基于动态特性分析的KVC800立式加工中心运行优化研究
2016-9-6 来源: 湖南科技大学机械设备健康维护省重点实 作者:蒋玲莉 谭清雅 唐思文
摘要:在数控加工中心设计之初常会考虑固有频率的影响,但由于加工过程中不可避免的误差,对已投入使用的数控加工中心开展动态特性分析,掌握其各阶模态,对于优化加工中心的运行仍必不可少。对KVC800立式加工中心开展了ANSYS有限元模态分析、锤击法试验模态分析以及升速过程中振动信号的瀑布图分析,通过相互对比与验证,发现加工中心存在工作转频内的低阶模态。切削动态测试验证在此低阶模态下工件加工精度略低,为加工中心的优化运行提供了可靠依据。
关键词:立式加工中心;有限元分析;模态试验;瀑布图;动态特性
数控机床是机械行业中的重要工具之一,是现代制造业的关键设备[1]。随着机床加工行业的迅速发展.对加工中心的加工性能及加工精度要求越来越高,对加工中心进行动态分析是提高加工中心的加工性能与加工精度的有效途径。加工中心在加工工件时产生的振动和形变都会对被加工对象的加工精度产生很大的影响,从而降低机床的加工效率以及刀具的使用寿命,更严重的是影响到机床的寿命。因此,对在线加工中心进行动态特性研究是优化加工中心运行的重要手段之一。
文中的研究对象是KVC800滑鞍型立式加工中心(见图1)。该加工中心结构主要由工作台、床身、床鞍、立柱、主轴箱及刀库六大部分组成,工作台作纵向进给,床鞍作横向进给,主轴箱作垂向进给运动,3个进给方向导轨均为矩形导轨,电机带动滚珠丝杠通过导轨实现3个方向的运动。对其动态特性进行分析,对比有限元结果以及试验结果,获取优化加工中心运行的工作参数。
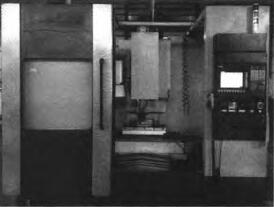
图1 KVC800立式加工中心
1、加工中心有限元振型分析
建立加工中心结构模型以及对其进行有限元分析是研究加工中心动态特性的前提工作㈨。由于加工中心结构复杂,通过合理地简化结构并使用SolidWorks建模软件完成其部件有限元模型的绘制。再将其导人ANSYS Workbenchl4.5软件中进行模态分析,是最终得到加工中心关键部件振型的最佳方案。通过适当的简化,建立加工中心的工作台、床身、立柱以及主轴箱的三维模型。
为了获取加工中心各部件的振型,对以上各部件进行材料属性定义、接触定义、网格划分以及边界条件设置等有限元分析前处理步骤[3]。
(1)设定材料属性
该加工中心的床身、立柱、主轴箱、床鞍和工作台的材料是铸铁。密度为7300 kg/m3.泊松比为0.25,弹性模量为135 GPa;丝杠、丝杠螺母的材料是高性能优质钢,密度为7 800 kg/m3。泊松比为0.3,弹性模量为200 GPa。
(2)定义接触对
在建模时,将滑块和工作台的接触面定义为绑定接触.这样的处理既有利于工作台系统的简化,又可以提高计算效率。同样的,滑块与立柱之间、滑块与床身之间的接触面均定义为绑定接触。加工中心所有导轨和滑块以及滚珠丝杠和丝杠母座之间的接触类型均定义为不分离接触。在进行切削加工时.导轨和滑块之间本身就是固定联结.丝杠和工作台之间并没有相对运动,这种接触设置符合实际情况。
(3)划分网格
该加工中心的床身、立柱、主轴箱、床鞍等结构形状复杂,且均设计有合理的布筋,所以为了减小网格划分的复杂度.在分析中采用自动划分网格的形式。工作台、滑块、导轨、丝杠母座等零部件。结构同样较复杂,故也采用自动划分网格的形式;滚珠丝杠在三维建模时被简化成一个圆柱体,所以采用映射划分网格的形式,得到规则的六面体单元。模态分析中没有应力集中现象.因此不需要考虑网格的疏密分布,要求网格尽可能均匀分布。
(4)施加边界条件
模态分析中的边界条件不包括载荷力。所以模态分析时,只需对其作位移边界条件限制即可。为了正确地模拟高速加工中心的工况,采用的约束方法是:对工作台系统的导轨进行固定约束,对丝杠两端施加圆柱约束;对床身、立柱上的导轨及丝杠同样分别施加固定约束以及圆柱约束;立柱是通过螺栓垂直安装在床身后部,所以需对立柱底部添加固定约束;主轴箱只做垂向运动.所以在主轴箱滑块面添加给定位移约束,将横向和纵向位移设置为0来约束主轴箱的横、纵向运动。
最终获取各部件的有限元振型分析结果(见图2),为试验模态测试的布点方案提供了依据。
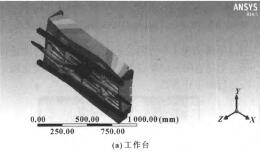
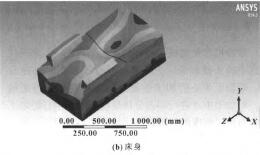
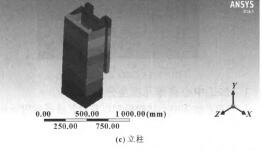
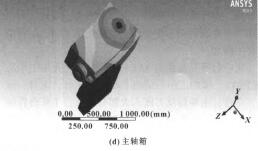
图2各部件有限元振型分析结果
根据加工中心各大部件有限元振型分析结果可知:工作台及床鞍振型变化最大的区域主要分布在工作台的两端4个角点处;床身振型明显变化的部位主要集中在床身上半部分前后两个自由端;立柱顶部的振型变化最大;主轴箱振型最大区域在主轴底部以及主轴箱顶部。
加工中心整机的有限元分析结果如表1所示。
表1整机前8阶频率
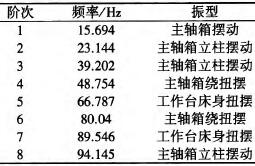
2、加工中心试验模态分析
试验模态分析和有限元模态分析是研究对象模态参数的常用手段,两者为现代加工中心的动态设计提供了2条最为有效的途径。试验模态分析方法是研究数控加工中心动态特性的常用方法,对加工中心结构的动态特性分析有着重要的作用H J。
2.1 测试系统
对KVC800立式加工中心进行试验模态测试的系统主要由3个部分(图3)组成。
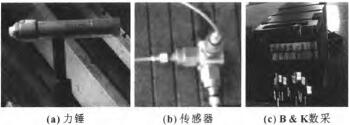
图3模态测试系统各组件
激励系统。试验中选用8206.002型脉冲力锤作为激励装置。该型号力锤能承受的压力为0—2 200N。为获得加工中心结构的低频段数据,力锤锤帽材料应选择为橡胶,橡胶锤帽比较软,需要添加附加质量才能够产生可以激发出更多模态的冲击力,使得激励信号有更多的能量。
测量系统。主要由力传感器和加速度传感器组成。利用力锤对结构锤击产生激励,输入到系统的信号则是锤击的力信号,所以一般用力传感器拾取;响应信号一般是传感器从被测结构件上拾取的速度、加速度或者位移信号。试验中利用特制的安装座在每个测点处安装3个方向的传感器。
数据采集处理系统。由数据采集卡、采集箱以及模态分析软件组成。试验中由力传感器和加速度传感器测得信号经过丹麦B&K数据采集器采集和储存,该采集卡有12个通道,测试频率范围为0—25.6kHz,当通道数不够时,即可用采集箱合并使用多块采集卡。试验采用丹麦B&K公司开发的模态测试模块(MTC Hammer)进行数据采集以及自带的分析模块(Modal Analysis)对数据进行处理分析。
2.2参数设置
(1)分析频率
影响加工中心性能的频率范围主要是低频段,且研究对象KVC800型立式加工中心工作时主轴的最高转速为6 000 r/min,根据公式凡=60f,整机的转频范围在100 Hz以内,故试验主要关心低阶频段上的模态参数。试验设定的分析频段为0~100 Hz。
(2)采样频率
采样频率的物理公式为:

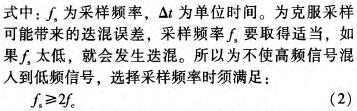
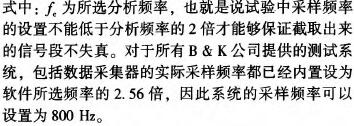
(3)平均次数
为了减少试验过程中噪声的干扰。提高分析的精度,试验采用多次敲击被测件的方法,通过集总平均处理最终计算出频响函数,平均次数设置为5。
(4)力锤触发设置
设置合理的触发方式对于瞬态信号的捕获有很大的作用。对于添加附加质量的橡胶锤头,激励力应设置在100—700 N之间,结合力锤操作者力度的大小,以及多次试验的试敲结果,设置激励力为120 N。
(5)窗函数选取
分析处理响应信号时需要截断信号,这时往往容易产生截断误差,所以需要添加窗函数来减小误差。锤击力的保持时间比较短,测试过程中不可能只测产生力的那一瞬间,所以需要通过对激励信号加力窗以减小后续时间段内噪声的影响:响应信号则加指数窗以减小泄漏误差。
(6)激励点及响应点布置
测试过程中激励点以及响应点的布置以有限元振型分析结果为依据[5。6]。工作台激励点布置在其振型较大的4个角点中任一角点附近,响应点主要布置在其上表面的4个顶点处;床身激励点则布置在其振型变化大的上半部分右侧面,响应点则分布在其右侧面的4个顶点以及前面上端的两顶点处:立柱部分激励点施加在其振型变化明显的上右侧面,响应点主要分布在右侧面4个角点和顶部2点:主轴箱部分激励点布置在有较明显振动的底部主轴的圆柱面上.考虑到主轴箱属于薄壁结构.其响应点则布置在下端主轴的2个圆柱面上。
各部件在整机约束环境中的试验模态分析结果如图4所示。
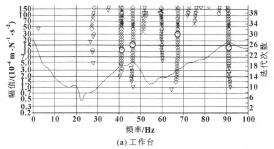
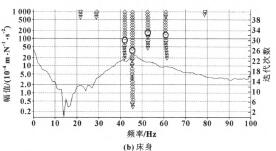
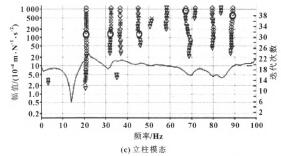
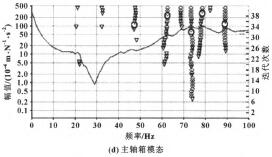
图4模态分析结果
3、加工中心升速过程的瀑布图分析
瀑布图是一种反映系统动态特性的频谱级联图,它可以将系统各转速下的频谱图描绘在同一张图上㈨。根据测得的瀑布图,可以清楚地了解到系统的固有频率、振动幅度以及稳定性等一系列动态特性。手动开启数控加工中心至最高转速,试验过程中主轴最高转速设置为5 500 r/rain,利用B&K测试系统的Labshop数据采集与分析模块对整个升速过程中的振动信号予以记录,并进行了瀑布图分析,瀑布图中的突变点反映了加工中心的各阶固有频率¨】。在加工中心工作台、床身、立柱以及主轴箱处分别测得的振动信号分析所得瀑布图如图5所示。
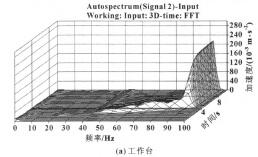
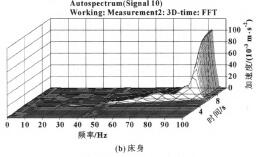
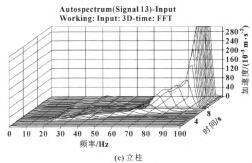
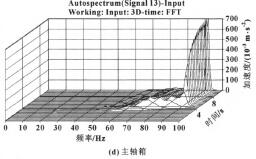
图5升速过程瀑布图
从试验模态分析图与瀑布图中筛选相互对应的模 态频率并加以对比。如表2所示。
表2模态试验与升速瀑布图所得模态频率对比
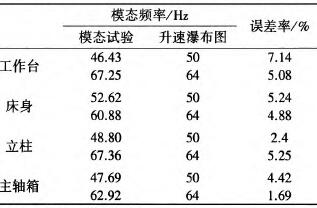
结合有限元分析结果以及表2可知:以有限元振型为依据,在50 Hz的工作转频下,由于主轴箱的摆动引起加工中-tL,振动从而影响加工质量:在64 Hz的工作转频下。工作台的摆动影响了加工中心的加工质量。因此,在实际加工工件过程中,应尽量避免50Hz及64 Hz的工作转频.即3 000 r/min和3 840r/min的主轴工作转速。
4、加工中心切削动态试验验证
加工中心的动态特性特别是工作频率直接影响着加工质量的好坏[9],.切削加工时的振动是影响加工质量的重要因素,通过测量加工件表面的粗糙度值可以有效地体现加工质量。为进一步验证分析所得的结果,开展加工中。tL,的切削动态验证试验。
分别以2 800、3 000、3 200、3 400、3 600、3 800和4 000 r/min的转速进行切削加工实验:然后,利用马尔公司研制的带有高精度测头的粗糙度仪M400。对不同转频加工后工件的表面进行粗糙度测量,对比分析粗糙度值来验证试验结果。
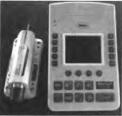
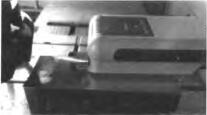
图6马尔粗糙度仪
不同工作转速下测得工件的表面粗糙度如表3所示。
表3粗糙度对比
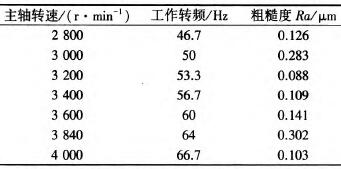
从粗糙度值结果不难看出:相较于其他工作转频.50和64 Hz工作转频下加工后的工件表面粗糙度值明显增大,有限元模态、试验模态以及振动测试的综合分析结果得到验证,50以及64 Hz是加工中心在工作过程中容易引发共振的频率值,影响加工质量,故而在加工中心的使用过程中应尽量避免长期使用3 000和3 840 r/min的工作转速。
5、结束语
(1)基于有限元分析理论,利用ANSYS软件对加工中心各部件三维模型进行了有限元振型分析,得到了加工中心振型变化明显的区域,为模态试验的激励点与响应点的布置提供了依据。
(2)基于有限元振型分析结果,利用丹麦B&K公司的模态测试软件对加工中心各部件进行了试验模态测试。通过B&K自带的Modal Analysis模态分析软件得到了加工中一tL,各部件的模态参数,为后续的对比分析提供了依据。
(3)利用B&K测试系统对加工中,tL,整个升速过程的振动信号予以记录,进行瀑布图分析,并从中获取模态信息,与试验模态测试结果进行了对比验证。获知在实际使用过程中应避开长时间3 000和3 840 r/min的主轴工作转速。
(4)结合切削加工验证试验,通过对比分析不同工作转频加工后的工件表面粗糙度值,验证了综合分析结果的准确性.为加工中一tL,的优化运行提供了可靠的依据。
投稿箱:
如果您有机床行业、企业相关新闻稿件发表,或进行资讯合作,欢迎联系本网编辑部, 邮箱:skjcsc@vip.sina.com
如果您有机床行业、企业相关新闻稿件发表,或进行资讯合作,欢迎联系本网编辑部, 邮箱:skjcsc@vip.sina.com
更多相关信息