基于特征的刀具“形-性-用”一体化设计方法
2017-2-17 来源:哈尔滨理工大学 作者:刘献礼 计伟 范梦超 王昌红
摘要:刀具作为机床的“牙齿”,在金属切削中非常重要,目前专用化是刀具发展的一个主要趋势,挑战刀具设计的灵活性和准确性。为了实现这一目标,提出了刀具“形-性-用”一体化设计方法,它以加工需求为驱动,利用切削过程中涉及的理论(几何约束、切削力作用、切削层作用机理、刀具强度理论、高温材料学属性以及化学反应关系等),并通过刀具设计特征,将刀具的形状、性能和使用结合起来,进而实现针对加工需求的专用刀具设计,以及相应的加工条件和切削参数等的确定。然后建立了刀具“形-性-用”一体化设计方法系统框架,并开发了其软件平台。最后采用示例分析,展示本方法的刀具参数优化过程和刀具建模过程,进而证明本方法的可行性。刀具“形-性-用”一体化设计方法为刀具专用化发展提供一种新方法和新思路。
关键词:刀具设计;刀具形状;刀具性能;刀具使用;刀具设计特征
0.前言
全球制造业的主要特点是:产品更新换代的速度不断提高,产品的种类增加,单件的批量降低,因此当前批生产模式渐渐地不能适应当前的制造业的发展趋势。在刀具行业中,刀具的“专用化”方向是改善刀具性能的一个重要方向,专用化程度提高必然引起刀具种类增加批量降低,因此挑战刀具设计与制造的精准性、灵活性和适应性。目前刀具设计方法主要有基于理论刀具设计、依靠经验的刀具设计及计算机辅助刀具设计。基于理论的刀具设计方法是通过切削过程的理论计算而得到最佳刀具参数,金属切削原理[1]为刀具设计提供了基本的理论指导。师汉民等[2-3]提出金属切削中的“最小能量耗散原理”,为现代切削加工中复杂现象的解释、建模、预测和优化提供了理论基础;并提出以“单元刀具非线性综合法”的方法来建立复杂刀具的切削模型,得出了消除排屑干涉、实现自由切削的充要条件。刘杰华[4]提出刀具精准设计方法,进行了多种刀具的精确设计与计算。许多学者[5-7]建立了刀具的数学模型。理论方法以计算为基础,可以降低试验消耗,但是由于切削过程中存在大量现有理论无法描述的现象,因此达到较高准确性难度较大,还不能满足现代刀具设计需求。
依靠经验和试验的刀具设计方法主要根据刀具磨损、刀具破损及刀具耐用度等基本规律和经验[1,8-9],针对一个或几个目标进行刀具材料选择和刀具几何参数的初步选择,并且进行大量的刀具材料选取试验和刀具参数优化试验[10-11],通过分析试验结果选出最优的刀具参数。这种方法具有一定的准确性,是目前刀具厂家最常用的方法。但是它对于新型工件材料具有盲目性;不能完全地考虑到刀具使用过程中的每个因素;并且易受到试验机床等加工环境的影响,具有不确定性。
计算机辅助刀具设计是将计算机、数据库及软件等技术应用在刀具设计中。刀具设计专家系统是较早的形式,即将刀具设计CAD 与专家系统结合,形成智能化的CAD 设计系统[12]。有学者将数控自动编程语言应用到刀具设计中,保留了作图直观性,又可以发挥计算机所达到的精确性[13]。有限元分析软件在刀具设计中的应用越来越多,缩短了刀具设计的周期[14-16];刀具参数化设计可以自动建模,很大程度上提高刀具设计的效率[17]。计算机辅助设计的应用较为广泛,并且刀具厂家都有软件系统,主要用于刀具建模。而专家系统应对新工件材料的能力有限,有限元仿真的准确性较低直接限制刀具设计质量。
综合分析以上三种刀具设计方法,发现目前刀具设计方法的不足主要体现在:刀具设计过程与切削工艺优化过程是分离的,这样就忽略了刀具、切削条件及刀具切削性能共同对加工的影响。因此,针对以上不足,本文提出刀具“形状-性能-使用”(“形-性-用”)一体化设计方法,并从以下方面进行展开:首先回顾刀具设计的相关研究;通过分析“形”、“性”、“用”之间的关系,提出刀具设计特征以及刀具“形-性-用”一体化设计方法;并在此基础上构建刀具设计方法系统框架,并开发系统软件,并示例分析刀具设计过程;最后总结本文研究贡献及将来的研究计划。
1.刀具“形-性-用”一体化设计方法
刀具“形-性-用”一体化设计方法就是综合考虑刀具“形”、“性”、“用”及其关联,因此需明确它们的关键因素及其关联。
1.1 刀具“形”、“性”和“用”的关键因素
图1 为刀具“形”、“性”、“用”的因素及其关联。刀具用户主要关注加工质量、加工效率和加工成本;刀具厂家为提高刀具性能,主要关注刀具本身,例如,刀具几何、材料、匹配性和制造质量,并为其提高服务水平而关注切削参数、切削条件及刀具使用姿态。目前,刀具厂家刀具设计主要依靠设计人员的经验进行刀具设计,然后利用切削试验验证,而不重视刀具设计中刀具“形”、“性”和“用”三者的关联。
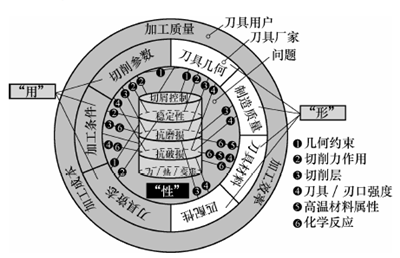
图1 刀具“形”、“性”、“用”之间的关系
(1) 刀具“形”。
刀具“形”是刀具自身特征,包括:① 刀具几何包括刀具的几何参数,刀具的外观尺寸、切削角度、刃口形式及参数等;② 刀具材料是与工件材料对应的刀具材料的种类,主要有PCD、PCBN、硬质合金等;③ 刀具材料和形状的匹配性是指刀具几何参数和刀具材料之间的匹配关系,例如,PCBN刀具常采用倒棱刃口;④ 刀具制造质量包括刀具材料制造质量、稳定性以及刀具加工质量、加工精度等。
(2) 刀具“性”。
刀具“性”是指提供达到加工目标的以切削过程物理现象为基础的刀具基本性能,包括:① 刀具抗破损性能是指刀具的刀杆、刃口等抵抗冲击的能力;② 刀具抗磨损性能是指刀具后刀面、前刀面等抵抗磨损的能力;③ 切屑控制性能是指刀具断屑和排屑的性能;④ 刀具动态性能用来描述当刀具悬伸量较大时,切削过程中刀具保持稳定工作状态的性能。
(3) 刀具“用”
刀具“用”是指刀具的使用条件,包括:① 切削参数为切削速度、切削深度、切削宽度和进给量等;② 工艺条件是指刀具的应用条件,包括冷却条件、冷却液类型和装夹条件等;③ 刀具使用姿态是指刀具在加工同一部位的不同姿态,主要为多轴加工中刀具的摆角。
1.2 刀具“形”、“性”和“用”之间的关联
刀具“形”、“性”和“用”中各个元素之间的关系较为复杂,它们是通过切削理论结合在一起,如图1 所示,包括以下几个方面。
(1) 几何约束关系:用于描述切削过程中存在的刀具、切屑和工件等运动学层面的几何约束关系,例如,切削流动和卷曲。
(2) 切削力作用:研究切削过程中切削力大小、方向以及作用点,通过这一理论可以控制切削过程中的稳定性。
(3) 切削层作用机理:切削实质是剪切滑移的过程,通过摩擦和挤压的方式形成被切削表面,并伴随着力、热和材料变形,因此切削层机理是描述切削过程中的刀具、工件和切屑之间作用。
(4) 刀具和切削刃强度理论:用于描述刀具结构和切削刃的抗御切削力和切削热的性能,刀具强度涉及刀具材料和刀具的结构强度。
(5) 高温材料属性:用于描述在高温条件下刀具和工件材料性能的变化,特别是机械物理性能,直接影响刀具的冲击韧性、抗弯强度、断裂韧性和耐热和导热性等,进而影响刀具的性能。
(6) 化学反应关系:由于切削过程中的高温高压环境,刀具、工件、切削液和空气之间可能发生的化学反应,发生化学反应可能加剧刀具的磨损、降低加工质量,甚至改变被加工件的表面结构。研究加工过程的化学反应可以提高刀具材料、切削液与工件的匹配性,进而改善加工环境。
1.3 刀具设计特征
刀具设计特征是指刀具设计过程中所关注的几何特征,是刀具几何的重要组成部分,与不同刀具类型有关。以整体式球头铣刀为例,如图2 所示,刀具设计特征包括顶刃刃型曲线、顶刃切削刃截面、周刃刃型和周刃截面等。刀具设计特征是刀具设计过程中“形”、“性”和“用”之间的信息载体,它承载了刀具设计所涉及的数据信息。
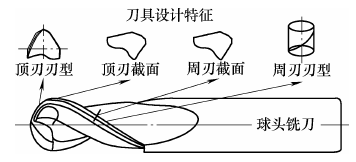
图2 刀具的设计和制造特征
1.4 刀具“形-性-用”一体化设计方法
图3 为刀具“形-性-用”一体化设计方法流程图,分别是刀具“形”,“性”和“用”3 个模块。其中,刀具“用”,用来接收加工信息(MI)和刀具信息(TI),并通过计算得到产生加工条件;刀具“形”模块通过刀具设计特征(TDF)优化和刀具整体优化,确定刀具材料和生成刀具几何形状;刀具“性”模块用来生成与刀具相对应的使用信息。
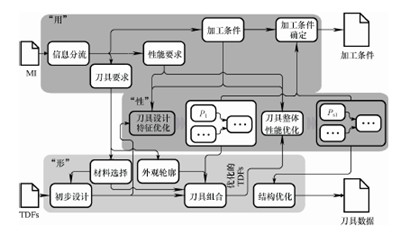
图3 刀具“形-性-用”一体化方法
刀具“用”作为本方法的驱动器,通过接收MI,将其信息进行分类,分别是对刀具“形”的要求(例如,工件材料对刀具材料的要求、工件几何对刀具外轮廓的要求)、对刀具性能的要求(例如,加工表面质量对切削力或切削温度的要求等)、以及对加工条件的要求(例如,加工机床的条件对切削参数的限制等)。然后将整合后的信息分别传给刀具“性”和“形”模块。待接收到刀具“性”模块返回的优化的切削条件信息后,最终确定加工条件。
刀具“形”模块通过接收刀具“用”对刀具要求,进行刀具材料选择和刀具轮廓形成,然后结合TDF,对刀具几何进行初步的设计(这仅仅是满足刀具可制造性的最低要求),形成初步设计的TDF和基本刀具模型;将初步设计的TDF 传递给刀具设计特征优化模块,得到优化后的TDF 和切削条件;刀具“形”模块结合刀具轮廓、基本模型、刀具材料以及优化的TDF,进行刀具组合;然后传递给刀具“性”模块对刀具整体性能进行优化,得到优化的刀具信息(输入到刀具“形”模块)和切削参数信和刀具整体优化,它们的优化流程相似,都是根据来源于刀具“用”模块的要求信息对优化流程进行匹配。要求匹配的原则为:原则1:高重要性优化原则,要求较高的性能刀具性能必须满足,采用优先优化原则;原则2:同等重要的加权原则,这类在优化过程采用加权分配原则。
刀具“ 形- 性- 用” 一体化设计方法通过“形”、“性”和“用” 3 个模块的交互作用,实现刀具形状、性能及使用的统一。
2.刀具设计系统实现
系统架构和软件开发是刀具设计系统实现的两个重要问题,下面对这两个方面分别进行研究:
2.1 刀具“形-性-用”设计方法系统架构
图4 为刀具“形-性-用”一体化设计系统框架,分为3 层,用户层、逻辑层和数据层。整个系统是由加工需求信息驱动,例如,工件的加工特征、材料、加工机床信息及加工要求(质量、效率和刀具成本)等信息。系统得到加工需求信息后,而将TI 传递到TDF 分解模块,将刀具分解为TDF,然后与MI 一起传递给刀具“形-性-用”设计模块,先优化每个TDF,再进行整体优化,得到刀具模型数据;同时优化加工条件和切削参数。将刀具、加工条件和参数数据传递到数据转换模块,将所有数据进行可视化处理,与用户端进行交互,用户可以对以上信息进行修改或确认,最后生成刀具模型和加工条件。由于目前的理论模型无法精确地描述高度非线性的切削过程,因此为了提高整个刀具系统的精度,需建立切削数据库:① TDF 数据库包含所有影响刀具性能的刀具设计特征;② 切削数据库是验中刀具磨损、刀具破损、切削力和切削温度等方面试验数据,为刀具、加工条件参数的确定提供指导;③ 知识库包含基本知识,例如刀具基本几何参数、基本刀具材料信息等。
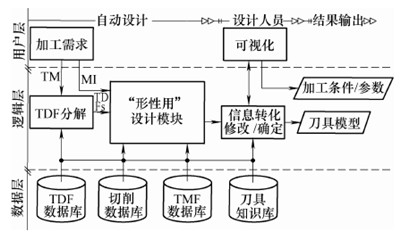
图4 基于刀具设计方法模型
2.2 刀具设计系统软件开发
采用C#编程语言编辑开发刀具设计系统的软件,其界面如图5 所示,包含7 个模块,其作用如下。
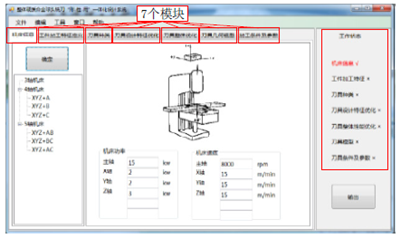
图5 刀具“形-性-用”一体化设计系统界面
(1) 机床信息模块:用于收集加工机床的信息,可以选择不同的机床结构、主轴及其他轴的功率和速度等信息。
(2) 工件加工特征定义:用于确定被加工工件的几何特征以及相关的物理特征,例如,工件的型面类型和硬度等;并且确定加工要求,例如加工表面质量和加工效率等。
(3) 刀具种类:用于确定刀具种类(普通球头铣刀和锥球头铣刀等)以及刀具的基本尺寸(刀具直径和长度等)。
(4) 刀具设计特征优化:用于优化刀具设计特征参数,根据不同的加工要求,确定每个设计特征的优化步骤,并得到刀具设计特征和切削条件及参数的初步优化范围。
(5) 刀具整体优化:用于对刀具整体性能进行优化,例如刀具动态性能和刀具的强度等;同时可以确定切削条件及参数的范围。
(6) 刀具几何模型:通过对刀具设计特征优化和刀具整体性能优化,确定刀具几何参数,并通过本模块展示刀具几何模型,进行修改、添加刀具特征及其参数,进而确定刀具几何模型。
(7) 加工条件及参数:通过刀具设计特征优化和刀具整体性能优化,展示切削条件及参数的范围,并进行修改或确定。
3.示例分析
刀具设计方法的准确性依赖于切削数据库的数据量及其准确性,由于目前并没有这种数据库,通过刀具设计实例与刀具性能评价来验证本文刀具设计方法困难较大。因此本节重点展示刀具设计过程中刀具参数和切削参数的传递过程,进而证明刀具设计方法的可行性。
以淬硬钢模具拐角精加工用球头铣刀设计为例说明刀具“形-性-用”一体化设计方法设计刀具的流程。图6 为带有拐角结构的淬硬钢模具,其中A-A 截面是拐角壁高度最大的位置,其高度为50mm,其加工需求信息和刀具信息如表1 所示。
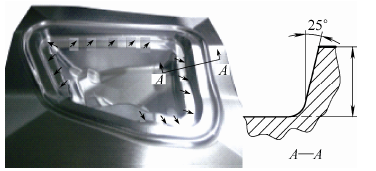
图6 模具拐角加工
表1 加工需求表
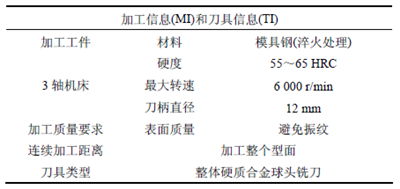
根据刀具设计系统,通过TDF 分解整体硬质合金球头铣刀被分为顶刃刃型、顶刃截面、周刃刃型和周刃截面等;然后这些TDF 和MI 一起进入“形性用”设计模块。
3.1 刀具“用”模块信息分配
刀具“形性用”模块中的“用”根据不同信息种类,进行信息分流:
3.1.1 对刀具“形”的要求
根据不同工件的材料属性(硬度、韧性等),选择最适合刀具基体和涂层材料。在数据库中有相应的数据表,如表2 所示,不同属性的工件材料对应着最适合的刀具基体和涂层材料。淬硬钢模具工件材料的硬度为55~65 HRC,工件材料硬度高,要求刀具材料具有高硬度和韧性,根据数据表选择超细晶粒硬质合金基体和TiAlCN 涂层。
表2 工件刀具材料对照表
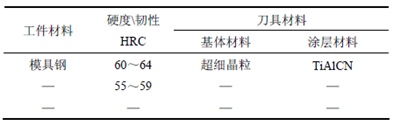
由于采用3 轴机床加工拐角,根据加工尺寸要求,为了防止加工干涉,刀具悬伸量需大于50 mm,记做Pcoa。
3.1.2 对刀具性能的要求
工件材料硬度高要求切削刃保持性高,即刀具切削刃的强度要高,同时切削过程中作用在切削刃的冲击力要低。连续加工距离要求是对刀具具有一定的寿命,即对刀具抗破损和抗磨损性的要求。工件拐角加工要求刀具具有高整体强度和刚性以避免刀具折断和切削振动过大。表面质量避免振纹是要求刀具切削过程平稳,即,使作用在刀具径向的切削力尽量小。
3.1.3 对加工条件的限制
工件材料为淬硬钢,则切削过程不能使用切削液。采用3 轴机床加工,因此球头铣刀刀具的摆角为0°;机床转速最大n 为6 000 r/min,根据公式,切削速度c v , ( ) c 1 000 π c v n = n D ( c D 为刀具直径),故( ) c c v ≤ v 6 000 。将以上两部分记为 ca P ,即加工条件和参数优化的边界条件。
3.2 刀具“形”模块的刀具初步设计
刀具“形性用”模块中的“形”得到刀具材料信息,根据数据库中刀具材料与刀具几何参数的关系,如表 3 所示,本文的超细晶粒硬质合金基体材料对应的刀具切削刃参数范围为cei P ,刀具整体参数范围为coi P 。
表3 刀具材料与刀具几何的关系

3.3 刀具“性”模块优化刀具设计特征
刀具设计系统中“性”模块基于刀具“用”对性能要求优化刀具设计特征,主要为切削刃截面,其主要指标为切削刃强度和耐磨性。即,保证切削刃具有一定的切削刃抗破损性能的基础上保证切削刃具有高耐磨性。
3.3.1 抗破损性优化
加工高硬度工件材料刀具切削刃截面常采用倒棱形式,如图7 所示,这种切削刃可以一定程度上提高刀具的切削刃强度(加工高硬度材料主要体
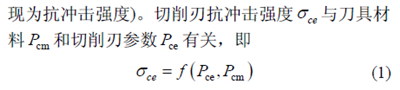
而切削过程的冲击载荷Fc与切削参数、工件材料属性有关(式2);并且冲击载荷与切削刃强度之间存在一定的关系才能保证刀具正常工作。
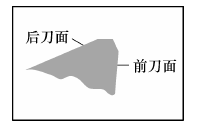
图7 刀具切削刃的截面示意图
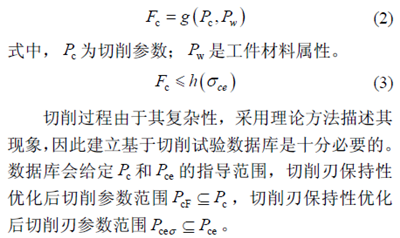
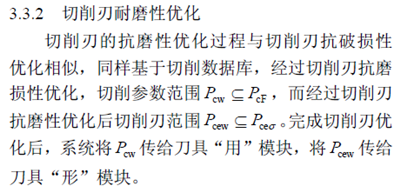
3.4 刀具“性”模块的刀具整体优化
整体刀具性能的主要指标为:刀具整体强度和刀具动态性能。
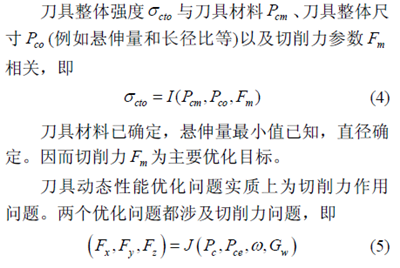
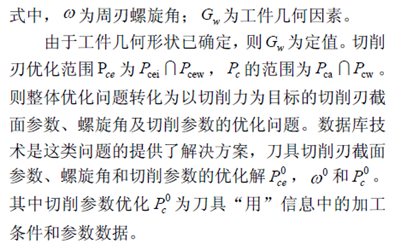
3.5 刀具“形”模块生成刀具模型
刀具参数优化后,刀具“形”模块在刀具几何方程的基础上可生成刀具模型。以球头铣刀端刃为例,说明刀具“形”模块生成刀具模型。首先建立坐标系,以刀具顶刃所在球的球心为原点,轴线为z 轴(图8),基于切削刃截面参数、刀具直径、螺旋角,建立刀具倒棱面、前刀面和后刀面方程[18]。
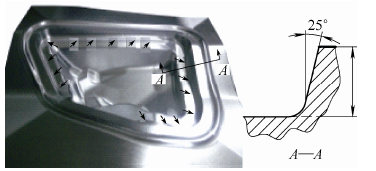
图8 刀具模型以及坐标系
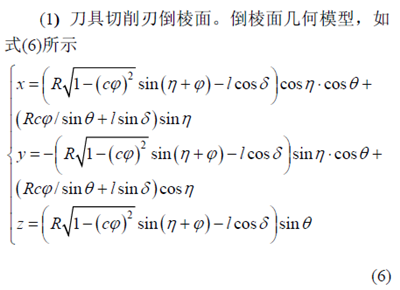
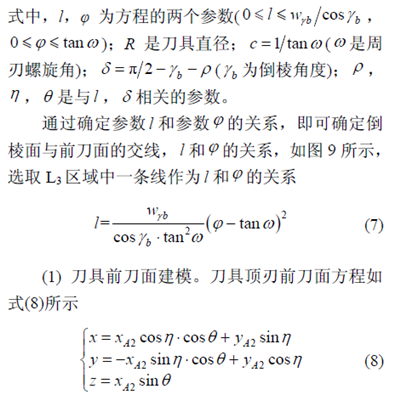
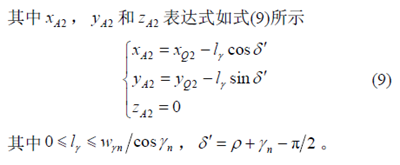
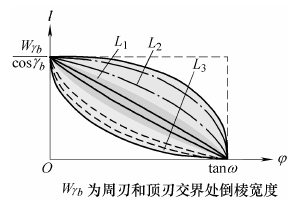
图9 参数l 和? 的关系图

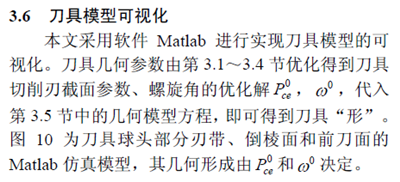
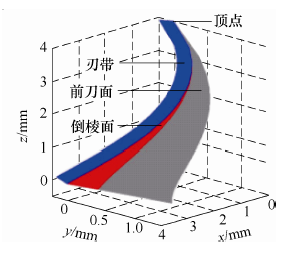
图10 刀具模型生成
4.结论
为了应对刀具专用化的发展趋势,本文充分考虑刀具的形状、性能与使用的三者之间的相互关联,提出一种基于特征的刀具“形-性-用”一体化设计方法。其中,刀具设计特征是整个设计系统的信息载体,体现了刀具“形”、“性”和“用”三者交互作用;刀具设计方法通过设计系统发挥作用,本文的刀具设计系统为三层结构,用户层、逻辑层和数据层。用户层可以用户进行交互,接收加工信息,确定刀具参数和加工条件等;逻辑层是“形-性-用”设计体系的数据传递模型;数据层基于切削数据库,为刀具设计的准确性提供保障。在此基础上开发了刀具设计软件。通过示例分析展示了刀具设计系统的刀具参数优化过程和刀具模型的生成的工作流程,进而证明本方法的可行性。进一步推进刀具“形-性-用”一体化设计方法的进程的主要挑战如下。
(1) 为搭建设计系统,需要完善现有切削理论体系使其适用于本系统,例如,建立以优化切削力分配为目标的切削参数、刀具参数的理论模型。
(2) 为完善刀具“性”模块中刀具设计特征、整体性能优化,需要研究性能要求匹配流程方法以及参数优化算法,并且确立其边界条件。
(3) 为提高刀具设计的精度,需要建立大量的数据库,因此数据结构优化算法研究对刀具设计系统的发展非常重要。
下一步研究中攻克以上问题,完善刀具“形-性-用”一体化设计的软件平台,并且应用在淬硬钢模具加工用刀具设计中。
投稿箱:
如果您有机床行业、企业相关新闻稿件发表,或进行资讯合作,欢迎联系本网编辑部, 邮箱:skjcsc@vip.sina.com
如果您有机床行业、企业相关新闻稿件发表,或进行资讯合作,欢迎联系本网编辑部, 邮箱:skjcsc@vip.sina.com
更多相关信息