高硬度花键滚铣复合加工方法研究
2021-1-12 来源:南京高速齿轮制造有限公司 作者:束长林,王炯,王明镜,曹荣青,樊凡
摘要:某风电主齿轮箱太阳轮花键热处理后硬度较高,滚齿齿面易产生拉毛凹坑的质量问题。文中选取了某2.5 MW低速级太阳轮花键作为研究对象,设计了高精度成型铣刀,计算了工艺过程参数,并进行加工试验验证,同时对比了滚铣复合工艺与普通滚齿工艺的加工效率,为改进高硬度花键加工方法提供数据支持。
关键词:滚铣复合;太阳轮花键;切削参数
0、引言
太阳轮是变速双馈式风电齿轮箱中的关键零件之一,太阳轮在与行星轮啮合过程中产生的交变应力会对花键使用寿命产生影响,对花键齿面质量及齿形精度提出较高要求。
我公司花键热处理后材料硬度高达45 HRC,已超过普通高速钢滚刀加工范围(26.7 HRC),齿面易产生凹坑、拉毛等质量问题,刀具易出现劈齿。虽然可增加进刀次数,但存在刀具磨损快、加工效率低的弊端,因此亟需一种新的花键加工方式以提高硬齿面花键齿面质量和加工效率。
本文选取某2.5 MW低速级太阳轮花键作为试验对象,设计了高精度成型铣刀,分析并确定了滚铣复合工艺过程参数,并进行加工试验验证,同时对比了滚铣复合工艺与普通滚齿工艺的加工效率。
1、高硬度花键加工过程设计
1.1、高硬度花键铣刀设计
目前我公司已采用滚铣复合加工方式用于大模数行星轮和太阳轮热处理前加工,因热处理前材料软,铣齿时采用通用的直线刀盘开槽,滚齿余量较大且不均匀。热处理后花键相比热处理前齿轮精度要求更高,需设计匹配花键齿形的成型铣刀进行滚铣复合加工试验。
用成形原理加工齿轮的刀具,其齿形或齿形的运动轨迹都符合齿轮齿槽的形状。本次选取的试验太阳轮花键螺旋角为0°,因此可直接将齿轮齿形作为刀具的齿形。
已知被加工齿轮的参数:模数m,齿数z,分度圆压力角α,变位系数x,齿顶圆半径ra,齿根圆半径rf,分度圆齿槽宽W。常采用直角坐标法计算齿形:取齿轮中心O为坐标原点,齿槽对称线为Y轴(如图1);取渐开线上任意点M,其半径为ry;设半径线OM与Y轴的夹角为ηy(任意半径齿槽中心半角),则M点的坐标为:
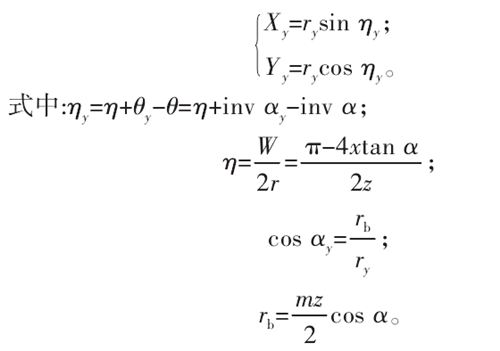
计算时采用的最小ry值应略小于齿轮的有效工作部
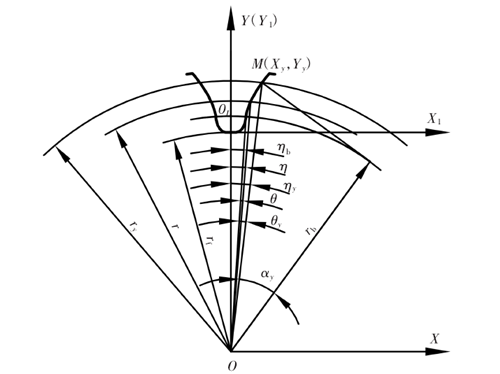
图1:齿形计算图
分起始点的向径(当rb>rf时取rb,当rb<rf时取rf);ry最大值应比齿轮顶圆半径ra大2~10 mm。将ry从rmin至rmax均匀取值代入上式,就可以计算出齿形上各点的坐标。
根据上述原理,利用计算机程序,绘制出齿槽图即铣刀齿形图(如图3),选取点标注尺寸。
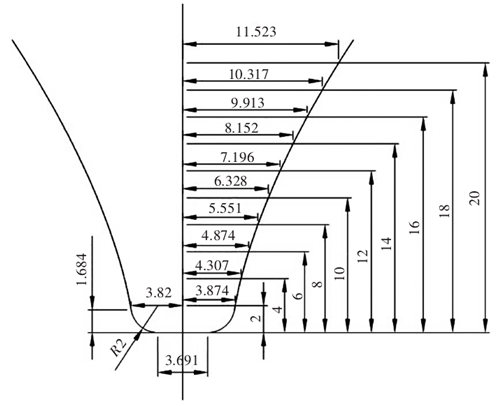
图2:铣刀齿形图
最后设计铣刀盘内外径尺寸:根据滚刀内孔直径设计内径尺寸,方便安装;根据铣刀盘齿数、滚刀外径尺寸和机床结构等因素来确定外径尺寸。
1.2、刀具安装间距确定
表1:刀具与零件参数
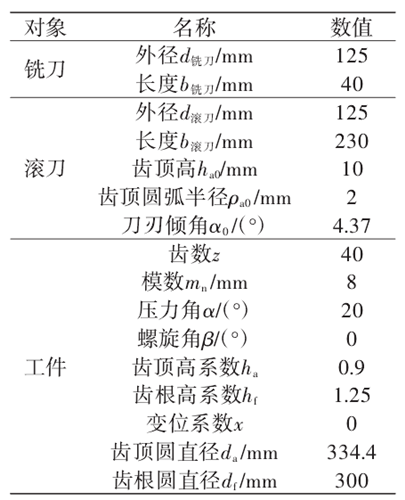
工件加工时,先铣削去除大部分材料,再采用滚削使工件达到精度要求。因此滚刀和铣刀需要同时安装在机床头架上,为避免一把刀具切削时,另一把刀具与工件干涉,需要先计算两把刀具的安装间距,刀具和零件参数如表1所示,计算示意图如图3所示。
1)铣削时滚刀安装 距 离 计算。铣齿加工时,理论上铣刀盘中心线与零件中心线重合,铣刀齿顶到达极限位置——齿轮齿根圆。由于滚刀和铣刀外径一样大,此时滚刀与铣刀的间隙距离
代入齿轮参数计算得出,滚刀最小安装间距为53.864 mm。
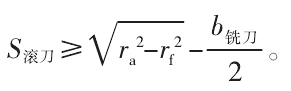
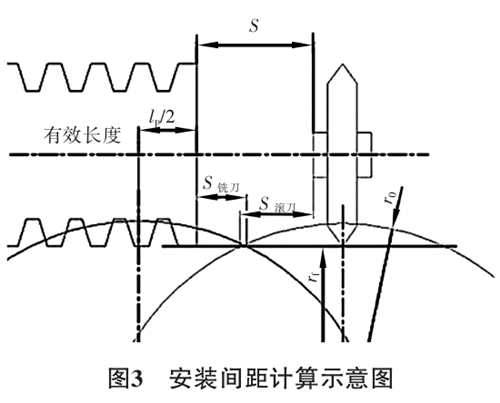
2)滚削时铣刀安装间距计算。如果把滚刀切齿过程近似地视为齿条与齿轮的啮合过程,在滚刀的切入端,在啮合长度lp0以外的滚刀刀齿虽不参加包络齿廓的工作,但却从齿轮毛坯的齿槽中切除金属,如图3所示。这部分必须有足够的长度,否则将使开始切入的刀齿负荷过重。因此,滚刀长度除了应包括包络齿形所需要的长度外,还应包括开始切除金属所必须的轮廓形成长度。由图4可见,轮廓形成长度大于啮合长度,因此计算安装长度时,应以啮合长度计算。
根据齿轮啮合中齿顶lpa位置或齿根 lpf位置中较大的间距,计算出啮合长度。图5(a)表示齿顶lpa<齿根lpf,图5(b)表示齿顶lpa>齿根lpf,并将其从滚刀法面转换到滚刀轴线平面。
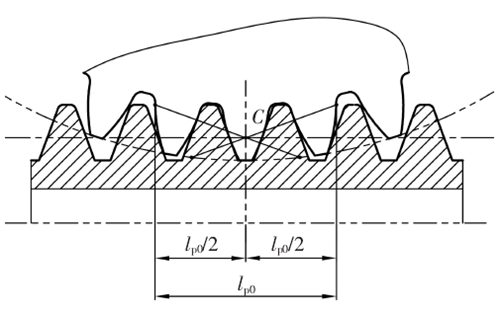
图4:齿轮滚刀的啮合长度
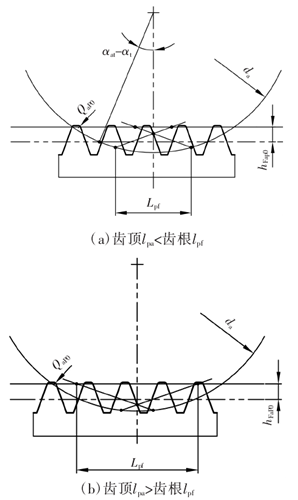
图5:齿轮啮合中齿顶位置或齿根位置
表2:齿轮滚刀的啮合长度计算步骤
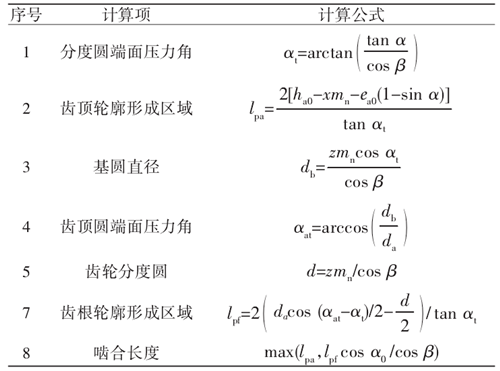
计算结果如表3所示。
滚齿加工时,为防止边齿包络不出完整齿形,滚刀窜刀πmn/2的距离,滚刀偏移πmn/2+lp0/2与零件中心线重合,滚刀齿顶到达极限位置—齿轮齿根圆,此时铣刀与滚刀间隙距离S铣刀≥
代入齿轮参数计算,得出铣刀最小安装间距为37.5 mm。
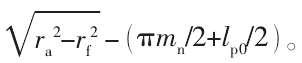
表3:齿轮滚刀的啮合长度计算结果 mm
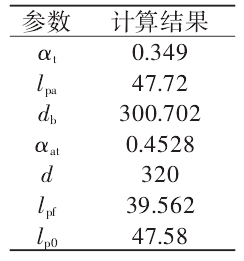
3)安全安装间距。最小安装间距取max(S滚刀,S铣刀),并考虑到头架全长375 mm,滚刀+铣刀长度=270 mm,选取安全安装间距S=80 mm。
2、花键滚铣复合试验分析
2.1、铣削能力和铣削精度验证
为检验铣削的对中情况,给滚齿预留余量,同时检查铣刀盘的制造精度,根据刀具性能设计铣削试验参数如下:线速度v=100 m/min,轴向进给速度f=300 mm/min,进刀深度ap=15 mm。
根据计量报告中左右齿面斜率偏差,计算并调整铣刀相对零件中心位置,一般通过在机床程序中调整刀盘Y轴位置来进行补偿。
2.2、铣削深度的确定
根据计量报告,结合滚刀对中误差,需要给滚齿留公法线0.9 mm的安全余量。因此滚削深度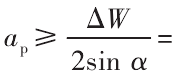
即不小于1.316 mm。
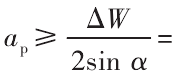
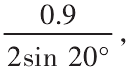
通过花键齿根圆和齿顶圆计算出全齿高17.2 mm,因此得到铣削最大深度为15.88 mm。结合参数输入习惯和公法线进刀原则,确定铣削深度15.5 mm。
2.3、确定滚齿参数
根据工件材料和刀具材料,结合最大切屑厚度和最大切削力的经验公式计算,得出理论滚齿参数:线速度为40 m/min,轴向进给为0.6 mm/r。采用该参数加工,齿面光亮,无积屑瘤、凹坑、拉毛等缺陷。
2.4、滚铣复合与硬滚加工效率对比
普通滚齿和滚铣复合工艺加工参数和工时对比如表4所示。普通滚齿工艺的总切削时间为385 min,滚铣复合工艺的总切削时间为157 min,采用滚铣复合工艺可提升加工效率约60%。
表4:滚铣复合工艺参数对比
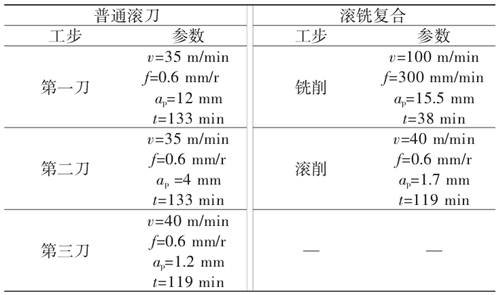
3、结语
本文针对热后花键硬度高,普通硬滚加工易产生齿面凹坑、拉毛等质量问题,通过改进加工方式,设计成型铣刀和滚铣复合工艺参数进行试验验证,研究结果如下:
1) 滚铣复合加工工艺可显著解决高硬度花键齿面凹坑、拉毛和滚刀崩刃等质量问题;
2)采用滚铣复合加工工艺,高硬度花键加工效率可提升1倍以上。
受高速钢滚刀切削速度和进给量的限制,铣齿后的滚削效率仍然较低,刀具磨损较快。因此,后续可选用硬质合金滚刀,进一步提高加工效率,稳定零件加工质量。
投稿箱:
如果您有机床行业、企业相关新闻稿件发表,或进行资讯合作,欢迎联系本网编辑部, 邮箱:skjcsc@vip.sina.com
如果您有机床行业、企业相关新闻稿件发表,或进行资讯合作,欢迎联系本网编辑部, 邮箱:skjcsc@vip.sina.com
更多相关信息