桌面数控车床结构的优化设计
2017-6-29 来源: 四川大学制造科学与工程学院 作者:黄纪刚 方辉 蒋滔 董秀丽
摘要:针对微小零件的加工制造,设计了1台桌面级数控车床。用Solidworks软件进行车床的结构设计,重点使用Solidworks软件中的 Simulation Xpress模块对车床关键部件的结构进行有限元静力学分析,经过计算求解,模拟出各部件在实际工作时所受的应力以及应变分布情况。根据计算结果,对结构进行针对性地优化。在优化的过程中,主要以质量最小化为优化目标,使结构在满足力学性能的前提下,尽可能轻量化,以降低成本。最终根据优化后的设计方案构建出桌面级车床。
关键词:车床;Solidworks;优化设计;有限元分析
随着社会的发展,人们趋于追求许多常用产品的小型化和微型化,制造业将面临越来越多加工微小零件的情况[1]。目前,数控机床作为制造业主要的制造设备,具有效率高、加工能力强等优点,但对于一些价值较低的微小零件来说,常规尺度的数控机床的加工成本较高。针对这样的需求,设计了1台桌面级数控车床,并采用有限元分析方法对初始设计方案进行了优化。桌面级机床的发展是对制造技术和制造装备的有益补充[2],它具有体积小、成本低、结构简单、传动效率高等特点,具有广泛的适用性。
1.车床结构设计
机械结构设计的传统方法需要大量的手工绘图,并根据设计者的经验来确定机械零件的结构。这种方法不仅劳动量大,而且无法科学地考察机械件结构设计的合理性,从而难以在设计初期及时发现设计的不当之处,导致出错率高,容易造成经济上的浪费。随着 CAD 软件的出现和流行,机械结构设计的传统方法逐渐被摒弃,利用功能强大的 CAD 件帮助设计人员完成机械结构的设计成为了现代机械设计的主流方法。利用现代 CAD 软件设计机械结构不仅能有效地避免劳动量大、出错率高、缺乏力学验证等不足,同时也缩短了设计周期、降低了设计成本[3]。Solidworks软件是目前行业内主流的 CAD软件之一,其功能强大,集三维建模、工程图制作、虚拟装配、运动仿真、有限元分析优化等功能于一体,完全能够满足现代机械设计的全部要求[4]。
本文采用Solidworks软件设计了桌面型车床的结构,设计流程框图如图1所示。
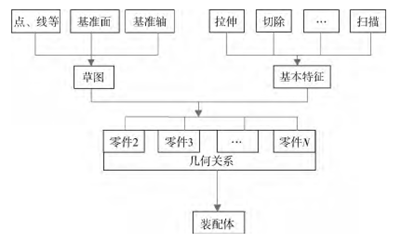
图1 桌面型车床的结构设计流程框图
设计的桌面级数控车床的装配体如图 2 所示。其主要技术参数如下:
1)床身尺寸为580mm×260mm×180mm,中心高为40mm;X、Y 方向行程分别为280 、150mm;选用自定心三爪卡盘,其夹持直径为2~22mm;
2)X、Y 方向分别由1对线性导轨实现其进给运动的导向。设计中选用 THK 超小化设计的 RSR系列导轨,其行走平行度精度可达 0.017 mm。X轴导轨选型为2RSR5N300L,Y 轴导轨选型为2RSR3N160L;选用精密滚珠丝杠作为车床传动件,X 轴丝杠选型为 BNK1202,Y 轴丝杠选型为 BNK1002。
3)主轴传动采取传动比为 1∶1.4的同步带一级传动,减少了许多中间传动机构,降低了传动的误差,提高传动效率;同时,主轴箱的结构简单,整体尺寸较小,符合该桌面型数控机床的设计理念[5]。
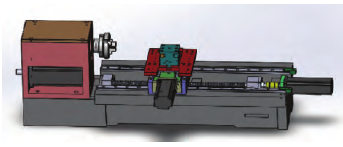
图2 桌面级数控车床装配体的设计原理图
2.基于Solidworks软件的结构分析
Solidworks软件具备优秀的有限元分析能力。可供设计者在制作工程图进入实际加工之前,对所设计的零部件结构进行科学地分析并优化求解,以达到结构最优。采用Solidworks软件进行结构有限元分析的一般流程为前处理、分析计算以及后处理[6]。前处理包括建立有限元模型、添加夹具、添加载荷以及指定材料;分析计算是软件根据设置自动进行网格划分以及计算求解;后处理则包括计算结果的显示与分析,检查其正确性,并可生成分析报表[7]。通过有限元对结构进行分析后,采用 Solid-works软件进一步对结构进行优化。现以床身为例,说明利用该软件对结构进行分析及优化的过程。
床身是机床的基础,本次设计 采用的是 卧式床身结构,并在床身下方布置排屑孔及排屑槽。床身采用优质铸铁整体铸造而成,并合理布置筋板,使床身在具有良好刚性的同时,用料最少,节约成本。另外,设计的床身上的所有加工表面均位于铸造面上部,使之后的加工更加简单;主轴箱安装面与 X 方向导轨安装面的基准一致,能有效保证主轴中心与 X轴平行。床身的前处理过程如图3所示。
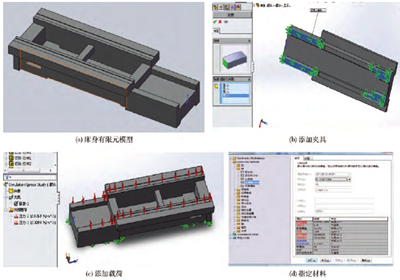
图3 床身前处理过程
1)床身结构的有限元建模图3(a)为桌面型车床床身的有限元模型。 建立其床身有限元模型时,忽略了各处的过渡圆角以及床身上的所有螺栓孔,因为这些结构不会对床身整体的质量及力学性能产生大的影响 ,忽略这些结构能简化模型,提高计算速度[8]。 模型建立完成后,选择Simulation Xpress插件为床身定义算例。
2)添加夹具添加夹具即为分析对象添加固定约束。设计的车床通过床身底部的 4个平面支撑,指定床身的固定约束,如图3(b)所示。
3)添加载荷床身主要受到主轴箱以及进给机构的正压力,通过Solidworks中质量属性估算出主轴箱自重约为178N,进给机构自重约为163N。分别为主轴箱支撑面和导轨安装面添加正压力为14.350、13.008kPa,如图3(c)所示。
4)指定材料指定床身材料为灰铸铁,灰铸铁的泊松比为0.27,拉伸强度为151 MN/m2,抗压强度为572MN/m2,如图3(d)所示。
5)分析与计算根据设置的参数,采用 Solidworks对床身结构进行有限元分析计算,模拟床身在工作状态下所受的应力及其变形情况,如图4所示。由结果分析可知:床身所受最大应力出现在床身中部,约为46.209 18kPa;最大应变出现在床身中部两侧,变形量约为2.2×10-4mm。
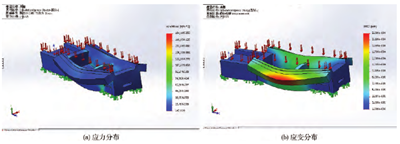
图4 分析结果
3.结构优化
由计算结果可知,床身受到的最大应力远 小于其拉伸强度,且变形很小,其结构还可进一步优化。由床身结构有限元分析的应力分布和应变分布能够看出,床身主轴箱安装部位的应力和应变都最小,故可作为结构优化的重点部位。在有限元分析的基础上,采用 Solidworks软件对结构进行优化,需要指定优化的变量、给定约束条件以及确定优化的目标。本文主要针对桌面级车床的轻量化设计,故指定床身主轴箱安装部位的厚度为变量,以安全系数为约束条件,优化求解的目标为质量最小化。床身结构优化设置和结果如图5所示。指定变量的初始尺寸为20mm,同时人为设置变量的上、下限分别为35和10mm,设置的最小安全系数为2.3。采用Solidworks进行优化求解,优化后变量尺寸为27mm,即主轴箱安装部位的厚度减少了7mm。床身初始质量约为32.862kg,优化后质量约为30.674kg。通过比较可知,优化后的床身结构更加合理,降低了成本。
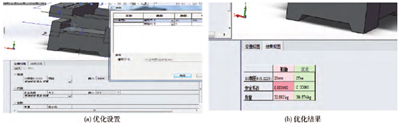
图5 床身结构优化设置和结果
通过对关键部件结构的有限元静力学分析以及结构优化,使设计方案更为合理,最终完成了桌面级车床的设计,并构建了其实体,如图6所示。
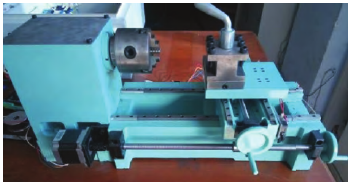
图6 桌面级车床实体
4.结论
1)采用 Solidworks软件进行机械结构设计,便于设计者查看、校对、修改以及表达设计方案,能极大提高设计效率。
2)采用Solidworks软件对结构进行有限元静力学分析,计算出各部件在工作状态下的应力和应变分布情况,供设计者考察结构设计的合理性,同时也为结构优化指明了方向。
3)Solidworks软件 在结构优 化 中 的 应 用,能 帮助设计者科学地优化其设计方案,以追求结构设计的最优化。
投稿箱:
如果您有机床行业、企业相关新闻稿件发表,或进行资讯合作,欢迎联系本网编辑部, 邮箱:skjcsc@vip.sina.com
如果您有机床行业、企业相关新闻稿件发表,或进行资讯合作,欢迎联系本网编辑部, 邮箱:skjcsc@vip.sina.com