高精密复杂斜轴承孔加工工艺研究
2020-10-11 来源:中国航发南方工业有限公司 作者:何晋,刘博逵,李钰,胡志星
摘要:分析了一种复杂钛合金机匣精密斜轴承孔的加工难点,确定了大长径比刀具一次装夹加工的方案,并从切削策略、参数优化以及采用高精度减振镗刀、重金属刀杆铣刀等减振刀具加工两方面进行工艺试验探究,进一步减小切削振颤,提高轴承孔的加工质量。
关键词:精密;斜轴承孔;减振镗刀;重金属刀杆;切削振颤
0 引言
某复杂钛合金机匣是一种新型航空发动机上的重要承力部件。机匣内腔复杂大支板两端的精密斜轴承孔,主要功能是安装轴承,支撑锥齿轮轴组件旋转传递扭矩,是该零件精度最高、加工难度最大的部位,它的加工精度高低直接关系到整台航空发动机的质量。
该机匣为大型整体铸造钛合金机匣(图 1),具有尺寸大,壁薄易变形,结构复杂等特点。零件材料为铸造钛合金 ZTC4,具有较优良的高温强度和硬度,是典型的难加工材料,主要表现为:加工时刀、屑接触面积小、应力大,温度高,刀具粘结磨损、扩散磨损严重[1]。两处精密斜轴承孔尺寸精度、形位要求及表面质量要求极高,直径公差 0.015,圆柱度 0.005,同轴度 0.01,垂直度 0.01,表面粗糙度 Ra0.4 ~ 0.8(图2)。为了保证轴承孔加工质量,必须满足以下加工条件:零件装夹刚度好,机床定位精度高,刀具切削刚性好,最好能够采用磨削或精密高速车削加工。但两
处轴承孔处于复杂狭窄异型支板腔内,轴线与基准平面成 18°夹角(图 2),受零件结构限制,无法进行磨削和车削,轴承孔加工精度不易保证。本文针对该机匣精密斜轴承孔复杂的结构形式,分析制定了角度头五轴加工、大长径比刀具一次装夹加工的方案开展试验研究,系统性的阐述了一种复杂精密斜轴承孔的加工方法。
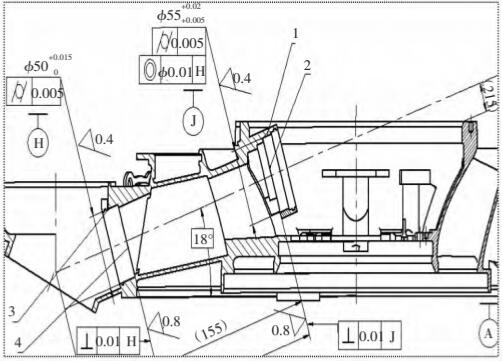
1.30# 轴承孔 2.30# 轴承孔内端面 3.29# 轴承孔 4.29# 轴承孔内端面
图 1 某钛合金机匣
1 、确定加工方案
通常航空发动机机匣上的轴承孔平行或垂直于机匣安装面,结构较为简单,不存在刀具柄部干涉问题,可采用精密卧式或立式加工中心加工,工件系统具有良好的切削刚性。而本文所述的机匣精密斜轴承孔为一种新型的轴承孔结构形式,轴线与基准平面成 18°夹角并处于复杂狭窄异型支板腔内,不适宜采用一般的轴承孔加工方法,需进一步分析研究加工方案。
两处斜轴承孔分别与某锥齿轮轴两端的 29# 轴承外环、30# 轴承外环配合,其中 29# 轴承孔(图 2)可采用一般五轴加工中心加工,刀具悬伸长度较短,具有较好的加工刚性,加工难度较低。30# 轴承孔轴线与机匣端面最小间距为 21.5 mm(图 2),若采用一般五轴机床加工,刀杆直径应小于 Φ40 mm 以避开端面干涉,同时悬伸长度接近 310 mm,刀杆长径比大于 7mm,加工振动大,同类长径比镗刀主要用于加工铝镁零件。综合考虑精密轴承孔加工的经济性和可行性,结合生产实际,拟定了角度头五轴加工和大长径比刀具五轴一次装夹加工两种方案分别进行试验研究。
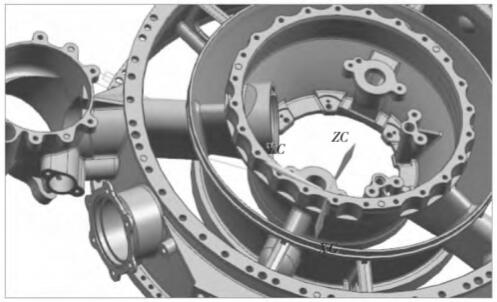
图 2 机匣精密斜轴承孔示意图
1.1 角度头五轴加工
角度头是数控加工中连接数控机床主轴和刀具的一种特殊刀柄,可以实现复杂结构件的一次性装夹多工序加工[2,3]。数控机床安装角度头后刀具旋转中心线与主轴中心线成角度加工工件,可以实现机床的立卧转换和任意角度的变换,增大机床的加工范围和适应性[4,5]。30# 轴承孔处于机匣狭窄内腔,首先考虑采用配置角度头的五轴加工中心加工(如图3),它的优势在于可以有效避让机匣狭窄内腔的结构干涉,不用定制价格高昂的加长刀具,降低了加工成本,且加工时刀具悬长较短,理论上应具有良好的加工刚性。
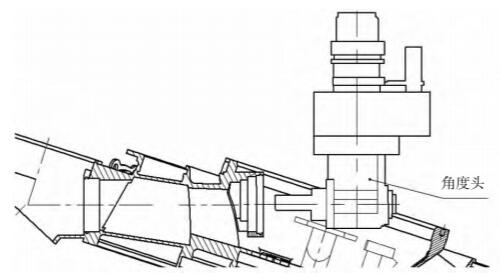
图 3 角度头加工示意图
但是经过试验分析,发现采用角度头加工存在以下问题:
(1)由于机匣内腔狭窄,且有多处凸台干涉,只能选取较小规格的角度头加工,但小型角度头刚性较差,容易振刀,不适宜加工精密孔。
(2)角度头加工精度不是很高,除了考虑零件装夹找正误差、机床工作台或主轴重复定位误差等因素,还需要考虑角度头的定位误差,多重误差累积,导致加工精度下降。
(3)该角度头一般安装在立式五轴加工中心上,采用角度头加工完 30# 轴承孔后,一般的五轴加工中心不能实现在一次装夹的情况下完成 29# 轴承孔的加工,必须掉头重新装夹或更换加工设备,重复装夹找正误差大,不利于保证两轴承孔的同轴度要求。
1.2 大长径比刀具五轴一次装夹加工
1.2.1 加工前准备
为了实现 29# 轴承孔、30# 轴承孔一次装夹加工,必须选用各坐标轴(X、Y、Z、A 轴)行程足够大的精密卧式五轴加工中心。专用夹具应垫高确保加工29# 轴承孔时机床刀座不触碰工作台。并且为了最大程度提高零件装夹系统刚性,减小切削振颤,对机匣环腔进行了灌蜡处理。另外,由于加工轴承孔时刀具避开干涉后悬伸长度较大,铣削加工径向切削力大,加工振刀严重,采用镗削加工会更有利于保证轴承孔的位置精度。经过招标比质比价,选用了一款长径比较大的进口标准镗刀(图 4)进行一次装夹镗削加工试验。
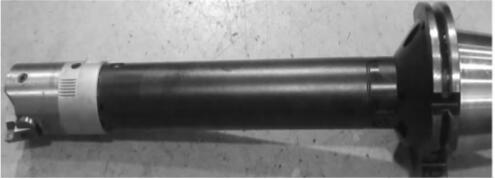
图 4 进口标准镗刀
1.2.2 加工步骤
(1)粗镗去余量:首先采用双刃镗削刀具粗加工轴承孔。双刃镗刀刚性较好,双刃切削金属去除率较高,在大长径比刀具的大余量切削加工中,双刃镗刀切削稳定性和效率明显优于单刃镗刀,粗加工后孔壁与内端面单边留余量约 0.1 mm 用于精加工。
(2)精加工轴承孔内端面:轴承孔内端面为精密配合面,精度要求很高,内端面与孔垂直度要求0.01,表面粗糙度 Ra0.8(图 2)。精加工时若采用镗刀一次加工轴承孔孔壁与内端面,由于镗刀片角度一般略小于 90°,不能满足端面垂直度要求,同时该端面径向宽度约 4 mm,加工时刀具切削刃接触面大,易振动,即使制造 90°非标镗刀片也无法保证加工精度。由此采用加长三面刃铣刀铣削轴承孔内端面,采用该方案加工,内端面与孔垂直度 0.01 基本可以满足要求,但 30# 轴承孔内端面上存在轻微振纹,表面质量略有不足。
(3)精镗轴承孔:采用加长单刃精镗刀精加工轴承孔(图 4)。单刃镗刀仅一个切削刃绕中心旋转切削,切削刃与零件所有触点处于至中心等距的旋转圆周上,加工一致性好,有利于提高轴承孔尺寸精度和形位精度,而双刃镗刀两刃高度存在细微差异,在进行小切深的精密加工时切削稳定性不如单刃镗刀。通过调试优化加工参数,基本可以保证轴承孔直径尺寸及其同轴度、轮廓度要求,但 30# 轴承孔孔壁表面存在轻微振纹,表面质量略有不足。另外,两处轴承孔由于结构限制,加工时所采用的镗刀、三面刃型铣刀在进刀和退刀时,均须抬刀绕行或主轴定向进刀以避开干涉。
1.3 方案对比
通过对以上两种加工方案进行分析对比,发现采用配置角度头的设备加工,虽然刀具成本较低,但是角度头加工精度不足,刚性差,加工振动大,轴承孔的同轴度、轮廓度等各项技术要求均无法满足,受限于角度头的结构特点,该方案能改进优化的空间很小。而大长径比刀具五轴一次装夹加工的方案基本可以满足轴承孔各项技术要求,可行性很高。但是此方案仍有不足,必须进行一系列工艺试验,解决加工振颤的不良因素,进一步提高轴承孔加工质量。
2 、轴承孔五轴加工工艺优化试验探究
轴承孔五轴加工工艺优化试验主要从切削策略、参数优化及减振刀具加工两方面进行了分析研究,旨在解决加工振颤,提高轴承孔加工质量。其中,29# 轴承孔加工时刀具悬伸长度不大,采用上述方案即可保证相应技术要求,后文仅针对 30# 轴承孔进行工艺优化试验研究。
2.1 切削策略、参数优化
2.1.1 轴承孔内端面铣削策略、参数优化
采用加长三面刃铣刀精加工轴承孔内端面时,对切削策略和参数进行了优化:
(1)采用小切深铣削法,尽量降低切削力,避免切削振动,粗加工后端面余量仅预留 0.1 mm 进行精铣。
(2)选用三角形刀片加工,三角形刀片仅刃尖进行切削,刃尖非常锋利,切削力小。
(3)刀具铣削轨迹外形直径应略小于孔壁直径,刀刃不触碰孔壁,以免端面与孔壁同时切削使切削抗力增大产生振刀,影响加工精度。
(4)直径方向不能进行分层铣削,防止出现接刀纹影响表面质量。
由于轴承孔内端面铣削主要产生径向切削力,普通加长铣刀刚性较差,优化切削策略后加工表面依然有轻微振纹,调试切削参数加工后表面质量虽有一定改善,但仍无法完全解决这个问题。
2.1.2 轴承孔精镗参数优化
在精镗 30# 轴承孔时,采用加长标准精镗刀,刀具长径比大,加工振动较大,孔壁表面存在轻微振纹,通过对刀具转速、进给、切深等切削参数进行了一系列的试验优化(见表 1),轴承孔加工质量取得了显著改善。
表 1 30# 轴承孔精加工切削参数调试记录表
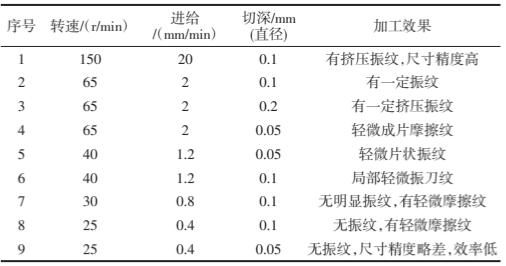
由表 1 可以看出,只有采用低转速、低进给,才能减少或消除加工表面的振刀纹,提高轴承孔表面质量;切深对表面质量影响不太大,切深较小时,表面质量稍好。其中,转速是对加工振动影响最大的因素,转速越高,刀具径向切削力越大,加工振动越大。通过对比试验效果,最终选定切削参数为:转速 25r/min,进给 0.4 mm/min,切深 0.05 mm,轴承孔表面加工质量基本满足设计图要求。
同时试验发现,当进给太小时,轴承孔垂直度、圆柱度等技术要求不稳定。分析认为,当转速一定时,随着刀具进给增大,单位时间内刀具轴向切削深度相应增大,主轴轴向切削力增大,制约刀具径向摆动的摩擦阻力增加,刀具切削振颤幅度反而减小,轴承孔形位精度提高。
通过调试优化加工参数,轴承孔内端面仍存在轻微振纹,孔壁表面质量基本达到设计要求,但轴承孔圆柱度、垂直度等要求不稳定。因此,需要进一步试验,采取措施提升刀具刚度,减小切削振颤,保证轴承孔所有技术要求和表面质量。
2.2 减振刀具加工
2.2.1 重金属合金转接杆铣刀精铣轴承孔内端面
加工 30# 轴承孔内端面时,刀具长径比大,铣刀若安装一般转接杆,加工时振刀严重,即使对切削策略和参数进行了试验优化,也无法完全消除切削振颤,因此选用了一种重金属合金转接杆的三面刃铣刀进行加工,该刀具刚性更强,切削振颤小,有效避免了切削振纹的产生,即使在进行大悬伸加工时,也可以保证加工的稳定性,零件表面质量较好,垂直度要求合格。见图 5。
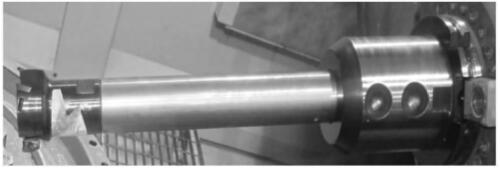
图 5 重合金转接杆三面刃铣刀
2.2.2 高精度减振镗刀加工轴承孔
通过试验分析,采用大长径比刀具五轴一次装夹镗削加工两轴承孔的方案具有较高可行性。但目前采用一般镗刀精加工轴承孔,切削参数在经过大量调试优化后,轴承孔的表面质量、圆柱度、垂直度仍不能同时达到最理想的要求。由于在深孔和高速的加工过程中,镗杆简化为细长悬臂梁结构,特别是大长径比镗杆,因为镗杆的悬伸过长引起刚度不足,使镗杆容易产生振动,影响加工精度[6]。通常情况下,镗削过程中的一般镗杆,在长径比(L/D)大于 4 时,比较容易产生振动,这是由于镗杆刚度不够导致的,并且长径比越大,振动幅度愈大,当镗杆长径比为 10时,机械加工过程中所产生的变形量,是长径比达到4 时的 16 倍[7]。加工 30# 精密轴承孔的镗杆长径比约为 7,同时钛合金材料具有较优良的高温强度和硬度,是典型的难加工材料,切削性能差,切削抗力大,进一步加剧了镗削过程中的刀具振动,零件形位要求和表面质量难以保证。因此必须考虑使用具有减振功能的刀具,通过引进多家国外刀具品牌的减振镗刀技术方案,经过对比分析,选用了山特维克一款高精度减振镗刀(图 6)对轴承孔进行加工试验。
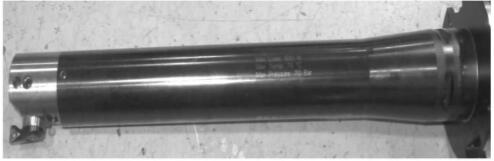
图 6 减振镗刀加工轴承孔示意图
减振镗刀主要通过阻尼减振的方式,提高刀杆的动刚度,减小刀具径向跳动量,从而提高轴承孔表面加工质量。试验过程中,综合考虑零件材料的切削性能、加工技术要求、刀具本身的减振效果、刀具寿命、让刀等因素,对减振镗刀切削参数进行了调试优化。
(1)切削深度:一般来说,切削深度应略大于刀尖圆角,加工时尺寸更稳定,以免在刀片圆角上切削时,切削部位主、副偏角不稳定,对让刀量大小产生影响,从而导致尺寸加工不稳定。但由此选用的切削深度相对较大,在进行精加工时,切削深度过大,切削阻力增加,让刀量增加,不利于保证尺寸精度,一般精加工切深选择 0.1 ~ 0.2 mm。同时减振镗刀是弹性结构,刀杆静态刚性不佳,切削让刀现象更为突显,切深 0.2 mm 时,让刀量约为 0.03 ~ 0.04 mm;切深 0.1 mm 时,让刀量约为 0.01 ~ 0.02 mm。因此,为了更好的保证尺寸精度,进刀时应根据切深适当补偿让刀量,经过试验摸索,给定切深为 0.1 mm,并预留约 0.02 ~ 0.03 mm 余量,加工后测量孔径计算实际余量,补偿刀具加工至最终尺寸,刀补值等于实际余量减去上一次切削时的让刀量,避免因上一次切削让刀回弹导致尺寸超差,切深 0.1 mm 时刀具让刀略大于 0.01 mm,同时最后精修时也会产生轻微让刀,根据实际经验,最终刀补值为实际余量减去 0.01mm 让刀量即可保证孔径尺寸要求。
(2)线速度:线速度是影响减振镗刀加工振动的最重要因素,线速度过大或过小,均可能引起切削振颤,根据山特维克多年的减振镗刀加工经验和试验摸索,切削钛合金材料线速度一般选用 40 ~ 80 m/min最佳,结合零件材料 ZTC4 的切削性能,经调试,最终给定线速度为 50 m/min,采用这一切削参数无加工振颤现象(图 7)。
(3)每转进给 f:根据表面粗糙度计算公式Ra = f 2 × 1000/(R × 8),在保证粗糙度要求 0.4 的前提下可计算求得 f 值,从公式中可以看出,粗糙度与每转进给成正比,与刀尖圆角成反比,在精密尺寸的实际加工中,为了减小切削力,提高切削稳定性,需尽可能保证刀片的锋利度,由此选用 R0.2 精车刀片,通过上述公式计算可得:f =(Ra × R × 8/1000)1/2 =(0.4 × 10-6 × 0.2 ×8/1000)1/2 = 0.025 3 × 10-3m为了保证粗糙度合格,选择的每转进给 f 应不大于 0.025 3 mm,但是切削时若进给量太小,会加速刀具涂层磨损速度,降低刀具寿命,影响尺寸加工精度,因此,最终给定每转进给 f 为 0.025 mm;采用这一切削参数加工,轴承孔表面质量可以达到理想效果(图 7)。
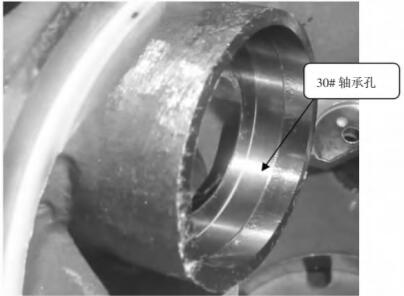
图 7 减振镗刀加工的轴承孔
采用大长径比高精度减振刀具在大行程卧式五轴加工中心一次装夹加工机匣两精密斜轴承孔,由于减小甚至基本消除了加工振动,切削稳定性好,相对于采用一般加长标准镗刀加工,轴承孔表面质量及其同轴度、垂直度等形位要求也有极大提高,轴承孔加工精度和表面质量基本满足了设计要求。
3、 结束语
通过对一种复杂精密斜轴承孔进行加工试验分析,确定了采用大长径比减振刀具在大行程卧式五轴加工中心一次装夹加工的工艺方案,两轴承孔加工精度基本满足了设计要求。采用上述方案加工的机匣轴承孔,锥齿轮轴装配效果良好,顺利通过了300 h 长期试车考核,未发生锥齿轮轴裂纹等现象。
投稿箱:
如果您有机床行业、企业相关新闻稿件发表,或进行资讯合作,欢迎联系本网编辑部, 邮箱:skjcsc@vip.sina.com
如果您有机床行业、企业相关新闻稿件发表,或进行资讯合作,欢迎联系本网编辑部, 邮箱:skjcsc@vip.sina.com
更多相关信息