高速切削铝合金用硬质合金刀具磨损机理研究
2020-3-31 来源:- 作者:李小龙 周燕 刘江 高军
摘要:在高速切削加工铝合金涡轮过程中,硬质合金刀具的磨损会直接影响刀具的使用寿命和加工精度,导致加工精度无法满足设计要求,在磨损严重时还会引起刀具和零件的损伤。本文以高效切削铝合金涡轮用硬质合金刀具为研究对象,通过四因素三水平正交试验对刀具磨损行为进行研究,观测和分析不同切削参数下硬质合金刀具的磨损状态及微观形貌,讨论并提出有效控制刀具磨损的措施。结果表明,该控制刀具磨损的措施在保证零件加工精度的同时具有一定的实际推广价值。
关键词 : 硬质合金;刀具;磨损;高速切削;铝合金
刀具是影响高速切削铝合金材料的一个关键性因素,目前在高速切削加工铝合金用刀具方面主要存在以下几个问题:(1)对于高速切削铝合金材料时刀具的磨损破损规律研究较少,在实际生产中对换刀没有统一的企业标准,往往根据工作人员的操作经验换刀,换刀过早或过晚易导致刀具浪费或零件超差[1]。(2)切削加工工艺差造成刀具过早失效。机械加工工艺对高速切削状态下的刀具失效具有十分重要的影响,加工现场对该类型机械加工工艺的研究和经验积累不多,面对种类繁多的高速切削生产状况,基本依靠工人的实际加工经验。实际加工过程中,刀具切削速度和主轴转速很容易落到共振区中,从而造成刀具的振动和冲击,加速了刀具的失效。防止刀具过早失效的重要措施是提高高速切削加工过程中的稳定性[2]。但是,企业生产现场对如何确定产生共振的不稳定区域没有有效办法。(3)工件成本高,损坏将造成巨大浪费[2]。铝合金工件成本价格昂贵,某些零件在加工过程中为消除残余内应力,还要经过去应力回火的热处理工序。大型箱体结构零件的铝合金材料毛坯体积大、铸造成本高,加工过程中刀具的快速磨损和破损极易造成尺寸超差或零件报废,给加工人员造成较大压力[3]。 为解决上述问题,张光明等[4]研究了铝合金高速切削速度对硬质合金刀具磨损的影响,郭新等[5]对铝合金薄壁中空结构件重负荷铣削刀具寿命及刀具磨损行为进行了分析,王敬春和冯明军[6]对球头铣刀精铣铝合金叶片的磨损行为进行了试验与研究,李亚平等[7]针对 211Z 铝合金铣削表面粗糙度进行了实验测试与理论分析。本文以高效切削铝合金涡轮用硬质合金刀具为研究对象,通过四因素三水平正交试验对刀具磨损行为进行研究,观测和分析不同切削参数下硬质合金刀具的磨损状态及微观形貌,讨论并提出有效控制刀具磨损的措施。
1、实验材料及方法
实验是在 BCH850 三轴高速铣床上进行的,刀具为机夹式立铣刀 , 刀片分别为 NASKA APKT113504PDFR-G2 刀片和 SANDVIK R390-11 T3 08E-NL H13A 刀片,刀具直径为 ϕ20 mm(NASKA 刀片)和 ϕ25 mm(SANDVIK 刀片)。工件材料为铝合金 7055,加工方式为单向顺铣,干切。切削实验仪器及刀具如图 1 所示。
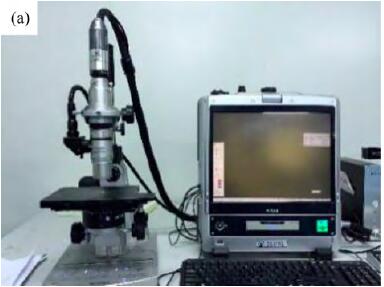
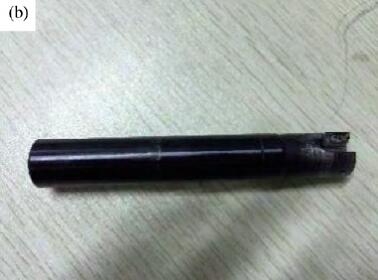
图 1 实验设备及刀具:(a)VH-8000 数字光学显微镜;(b)机夹式立铣刀
为了减少实验次数,同时不降低各实验数据预测的准确性和信息量,采用正交实验方法,设计四因素三水平 9 组实验[8],实验参数和因素水平如表 1和表 2 所示。
2、结果与讨论
2.1 切削参数对刀具磨损的影响
根据表 1 和表 2 正交实验数据可得直观分析表 3。分析表 3 可得切削 30 min 时切削参数对刀具后刀面磨损量(VB)的影响趋势,按照极差大小,对刀具后刀面磨损影响最大的切削参数是每齿进给量(0.045),其次是切削速度(0.033),然后是径向切宽(0.027),最后是轴向切深(0.018)。
表 1 NASKA 刀片正交实验参数与因素水平

表 2 SANDVIK 刀片正交实验因素与水平

表 3 NASKA 刀片正交实验结果分析

注:∑T 表示的是切削参数对刀具后刀面磨损量影响程度的总和,均值表示的是切削参数对刀具后刀面磨损量影响程度的平均值,极差表示的是切削参数对刀具后刀面磨损量的影响程度。
极差数据显示每齿进给量(fz)对刀具后刀面的磨损量影响最大,同时每齿进给量(fz)还对刀具破损有着十分重要的影响。图 2 所示为不同切削参数下 NASKA 刀片崩刃现象。由图 2 可以看出,当 fz为 0.3 mm 时发生了崩刃现象。由实验结果可以看出,每齿进给量(fz)对刀具破损有着显著的影响,随着每齿进给量(fz)的增大,刀具破损明显增多[9]。
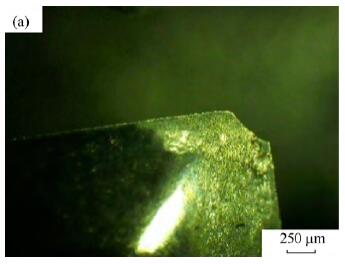
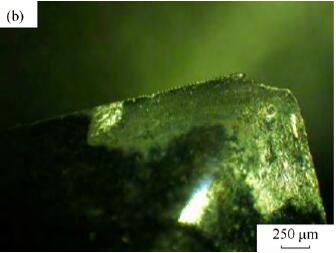
图 2 不同切削参数下 NASKA 刀片崩刃现象:(a)fz = 0.3 mm,ap = 1 mm,ae = 11 mm,Vc = 942 m/min;(b)fz = 0.3 mm,ap = 2 mm,ae = 7 mm,Vc = 471 m/min
2.2 刀具磨损机理分析
2.2.1 黏结磨损
高速切削时,接触区的压力升高,使刀具和工件材料实际接触面积增加,由于两者同时沿着刀具的前、后刀面连续移动,导致刀具表面的氧化层和其它吸附膜逐渐破坏,主要体现在刀具和刚从工件材料内部切削出的新鲜表面间形成强烈的黏结[10–12]。在接触区压力下的弹塑性状态铝合金初熔温度为 488 ℃,一般来讲,在中等偏低的切削速度下容易产生黏结磨损。图 3 所示为刀面黏结磨损宏观形貌,如图可见,由于铝合金的塑性较强,在 9000 r/min 转速下高速切削时,黏结程度虽有所减轻但仍存在黏结现象[11,13]。
在自带能谱分析仪(energy disperse spectroscope,EDS)的扫描电子显微镜(scanning electron microscope,SEM)下对黏结物进行了形貌观察和成分分析,结果如图 4 所示。由图 4 可知,黏结物的主要元素是 Al,还含有少量的 Mg、Zn,这是 7075 铝合金的主要组成
成分,可以判断这些黏结物是铝合金工件材料,证明了在切削铝合金材料过程中发生了轻微的黏结磨损。
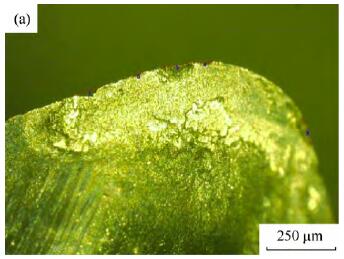
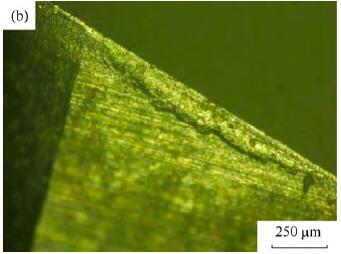
图 3 刀具(a)和后刀面(b)黏结磨损宏观形貌(fz = 0.3 mm,ap = 1 mm,Vc = 706 m/min)
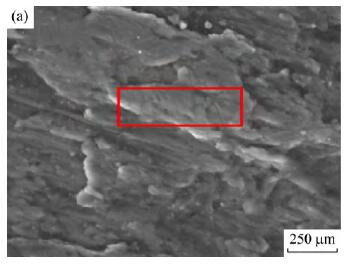
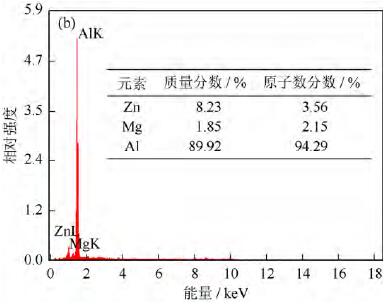
图 4 黏结物显微组织形貌及能谱分析:(a)扫描电子显微形貌;(b)能谱分析
2.2.2 扩散磨损
在自带能谱分析仪的扫描电子显微镜下对刀具刀刃破损处进行了形貌观测以及成分分析,结果如图 5 所示。由图 5 可知,磨损处成分既包括刀具材料成分(W、Co 元素),又包括铝合金工件成分(Al、Mg、Zn 元素),说明在切削过程中工件材料的化学元素很有可能扩散到刀具基体里面,使得刀具基体的成分发生了变化。
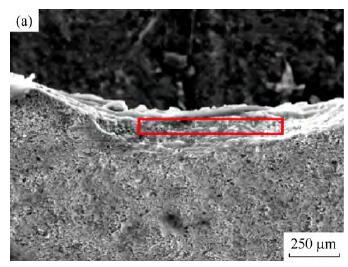
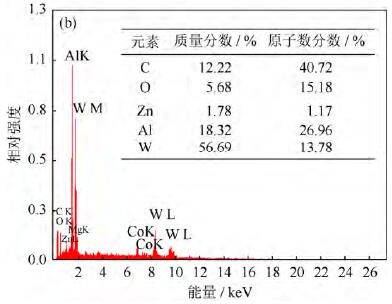
图 5 后刀面磨损处显微组织形貌及能谱分析:(a)扫描电子显微形貌;(b)能谱分析
2.3 控制刀具磨损的有效措施
根据以上典型刀具的磨损实验研究,提出以下控制刀具磨损的措施:(1)每齿进给量是影响刀具耐用度的关键因素,随着主轴箱每齿进给量的增加,刀具耐用度的改善程度将降低[12]。(2)切削速度在500~1500 m/min 对刀具耐用度的影响不明显,因此在许可条件下应尽量提高切削速度,这样可同时兼顾效率和刀具耐用度。(3)根据切削参数选用原则,建议切削参数如下:切削速度为 1000~1500 m/min,每齿进给量为 0.15~0.25 mm,在机床功率、刚度及扭矩允许的条件下尽量采用高速、小进给。采用优化后的切削参数进行切削,可保证零件加工精度,有效地控制刀具磨损量,延长刀具使用寿命[12,14–15]。
3、结论
(1)通过四因素三水平正交试验对高速切削铝合金涡轮用硬质合金刀具的磨损行为进行了实验研究,观测和分析了不同切削参数下硬质合金刀具的磨损状态及微观形貌,讨论了切削参数对刀具磨损的敏感程度,得出了刀具磨损受切削参数的影响程度:每齿进给量>切削速度>切削宽度>切削深度。
(2)高速切削铝合金材料时,刀具的主要失效机理突出体现在黏结磨损和扩散磨损,其中前刀面的黏结情况明显较后刀面严重。
(3)提出了有效控制刀具磨损的措施,建议切削参数如下:切削速度为 1000~1500 m/min,每齿进给量为 0.15~0.25 mm,在机床功率、刚度及扭矩允许的条件下尽量采用高速、小进给。该措施在保证零件加工精度的同时可有效地控制刀具磨损量,延长刀具使用寿命,具有一定的实际推广价值
来源:运城职业技术学院机电工程系 内蒙古工业大学机械学院 内蒙古第一机械制造集团有限公司
投稿箱:
如果您有机床行业、企业相关新闻稿件发表,或进行资讯合作,欢迎联系本网编辑部, 邮箱:skjcsc@vip.sina.com
如果您有机床行业、企业相关新闻稿件发表,或进行资讯合作,欢迎联系本网编辑部, 邮箱:skjcsc@vip.sina.com