数控车床床身铸件的铸造工艺改进
2016-9-1 来源:沈阳机床银丰铸造有限公司 作者: 李鹏明 刘源 王铸 张文军
摘要:介绍了机床床身的铸件结构及技术要求,详细阐述了该件的原生产工艺:分型面选择在地脚面所在平面,铸件收缩率为1%,采用开放底返式浇注系统,直浇道采用4,75 mm耐火管,横浇道截面积为49.5 cm2,内浇道是5根咖30 mm耐火管,内浇道之间的距离为40 mm。生产结果显示:内浇道附近导轨局部表面有砂眼、粘砂等缺陷,清理困难。分析其原因后,通过更改内浇道位置,扩大内浇道与横浇道的距离,并采用双排横浇道,较好地消除了床身铸件导轨产生的砂眼、粘砂等缺陷,使铸件的出品率提高到89%以上。
关键词:灰铸铁;数控车床床身;导轨;工艺改进
随着数字技术的发展、普及和柔性化生产的需要,开始研制具有高精度、高效率、高自动化等优点的数控车床。它对国计民生的一些重要行业(IT、汽车、轻工、医疗等)的发展起着越来越重要的作用,因为这些行业所需装备的数字化已是现代发展的大趋势㈣。总体而言,数控车床是一种高精度、高效率的自动化机床,由数控装置、床身、主轴箱、刀架进给系统、尾座、液压系统、冷却系统、润滑系统、排屑器等部分组成,床身是其组成部分的基础部件,铸件技术要求严格,不允许有气孔、砂眼、缩孔等铸造缺陷,铸件质量应符合JBn/T 3997标准,严格按照铸件验收技术条件验收㈣。
笔者公司生产的床身铸件形状结构复杂,材料牌号为HT300,最大轮廓尺寸1 745 mmx920minx741 mm,壁厚较厚处25 mm,壁厚较薄处18mln,平均壁厚20 mm,导轨处壁厚达41 mm,铸件质量1 265 kg,铸件结构如图1所示,其化学成分及力学性能如表1所示。
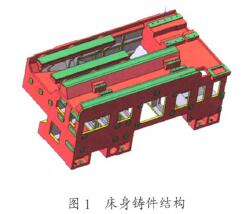

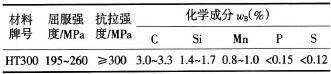
1、工艺难点分析
由于铸件为床身类零件,2条导轨处壁厚41mrfl,长度1 348 mm,宽度168 mm,内腔筋板壁厚较薄,最薄处18 mm,易产生缩孔、裂纹、浇不足等缺陷。导轨表面质量要求严格,不允许有气孔、砂眼、缩孔等铸造缺陷,铸件滑动导轨处硬度为190~255 HBW,铸件内腔筋板交叉处热节形成可能性较大,极易产生粘砂现象。如何设计合理的铸造工艺,减少铸件产生的缺陷,满足铸件内在和外在的技术要求,是床身铸件铸造生产中的难点。
2、铸造工艺设计
2.1分型面和浇注位置的选择
选择呋喃树脂砂手工木底板造型方法,考虑到铸件的使用要求和技术要求,铸件遵循顺序凝固的原则,确定选用上、下2箱造型方法,床身的导轨面是关键表面,不允许有砂眼、气孔、渣孔、裂纹和缩松等缺陷,而且要求组织致密、均匀,以保证硬度值在规定的范围内。床身导轨截面比较厚大,最佳浇注位置是导轨面朝下,分型面选择在地脚面所在平面,如图2所示。
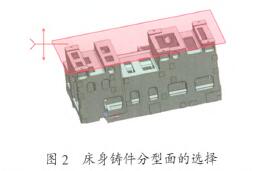
2.2工艺参数的选择
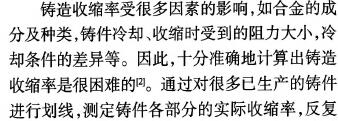
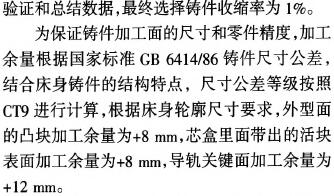
分型负数选择2 mm,均放在下箱,其余未注间隙为1 mm,未注拔模斜度+2 mm,内腔筋板拔模斜度单侧+3 mm。
2.3浇注系统的设计
考虑到铸件壁厚较薄,为防止铸件浇不足和导轨表面出现砂眼等缺陷,设计成开放、底返式浇注系统,直浇道采用西75 mm耐火管,横浇道截面积为49.5 cm2,内浇道选用4,30 mm耐火管(5根),浇注系统设计如图3所示。
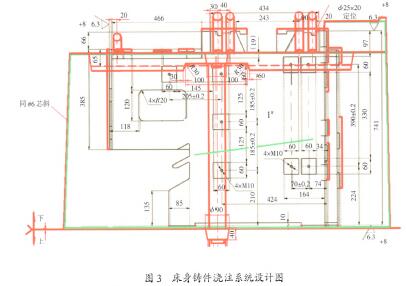
3、生产质量的控制
3.1 模具制备
模具采用红松和多层板制作,保证铸件模具的整体强度和刚度,在吊运、起模过程中不得有任何变形,模具两侧做出起模装置,保证吊运起模的安全性,模具表面光洁度达到1级,表面刷油漆[61,铸造圆角从外模和芯盒做出,模具采用上、下2箱,分型负数2 mm,均在下箱。
3.2造型和制芯
造型时要注意上箱排气定位,保证型腔内排气顺畅,浇注系统采用专用陶瓷耐火管,摆放浇道要认真仔细,防止散砂进入浇注系统内。制芯过程中芯盒和附件要放置准确,以防起芯困难,出气棒放在出气定位凹槽内,共6处,芯头下部要放出气棒,防止浇注时排气不顺,导致铸件产生缺陷。
3.3铸型装配
铸型装配前要检查芯头、外型排气眼是否通畅,砂型是否清理干净,是否有漏涂涂料,下完芯后,芯吊要用新制树脂砂填补,并刷2遍锆英粉涂料,点火烘干后,再次检查尺寸形状是否符合图纸,浇冒口系统内和型腔内是否干净,芯头间隙是否填严,防止铁液钻入或者跑火。在下箱箱口处围一圈石棉绳和一圈耐火泥,压上纸条检查尺寸,确定合格后再合箱,箱口用型砂塞紧,防止浇注跑火,然后放好浇口盆准备浇注15]。
4、生产结果
经过实际生产首件验证,使用原工艺生产的铸件,铸件导轨大部分表面质量良好,铸件组织致密,力学性能和化学成分均达到技术要求。但在内浇道附近导轨局部表面有砂眼、粘砂等缺陷,清理困难,使后续加工环节困难增大。5工艺改进及效果
5.1 工艺改进
导轨表面粘砂的主要原因是内浇道分布比较集中,容易引起过热,造成铸件粘砂,为此将内浇道之间的距离从原来的40 mm改为150 mm、170 mm。改进后的新工艺如图4所示,内浇道开设位置和数量按照顺序凝固和补缩原则来确定,因此将内浇道开设在厚壁处(导轨端面处),使铸件厚大部分得到较充分地补缩,避免出现缩孔、缩松等铸造缺陷。
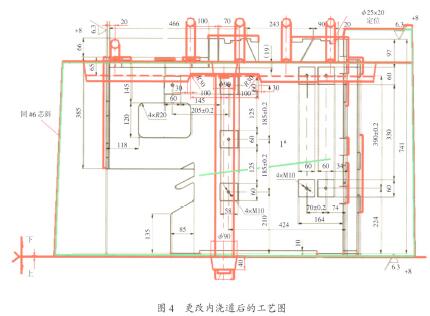
内浇道适当远离横浇道可减小铸件的铸造应力和变形,为此,新工艺采用双横浇道,目的是控制金属液充填铸型的速度及充满铸型所需的时间,使金属液平稳均匀、连续地充满型腔,阻止熔渣、气体以及砂粒、金属氧化物等随金属液进入型腔,使金属液有合适的上升速度,使铸件进行顺序凝固。
据资料分析㈣,铁液中对应直径1 mm的渣团,其悬浮速度为0.37 m/s,相当于0.25 kg/cmz·S的比流量,该值比实际应用的最小比流量0.35kg/cm2·S还小。因此,要在横浇道内捕获更小的渣团,需要更低的流速和更大的横浇道截面积,将横浇道截面积扩大、做高,如F横/F内=2~4,但横浇道太大会浪费金属,故采用双排横浇道,工艺如图5所示。
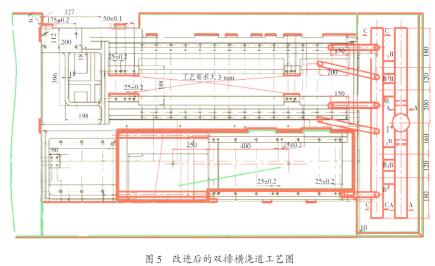
5.2改进后效果
(1)改进后,原有的铸件导轨局部表面粘砂现象完全消除,铸件表面质量满足JBn/1’3997技术要求。
(2)导轨表面的砂眼缺陷也已完全消除,双横浇道阻渣能力更强,更容易阻止熔渣颗粒进入铸件,内浇道放在导轨上面,使铸件实现顺序凝固,避免铸件厚大部分出现缩孔、缩松缺陷,提高了铸件的出品率,使其达到89%以上。
6、结束语
针对数控车床床身铸件导轨处易产生粘砂、砂眼、熔渣等缺陷问题,分析其产生的原因,通过对原铸造工艺进行改进,更改内浇道位置,使内浇道距离横浇道更远,并采用双排横浇道,较好地解决了床身铸件导轨产生砂眼、粘砂等缺陷。
参考文献
【1】王文清,李魁盛.铸造工艺学【M】.北京:机械工业出版社,2002.
【2】陈琦,彭兆弟.铸造技术问题对策【M].北京:机械工业出版社2001,
【3】中国铸造协会.铸造工程师手册[M].北京:机械工业出版社2007
【4】郭林.破碎机前端的铸造生产【J】.铸造技术,2011,(01):139—141
【5】林钰杰,吴宝成.铸态QT600—10的生产工艺叨.现代铸铁,2014,(04):32—34.
【6】糟国睿.141气缸盖铸件铸造缺陷的防止措施叨.现代铸铁,2015,(03):42—45.
【7】黄政.离合器壳体铸件缺陷分析与防止措YgO].铸造技术,201 1,(01):39—41.
投稿箱:
如果您有机床行业、企业相关新闻稿件发表,或进行资讯合作,欢迎联系本网编辑部, 邮箱:skjcsc@vip.sina.com
如果您有机床行业、企业相关新闻稿件发表,或进行资讯合作,欢迎联系本网编辑部, 邮箱:skjcsc@vip.sina.com