数控车床主轴温度场分布检测与控制措施
2019-5-30 来源:沈阳理工大学 机械工程学院 作者:史安娜 ,曹富荣 ,刘斯妤
摘要:数控车床主轴的热变形对加工产品的质量和精度有重要的影响,温度场的分布不均匀是导致热变形的主要因素。以CAK3665经济型数控车床主轴为研究对象,应用FLIR红外热成像仪测温技术对车床主轴的温度场展开测量,分析造成车床主轴的温度场分布不均匀的热源,测出随着车床主轴在中速下连续运转,各测点的稳定温度以及温升变化规律。提出改善温度场分布不均匀的方案,为后续进行热分析以及实现数控车床的高速高精密加工奠定基础。
关键词:数控车床;温度场;FLIR热成像仪
引言
数控加工技术向着高可靠性、高速度以及高精度的方向快速发展,现代制造行业对数控机床的加工速度、加工效率的要求越来越高。改善车床的热特性,成为制造业发展中最重要的研究课题之一。数控车床产生的热变形,是因为车床的温度升高而造成车床部件会膨胀或者变形,从而导致刀具与工件之间的相对位移产生变化。热误差是高精度、高速机床的最大误差源,约占总误差的70%左右。主轴作为高档数控车床的最重要零部件之一,主轴的热变形主要是由主轴的温度场分布不均匀所导致的,对数控车床主轴的温度场进行测试,对后续进行热变形分析,提高车床的加工精度、加工效率显得尤为重要。
以CAK3665数控车床主轴为研究对象,对主轴热稳定后的整体温度变化以及分布数据进行测试,并提出改善由于热源所造成的主轴温度场分布不均匀的方案。直接对改善车床主轴的热特性提供了依据。
1、数控车床主轴的热源
在正常工作的情况之下,数控车床的主轴受到内、外热源的作用,这些热源都不是恒定的,内部热源与外部热源的分类如图1所示。由于主轴上各零件的机构、材料、形状都不尽相同,受热性能也不相同;在结合面处的每个连接件之间有不相同的表面传热情况以及一定的热阻等因素,使得数控车床主轴表面产生了一个多变、复杂的温度场。在形成的温度场作用的影响之下,主轴上每个零部件材料所生成的热应力与热位移随着零部件的形状、支承的方式以及材料本身的物理属性的不同而不同,这样,主轴的热变形问题将变得更为复杂。
对主轴部件的加工精度起着最重要影响作用的因素不是温升,而是主轴上温度场的分布,其实是指温度的梯度与温度场相对于主轴的对称性分布。虽然主轴部件的温升比较高,但是,其温度场的分布比较均匀,主轴系统每个点上的温差比较小,主轴上温度的梯度也很小,这样,由温升引起的误差很小。但是,即使主轴系统的温升很小,而主轴上每个点的温度场分布不对称或者是各个点的温差比较大,这样,所导致的加工误差也会很大。
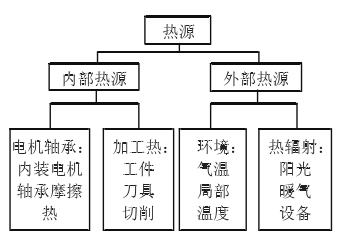
图1 内外热源分类示意图
2 、FLIR红外热成像仪测温
红外测温为非接触式测量,不改变被测量介质的温度场,并且可以对移动物件的动态温度进行测量。红外测温的缺点为,在1000℃以下进行测量时,温度误差较大。但是,对于运行中的机床进行测量,尤其是指对旋转部件的温度检测,这种非接触式的测温方式是最为合适的。
利用热成像仪来检测物体辐射单元的辐射能量。利用斯蒂芬.玻尔兹曼定律来求辐射单元的表面温度,被测物体表面的辐射能量被红外线热像仪转化成为视频可见的图像,通过光扫描机构,红外探测器进行探测辐射单元的辐射能量,并且将辐射单元的辐射能量转化成为电子视频信号,再经过信号的处理,能够显示出可见的图像。热像图用来表示被测量表面的二维辐射能量场以及所对应的物体表面的温度分布场。
在测量之前确定的参数有:被测量物体表面的发射率ε,被测量物体和热成像仪检测元件之间的距离Dobj,被测量物体周围的温度或者环境反射温度Trefl,及其大气温度Tatm。
斯蒂芬.玻尔兹曼定律:
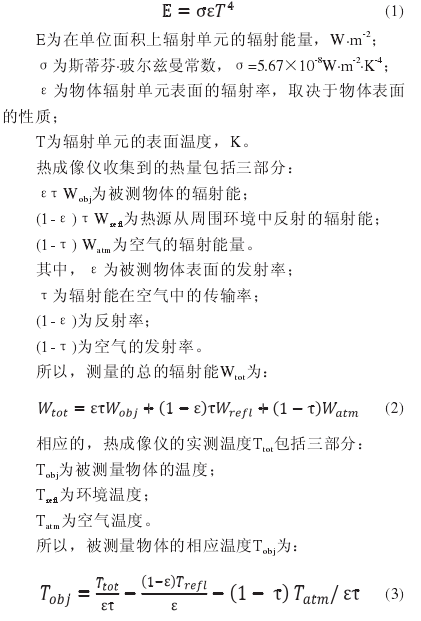
3、实验检测
以沈阳机床集团CAK3665经济型数控车床主轴为研究对象,进行测试该机床主轴的温度场分布以及温升变化规律。CAK3665数控车床的整体结构示意图如图2所示。
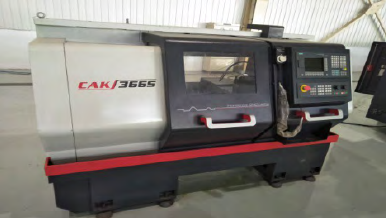
图2 CAK3665数控车床整体图形
机床在冷态下开始试验,环境温度为22℃,相对湿度为50%,由于主轴采用铸铁材料,其传播率为1.00,反射率为0.637,热成像仪与发热点的距离为2,满足在试验前12小时之内没有工作,试验时不准机床中途停车。
利用FLIR热成像仪作为本试验主要的仪器设备,在数控车床主轴前后轴承以及其他主要热源处布置测点,实验时直接对各测点进行测量即可,该机床主轴的最高转速为4000r/min,应采用2000r/min的转速对数控车床主轴的温度场进行测试,可保证机床在高速运行时绝对安全,并通过软件的处理转换为实际的温度值。在主轴运转时,运用热成像仪对主轴进行定期拍照,记录每一时刻的主轴温升热场,测得每一时刻各测点的温度值,温度测试系统的连接图如图3所示,其中,1为红外热像仪,2为火线,3为运行数据釆集及处理软件的PC机,4为电源模块。测试现场的图片如图4所示。
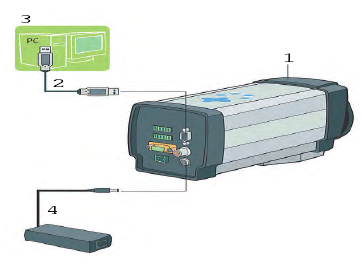
图3 温度测试系统连接示意图
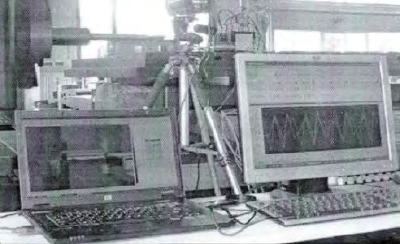
图4 测试现场照片
主轴总共运行540min,当主轴连续转动270min时达到热稳定状态,在该状态下主轴的温度场分布如图5所示。以最终主轴前后轴承处的最高温升作为考核的指标,车床主轴在中速下连续运行270min,主轴轴承温升测量结果如表1所示。主轴在转动过程中各个测量点的温度时间变化曲线如图6所示。
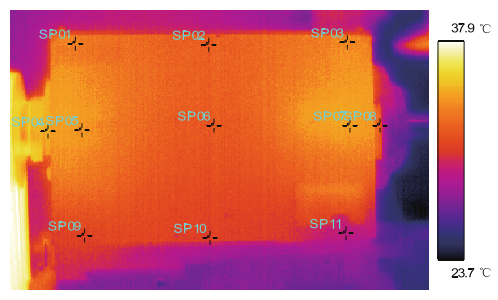
图5 热成像仪测量的温度分布
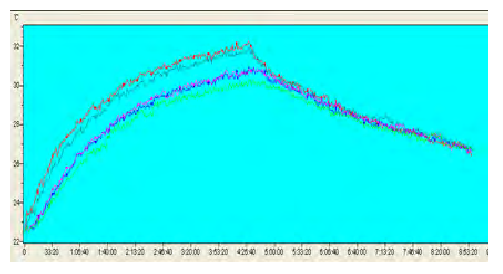
图6 温度变化曲线
4、实验结果分析
通过以上实验,得出了数控车床主轴温度分布图,以及温度随时间的变化规律,由图5可知,由于热源的作用,使得整个温度场的分布不均匀,在前后轴承及法兰盘所在位置处的温度比其他地方高,主轴后轴承处的温度比前轴承处的高,主轴后轴承法兰盘处的温度也比前轴承法兰盘处的高,主轴头部将有翘曲的趋势,严重影响机床加工精度。由图6知,从冷态下开始试验,车床主轴总共运行540min,在前270min运行的过程中,随着车床主轴的运转,各测点的温度逐渐升高,当车床主轴连续转动270min时达到温升稳定,各测点的温度值将不再随着主轴的运转而增加,后270min停车冷却,各测点的温度逐渐降低。由表1可知,当车床主轴连续转动270min时,各测点的温度值将趋于稳定,此时,SP4(后轴承法兰盘)处的温度值为32.281,SP5(后轴承)处的值是31.582,SP8(前轴承法兰盘)处的温度值为30.744,SP7(前轴承)处的温度值是31.863,由此得出前轴承法兰盘处的最高温升为7.8,后轴承法兰盘处的最高温升为9.3。
5、改善温度场分布不均匀的措施
主轴的热变形主要是由主轴的温度场分布不均匀而导致的,而温度场的分布不均匀是由主轴的冷源与热源的综合作用所引起的。综合以上实验测试的结果,提出以下措施:
1)选择合适的轴承支撑系统。使得主轴两端的轴承热变形基本一致,避免主轴发生翘曲。
2)改善冷却与散热条件。用循环水、循环冷空气等方法对主要的发热体进行冷却,以便带走主轴上的热量,从而减小主轴的热变形量。
3)均衡温度。在主轴结构中,通过对主轴各部位的温度快速均衡,使得温度较高位置的热量快速的传到温度较低的位置,以便达到热量与变形的平衡。
4)改善主轴结构。将主轴设计对称结构,以便在温升较大时,主轴各个部位所发生的变形平衡,减小加工误差。
表1 主轴轴承在中速下不同时间内的温升测量结果
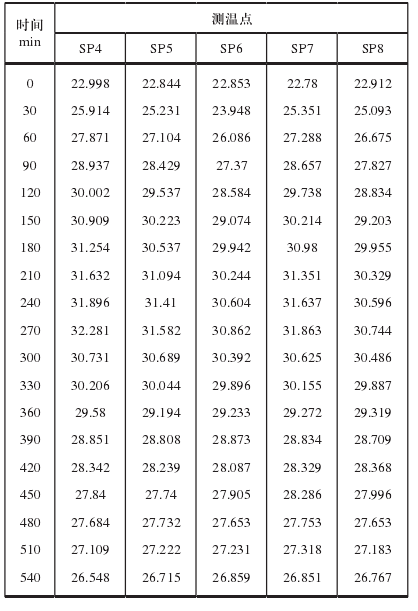
设计到仿真优化过程。通过数字化工厂仿真平台,可直观地观察机器人在工作过程中运动状况,对机器人及设备的运动轨迹进行建模仿真,并对整体生产线进行节拍优化,很好地指导生产实际,极大提升工程设计人员的设计效率,减轻设计人员的工作强度,缩短工艺规划时间,优化生产布局,避免机器人与设备间的干涉情况,减少不必要的浪费。
投稿箱:
如果您有机床行业、企业相关新闻稿件发表,或进行资讯合作,欢迎联系本网编辑部, 邮箱:skjcsc@vip.sina.com
如果您有机床行业、企业相关新闻稿件发表,或进行资讯合作,欢迎联系本网编辑部, 邮箱:skjcsc@vip.sina.com
更多相关信息