叉架零件加工方案设计
2019-11-21 来源:广东省技师学院 作者:李建华
1、提出问题
受到机床本身精度的影响,在车床上加工零件时,很难保证零件上的某些形位公差要求。如图 1 所示叉架零件,图纸中的两处对称度在实际生产过程中难以保证。经过分析,利用定值对刀杆和定值对刀块转移误差的方法能解决该处对称度超差的问题。
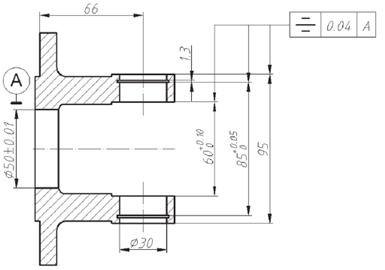
图 1
2、解决方案
图 2 为工件毛坯图,该叉架零件原定的加工方案是 :划线→车削 Φ50±0.01mm 内孔→按线钻孔 Φ28mm →镗削60+0 . 1 0 0mm 尺寸→镗削 95mm 尺寸→镗削 Φ30mm 内孔,然后以 60+0 . 1 0 0mm 尺寸的一个端面进行对刀,移动工作台切槽,再用定值对刀杆来保证 85+0 . 0 5 0mm 尺寸和 0.04mm 的对称度要求。
按照这个加工方案进行生产,图纸上的 0.04mm 对称度公差要求很难保证。因此,我们拟在 C620 卧式车床上,采用转移误差的方法,来解决对称度超差的问题。同时以将原来的四道工序(划线→车→铣→镗)减少至两道工序(划线→车)。从而降低生产成本并提高产品质量。
该叉架零件在工作时,绕 Φ50±0.01mm 孔轴线作高速旋转,其形位精度对整机工作的稳定性和使用寿命起决定性作用。因此,尺寸 85+0 . 0 5 0mm加工精度和尺寸85+0 . 0 5 0mm、尺寸 60+0.10
0mm、95mm 对基准 A 的对称度要求很高。要保证这几处形位精度,第一是零件的定位基准尽量与设计基准统一,并且可靠定位。因此,直接采用 Φ50±0.01mm 内孔定位。第二是车床刀架轴向移动精度。我厂的 C620 卧式车床小滑板和床鞍纵向进给精度分别为 0.05mm 和 1mm,不足以保证零件的公差。
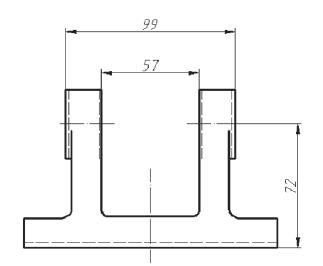
图 2 工件毛坯图
为此,我们设计了一套专用夹具,该夹具以零件Φ50±0.01mm 内孔定位,保证了设计基准与定位基准统一。为了保证各个尺寸精度,使定位基准与对刀板有很高的位置精度。我们采用先在坐标镗床上加工完定位架后,接着在平面磨床上配磨对刀板的方法。然后,制做定值对刀量规,来保证实现刀架轴向移动距离的精度,以控制在加工完叉架的一侧端面及切槽后,旋转 180°加工另一侧端面及切槽。
因此,尺寸精度完全由对刀精度和定值对刀量规制造精度所决定,不会受到车床小滑板和床鞍进给精度的影响,而对称度仅取决于零件定位精度。由于这个专用夹具的工件定位精度很高,刀架的移动距离又能保证得到很高的精度,从而解决了零件的高对称度要求的问题。
操作方法(如图 3、图 4、图 5、图 6、图 7 所示):首先将定值对刀块和定值对刀杆组装好,再移动床鞍,用对刀块和对刀杆组件确定定位板与床鞍前端面定位螺钉的位置。接着,移动车床小滑板将端面车刀或切槽刀与对刀板进行对刀,从而保证端面车刀或切槽刀与对刀板,定值对刀杆组件与床鞍前端的定位螺钉同时定位。然后去掉对刀组件中的定值对刀块,移动床鞍,用定值对刀杆与定值对刀块差值确定车刀的位置车削叉架的外侧端面。采用可调对刀杆确定车刀的位置车削叉架的内侧端面。然后将叉架旋转 180°加工另一侧内外端面。接着,确定切槽刀的位置切出第一个槽。此时床鞍移动的距离是对刀块的厚度尺寸,正好也是切槽刀从对刀板移动到第一个槽的位置。
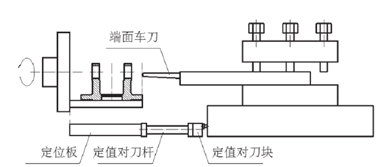
图 3 端面车刀对刀
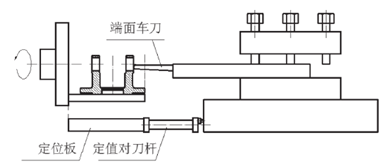
图 4 车削外侧端面
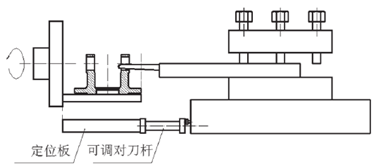
图 5 车削内侧端面、车孔、铰孔
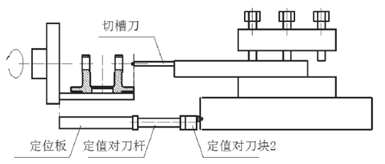
图 6 切槽刀对刀
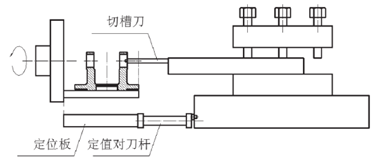
图 7 切槽
同样,利用不同的对刀组件车削叉架的近端内外端面。然后又将叉架旋转 180°,并找正,重复上述步骤。从而保证尺寸 85+0 . 0 5 0mm 的精度和叉架的对称度要求(0.04mm)。从上述操作方法可以看到,端面车刀和切槽刀沿车床主轴方向移动距离的精度,完全由尺寸精度很高的对刀块及对刀杆所决定,有效保证了叉架零件图纸中的 3 处对称度要求。
对于加工类似的叉架零件,只需更换夹具中的定位件、对刀块、对刀杆即可。经过实际生产的检验,此加工方案有效地保证了零件的尺寸精度与形位公差,降低了生产成本,提高产品的质量。
投稿箱:
如果您有机床行业、企业相关新闻稿件发表,或进行资讯合作,欢迎联系本网编辑部, 邮箱:skjcsc@vip.sina.com
如果您有机床行业、企业相关新闻稿件发表,或进行资讯合作,欢迎联系本网编辑部, 邮箱:skjcsc@vip.sina.com
更多相关信息