当今制造业生产经济学的现实
2019-3-12 来源:山高刀具集团技术培训 作者:Patrick de Vos
机床车间希望能够将零件生产控制在一定时间和成本内。实现这一目标需要平衡很多因素,包括切削参数、刀具成本和更换时间、机床利用率、工件装卸费用以及材料和人工成本。
生产经济学是兼顾各种工艺因素以获得理想结果的艺术和科学。在两个多世纪的加工历史中,生产经济学的要数量成倍增加。首先,制造业从工艺级单项产品的生产,发展到使用机床大规模生产标准化零件。制造方法的改进带来了第二代批量生产,其中包括生产线的运用以及相同零件的产量日益提高,这就是“大批量低混合”(HVLM) 产品方案。然后,数控机床和机器人造就了第三代批量生产效率。最近,应用于编程、机床控制和工件装卸系统的数字技术正在促进第四代制造生产(称为“工业4.0”)的发展,它能实现经济高效的“高混合小批量”(HMLV) 生产。
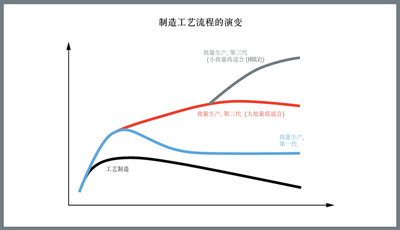
制造工艺演变
为了有效地实现从 HVLM 向 HMLV 生产的转变,制造商必须清楚认识到生产经济学正在不断地变化和增长,然后利用可用的信息和技术来分析运营状况并实现运营目标。一个关键转型因素是抛弃过于简单的理念和做法,确认哪些隐性成本可能会阻碍生产率的提高。
大批量、低混合,简单经济学?
标准化加工工艺起源于 19 世纪,用于加快生产具有可互换零件的相同产品。汽车制造业将这种 HVLM方法改进到了极致,发展出传送生产线和其他工艺方法,多年来制造了数十万甚至数百万相同的零部件。
HVLM 生产周期长,这使得制造商能够微调多个工艺因素,以实现最大产量、保持质量一致以及降低成本。包括换刀系统、托盘交换系统及机器人在内的辅助技术进一步降低了生产变动性。可以说操作过程完美运行,能以可预测的成本实现 100% 产量,而且能消除计划外闲置时间,杜绝次品和返工,也无需去毛刺等二次操作。
有个说法是刀具成本通常约占总生产成本的 3%。3% 可以作为一个基准,但往往实际情况下并不能直接以此衡量。例如,工件材料的加工特性影响很大,加工材质从钢材切换到钛材可能会使刀具使用率增加五倍。在其他条件相同的情况下,3% 将变为 15%。
仅关注刀具啮合时间会导致其他因素被忽略,例如因换刀而产生的闲置时间。这种方法实际上掩盖了现实。制造商应该了解加工时间、装夹时间、换刀时间、装载和卸载以及其他因素会相互影响和干扰。在关于工艺因素之间意外作用的简化示例中,车间加工一个零件需要 2 分钟的切削时间和 2分钟的工件装卸时间。刀具转位花掉 1 分钟,刀具在使用寿命内可加工 5个工件,因此每个零件所需的刀具转位时间为 0.20 分钟。由于每个零件需要 4.2分钟的加工时间,所以每小时产量略高于 14 个工件。每个刀具的成本为 15 欧元,5个工件所需的刀具寿命决定了生产 14 个工件需要 2.8 个刀具(42 欧元)。机床成本为每小时 50欧元。这样,每小时生产 14 个工件的总成本为 92 欧元。
然后,为了提升产量和生产率,车间将切削速度提高 10%。这样可将切削时间缩短 10%(达到1.8分钟),但也使刀具寿命缩短大约一半,这意味着在需要转位之前,一个切削刃只能生产 2.5个工件。刀具转位时间仍为一分钟,工件装卸两分钟。一个工件的生产时间为 4.2 分钟(切削 1.8分钟,工件操控 2 分钟,刀具转位 0.4 分钟),换算一下也就是每小时生产 14个工件。机床和刀具的成本是相同的,但现在每小时需要耗费 5.6 个刀具(84欧元刀具成本)。 尽管努力提高产量,但 14 个工件的生产时间是相同的,而成本则从 92 欧元上升到了 134欧元。
在这种情况下,提高切削速度不会使操作更加高效。更改切削时间会影响加工系统中的其他因素,在本例中影响的是刀具寿命和刀具转位时间。因此,车间必须仔细权衡流程变更的各种后果。
隐性成本的另一种形式涉及工艺步骤的执行情况。例如,在许多加工车间中,最典型的隐性成本就是刀片转位所花费的时间。指定的刀片转位时间可能是一分钟。然而在车间实际测量时发现,它可能是两分钟、三分钟甚至十分钟,时间相差 60 到 600 秒。
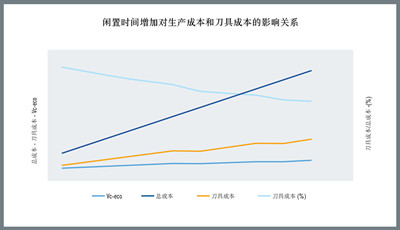
刀具成本随闲置时间的变化
高混合、小批量,全面的考虑
如今,全球竞争促使制造商生产不同类型的产品,以满足较小用户群的需求。先进的计算技术可以快速更改零件的设计和加工程序,还可以轻松跟踪产品的变化和库存。结果是制造商转而采用“高混合、小批量”(HMLV)生产方案。如今,这种方法已经发展到足以高效地制造个位数产品,甚至是大量生产单项产品。
HVLM 的更长生产周期允许制造商从容地规划和微调工艺因素。在 HMLV生产方案中,生产计划是不同的。计算机化的工程和库存技术支持快速变换产品类型和产量,但 HMLV 规划过程变得复杂且反应灵敏。客户订购十个零件后,可能会接着订购两个、五个零件甚至是单一产品多个批次的不同零件。工件材料可能从钢材换成铝材再换成钛材,零件几何形状可能从简单变得复杂。但是没有足够的试运行时间来确定刀具寿命。
为了管理 HMLV 生产方案中的刀具寿命,车间通常会对刀具的预期寿命做出保守猜测;为了安全起见,每次加工都会使用新刀具,并在刀具达到其完整的生产寿命之前将其丢弃。切削时间只是整个加工中的因素之一。在 HMLV 生产中,操控不同工件和夹具以及更换刀具和转位刀片所需的时间通常比实际切削时间更长。刀具、机床、闲置时间、直接的人工和工件材料因素中可能包含隐性成本。最新的生产经济学方法考虑了刀具和工件材料成本、设备和生产成本、停机期间的设备成本以及人员工资和维护成本。

生产经济学
快速变化的 HMLV 产品需求增加了实现高百分比合格率的难度。在生产周期较长的 HVLM
生产中,经过试验和调整可以获得高达 90% 的合格率。另一方面,HMLV合格率可能是二元的。成功的单件生产代表 100% 的合格率,但是当零件不合格或工件毁坏时,合格率变为零。由于对质量、成本和时间效率的要求保持不变,一次合格率成为首要要求。在这种情况下,避免刀具破损可能是最重要的考虑因素。一个有利方面是刀具磨损在短期加工中影响极小,并且车间可以在合理范围内应用更强劲、更高产的切削参数。
一个相关变量是确定何时转位刀具最合适。如果等待时间过长,即使没有损坏工件,也可能导致刀具破裂,至少会中断生产。另一方面,过于频繁的换刀会增加刀具成本,并会因停止加工和转位刀具而耗费更多时间。确定何时更换刀具需要审视换刀时机与整个加工系统的关系,以便制定换刀协议并遵循相关规则。
结论
金属切削系统中的加工因素之间不是一对一的关系。改变切削工况、工件材料或产品产量将影响刀具寿命以及加工系统的许多其他方面。在制造工厂,生产经济学面临的挑战是要了解这些关系,并制定相应策略以务实的方式平衡这些因素。然而,并非车间中的每位工人都能成为数学教授,而且他们没有时间深入了解这些加工背后的关联。因此,供应商可以提供工艺分析和管理服务,帮助制造商全面了解其特定运营情况,并就如何最大限度地提高生产率和经济实力提供有力指导。
令人惋惜的是,许多车间所有者拥有大量的业务和付费客户,但企业仍然面临亏损。解决之道是认清当前生产经济学揭示的许多影响因素,发现和消除被忽视和隐藏的成本,以使他们的制造业务能够获得最大回报。
附注
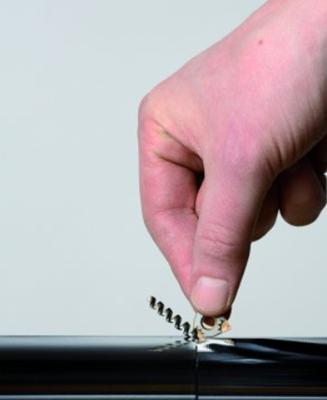
Duratomic 切屑
自动化分析
从批量生产初期开始,影响制造生产率和成本的因素数量已经成倍增加。随着加工操作和设备变得越来越复杂,制造系统的各种要素之间的关系也变得日益复杂。这些要素都不是孤立存在的,例如,改变产量要求将会影响刀具、设备、维护、人工和其他成本。
确定影响因素的数量及其相互关系本身就是一项重大挑战。由于这种复杂性,我们必须借助系统性方法来衡量、控制和管理制造过程。
山高的“生产率成本分析”(PCA) 系统可以检查整个制造过程,以确定降低成本和提高生产率的方法。该系统依托山高长达数十年的全球制造经验和技术底蕴。山高将这些知识与先进的计算机分析和算法结合在一起,包括采用蒙特卡罗模拟方法实现成本建模的自动化。
山高技术专家能为客户执行 PCA,评估其制造过程中所使用的刀具和技术,从而生成包含工艺信息(比如刀具和切削参数)和成本信息(包括每件成本、每小时产出和投资成本)的综合报告。PCA可以评估从单个机床操作到整个制造流程。
做这项分析的目的在于提高生产率,这对成本的影响最大。该系统考虑了瓶颈问题及操作限制,可以识别哪些方面需要进行更深入的研究。
通过对操作或设施进行时间和成本方面的基准研究,PCA 软件将在初始阶段检查刀具因素,包括工艺参数、循环时间和产量要求。第二阶段会进行类似的刀具检查,但会对切削工况和刀具进行调整。第三阶段可能考虑工艺、运营因素以及其他方面的改进,比如机床升级。
无论制造商服务于什么行业,使用山高 PCA 系统后通常可以节约 30% 的总成本、生产率提高约 40% 。
投稿箱:
如果您有机床行业、企业相关新闻稿件发表,或进行资讯合作,欢迎联系本网编辑部, 邮箱:skjcsc@vip.sina.com
如果您有机床行业、企业相关新闻稿件发表,或进行资讯合作,欢迎联系本网编辑部, 邮箱:skjcsc@vip.sina.com
更多相关信息