在航空发动机加工中摆线铣加工技术的应用
2015-12-22 来源:中航工业西安航空发动机(集团)有限公司 作者:廖铃吉
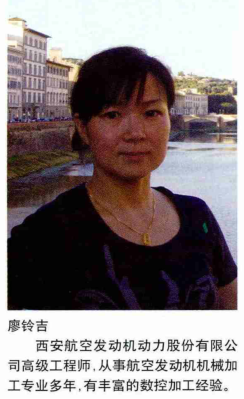
与传统加工不同,摆线铣加工过程中刀具-工件包角一直处于较小的状态,刀具在公转一周的过程中处于切削状态的时间较少,从而非常有利于切屑的排出与刀具的散热。摆线铣削主要目的是在充分满足径向切深的情况下避免槽铣等全浸入式铣削。这对于减少刀具的磨损、延长刀具的使用寿命非常有利。而对于采用较小的刀具-工件包角有可能带来的切削效率降低,在摆线铣技术中,可以采用比常规铣削方法更大的轴向切深以提高材料去除率。
高温合金、钛合金等难加工材料在航空发动机零部件中广泛应用,如航空发动机整体叶盘、机匣等复零部件。这类材料切削性能差,在加工时切削力较大、切削温度高,造成刀具磨损严重。生产实践中,通常采用较为保守的切削参数以降低刀具磨损速率和控制工件表面加工质量。但是,这会造成产品的加工效率较低。如何提高这类材料的切削加工效率、降低产品的生产周期与生产成本一直是工业界及学术界研究的难点与热点。德国亚琛工业大学的研究发现,在切削难加工材料时,刀具-工件包角对刀具的磨损有重要影响。有效控制刀具-工件的包角对于控制切削加工过程中的热力耦合作用、减少刀具磨损有显著效果。摆线铣加工技术是一种在切削过程中对刀具进行降低负载和充分冷却的加工技术。摆线铣加工过程中,由于刀具-工件之间具有较小的包角,可以在切削难加工材料时提供有效的冷却与润滑,从而可以提高切削速度、避免满刀切削、降低刀具的磨损,近年来逐渐引起了工业界的重视并在难加工材料的粗加工中进行了应用。
摆线铣加工技术
1 摆线铣加工中的力热耦合作用
特点
粗加工过程中通常期望提高材料去除率。传统铣削方法通常采用增大刀具啮合角来满足材料去除率的要求。然而,这必然导致刀具和工件之间的接触时间长、切削温度升高,进而影响刀具使用寿命。如图 1所示,以槽铣为例,使用传统的工艺方法开槽时,刀具啮合角可以达到180°。过大的刀具浸入角 (刀具包角)会产生过大的径向力,使刀具发生弯曲变形,从而影响腔槽的几何尺寸。
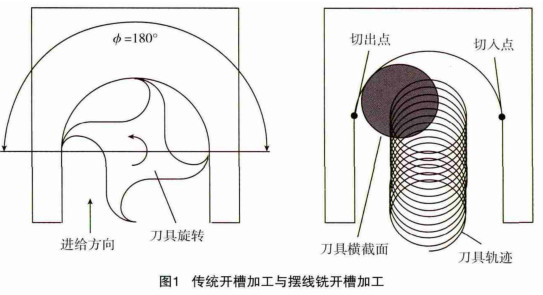
此外,当刀具 -工件包角过大时,切削热不断积累、加工温度升高,从而导致切削温度超过了刀具涂层的耐温极限,形成刀具涂层失效、加剧了刀具磨损,如图 2 所示。因此,加工时不得不选取保守的轴向切削深减小切削量、降低刀具的磨损速度。这种情况不仅降低了加工效率,还影响了加工的精度。
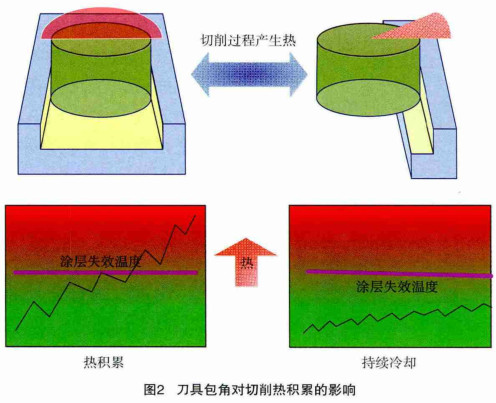
与传统加工不同,摆线铣加工过程中刀具 - 工件包角一直处于较小的状态,刀具在公转一周的过程中处于切削状态的时间较少,从而非常有利于切屑的排出与刀具的散热。摆线铣削主要目的是在充分满足径向切深的情况下避免槽铣等全浸入式铣削。这对于减少刀具的磨损、延长刀具的使用寿命非常有利。而对于采用较小的刀具 -工件包角有可能带来的切削效率降低,在摆线铣技术中,可以采用比常规铣削方法更大的轴向切深以提高材料去除率。
切削力方面,摆线铣时刀具在每公转一周的过程中,径向的切削深度从零开始逐渐增加到最大,然后再逐渐减小到零。切削力也经历着从零增大到再减小的过程,如图 3 所示。
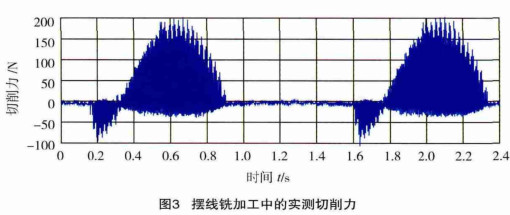
因此,切削过程中刀具负载不会出现突变的情况。此外,因为摆线加工中刀具的径向切削深度较小,所以切削合力也较小。较低的切削温度以及小径向切深带来的低切削力使得在摆线铣过程中可以采用相对于传统加工 2~3 倍以上的进给速度,从而有效提高加工效率。
2 摆线铣的轨迹形式通常采用的摆线刀具轨迹有两种模型:圆形模型和次摆线模型,如图 4 所示。其中,圆形模型轨迹由圆和直线段组成,刀具公转运行轨迹为圆形,旋转一周后沿圆弧一侧的直线移动一个步长再进行公转。这种加工轨迹的计算较为简单,但是会产生加速度的不连续。
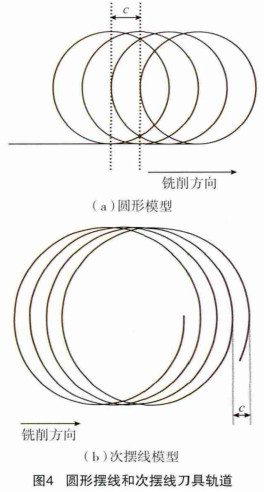
次摆线模型轨迹与圆形模型轨迹相比,主要差别在于刀具进给方向上的运动不单纯是直线运动。这种摆线轨迹在切向和曲率上都是连续的,更容易满足数控机床的运动学要求除上述轨迹之外,逐渐被普遍采用的一种摆线铣加工轨迹如图 5 所示。这种轨迹在次摆线轨迹的基础上缩短非切削部分的轨迹长度,采用直线进行连接,从而有助于提高加工效率。目前摆线铣加工轨迹生成方法中主要采用这种轨迹形式。
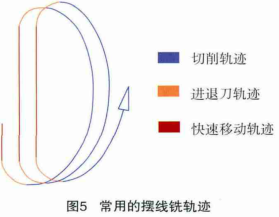
3 摆线铣加工技术的优点相对于常规加工轨迹形式,摆线铣加工技术具有如下优点:
(1) 摆线铣加工中,刀具沿摆线轨迹进行切削,可以适应各种加工余量的变化,从而降低加工余量突变对刀具的破坏。
(2)特别适合难加工材料的切削加工,如高温合金、钛合金、耐热不锈钢等材料。
(3)摆线铣加工技术可以采用较大的轴向切削深度,从而可以代替传统加工中需要进行多次分层的情况。例如,在航空发动机用高温合金的切削过程中,轴向切深可达 20mm
(4)摆线铣加工过程中刀具负载在每一个摆线循环中都经历了从小到大然后再变小的过程,不会出现刀具负载的突变,从而可以有效减少刀具的磨损。刀具寿命最高可延长5 倍以上,从而也相对降低了对刀具品质的要求。
(5)在每一次刀具公转走刀循环过程中,到包含了切削过程和非切削过程,切屑薄容易排出,使得切削区域冷却充分。切削条件得以改善,可以保持高的切削速度,进一步延长了刀具使用寿命。
(6)摆线加工中可以使用密齿刀,从而可以进一步提高切削参数和加工效率。在使用摆线铣加工时,采用 12mm 直径密齿刀具加工高温合金时的进给速度可达 800mm /min 以上,单件的加工时间最多可以降低75% 。
(7) 由于切削时切削力较小,将摆线铣技术与高速加工技术结合则特别适合薄壁零件的高效加工。摆线铣加工技术的发展现状随着数控机床性能的不断提高以及摆线加工技术的不断完善, 国内外工业界对摆线加工技术的应用也逐渐增多。美国 CELER ITIVE技术公司对摆线铣加工技术进行了发展,开发出了专用的 VoluMill软件,并申请了相关轨迹生成方法的专利。VoluMill软件目前已可直接集成于SiemensNX、PTC、OpenMind 等主流软件中。
英国 Del cam 公司近年来在摆线铣加工技术的基础上开发了专门针对粗加工的 V ortex技术。利用该技术在加工钛合金零件时加工效率可以提升 60% 以上。利用 Vortex技术生成的加工轨迹如图 6 所示。
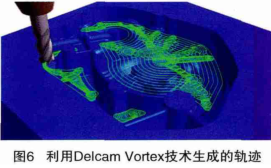
除了在型腔类零件的加工中使用摆线铣加工技术,在复杂薄壁零件加工中的应用也逐渐增多。德国M TU 航空发动机公司从 2000 年开始研究摆线加工技术在航空发动机整体叶盘加工中的应用,经过 10 余年的研究开发成功并在整体叶盘的加工中进行了应用。根据 M TU 航空发动机公司的研究报告,采用摆线铣加工技术加工高温合金 In718 整体叶盘时,加工时间可以缩短至原来的34% 左右,加工过程中使用的刀具数量降为原来的 28% ,叶盘加工中的刀具成本降为原来的 38% 。摆线铣加工技术(图 7)为 M TU 航空发动机公司整体叶盘的加工带来了巨大的效益。此外,DPTechnology公司从2012 年开始也在软件中集成了整体叶盘的摆线铣粗加工开槽模块。
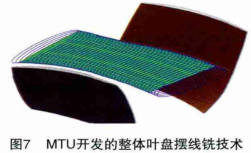
德国的OPENMIND软件公司在VoluMILL的基础上开发了hyperM A X X 模块,可以在类似发动机机匣的复杂薄壁环形件的加工中进行应用,如图 8 所示。该模块具备2 轴、3 轴以及 5 轴的摆线加工轨迹生成能力。
除了软件公司对摆线铣加工技术进行开发与集成之外,数控系统制造商也逐渐增加了该项功能。海德汉 iTN C 530 系统增加了 275 摆线槽加工循环,可以用于任何槽的高效完整加工。该循环采用直线前进运动与铣刀圆周运动叠加形成轨迹。该功能特别适用于铣削高强度或高硬度的材料,在采用 275 摆线加工循环时允许使用大的切削深度和高速的切削运动。
摆线铣加工难点分析摆线铣加工技术在难加工材料的高效切削加工中作用显著, 但是在实际应用过程中仍存在以下几个难点:
(1)刀具 -工件包角的确定。在生成摆线铣加工轨迹时,刀具 -工件最大包角的选择对加工效率有显著影响。刀具 -工件包角选择过大会导致刀具的加速磨损,而选择过小又会导致加工轨迹过长,影响加工效率。刀具-工件包角的大小对切削过程中力热耦合作用有重要影响, 进而影响到刀具的使用寿命和加工效率。因此,需要针对不同的工件材料,通过切削试验确定较佳的刀具 - 工件包角。
(2)摆线加工轨迹的生成。目前的主流软件中,都已具备简单摆线铣加工轨迹生成的功能。但是对于复杂曲面结构零件,则需要较为复杂的摆线铣加工轨迹生成方法。摆线轨迹生成要求光顺性较好,以使得机床在运行过程中能获得较好的加减速性能。此外,目前的摆线加工轨迹应用在 2~3 轴中的应用较多,在 5 轴加工中的应用较少。在生成 5 轴摆线铣加工轨迹时,由于刀具轴向切深较大,刀轴矢量的变化对刀具负载的变化影响较大。因此,如何对 5 轴摆线铣加工中的刀轴矢量进行控制也是摆线铣加工轨迹生成中的难点。
(3)切削刀具的选择。摆线铣加工方式可用于航空发动机复杂薄壁零部件的高效粗加工,如整体叶盘、机匣等。这类零件通常加工区域空间有限,必须选择合适直径的刀具进行加工。此外,在加工难加工材料时,还应考虑在摆线铣加工过程中采用密齿刀进行加工。
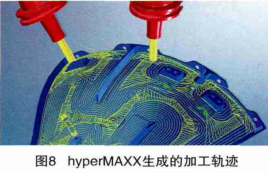
摆线铣加工技术的应用验证摆线铣加工技术在难加工材料和薄壁零件加工过程中显现出的优势为航空发动机难加工材料复杂结构零部件的高效粗加工提供了一种新的可能。同时,对刀具要求的降低与加工效率的提升也大大降低了航空发动机复杂零部件的加工成本。图 9 所示为采用摆线铣加工方法和常规方法加工航空发动机用G H 4169G 材料时的刀具磨损情况对比结果,所用刀具为国产普通硬质合金涂层刀具。从结果中可以看出, 在相同的材料切除量与加工时间情况下,采用摆线铣加工时的刀具磨损量远低于使用常规加工方法时的刀具磨损量。
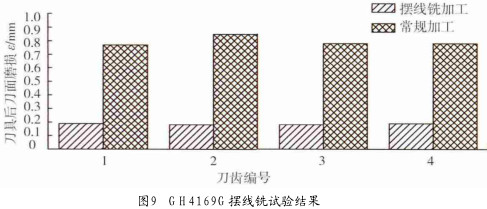
为进一步验证摆线铣加工技术,对航空发动机机匣模拟件进行切削加工。工件材料为耐热不锈钢,所用刀具为 12m m 国产硬质合金平底刀。刀具轴向切深为 2. 5m m ,待切除的材料体积为 79cm
3。采用摆线铣方法的加工时间为 31m in,加工后刀具磨损量较小。机匣试件摆线铣试验结果如图 10 所示。上述试验验证结果充分显示出摆线铣技术在航空发动机难加工材料零部件高效粗加工中应用的潜力。
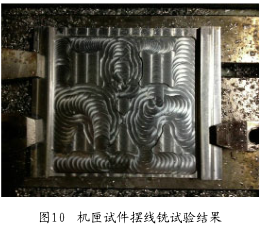
结束语
难加工材料在航空发动机中大量使用,随着数控机床性能的提高,采用摆线铣加工技术实现航空发动机难加工材料复杂零部件的高效粗加工已成为可能。目前,摆线铣加工技术已在多款软件中进行了集成与应用,但在结合发动机复杂零部件的加工应用中还需要在以下几个方面加强:
(1)常用航空发动机难加工材料的基础切削参数。在应用摆线铣加工技术时,确定合适的刀具 - 工件包角与切削参数对发挥摆线铣的加工优势、提高加工效率有重要作用。
(2)多轴摆线铣加工策略研究。航空发动机机匣、整体叶盘等零部件结构复杂,在如何结合这类零件的结构特点高效应用摆线铣加工技术方面需要进一步深入研究。
(3)摆线铣加工技术应结合数控加工装备与刀具的特点。摆线铣加工技术具有切深大、速度高的特点,在规划摆线铣加工轨迹与确定切削参数时应结合数控装备和切削刀具的特点,充分发挥摆线铣技术的优点与数控设备的利用效率。
投稿箱:
如果您有机床行业、企业相关新闻稿件发表,或进行资讯合作,欢迎联系本网编辑部, 邮箱:skjcsc@vip.sina.com
如果您有机床行业、企业相关新闻稿件发表,或进行资讯合作,欢迎联系本网编辑部, 邮箱:skjcsc@vip.sina.com
更多相关信息