利用普通车床加工细长杆零件的工艺改进
2017-11-15 来源: 包头职业技术学院车辆系 作者:贾玉梅
摘 要:通过改进细长杆零件装夹方法、跟刀架的结构及调整方法,优化刀具的几何参数,改变刀具的安装位置和车削走刀方向后,加工完成的细长杆零件尺寸精度、形状精度等加工精度满足图样要求,省去了成品校直工序,降低了加工成本,缩短了加工周期,提高了生产效率。
关键词:零件;刀架;刀具;加工精度
所谓细长杆是指零件的长度L 与直径d 之比≥25。与一般的轴类零件相比,细长杆零件存在工件细长、刚度差及受热影响变形较大的特点,这给车削加工带来很大的困难,不容易获得良好的几何精度[1-2]。在普通车床上的常规车削方法是:先将细长杆零件装夹于车床主轴箱的三爪自定心卡盘和尾座的顶尖之间,然后在中心架、跟刀架的配合下,采用正向切削法用标准刀具进行车削。由于细长杆零件本身结构的特点以及加工工艺的原因,车削完成的细长杆零件有较大的弯曲变形[3-4]。为了使零件达到图样要求的精度,应增加校直工序,零件精度要求越高,校直的次数越多。尽管经过了校直工序,有些细长杆零件还是因为不能满足图样要求而报废。
1 、改进加工工艺技术方案
加工工艺改进方案如下;
1)细长杆零件夹紧措施。用卡爪定心、夹紧细长杆零件时,在3个卡爪与零件的接触面之间分别垫1个4~6mm的钢丝段,细长杆零件装入卡爪的长度为15~20mm,钢丝段横向放入卡爪的防滑槽内,
2)跟刀架的结构形式及调整顺序。跟刀架采用3个支承爪结构,调整顺序依次为:后支承爪→上支承爪→下支承爪。
3)车刀安装位置。粗车时,刀尖应高于细长杆零件轴向中心线0.4~0.6mm;精车时,刀尖应低于细长杆零件轴向中心线0.1~0.2mm。
4)走刀方向。走刀方向为反向切削。
5)尾座顶尖预紧力的调整。车刀参与切削前,尾座顶尖预紧力的调整方法如下:用手捏住转动的尾座顶尖,尾座顶尖即停止转动,而细长杆零件仍然转动;松手后,尾座顶尖能随着细长杆零件继续同步旋转,尾座顶尖的顶紧力达到这种状态时开始进行切削工序。
6)车刀几何参数。主偏角75°~80°、前角20°~30°、刃倾角3°~5°、主后角10°~15°、副后角2°~3°,前刀面磨R1.5~R3mm 的断屑槽,刀尖圆弧半径<0.3mm。
7)热处理。粗加工后热处理:中温时效温度400℃,保温4h,随炉冷却;弯曲度若不满足要求,需要增加校直工序,之后低温时效温度200~240℃,保温2~3h,随炉冷却。
2、改进加工工艺与常规加工工艺对比
2.1 装夹方法
常规的装夹方法,三爪和顶尖将细长杆零件刚性夹紧,所以在车削过程中,细长杆零件由于切削力、切削热及自重的影响而产生的变形无法调整,切削过程中这种变形的不断积累,必然导致细长杆零件产生严重的弯曲变形。改进的装夹方法,用卡爪定心、夹紧细长杆零件时,在3个卡爪与细长杆零件的接触面之间分别垫1个5mm 的钢丝段。细长杆零件装入卡爪的长度为15~20mm,钢丝段横向放入卡爪的防滑槽内,由于钢丝段为柔性结构,所以当细长杆零件在切削状态产生热变形时,可以起到方向调节的作用,或在细长杆零件靠近卡爪处车一段“缩颈”,也可以实现方向调节的目的。这些措施的实施,可以有效控制细长杆零件在车削过程中的变形,从而减小或避免细长杆零件的弯曲变形。
2.2 车削的走刀方向
常规的走刀方向为正向切削,即从尾座向主轴箱方向的切削,切削产生的轴向分力指向主轴箱,由于细长杆零件刚性装夹于三爪自定心卡盘上,无法消除切削产生的轴向分力,这就使细长杆零件受压而产生弯曲变形。
改进的走刀方向为反向切削,即从主轴箱向尾座方向的切削,切削产生的轴向分力指向尾座,此时如果尾座顶尖的顶紧力合适,将会平衡掉这个轴向分力,从而使细长杆零件受热伸长后的变形量得以释放,从而避免细长杆零件的弯曲变形。
2.3 尾座顶尖预紧力的调整
车刀参与切削前,用手捏住旋转的尾座顶尖,尾座顶尖即停止旋转,而细长杆零件仍然旋转;松手后,尾座顶尖能随着细长杆零件继续同步旋转,尾座顶尖的预紧力达到这种状态时,就可以使细长杆零件受热伸长后的变形量随着尾座顶尖预紧力的变化而释放。
2.4 跟刀架的安装
2.4.1 跟刀架的结构
常规的跟刀架结构为2个支承爪结构,上面1个,后面1个。细长杆零件由于没有对称的平衡力夹紧,所以在车削过程中,由于本身的重力及不可避免的弯曲,会因离心力瞬时离开或接触支承爪而产生振动,从而不能保证细长杆零件加工的尺寸精度和形状精度。
改进的跟刀架结构为3个支承爪结构:上支承爪、下支承爪和后支承爪。跟刀架的3个支承爪与车刀组成2对平衡的径向力,使细长杆零件在车削时,上下、前后都不能移动,车削过程稳定,不易产生振动,从而保证了细长杆零件加工的尺寸精度、形状精度和表面粗糙度要求。
2.4.2 支承爪的调整顺序
跟刀架支承爪的调整,先调整后支承爪,即与车刀相对的支承爪,以确保刀具的切削位置,再顺序调整上支承爪和下支承爪,保证工件重力方向支承和夹紧的平衡性。调整时,综合运用手感、耳听和目测等方法,使跟刀架的支承爪刚好接触细长杆零件。如果跟刀架的支承爪和细长杆零件接触压力过大,会把细长杆零件车成竹节形,反之则不能起到跟刀架的作用。
2.4.3 基准外圆的车削
装夹细长杆零件后,在靠近三爪自定心卡盘处车长度约40mm的基准外圆,用于安装跟刀架。切削量大小视细长杆零件毛坯料的实际情况而定。
2.5 车刀的几何参数
常规车刀的几何参数为:前角10°~15°、主偏角80°~93°、刃倾角0°、主后角6°~8°。改进车刀的几何参数如下:1)为减小细长杆零件弯曲变形,车削过程中径向切削力越小越好,合理的车刀主偏角为75°~80°;2)为减小切削力和切削热,应选择较大的车刀前角20°~30°;3)车刀前刀面磨R1.5~R3mm的断屑槽,使切削顺利卷曲折断;4)车刀刃倾角选择3°~5°,使切屑流向至待加工表面;5)车刀切削刃表面粗糙度>Ra0.4μm,并要经常保持锋利;6)为降低车刀的磨损,选较大的主后角10°~15°,另外在车刀主后角的最前端即从刀尖开始磨出副后角2°~3°,副后角可起到支承工件,有效减小径向切削力,使加工平稳的作用,刀尖圆弧半径<0.3mm。
2.6 车刀的安装位置
在常规车削时,刀具的刀尖与细长杆零件的轴向中心线齐平,很容易出现扎刀现象。
改进的装刀位置:粗车工序,装刀时刀尖应高于细长杆零件轴向中心线0.5mm,可避免产生扎刀现象;精车工序,装刀时刀尖应低于细长杆零件轴向中心线0.1mm,可起到支承零件的作用,使车削过程更加平稳、可靠,车削效果更好。
2.7 车刀材料及规格
粗车工序选用耐磨性好的硬质合金车刀(YT15、YT30)。精车工序选用高速钢宽刃车刀(W18Cr4V宽刃车刀),可进行大走刀量切削,从而提高细长杆零件的尺寸精度,降低表面粗糙度。刀具材料与常规车削选用的相同,但精加工时选用的刀具规格不同,即宽刃车刀。
3 、装夹结构示意图
装夹结构示意图如图1所示,局部放大示意图如图2所示。
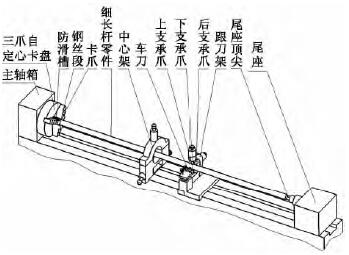
图1 装夹结构示意图
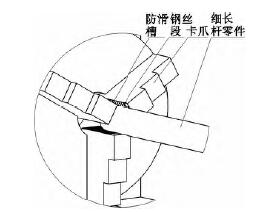
图2 装夹结构局部放大示意图
4、结语
通过改进细长杆零件装夹方法,改变车削的走刀方向和刀具的安装位置,改进跟刀架的结构及调整方法,优化刀具的几何参数,加工完成的细长杆零件尺寸精度、形状精度等加工精度满足图样要求,省去了成品校直的工序,降低了加工成本,缩短了加工周期,提高了生产效率。
投稿箱:
如果您有机床行业、企业相关新闻稿件发表,或进行资讯合作,欢迎联系本网编辑部, 邮箱:skjcsc@vip.sina.com
如果您有机床行业、企业相关新闻稿件发表,或进行资讯合作,欢迎联系本网编辑部, 邮箱:skjcsc@vip.sina.com