微小颗粒对刀具测量精度的影响及误差消除研究
2020-2-4 来源: 中北大学机械工程学院 作者:李晓男 曾志强 王日俊 党长营 等
摘 要: 为了消除微小颗粒对刀具测量精度的影响,提出一种基于机器视觉的通过设定阈值和方向选定消除微小颗粒的方法。首先,对刀具进行亚像素边缘提取,通过设定阈值确定刀具边缘,利用刀具边缘和微小颗粒边缘法线方向的不同,找出微小颗粒边缘并对其快速有效的消除。最后,在测量系统上对该方法进行验证。实验结果表明,经过消除微小颗粒后的刀具测量精度达到±0. 02 mm,且单次测量平均运行时间为 100. 76 ms,该方法能快速有效地消除微小颗粒对刀具测量的影响,提高刀具的测量精度,能够满足刀具测量高精度的要求。
关键词: 微小颗粒; 刀具; 机器视觉; 阈值; 法线方向; 高精度
随着我国提出中国制造 2025 制造强国的目标,制造业正在快速的发展,同时对于制造业的高精度、高效率测量也越来越受到重视 。基于机器视觉技术的刀具在线高精度测量技术是保证高精度制造加工的重要手段之一。然而,刀具的测量工作环境较恶劣,测量精度易受到工作环境中微小颗粒等因素的影响,这对高精度加工制造就会因测量精度不足导致加工产品不合格,进而造成较大的经济损失。因此,研究对微小颗粒的消除对高精度测量具有重要的工程意义和实用价值。H. H. Shahabi 等对采集到的刀尖图像进行中值滤波以及形态学开运算处理,达到减少光线强度变化和降低粉尘微小颗粒对刀尖测量精度影响的目的 。
此算法能消除一定的粉尘微小颗粒的干扰,但是对图像进行形态学开运算会改变刀具边缘的实际轮廓,使测量精度提高有限 。周洋利用霍夫变换和差分逼近几何法将刀具轮廓分为直线和圆弧,并进行了两种方法的比较分析———把刀具轮廓假设为直线-直线连接或直线-圆弧连接两种情况,证明了前者抗噪更强,计算量更小。但是此方法假设过于理想化,不适合粉尘微小颗粒这种形状不规则性和提取的边缘多样性的特点。对于没有采用微小颗粒消除技术的刀具检测仪,一般测量者采取先擦试刀具后再测量,但是此方式也无法保证空气中的粉尘再次附着,而且对刀具进行反复擦试会使测量效率大大降低。
针对上述问题,本文主要运用机器视觉图像处理软件 Halcon 并结合 . NET,采用图像处理技术,对图像进行边缘检测,粉尘微小颗粒消除、边缘拟合等方法达到微小颗粒的最终消除。
1 、微小颗粒对刀具测量精度的影响
由于加工车间的环境较为恶劣,空气中常常会充满粉尘,而且在刀具加工过程中产生的切屑也极易附着于刀具表面,这些微小颗粒会对测量过程中刀具的边缘提取与边缘拟合产生一定的干扰。对于只附着在刀具表面的切屑的边缘提取以及拟合,由于其灰度值和刀具的灰度值相近,对于小的离群点可以直接使用最小二乘法拟合原理进行拟合,对于遇到较大的离群点或者拟合点的样本数量不足这些情况时,在使用最小二乘法拟合原理的同时加入权重函数再进行拟合。
对于附着在刀具表面的粉尘、切屑等微小颗粒而言,粉尘的灰度值较高且灰度分布不均匀、范围广,如图 1 所示,边缘提取时会得到多段边缘信息,如图 2b所示,若是直接使用附着切屑的刀具的边缘拟合方法,会拟合出多条线段,如图 2c 所示,无法有效获得所需的刀具单向边缘信息,难以保证测量参数的精确性,甚至导致测量失败。一般测量者先擦试刀具后再测量,但是也无法保证空气中的粉尘再次附着,而且对刀具进行反复擦试会使测量效率大大降低。其中图 2 是含有粉尘颗粒对刀具拟合的影响: ( 1) 含有粉尘微颗粒的刀具图,如图 2a 所示; ( 2) 提取出的亚像素边缘,如图 2b 所示; ( 3) 拟合效果,如图 2c 所示,其结果没有拟合出刀具单向边缘,进而影响后续的测量精度。
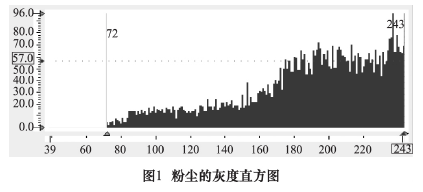
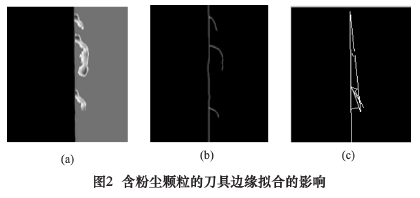
2 、消除微小颗粒的方法研究
为了达到消除微小颗粒的目的,本文采取图像处理技术对微小颗粒进行消除。首先对刀具图像进行边缘检测,分析微小颗粒边缘特点,并引入相关概念,再根据消除微小颗粒的原理对其进行消除。此以处理附着微小颗粒的平底铣刀图像为例。
2. 1 边缘检测
Canny 算子是具有滤波、增强和检测的多级优化算子 ,在图像处理前,Canny 算子首先使用高斯平滑滤波器来平滑图像以消除噪声,Canny 分割算法使用有限的点并采用一阶偏导的方法进行梯度幅值和方向的计算。在处理过程中,Canny 算子还将经过一个非极大值抑制的过程,最后,Canny 算法通过设定两个阈值来检测边缘,使其连续性更好。
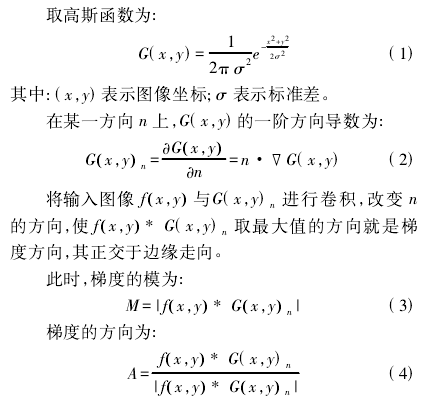
基于 Canny 算子对边缘检测的优点,本方案选择Canny 算子对刀具区域进行亚像素级边缘提取。
2. 2 微小颗粒边缘的特点
基于对切屑等金属微颗粒的可以直接使用最小二乘法并加入权重函数的方法进行边缘拟合,故可以不进行消除。本文主要对粉尘微小颗粒的边缘进行消除,通过对刀具图像边缘提取,提取的粉尘边缘或者刀具边缘的断线此统称为分枝,其类型大概可以分为以下 3 种情况如图 3 所示:
( 1) 交叉边缘,此刀具的边缘与粉尘的边缘出现交叉现象,如图 3a 所示。
( 2) 噪声点,由于噪声在前期没有完全消除,而导致边缘提取后 的 图 像出 现 点 状的 噪 声 点,如 图 3b所示。
( 3) 断线,由于光源角度等原因使粉尘中间段的灰度高于两端而造成提取边缘时出现断裂,如图 3c 所示,或者亚像素边缘提取灰度阈值选取造成的刀具边缘有断裂,如图 3d 所示。
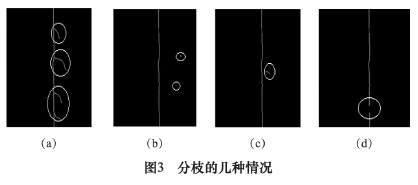
2. 3 消除分枝原理
通过分析刀具亚像素边缘图像可知,基本上所有的交叉边缘在交叉点处和刀具边缘的主干都会成一个比较大的夹角,粉尘微小颗粒的断线和噪声点都偏离刀具边缘主干,而且边缘提取后由噪声产生的边缘也非常短。
基于此种情况,提出一种基于曲线追踪技术的消除分枝的算法,其基本思想是: 利用阈值选择和刀具边缘和微小颗粒边缘方向不同原则,对微小颗粒进行消除。首先通过设定阈值找出刀具边缘的主干,然后在所有的交叉点和断点处,消除与刀具边缘法向方向不一致的分枝,这样最后得到的就是具有单一连通性的曲线,那些与刀具边缘方向不一致和小于阈值的分枝都会被消除。
2. 4 消除分枝过程
以处理平底铣刀的其中一条边缘为例,消除分枝的具体步骤如下:
Setp1: 首先设定一个长度阈值。
Setp2: 找到图像中所有的分枝,如图 4a 所示,并计算交叉点、端点和孤立点的个数,如果没有交叉点和独立点且端点数不大于两个,则不进行消除分枝操作,退出。
Setp3: 如果交叉点只有一个,计算各个分枝长度,选取较长的一根作为主干,然后计算主干和各个分枝在交叉点处的法线方向,保留与主干夹角最小的分枝。
Setp4: 如果交叉点多于一个,计算各个分枝的长度,先将长度小于阈值的分枝消除。
Setp5: 再次计算交叉点的个数,判断有无交叉点,如果没有,执行下步操作; 如果有一个,则重复步骤( 3) 操作; 如果还有多个,则重新设定阈值,重复步骤( 4) 操作,直至没有交叉点为止,此时剩余的部分应该就是主干和断线、孤立点,如图 4b 所示。
Setp6: 计算此时图中的端点数,如果端点个数不多于两个,进行下步操作,如果多于两个,则证明有断线存在,然后计算与该端点相连的断线在该点处的法线方向,与主干过此点的法线方向进行比较,保留与其方向最为接近的分枝。
Setp7: 清除孤立点。
Setp8: 输出结果,即输出的就是消除粉尘微小颗粒后的刀具边缘,如图 4c 所示。
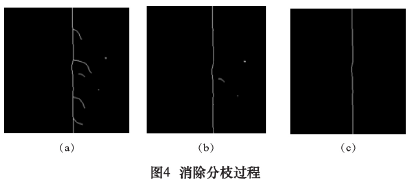
3 、实验研究
3. 1 实验平台搭建
为了验证此算法能较好的消除微小颗粒,运用此算法并以刀具测量系统( 以下简称“检测仪”) 中的刀具直径测量为例进行验证。实验平台的搭建如图 5 所示。实验平台主要包括铣床、被测刀具和检测仪,其检测仪主要包括照明系统、CMOS 工业相机、镜头、驱动部分、显示器以及微型计算机等。照明系统实现对被测刀具的稳定、均匀照明; COMS 工业相机精确采集刀具图像; 镜头的主要作用是将目标成像在图像传感器的光敏面上; 驱动部分主要驱动照明系统亮度的调节;显示器主要是图像和结果的显示; 微型计算机主要做图像的数字化处理。针对该系统要求选取如下硬件:相机选用 MV-EM 1200C 型相机,其 1 200 万的像素在视场为 5 mm×5 mm 时像素精度可达 1. 5 μm; 镜头选用清晰度高、倍率可变、光学无畸变、高对比度的 BT-2216 型双远心镜头; 光源采用 OPT - RI9060 - W 型矩形光。
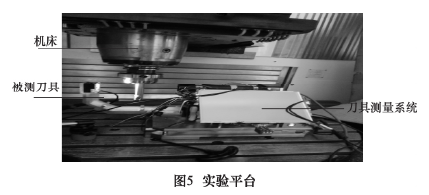
3. 2 图像处理消除微小颗粒及实验数据分析
其中利用检测仪拍摄并选取含粉尘微小颗粒较多且颗粒较明显的平底铣刀图像为例,利用 Halcon 软件结合 . NET 和对其进行相关图像处理,获得消除微小颗粒的图像。图 6a 为刀具原图,b 为二值化后的旋转刀具后的包络图像,c 为利用 Canny 算子提取的刀具以及粉尘微小颗粒的亚像素边缘图像,d 为消除粉尘微小颗粒分枝后的效果图像,e 为直线拟合后的刀具边缘图像,f 显示了消除粉尘微小颗粒后的结果在刀具包络图像中的位置。从这些图中可以看出此消除粉尘微小颗粒的算法,能较好地消除粉尘微小颗粒,获得刀具的单一连通边缘。
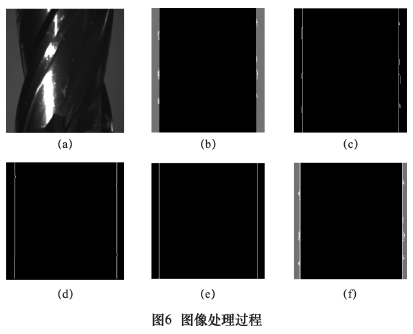
对于刀具几何参数测量的高精度要求,利用本算法对获取的刀具边缘进行拟合后进行一维距离直径测量。采用上述图像处理方法,选取四幅含有较多且明显的粉尘微小颗粒的平底铣刀图像进行实验,其直径分别为 10 mm、16 mm、20 mm、32 mm,首先使用刀具视觉检测仪测量( 刀具擦除粉尘等微颗粒干净后进行测量) 的刀具直径分别为 10. 027 5 mm、16. 024 7 mm、20. 026 2 mm、32. 025 6 mm。为了减小误差,本实验对以上四种刀具分别进行 5 次测量,并且刀具直径测量分两种情况,一种是消除粉尘前的刀具直径测量数据对比结果如表 1; 一种是消除粉尘后的刀具直径测量数据对比结果如表 2 所示。
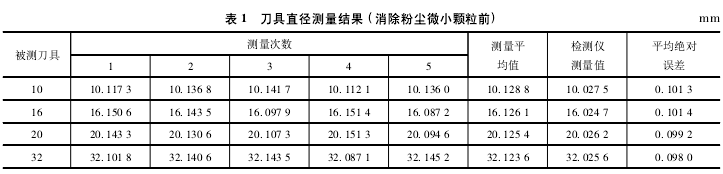
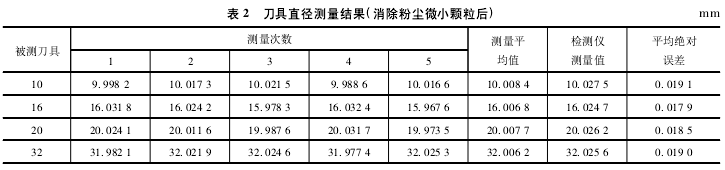
经过两组数据进行比较,消除粉尘微小颗粒前的刀具直径测量结果的平均误差最大达到了 0. 101 4mm,误差较大; 而运用本算法消除粉尘微小颗粒后的刀具直径测量结果,其最大的平均绝对误差为 0. 019 1mm,测量精度达到±0. 02 mm,且单次测量平均运行时间为 100. 76 ms,运行效率比较高,可以较好满足测量要求,对于圆鼻刀、球刀等圆弧部分的微颗粒消除,此消除粉尘微小颗粒对刀具参数测量精度影响的方法同样适用。
4 、结语
本文从理论上分析了微小颗粒对刀具测量精度的影响,并在刀具边缘拟合的过程中通过消除分枝算法对微小颗粒进行消除。在高精度刀具测量系统上对手动擦除粉尘微小颗粒的检测仪测量所得数据和使用本算法消除粉尘微小颗粒前后测量所得数据进行了数据对比。实验结果表明,测量精度达到±0. 02 mm,单次测量程序的平均运行时间为 100. 76 ms,该方法能快速有效地消除粉尘微小颗粒对刀具测量的影响,提高了刀具测量的精度。
投稿箱:
如果您有机床行业、企业相关新闻稿件发表,或进行资讯合作,欢迎联系本网编辑部, 邮箱:skjcsc@vip.sina.com
如果您有机床行业、企业相关新闻稿件发表,或进行资讯合作,欢迎联系本网编辑部, 邮箱:skjcsc@vip.sina.com
更多相关信息