基于ABAQUS 的数控车床刀具刀架的有限元分析
2016-12-7 来源:辽宁建筑职业学院机械工程 作者:纪海峰
摘 要:在切削加工中,刀具的刚度、强度以及产生的共振等问题都会影响加工精度,是机械机构设计研究时不可忽视的问题,利用有限元分析软件ABAQUS 对在粗车时对刀具的刚度和强度进行了静力学分析,对刀具刀架进行了模态分析,得到刀具刀架的前4 阶固有频率和振型,并验证了刀具和刀架的设计均合理,所使用的研究方法为今后验证类似模型验证提供了参考依据。
关键词:数控车床;刀具刀架;ABAQUS;有限元分析
0.引 言
在车削加工中,刀具的刚度和强度是保证加工精度的重要原因之一,在加工过程中工件及刀架系统的变形而产生的低频振动和因频率接近车刀的固有频率而使车刀发生变形的高频振动均是产生振动的原因[1] 。这会使加工精度大大降低,使加工后的工件尺寸产生较大误差,同时也会直接影响车床的稳定性。因此有必要对刀具和刀架进行模态分析,从而加深对其动态特性的进一步了解。
笔者主要以CAK40100 数控车床上的刀具刀架为研究对象,通过使用ABAQUS 软件对刀具刀架进行有限元静力分析和模态分析,对刀具的刚度和强度进行分析,同时找出刀具刀架的共振频率,并通过机床的共振频率来对结果加以验证。
1.车刀有限元静力分析
对工件加工的过程中,刀具质量和性能的优劣对工件的加工精度有着十分重要的影响。这样对刀具的分析则显得十分必要。接下来就以车刀为例,使ABAQUS 软件对车刀进行静力分析和模态分析,获得车刀受力后的参数、固有频率和振型,并对结果进行分析和验证。
1. 1 车刀选择
本次选用的数控车刀为55°的偏刀,其组成为可转位刀片,刀杆和螺钉,并使用Pro/ E 软件完成了对刀具的建模,车刀的组装图如图1 所示。该车刀的主要物理特性参数如表1 所示,其中刀杆材料为钢,可转位刀片材料为WC 硬质合金。
表1 可转位车刀主要的物理参数表
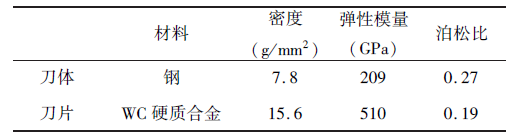
1. 2 模型导入
为了避免在模型导入后的网格划分阶段出现问题,需要对车刀模型进行简化,将其上面所有的倒圆角去掉,并且将螺钉部分进行省略,简化之后的车刀模型如图2 所示。简化后将其保存成Parasolid(?. x_t)格式,以备后续调用。
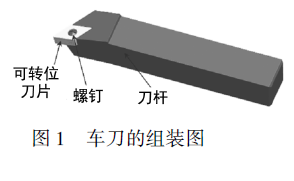
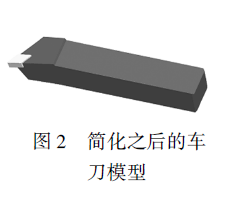
1. 3 网格划分
对车刀的网格划分使用四面体单元来进行划分。在划分的过程中,主要受力部分的网格需要对其进行详细划分,由于刀尖受力较复杂且为了今后能够更好的对其进行分析,所以刀尖部分的网格划分需要十分详细。由于刀杆部分是固定的,受力相对简单,且考虑到应尽量的节省计算机的资源,所以在对刀杆部分简化处理,这样完成整体网格划分的刀具如图3。
1. 4 刀具受力分析
在车削加工工件的过程中,车刀主要受两种外力:第一种是在生成切屑的过程中,所发生的弹性和及塑性变形对车刀所产生的抗力,第二种是切屑和工件表面对车刀的阻力,它作用在前刀面和后刀面上,但是对于尖锐的刀具来说,作用在前刀面的切削力是主要的,作用在后刀面的力所占的比例很小[3] ,所以在大切深的时候,可近似的认为前刀面的作用力约等于切削力。车削时刀具受力分析如图4 所示[4] 。
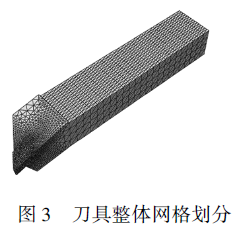
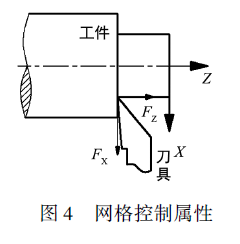
在车削过程中,考虑到低转速,大切深的情况下是切削力最大的极限工况,所以选择粗车的情况来进行分析,粗车时相关参数如表2。由于模拟的是刀具所受的轴向力最大的极限情况,所以刀具主要受轴向力作用,即刀杆固定,刀尖处主要施加轴向载荷。
表2 粗车时的各项参数
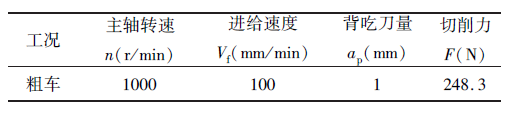
1. 5 结果分析
通过ABAQUS 软件分析可知在粗车的工况下:粗车的静态分析刀尖处是应力、应变最集中地地方,同时发生位移也最大,其最大应力为4. 984e+3 MPa,即4 984 MPa;最大位移量为1. 662e-01 mm,即0.166 2 mm;最大应变1. 366e-02,车刀各项分析结果如图5 所示。从分析结果可看出,在粗车时最大位移和最大应力均发生在刀尖处,应力值为4 984 MPa,已经非常接近5 460 MPa,但在其允许范围内。最大位移为0. 166 2 mm,位移量也十分微小,而应变为0.013 66,非常微小可以忽略不计,所车刀是合格的。
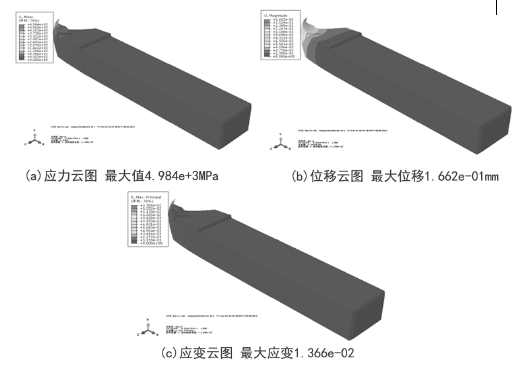
图5 车刀各项分析结果
通过本次分析可以看到,当粗车时如果一些参数没有调整好,很可能会发生刀具破坏即崩刀现象,这与实际的加工情况吻合,所以在进行粗车时进给量不应过大,以避免出现崩刀现象,从而影响加工。
模态分析理论
假设结构的自由度为N,则结构的其矩阵形式如下所示[5-8] :
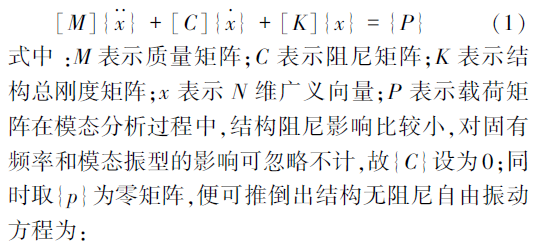
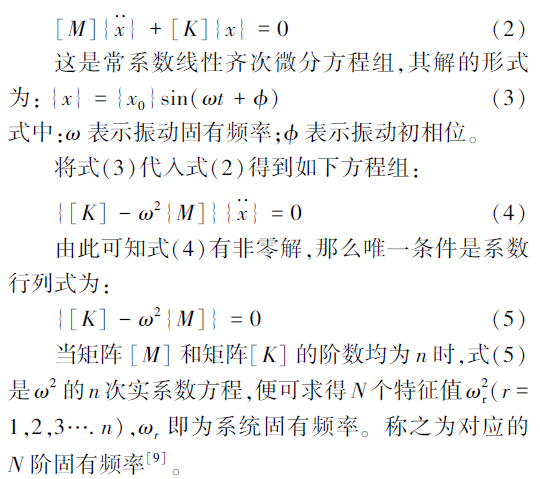
2.刀具刀架的有限元模态分析
2. 1 刀具刀架三维模型的建立
刀具刀架可看做是一个系统的模态分析,主要任务是计算其固有频率和振型,由于刀具刀架零件比较复杂,适当的处理简化可以减少计算机运算资源,因此在进行模态分析前对刀具刀架零件模型进行了相应的简化处理,将刀具刀架三维模型导入ABAQUS软件后生成的刀具和刀架模型如图6 所示。
2. 2 刀具刀架有限元模型的建立
接下来使用ABAQUS 软件来模拟所建立的刀具刀架模型的模态分析,在属性中将刀头、刀杆和刀架的各项物理特性(如密度、弹性模量和泊松比等)如表3 所列,并参数输入到属性里。
表3 刀具刀架主要的物理参数表
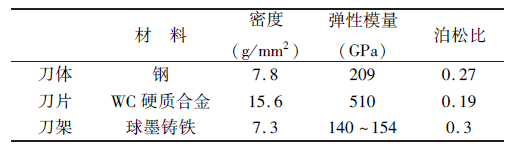
对刀具刀架的三维模型进行网格划分,选用四面体单元来对主轴进行网格划分,在进行网格划分的过程中,一些关键的地方需要进行更加细致的网格划分,这样才能将分析的结果与真实加工的情况更加贴切。在加工过程中,刀具的刀尖部分受力是最主要的,所以需要更加详细的来进行划分,刀架顶部的属于非受力和变形区域,所以网格可划分密度较低,划分完毕的刀具和刀架的网格划分模型如图7 所示。
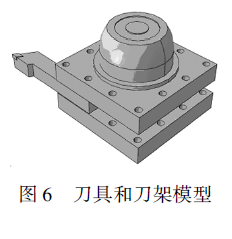

3.刀具刀架的有限元模态分析
对刀具刀架进行模态分析,为了与实际的加工工况相一致,在对其进行受力分析的过程中,在刀架的底部施加边界条件,对其进行约束,以模拟真实加工中的载荷情况。分析完毕后,取前4 阶结果,如表4。经过分析计算后,所得前4 阶的振型图如图8。
表4 刀具刀架分析结果
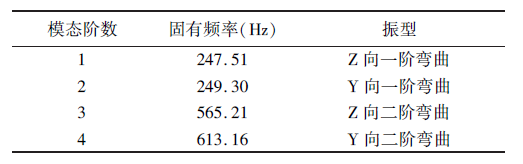
通过对以上的频率进行分析,在第1 阶和第2阶,刀具的独立振动较大,从第3 阶开始刀具和刀架均发生比较大的振动,所以在对其进行模态分析的时候,首先分析较低阶的模态。已知转速与频率的关系为:n =60 f,式中,n 为转速,f 为频率。处于对安全性能考虑,要求刀具和刀架的最高转速应低于1 阶临界转速的75%。从表4 中可得,其1 阶的临界转速的75%为60×247. 51×0. 75 =11 137. 95 r/ min,而本车床最高转速为2 500 r/ min,远远低于1 阶的临界转速,说明刀具刀架的设计也是合理的,并能够避开共振区,保证加工精度。
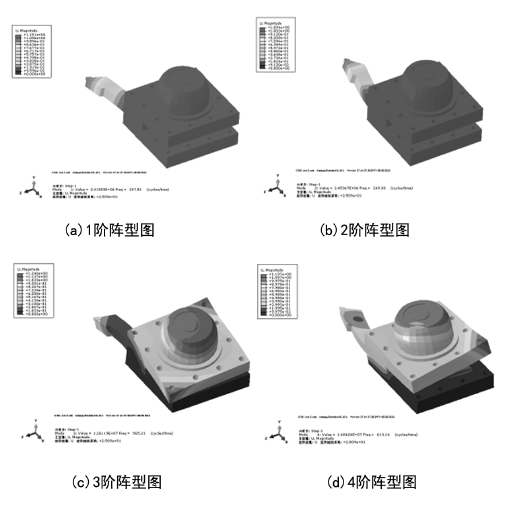
图8 前4 阶各阶的阵型图
4.结论
介绍了使用ABAQUS 软件对刀具进行静力分析,通过刀具的应力、应变和位移云图的分析对其刚度和强度进行了验证,同时又对刀具刀架进行了模态分析,计算了刀具刀架的固有频率和振型, 并通过对固有频率和振型的分析, 得到了刀架系统在切削过程中容易发生共振的频率范围,同时也验证了原有的刀具刀架设计的合理性,为今后进一步的动力学研究提供了依据。
投稿箱:
如果您有机床行业、企业相关新闻稿件发表,或进行资讯合作,欢迎联系本网编辑部, 邮箱:skjcsc@vip.sina.com
如果您有机床行业、企业相关新闻稿件发表,或进行资讯合作,欢迎联系本网编辑部, 邮箱:skjcsc@vip.sina.com