主轴一刀柄和刀柄一刀具结合面参数对稳定性Lobe图的影响
2016-10-25 来源:常州信息职业技术学院机电学院 作者:王二化 吴波 胡友民 杨叔子
摘要:为探索主轴一刀柄和刀柄一刀具结合面参数与立铣加工过程稳定性的关系,以主轴一刀柄和刀柄一刀具结合面参数辨识方法和两自由度立铣加工过程动力学模型为基础,研究了主轴一刀柄,以及刀柄一刀具结合面参数等因素对稳定性Lobe图的影响。结果表明:主轴一刀柄和刀柄一刀具结合面的直线刚度对稳定性Lobe图的影响最大,其他结合面参数对稳定性Lobe图均有不同程度的影响;和主轴一刀柄结合面参数相比,刀柄一刀具结合面参数尤其是转动刚度对稳定性Lobe图的影响更大。
关键词:立式铣削;结合面;颤振;Lobe图
0.前言
随着制造技术的不断发展,高速切削日益成为制造行业中的一项关键技术,在减少工件变形、提高产品质量和加工效率方面具有无可比拟的优越性。目前,加工过程稳定性问题,特别是切削颤振已经成为制约高速切削技术快速发展的一个重要因素,它不仅会限制机床的生产率,而且会严重影响工件表面质量,大大加剧刀具磨损,极端恶化工作环境。其中,颤振和稳定状态下加工的产品表面如图1所示。
图l表明,和稳定状态相比,颤振状态下加工的工件表面有明显切痕。因此,为提高立铣加工过程稳定性,通常利用稳定性Lobe图来确定切削过程中稳定和不稳定的切削区域。作为切削宽度和主轴转速的函数,稳定性Lobe图可以帮助机床操作人员选择合适的切削参数。稳定性Lobe图一般通过分析或数字时域方法得到,不管使用什么方法,都需要预先获取机床的动力学知识。对于两自由度立铣加工过程动力学模型来说,机床的动力学知识就是机床刀尖频响函数。目前,机床刀尖频响函数主要通过动柔度耦合子结构分析方法(Receptance Coupling SubstructureAnalysis,RCSA)计算,可以大大减少模态锤击法的实验次数。
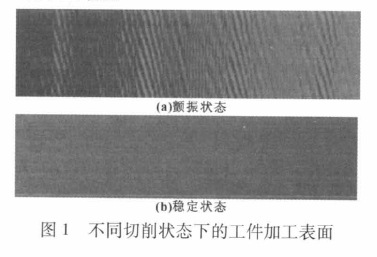
研究表明,在利用RCSA方法进行机床刀尖频响函数预测过程中,主轴一刀柄和刀柄一刀具结合面参数的变化可以直接影响机床刀尖频响函数,进而影响加工过程稳定性Lobe图。
文中在前期主轴一刀柄和刀柄一刀具结合面参数辨识方法¨0]研究基础上,通过理论计算和实验方法,重点分析各个结合面参数对稳定性Lobe图的影响。
1.主轴一刀柄和刀柄一刀具结合面参数辨识模型
基于Timoshenko梁理论、传递矩阵法和RCSA耦合算法,预测立式铣床刀尖频响函数,以预测与实验刀尖频响函数之间的误差为目标函数,建立主轴一刀柄和刀柄一刀具结合面参数辨识模型。首先,根据立式铣床主轴箱结构封闭的特点,本研究不考虑主轴和轴承之间的弹性支撑,将立式铣床分解成主轴装配体、刀柄和刀具3个子结构,如图2所示。
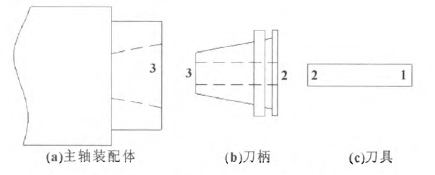
图2主轴装配体、刀柄和刀具子结构
在以上3个子结构中,主轴装配体端点频响函数通过锤击方法获取。利用Timoshenko梁理论建立刀柄和刀具动力学模型,通过传递矩阵法计算刀柄和刀具子结构的各个端点频响函数。得到主轴装配体、刀柄和刀具各个子结构端点频响函数后,利用直线、转动弹簧和阻尼单元将3个子结构连接起来,建立主轴装配体一刀柄一刀具的耦合模型如图3所示。
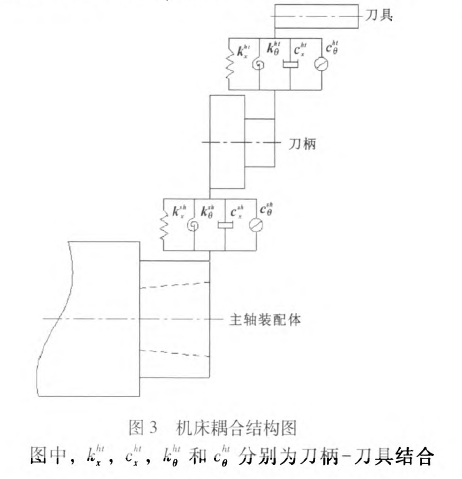
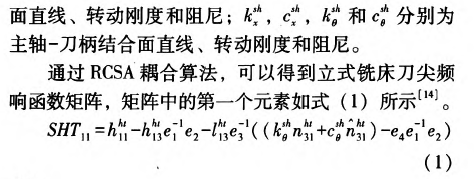
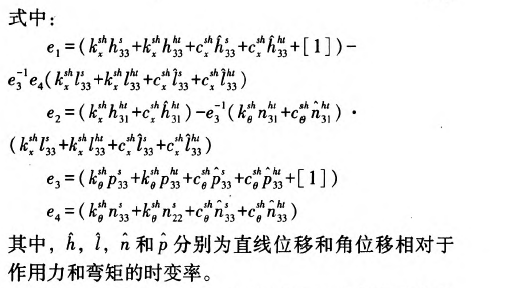
式(1)中,主轴一刀柄和刀柄一刀具结合面参数通过向量表达如式(2)所示。

假设在感兴趣的频带有m个频率测试点,可以构造误差向量如式(3)所示。
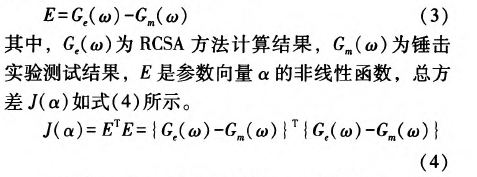
以总方差J(a)为目标函数,以参数向量“为优化参数,通过粒子群和局部搜索优化算法¨刮求解全局最优解,最优解即为需要辨识的主轴一刀柄和刀柄一刀具结合面参数。
2.立铣加工稳定性Lobe图预测
根据实际加工过程,建立两自由度立铣切削过程动力学模型如图4所示。
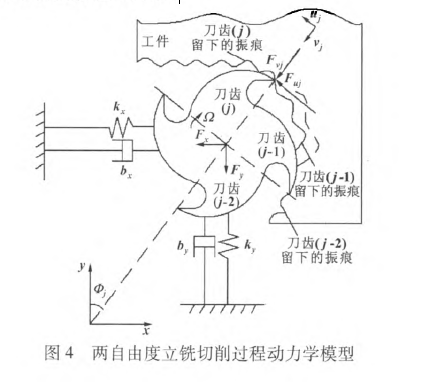
切削系统在x和Y轴方向的动力学方程如式(5)和(6)所示。

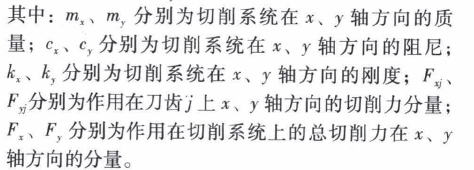
以立铣加工过程动力学模型和切削力理论为基础,结合立式铣床固有的振动特性,可得轴向切深临界值如式(7)所示。
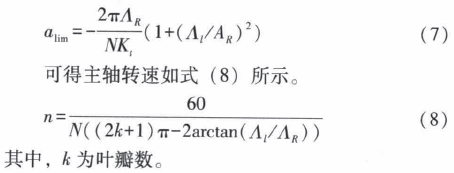
根据上述公式分别计算临界轴向切深及对应的主轴转速,在颤振发生频率范围内重复以上过程,可得立铣加工过程颤振稳定性lobe图。具体步骤如下:
(1)通过本研究提出预测方法,获取机床刀尖频响函数;
(2)在机床刀尖频响函数中,选择主模态附近的颤振频率;
(3)求解动态铣削系统的特征值;
(4)计算临界切深及对应的主轴转速;
(5)在设定的颤振频率范围内,重复上述过程。
3.立铣加工稳定性Lobe图仿真及实验研究
以DM4600立式铣床为研究对象,进行结合面参数辨识及机床刀尖频响函数预测和振动测试,并完成切削颤振实验研究。所用刀柄和刀具尺寸如图5所示。
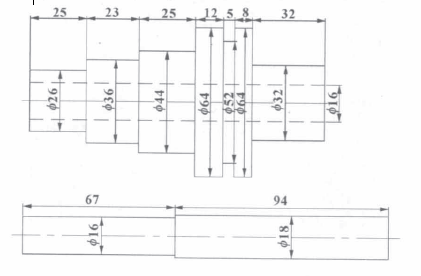
图5 刀柄和刀具尺寸
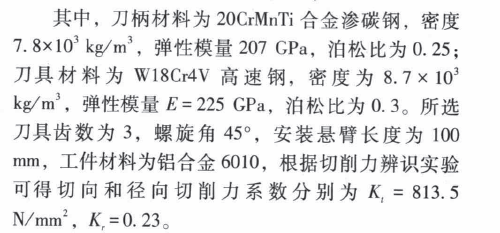
根据上述方法,可得主轴一刀柄和刀柄一刀具结合面参数辨识结果如表l所示。
表1 结合面参数辨识结果

预测与测试的机床刀尖频响函数如图6所示。
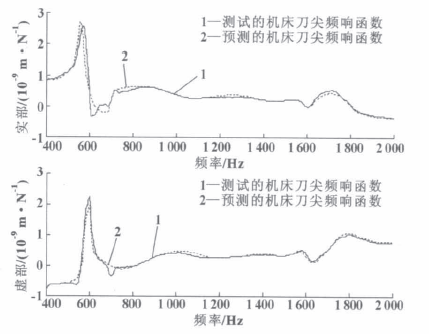
图6预测与测试的机床刀尖频响函数
将辨识得到的主轴一刀柄和刀柄一刀具结合面参数代入到机床刀尖频响函数预测模型中,可以得到预测的机床刀尖频响函数,将预测得到的刀尖频响函数和激振实验测试得到的刀尖频响函数进行比较,结果如图6所示。
图6显示,除600 Hz附近有一些波动外,预测和测试得到的机床刀尖频响函数一致性较好,说明辨识出的结合面参数具有较高精度。立铣加工过程实验装置如图7所示。
如图7所示,首先将测力仪装夹在工作台上,并通过螺钉将铝合金工件与测力仪连接,通过测力仪获取切削力系数和切削过程的动态铣削力;为了进一步区别颤振状态和强迫振动状态,将两个三向PCB传感器分别固定在主轴的算和Y轴方向,监测铣削过程

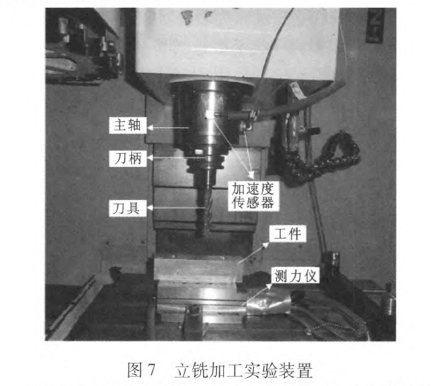
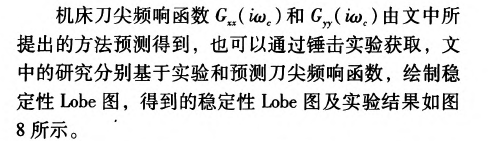
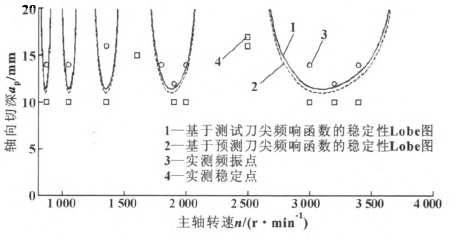
图8立铣加上稳定性Lobe图与实验结果
由图8可以看出,基于预测和实验刀尖频响函数的稳定性Lobe图总体趋势一致,但在主轴转速一定的前提下,预测极限切深小于实验极限切深。说明,根据预测稳定性Lobe图选择切削参数,可以保证切削过程的稳定性,但轴向切深选择有些保守,会在一定程度上影响加工效率。此外,可以看出,颤振稳定性Lobe图预测结果与实测稳定、颤振点非常一致,具有较高精度。
4.主轴一刀柄和刀柄一刀具结合面参数对稳定性Lobe图的影响分析
4.1主轴一刀柄结合面参数对稳定性LDbe图的影响分析
保持其他参数不变,仅改变主轴一刀柄结合面直线、转动刚度和阻尼参数,并利用传递矩阵法和RC.sA相结合的方法预测刀尖频响函数,最后,通过上述方法计算立铣切削过程稳定性Lobe图,结果如图9-12所示。
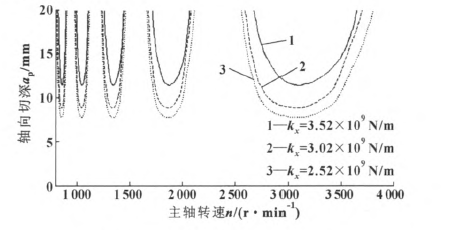
图9不同主轴一刀柄结合面直线刚度条件下的稳定性Lobe图
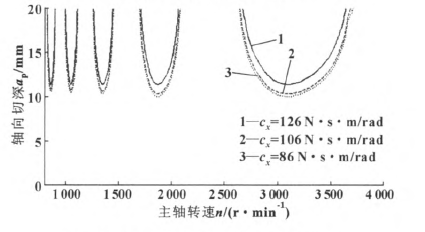
图10不同主轴一刀柄结合面直线阻尼条件下的稳定性Lobe图
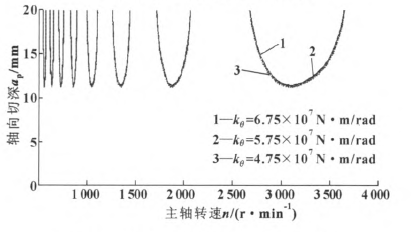
图11 不同主轴一刀柄结合面转动刚度条件下的稳定性Lobe图
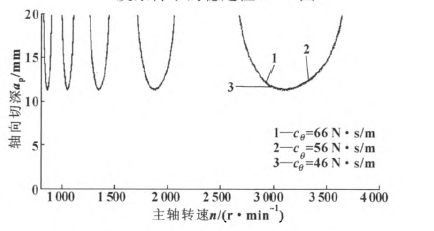
图12不同主轴一刀柄结合面转动阻尼条件下的稳定性Lobe图
由图9可以看出,随着主轴一刀柄结合面直线刚度的连续减小,极限轴向切深a。不断降低,在较低转速区域和较高转速区域降幅一致,并且降幅较为明显,说明主轴一刀柄结合面直线刚度对刀尖频响函数影响较大,因此,为了提高切削过程稳定性,在机床研发和制造过程中,应尽可能提高主轴一刀柄结合面直线刚度。由图10可以看出,随着主轴一刀柄结合面直线阻尼的增大,极限轴向切深口。也不断增加,因此,可以通过增加阻尼器的方法抑制颤振,保证高速切削过程的稳定进行。由图11和12可以看出,主轴一刀柄结合面转动刚度和阻尼对稳定性Lobe图几乎没有影响,这主要归因于转动刚度和阻尼对机床刀尖频响函数的影响微乎其微,基本可以忽略不计。因此,如果想通过改变主轴一刀柄结合面转动刚度和阻尼,提高切削过程的稳定性是不可能。
4.2主轴一刀柄结合面参数对稳定性Lobe图的影响分析
同样,其他参数保持不变,分别改变刀柄一刀具结合面直线、转动刚度和阻尼,并基于传递矩阵法和RCSA相结合的方法预测刀尖频响函数,最后,通过上述方法计算立铣切削过程稳定性Lobe图,结果如图13一16所示。
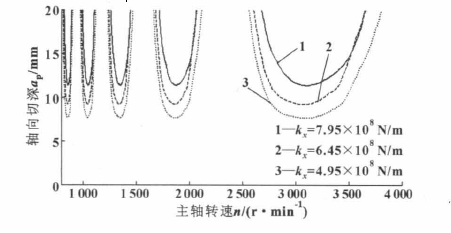
图13不同刀柄一刀具结合面直线刚度条件下的稳定性Lobe图
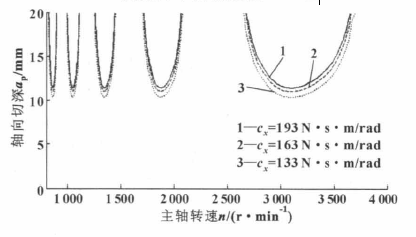
图14不同刀柄一刀具结合面直线阻尼条件下的稳定性Lobe图
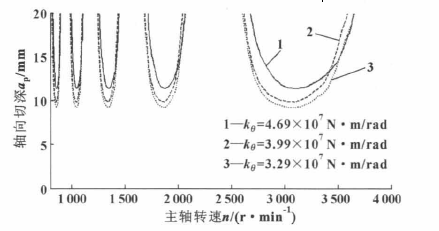
图15不同刀柄一刀具结合面转动刚度条件下的稳定性Lobe图
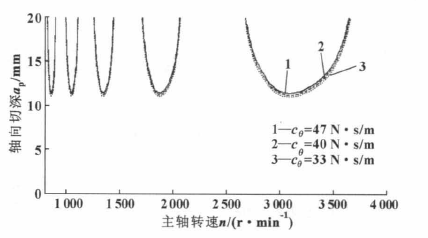
图16不同刀柄一刀具结合面转动阻尼条件下的稳定性L0be图
由图13可以看出,和主轴一刀柄结合面直线刚度类似,刀柄一刀具结合面直线刚度越大,极限轴向切深o。也越大。图14表明,其他条件保持不变,增大刀柄一刀具结合面直线阻尼,可以提高切削过程的稳定性。由图15可以看出,刀柄一刀具结合面转动刚度的降低,也会引起极限轴向切深Ⅱ。的减小,并且减幅较大,这点和主轴一刀柄结合面转动刚度不太一样,主要因为,刀具通过结合面和刀柄直接相连,转动刚度可以直接影响刀尖频响函数,并进而影响稳定性Lobe图,因此,也可以通过增加刀柄一刀具结合面转动刚度,提高切削过程的稳定性。由图16可以看出,刀柄一刀具结合面转动阻尼的减少,也会引起极限轴向切深口。的减小,但影响比较小,对实际切削过程意义不大。
5.结论
在前期主轴一刀柄和刀柄一刀具结合面参数辨识方法研究基础上,通过理论计算和实验方法,重点分析了各个结合面参数对稳定性Lobe图的影响。研究结果表明,主轴一刀柄和刀柄一刀具结合面的直线刚度对稳定性Lobe图的影响最大,其它结合面参数对稳定性Lobe图均有不同程度的影响。此外,和主轴一刀柄结合面参数相比,刀柄一刀具结合面参数尤其是转动刚度对稳定性Lobe图的影响更大。
投稿箱:
如果您有机床行业、企业相关新闻稿件发表,或进行资讯合作,欢迎联系本网编辑部, 邮箱:skjcsc@vip.sina.com
如果您有机床行业、企业相关新闻稿件发表,或进行资讯合作,欢迎联系本网编辑部, 邮箱:skjcsc@vip.sina.com