有效控制薄壁铝合金细长轴加工变形的方法分析
2020-2-11 来源:天津机电职业技术学院 北华航天工业学院 作者:张文健 杨嵩
摘要: 针对薄壁铝合金细长轴零件在加工过程中容易发生变形的特点,阐述了引起加工变形的原因,并通过改变相应加工工艺等措施来控制加工变形,从而保证了工件的尺寸与形位公差以及表面粗糙度要求,关键步骤选用双顶尖装夹以及增加辅助虎钳顶夹的加工工艺,在生产实践中具有指导意义。
关键词: 细长轴; 薄壁; 铝合金; 加工变形
1、 引言
根据生产要求,需将毛坯直径 30mm、长度360mm 的 LY12CZ 铝合金加工成图 1 所示的细长轴类零件。要求细长轴两端外圆与其中心轴线的同轴度要求为 0. 05mm,中间两个凹槽底面与其轴线的垂直 度 要 求 为 0. 05mm,两端外圆尺寸精度为25. 40- 0. 1,整个工件的形状位置公差与尺寸公差要求都很高。
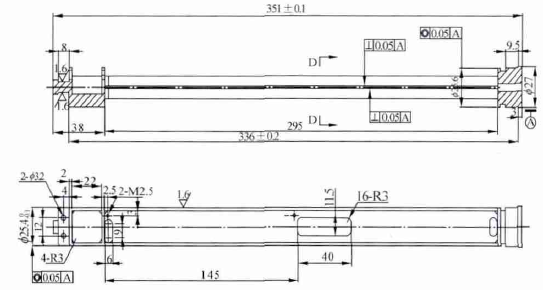
图1 零件主俯视图
图 2 为零件 D 向视图。由图可知,零件中间部分加工完成后的厚度仅剩 1. 5mm,在加工中极易出现加工振动变形,影响加工质量,严重时会使工件报废,因此,在加工过程中如何防止加工变形是首要要考虑的问题。
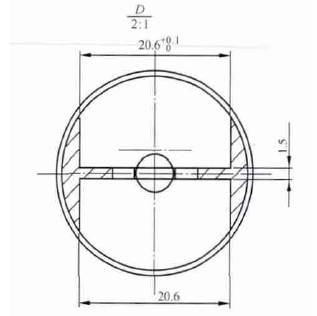
图2 零件 D 向视图
2、 改进工艺流程
2. 1 原有加工工艺分析
原有加工工艺流程: 粗、精车外圆→粗、精铣细长轴各个加工部位→钻端面孔→攻端面 M5 螺纹。按照该加工工艺加工完毕后,发现工件发生严重弯曲变形,变形量达到 3 - 5mm,变形部位发生在工件的中心位置,向铣完一端的凹槽方向弯曲,与原图形位公差要求严重不符,工件报废。
通过分析发现,造成加工弯曲变形的主要原因是粗车加工完成后直接精车,此时工件的加工变形不明显,继而进行粗铣与精铣的加工,由于粗铣加工完一端凹槽旋转 180°加工第二个凹槽时,工件中部凹槽的部分由于单方向受力不均匀,工件必然会向强度薄弱的一方( 已加工完方向) 弯曲变形,造成工件报废,出现该现象也与刀具角度、装夹方式、铝合金特性、冷却是否充足等因素有关。
2. 2 改进的加工工艺
为了有效控制加工变形,保证工件的尺寸公差与形状位置公差,需要改进加工工艺。改进的加工工艺如下:
①粗车: 两端打中心孔,通过一夹一顶的方法车端面,外圆车至 27. 3 ± 0. 1、长度 351. 5mm,需要注意的是两端中心孔( 顶尖孔) 要小;
②粗铣: 在加工中心上通过分度头一夹一顶的方法铣两侧 295 × 20. 6 两槽,各槽单边为精铣加工留 0. 3mm 余量。注意旋转 180°加工第二个凹槽时工件中部要增加辅助虎钳顶夹的装夹工艺,以保证工件的形状与位置公差要求;
③时效处理: 精车加工前,把工件重新加热到180 ± 5℃ ,保温 4 小时,然后随炉冷却,使得经过时效处理后强度与硬度显著提高,而塑性则有所下降,提高切削加工性能,为下一步精加工工序时保证加工尺寸精度与形位公差打下良好基础。
④精车: 为使工件在静止状态下也能保证形位公差,采用双顶尖方式装夹工件,精车外圆尺寸270- 0. 1到尺寸,精车两端面,保证两端面相对于轴线的垂直度要求控制在 0. 05mm 以内,右端保留中心孔,M5 暂不加工,通过开口套装夹工件外圆,找正工件外圆钻 M5 底孔,倒角 1 × 45°。
⑤精铣: 在加工中心上通过分度头一夹一顶的方法铣 295 × 20. 6 两槽到尺寸,注意控制两个凹槽底面与其轴线的垂直度要求为 0. 05mm; 同时为了避免在加工第二个凹槽时向第一个凹槽方向的加工变形,中间采用虎钳夹持的方法来保证工件的刚性,从而有效控制工件的尺寸与形位工差要求。
3 、加工工艺关键步骤
( 1) 双顶尖装夹精车细长轴外圆
由于原有加工工艺难以保证工件尺寸与形位公差要求,所以需要改变加工工艺,将精车工序放置在粗铣加工工序后,将粗铣加工完后的变形在精车工序内消除。另外,在精车加工前增加了热处理加工工艺,就会将粗车、粗铣加工造成的加工弯曲变形在时效热处理阶段进行消除,释放内应力,工件内部组织强化,强度与硬度显著提高,为精车、精铣打下良好基础。区别于粗车时一夹一顶的装夹加工工艺,在精车时采用了双顶尖装夹的加工工艺。零件在粗车、粗铣后由于受力变形会造成工件在静止状态下有一个较大的弯曲,所以在精车阶段的主要任务是将粗车、粗铣造成的加工变形控制在合格的公差范围内。采用双顶尖装夹工件时,车床顶尖是一个与车床主轴同心的圆锥,分为前顶心和后顶心。后顶心装在车床尾部,使用时将其顶在被加工件的旋转轴心上,起到稳定工件旋转轴心的作用,前顶心装在车床主轴上或用三爪自定心卡盘夹持,使用时将其顶在被加工件的旋转轴心上,起到带动工件旋转和稳定工件旋转轴心的作用。
使用双顶尖加工时,由于顶心和工件的接触面小,传动力矩短,所以不太适合用于直径较大的工件或进刀量大的场合,但由于顶心夹持时具有自动对准工件旋转轴心的作用,所以适用于需要多次重复装卸的加工工件。
刀具角度的选择也很关键,实践证明,合理的车刀角度为前角 γ0= 18°- 20°,后角 α0= 20°- 24°,主偏角 κr= 90°- 95°,副偏角 φr= 10°- 12°,刃倾角 λs= 15°- 20°。此外,采用双顶尖装夹,顶尖不能顶得太紧或太松,车削过程中需随时注意并及时调整。车削加工前,床鞍应左右移动全行程,观察有无碰撞现象。
( 2) 利用分度头在加工中心上进行精铣加工
精铣加工前要在加工中心上对分度头进行找正,确保分度头在机床上自身的位置精度。分度头找正的步骤为: ①分度头的主轴轴向在数控铣床上确保与机床工作台 X 向平行,用杠杆百分表检验验棒根部的圆跳动,使之在 0. 03mm 以内; ②检验验棒端部圆跳动,通过调整达到 0. 03mm 以内; ③检验验棒的上母线,通过切高点的方法,调整分度头是否仰头或俯头,保证分度头的轴向与数控铣床 X 向平行; ④检验验棒的侧母线,确定分度头与机床工作台X 向平行。验棒找正后,将细长轴零件装夹在分度头上,通过一夹一顶的方式进行 295 × 20. 6 两槽的精铣加工。
( 3) 利用平口钳夹持中间部位进行反向精铣加工
通过实例验证,铝合金薄壁细长轴在没有夹具顶卡的情况下加工完第一面后还勉强可以进行加工,旋转 180°后加工第二面时由于工件受力变形,刀具与工件接触处发出巨大的响声及颤动,会出现铣刀崩刃、工件撅起等严重后果,此时工件不能正常加工。因此需要改进加工工艺,采取措施为通过采用平口钳装夹薄壁细长轴零件的中间部分( 见图 3)增加对工件的夹持力,提高细长轴自身刚度,防止切削振动,保证工件的顺利加工。
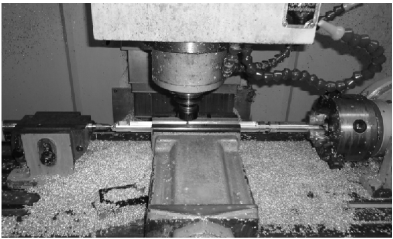
图 3 平口钳顶夹中间部位加工薄壁零件
采用平口钳夹持细长轴中间部位的装夹工艺时需要注意,采用压表法将虎钳的固定钳口与细长轴轻轻贴合,通过 0. 02mm 塞尺控制好细长轴与固定钳口的缝隙,在装夹过程中既要保证虎钳装夹不能过定位,细长轴又能转动自如,工件的弯曲变形被控制在很小范围内,有效保证了细长轴的定位精度。
应注意在旋转细长轴时,必须将细长轴与固定虎钳之间的切屑清除干净,防止工件外表夹屑或者切屑划伤细长轴的外加工表面,影响细长轴表面粗糙度精度要求。最终加工完的零件见图 4。
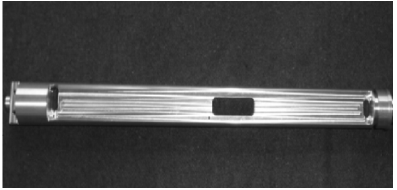
图 4 薄壁细长轴零件加工效果
4 、结语
针对细长轴薄壁铝合金零件难加工以及容易发生加工变形的特点,详细阐述了具体加工工艺步骤以及选用合适的装夹工艺来保证其尺寸与形状位置公差以及表面粗糙度要求,关键步骤采用双顶尖装夹与虎钳顶夹的辅助装夹加工工艺,改变了细长轴在铣削加工过程中的固有共振频率,解决了刚性差问题,大大提高了细长轴的整体机械切削加工性能,这种加工方法在生产实践中具有实践指导意义。
投稿箱:
如果您有机床行业、企业相关新闻稿件发表,或进行资讯合作,欢迎联系本网编辑部, 邮箱:skjcsc@vip.sina.com
如果您有机床行业、企业相关新闻稿件发表,或进行资讯合作,欢迎联系本网编辑部, 邮箱:skjcsc@vip.sina.com
更多相关信息