铣削应用中切屑厚度模型的演变
2016-7-20 来源:山高刀具集团 作者: 培训经理 Patrick de Vos
上海, 2016 年 06 月 - 金属切削工艺的结果取决于多种因素。其中一个最重要但也最不为人所知的因素是切削刀具所切削下来的“切屑的厚度”。基本上,切屑厚度是指与切削刃呈直角的未变形材料的厚度测量结果。切屑厚度与某些因素相关,例如与影响刀具和工件的作用力密切相关。过大的切屑厚度会导致切削刃崩刃和断裂,而切屑厚度过小会导致切削刃快速磨损。
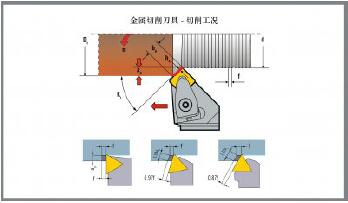
图 1:HQ_ILL_Metal_Cutting_Tools_Cutting_Conditions.jpg
通过确定和控制切屑厚度,制造商可以最大限度地提高金属切削的生产率和效率、针对特定的工件材料定制切削工艺以及控制成本。由于没有充分认识到切屑厚度的重要性,很多制造商的切削刀具或者负载过重,或者利用不足,这都会对刀具的使用寿命和生产率产生负面影响。
既然如此,我们可以借助一些数学模型来了解切屑厚度的功能意义。切屑厚度模型最初是一些用于计算在稳定车削加工中产生的切屑的简单等式,后来越来越复杂,并将断续铣削环境中的多种变量纳入考虑范围。
铣削应用中的切屑厚度模型
在连续车削加工中,切屑厚度会保持不变。但在铣削加工中,切屑厚度会随着切削刃间歇性地出入工件而不断变化。
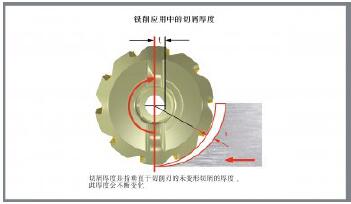
图 2:HQ_ILL_Chip_Thickness_In_Milling.jpg
为了简化对铣削切屑厚度的理解,大约 40 年前,金属切削研究人员提出了“平均切屑厚度”这一概念。他们建立的公式以数学方式创造了具有一致平均厚度的理论切屑。平均切屑厚度模型有助于更好地理解和控制铣削加工。
当确定平均切屑厚度时,必须考虑到刀具在工件中的径向啮合量以及切削刃槽型、刀具主偏角和进给量。通过调节进给量,机械师可以控制切屑的厚度。
刀具与工件的啮合角度是可以根据刀具的直径和切深由小到大变化的。径向啮合量越小,产生的切屑越薄。随着径向啮合量的增大,当啮合量为刀具直径的50% 时,切屑厚度将达到最大值。当径向啮合量超过 50%时,切屑将开始再次变薄。
切削刃的刃口处理也会影响切屑厚度。切屑厚度通常必须不小于切削刃刃口的半径。例如,当切削刃的半径为60 μm 时,需要调节进给量以产生至少 60 μm 的切屑厚度。当进给量过低时,切削刃会与工件摩擦且无法切削工件材料。
铣刀的切削刃刃口处理常常通过增大刃口圆角半径来提高刃口的强度从而降低崩刃和刃口破损的风险。此类刃口处理包括研磨、倒角和倒棱。当铣削难加工材料或粗糙表面时,这些刃口允许使用更激进的进给量。目标是在切削刃的后面形成切屑,并因此避免由于集中产生压力和影响而导致切削刃加速磨损或断裂。调节进给量可改变切屑的形成位置并控制切屑厚度。增大进给量会导致切屑变厚,减小进给量则产生更薄的切屑。
刀具的主偏角直接影响切屑厚度。当刀具的主偏角为 90 度(就像方肩铣刀那样)时,切屑厚度就是 100%的进给量。但当刀具的主偏角为 45 度时,切屑厚度是进给量的 70%,这是因为切屑是在更长的一段切削刃上形成的。减小切削刃的角度会导致切屑变薄,必须增大进给量以保持所需的切屑厚度。
平均切屑厚度等式的应用
平均切屑厚度等式考虑到了刀具的切削刃角度和径向啮合量。图 3 分别以蓝色和红色展示了该等式在侧铣和中心铣削的应用。在主图中,将刀具的径向啮合量与刀具的直径进行了比较,并将比较结果表示为Ae/Dc比率。图一角的小图显示了刀具的主偏角所产生的影响。
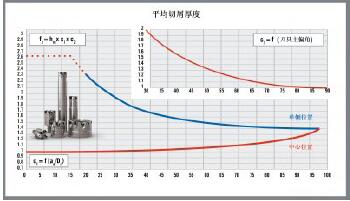
图 3:HQ_ILL_Average_Chip_Thickness.jpg
此图显示了当平均切屑厚度公式不完全有效时的情形。当侧铣时,与刀具直径相比径向切宽非常小时,此公式不适用(请参见虚线)。而在中心铣削中,当刀具直径的50%以上参与切削时,红线表明了进给量是需要不断加大的。这与实践经验相悖(刀具的啮合量增大时,通常会导致进给量减小。因此,当径向啮合量大于刀具直径的 20% 到 25% 和小于刀具直径的 50% 到 75% 时,平均切屑厚度模型最为有用。
平均切屑厚度模型基于几何因素并对复杂情况进行了简化。数十年的应用表明,在刀具寿命等式中使用平均切屑厚度模型可以得出误差在 ±15% 以内的估算结果。如此高的精度足以满足功率和扭矩计算以及多种常规工件材料加工的要求。此外,通过人工方式对平均切屑厚度等式进行求解时,所花费的时间和精力也在合理范围内。
但当应用场合需要更高的精度或者铣削难加工的材料时,需要使用包含其他因素的模型。
等效切屑厚度
瑞典的研究人员 Sören Hägglund 开发出了一种更全面的模型,这种模型提供了一种称为等效切屑厚度的测量方法,可以得出误差在 ±2% 以内的刀具寿命预测。在图 4 显示的模型中,黄色弧形代表铣刀所产生的实际切屑的厚度变化。橙色条形显示了平均切屑厚度方法,是黄色图片的展开版本。蓝色条形代表等效切屑厚度。它们的一个主要差别在于,等效切屑厚度模型考虑到了切削刃在切削时所花费的时间。这一点非常重要,原因在于刀具在工件中的啮合量并不固定,切削刃在切削时花费的时间也不尽相同,而且所产生的切屑厚度也会发生变化。
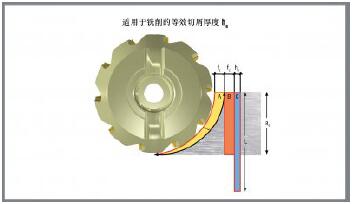
图 4:HQ_ILL_Equivalent_Chip_Thickness_For_Milling.jpg
等效切屑厚度模型还考虑到了刀具的刀尖圆弧半径对切屑厚度的影响。该模型采用了瑞典工程师 RagnarWoxén 在 20 世纪 30 年代初原本为车削加工开发的一个概念。Woxén 的公式可计算出刀具刀尖的理论切屑厚度,非常透彻地分析了刀尖圆弧半径,并能够利用矩形来说明切屑面积。
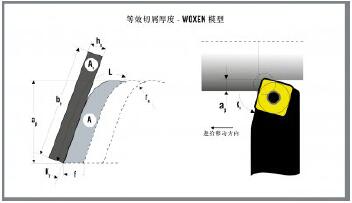
图 5:HQ_ILL_Equivalent_Chip_Thickness_Woxen_Model.jpg
通过计算切屑厚度,制造商可以避免由于切屑的厚度小于特定的最低水平或大于特定的最高水平而产生问题。当径向啮合量相对于刀具的直径增大时,必须减小进给量以保持相同的切屑厚度。这样可以确保最大切屑厚度不会变得过大,否则会导致刀具寿命缩短并最终断裂。
另一方面,当加工应变硬化的材料(例如超级合金和钛合金)时,形成比特定最低水平更厚的切屑特别重要。当切削刃产生过薄的切屑时,会导致后来使用的切削刃切削出加工硬化的区域。切削最终产生的这一层应变硬化材料时,会加速刀具磨损,并可能导致刀具寿命缩短三分之二。
很多车间会采用与加工淬硬钢相同的策略来加工容易出现加工硬化的材料,并且使用更小的切削深度和进给量。结果,铣刀运行时使用的参数通常无法达到足够大的切屑厚度,铣削质量也会不尽如人意。选择传统铣削策略或顺铣策略(参阅附注)也会影响切屑厚度以及容易出现加工硬化材料的加工。
结论
控制切屑厚度是成功进行铣削加工的一个关键因素。要充分利用切屑厚度概念,需要首先计算等效切屑厚度,然后确定切屑厚度的下限和上限。
由于复杂的等效切屑厚度模型包含一组变量,因此对等式进行求解时需要花费的时间和精力要比经过简化的平均切屑厚度模型多很多。在生产环境中通过人工方式进行这些计算时,既不划算,也非常耗时。
但可以利用计算机软件程序来计算加工参数(例如山高提供的程序),用户在几秒钟内即可输入数据并求出等式的结果。这可优化铣削工艺,从而提高生产率和盈利能力。
附注
切屑厚度和铣削技术
采用等效切屑厚度这一概念时,需要考虑切屑的形成方式。进行铣削加工时,会以两种不同的方式形成切屑,具体情况取决于相对于工件移动方向的刀具旋转方向。这两种方法是传统铣削(向上)和顺铣(向下)。在传统铣削中,刀具的旋转方向与工件进给方向相反。在顺铣中,刀具的旋转方向与工件进给方向相同。
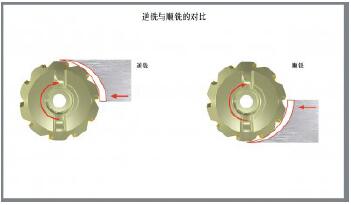
图 6:HQ_ILL_Up_Milling_Versus_Down_Milling.jpg
在传统铣削中,切削刃以零切削深度进入工件。切屑的厚度在开始形成时最小,在结束时达到最大值。相反,顺铣时形成的切屑厚度在开始时达到最大值,然后逐渐减小到最小值。
使用传统方法进行铣削时,切削刃会在切削之前摩擦工件,而且薄切屑的吸热能力较差。这两种情况都会导致工件表面发生应变硬化以及刀具寿命缩短。切屑会掉落在刀具的前面,因此可能被再次切削并导致表面粗糙度下降。在水平铣削中,向上的切削力可能会将工件提起,因此需要使用复杂的工件夹具。
顺铣之所以倍受青睐,是多种原因造成的。切削刃在进入工件进行切削时无需摩擦,因此最大限度延长了刀具寿命、减少了所产生的热量。需要的机床功率更小,切屑掉落在刀具的后面,可最大限度避免再次切削而且提高了表面粗糙度、延长了刀具寿命。切削动作会产生向下的力,有助于稳定工件和简化夹具。当加工超级合金、不锈钢和钛合金等材料时,切屑的初始厚度可实现散热并最大限度减少工件表面的应变硬化。
然而,顺铣时产生的向下的力可能会导致机床工作台反冲,尤其是在较旧和/或手动铣削的设备上。反冲会影响精度并导致刀具由于切屑负载增大而可能断裂。因此,当使用不太稳定的机床和工件时,可能需要采用传统铣削方法。
当铣削铸件、锻件和表面硬化材料时,也可以优先使用传统铣削方法。这是因为传统方法会在材料的硬化表面或粗糙表面的下方开始切削,而在顺铣中,刀具以完整的切屑厚度进入到零件中,因此可能会导致切削刃在遇到材料的硬化区域时崩刃。
投稿箱:
如果您有机床行业、企业相关新闻稿件发表,或进行资讯合作,欢迎联系本网编辑部, 邮箱:skjcsc@vip.sina.com
如果您有机床行业、企业相关新闻稿件发表,或进行资讯合作,欢迎联系本网编辑部, 邮箱:skjcsc@vip.sina.com
更多相关信息