿方式,以消除因零部件制造误差、装配误差、运行磨损等引起的进给轴直线运动位置误差,如反向间隙、螺距误差等,进而提高进给轴的位置精度。
本文以某型配备西门子 SIMUMERIK840D sl 系统的机床为研究对象,其数控系统配备PCU 50.5-C控制单元、NCU 710.2数控单元;进给轴 X 有效行程为 1100 mm,测量装置为海德汉LS187C-1340型光栅尺;Z轴有效行程为370 mm,测量装置为海德汉 LS187C-440 型光栅尺。在其精度调试过程中,使用雷尼绍 XL-80 型激光干涉仪实现对直线运动轴 X 与 运动位置精度的测
量;基于对应的运行误差数据,求得相应进给轴滚珠丝杠的反向间隙补偿值和螺距误差补偿值,并在数控系统中对反向间隙和螺距误差进行软件补偿,以实现提高X、Z轴位置精度的目的。
1 、进给轴位置误差测量
使用激光干涉仪XL-80测量系统的线性测长组件测量进给轴的位置误差,主要包括激光头、补偿器、带云台的三脚架及线性测量镜组。线性测量镜组主要由分光镜、线性反射镜及光靶组成。数据采集与分析分别使用专用的线性测长软件与数据分析软件。下面以X轴为例,介绍进给轴位置误差测量。
1.1 激光干涉仪测量准备
测量 X 轴线性位移时,主要测量组件在机床上的基本布置如图1所示。应先做好测量前的准备工作。
1)在X轴运行方向前方稳固地架设好三脚架与云台,在云台上固定好激光头,调整位姿微调旋钮,使各个方向的调整行程处于中间位置。
2)连接好激光头电源及温度、湿度传感器,打开电源开关,转动激光头光闸,使射出的激光束最细;调节三脚架位置与脚的高度,配合使用系统自带的微型水平仪,使激光头水平,且射出的激光束与X轴运行方向基本平行。
3)将 X 轴滑台移动到离激光头最近的位置,在滑台上固定好反射镜;调整磁力表座位置和高度,配合使用微型水平仪与光靶,使反射镜水平,且激光正中光靶靶心。
4)利用手轮缓慢移动滑台远离激光头,调整云台的左右角度,使光点向相反方向偏离光靶中心大致相同的距离;移动滑台靠近激光头,调整云台的左右位置,使激光束正中反射镜靶心。
5)重复过程 4),直至 X 轴移动过程中激光束始终击中反射镜靶心而不偏离,此时激光束与 X轴运行方向已完全平行;去掉光靶,旋转激光头闸至工作位置,反射光束应全部射入激光接收孔,激光头5个信号强度指示灯应至少点亮4个。
6)在激光头与反射镜之间的合适位置固定好分光镜,将分光镜分光到反射镜的一侧用光靶盖住,调整磁力表座位置与高度,使分光镜的反射光束完全射入激光头接收孔,且信号强度指示灯至少点亮4个。
7)取下分光镜分光到反射镜一侧的光靶,此时激光束应通过分光镜至反射镜,反射后光束再次回到分光镜,并与分光镜上的反射光束产生干涉,干涉光束被激光头接收,接收信号强度指示灯应至少点亮4只。测量准备工作完成。
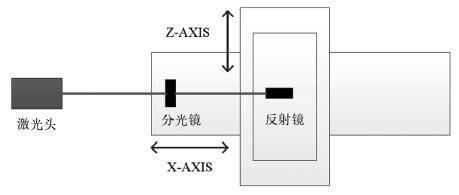
图1 测量X轴线性位移主要组件在机床上的基本布置图
1.2 数据测量
激光干涉仪安装就绪后,编写专门用于数据测量的机床运行程序,并设置好数据采集软件,运行数控程序,便可实现数据的自动采集。数据测量前,应在数控系统中将反向间隙值设置为
0,即MD32450 BACKLASH[1]=0;禁止螺距误差补偿,即32700 ENC_COMP_ENABLE[1]=0 。
1.2.1 机床进给轴测量运行程序
机床 X 轴有效行程为 1100 mm,绝对坐标位置为-450.000~+650.000,数据测量间隔为100 mm,每一行程共测量 11 个点的数据。故设置数控程序起始点为-400、终止点为600,每运行100 mm停止 4 s,等待激光干涉仪采集数据;滑台运行到两端后越程 4 mm 返回,共运行 5 次。数控程序如下:
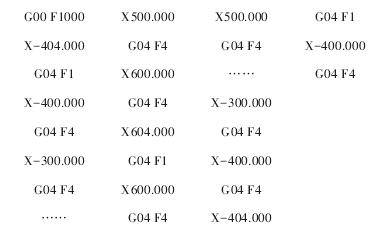
启动数控程序,当滑台从-404 mm 运行到-400 mm位置、即在第一个GOF4处时,暂停程序,待设置好数据采集软件后再开始运行。
1.2.2 线性位移数据采集与分析
启动电脑上的线性测长软件,按照提示的步骤,进行数据采集参数设置。设置第一定位点0 mm、最终定位点1000 mm,间距值100 mm,精度为小数点后3位;设置测量定位方式为线性定位,测量次数为 5 次,方向为双向;填写测量时间、地点等信息;数据采集方式、停止周期、越程大小等为缺省值。完成上述设置后,软件自动开始测量,自动采集的第一个数据为 0.000 mm
。此时启动数控程序,软件便自动在每个暂停时间段采集相应的线性位移数值,直至全部 55 个点的数据采集完毕。
打开数据分析软件,X轴线性测长误差曲线如图2所示,其中横坐标表示测量目标值、纵坐标表示实测值与目标值的差值。
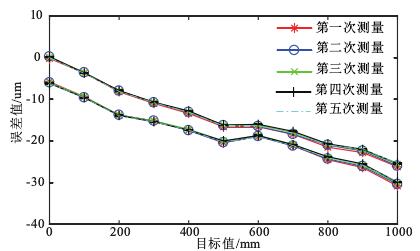
图2 X轴线性测长误差曲线
在“分析数据”菜单中选择“ISO 230-2 1997统计数表”项,用软件计算出实际的各项误差值。可以得到,X轴反向间隙为6.1 μm、重复定位精度为6.8 μm、定位精度为31.4 μm。
2 、反向间隙补偿与螺距误差补偿
根据测得的实际误差值,利用数据分析软件,得到补偿数据。在“分析数据”菜单中选择“误差补偿图表”,设置图表类型为“均值补偿”,补偿类型为“绝对值”,补偿分辨率为0.001 mm,正负符号转换为“误差值”,补偿起点为0、终点为1000 mm,间隔为 100mm。然后单击“绘制误差补偿图表”,得到轴反向间隙补偿数据为-0.0004 mm。螺距误差补偿数据如表1所示。
表1 X轴螺距误差补偿数据
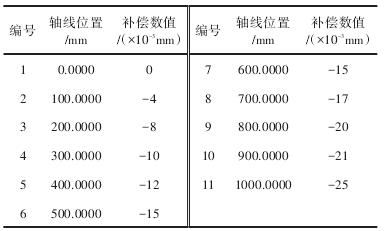
2.1 反向间隙补偿
根据上述误差数据,将反向间隙补偿值输入到数控系统中,即MD32450 BACKLASH[1]=-0.004,然后按 Reset,机床回参考点后反向间隙补偿生效。
2.2 螺距误差补偿
根据西门子 840D sl 数控系统螺距误差补偿使用说明,按如下步骤进行螺距误差补偿:
1)根据“误差补偿图表”编制补偿文件,文件名为X-BUCHANG.MPF,如表2所示。
表2 X轴误差补偿文件
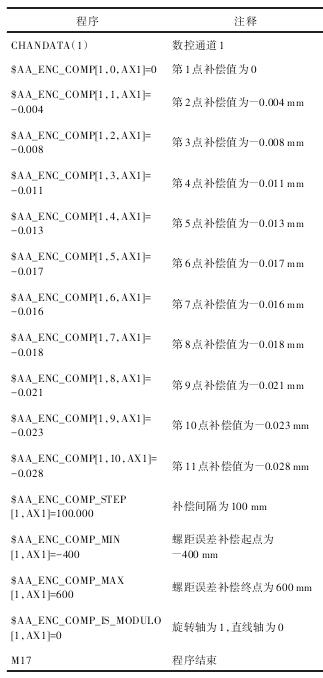
注:方括号内第 1 个“1”代表测量系统为光栅尺、第 2 个数字代表补偿点,“AX1”表示轴1,即X轴
2)计算补偿点数N:

式中:Cmax表示补偿位置坐标上限,Cmin表示补偿位置坐标下限,C 表示补偿间距。
根据 X 轴实际情况,其补偿点数 N 为 11。在数控系统中设置参数 MD38000[1]=11,方括号中的“”表示机床采用光栅尺作为测量系统。修改参数MD38000时应注意数据备份。
3)设置参数 MD32700=0,将上述螺距误差补偿文件 X-BUCHANG.MPF 拷贝到数控系统中,并执行一次;再将 MD32700 设置为 1,按复位键,机床回参考点,螺距误差补偿功能立即生。
3、 误差补偿前后进给轴位置精度对比
X 轴反向间隙补偿和螺距误差补偿生效后,使用 XL-80 激光干涉仪再次测量该轴的位置精度,其线性测长误差曲线如图3所示。
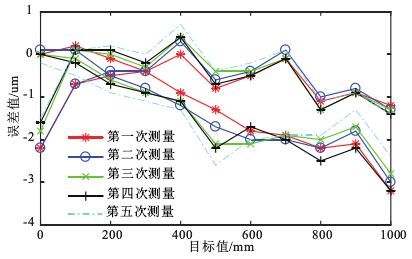
图3 X轴误差补偿后线性测长误差曲线
X 轴进行误差补偿前后,其位置精度数值如表 3 所示,定位精度提高了 598%,重复定位精度提高了106%。该机床 Z 轴有效行程范围为−330~40 mm,设置补偿初始位置为−300、终止位置为0,间距为50 mm,共补偿 7 个点。按照 X 轴补偿方法,对 Z轴进行反向间隙补偿与螺距误差补偿。如表4所示,补偿后定位精度提高了 165%,重复定位精度提高了111%
。
表3 X轴误差补偿前后位置精度对比
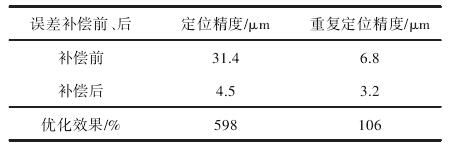
表4 Z轴误差补偿前后位置精度对比
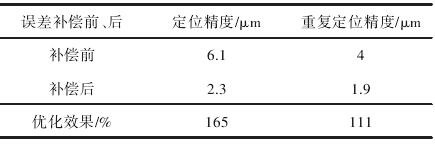
4 、结束语
在新机床的装配调试与旧机床的维护保养中,利用激光干涉仪测量进给轴的位置误差,并在数控系统中进行反向间隙补偿和螺距误差补偿,能有效地提高进给轴的位置精度。这项工作对提高加工质量、节约经费等具有重要意义。本文讲述的机床进给轴位置误差补偿方法和过程具有普遍性,不同的测量方法、不同的数控系统,均能实现软件误差补偿功能,应在机床的调试和维护中大力普及和推广。
投稿箱:
如果您有机床行业、企业相关新闻稿件发表,或进行资讯合作,欢迎联系本网编辑部, 邮箱:skjcsc@vip.sina.com
如果您有机床行业、企业相关新闻稿件发表,或进行资讯合作,欢迎联系本网编辑部, 邮箱:skjcsc@vip.sina.com